Pengeboran adalah konstruksi pekerjaan terarah penambangan dengan diameter kecil dan kedalaman yang besar. Mulut sumur terletak di permukaan bumi, dan bagian bawahnya terletak di bagian bawah. Hari ini, pengeboran minyak dan sumur gas untuk ekstraksi mineral yang relevan.
Tugas dan tujuan pengeboran minyak dan gas
Saat ini, minyak dan gas diekstraksi dari sumur. Meskipun banyak cara yang berbeda untuk membuat sumur, mereka masih berkembang, metode baru sedang dikembangkan untuk mempercepat pekerjaan dan mengurangi biaya biaya mereka.
Proses pengeboran modern terdiri dari langkah-langkah berikut:
- poros tenggelam
- Pemisahan lapisan
- Pengembangan dan pengoperasian sumur
Pengeboran sumur dibagi menjadi dua tahap, yang harus dilakukan secara paralel satu sama lain: pendalaman bagian bawah dan pembersihannya dari batuan yang dapat dirusak. Pemisahan batuan juga dilakukan dalam dua tahap: pemasangan pipa selubung, penyambungan dan penyegelan satu sama lain.
Terlepas dari kenyataan bahwa di rumah tidak ada yang akan mengebor sumur industri untuk minyak dan gas, menarik untuk mengetahui berapa biaya sumur minyak dan metode mana yang paling banyak digunakan.
Proses pengeboran minyak - video
Metode pengeboran dasar
Saat ini, berbagai metode pengeboran dipraktekkan. sumur minyak, tetapi yang paling umum di antara mereka adalah:
- Pengeboran putar dengan caisson untuk sumur
- Pengeboran turbin
- Pengeboran sekrup
Pengeboran putar sumur minyak adalah salah satu metode yang populer. Pahat, melewati kedalaman batuan tanah, berputar bersama dengan pipa bor. Torsi dari sistem semacam itu, pertama-tama, tergantung pada ketahanan batu-batuan yang ditemui di jalan.
Pengeboran sumur rotari berutang popularitasnya pada keuntungan seperti kemampuan untuk menahan fluktuasi WOB yang besar, independensi pengaturan dari faktor-faktor asing, dan lintasan yang besar dalam satu putaran.
Pengeboran sumur minyak dilakukan melalui instalasi di mana bit berinteraksi dengan turbin turbodrill. Unit didorong ke rotasi oleh aliran fluida yang bersirkulasi di bawah tekanan tinggi melalui sistem stator dan rotor. Karena itu, termasuk pengangkatan dan pemompaan air sumur.
Torsi tidak tergantung pada kedalaman sumur, sifat batuan, kecepatan rotasi dan beban aksial. Pada saat yang sama, koefisien transfer di pengeboran turbin urutan besarnya lebih tinggi daripada dengan putar, tetapi biaya pekerjaan lebih besar karena kebutuhan energi yang besar, tidak mungkin untuk dengan cepat mengkonfigurasi ulang parameter pemasangan.
Pengeboran sekrup sumur minyak dan gas terletak pada kenyataan bahwa mekanisme kerja utama terdiri dari sejumlah besar mekanisme sekrup, sehingga frekuensi rotasi bit yang optimal tercapai. Terlepas dari semua prospeknya, metode ini belum mendapatkan distribusi yang tepat, tetapi memiliki potensi besar untuk ini.
Masalah harga
Setelah mengetahui sendiri bagaimana sumur minyak dibor, pertanyaan tentang berapa banyak yang harus Anda keluarkan untuk mengebor satu meter corong berikutnya tentu menjadi menarik.
Saat ini, biaya pengeboran sumur minyak sangat besar dan tergantung pada sejumlah besar faktor:
- Kedalaman sumur
- Kebutuhan untuk membeli casing pipa plastik untuk sumur
- Kondisi sekitar
- Tenggat waktu
Jika kita berbicara tentang angka pasti, maka harga sumur dengan kedalaman 2000-3000 meter adalah dari 30 hingga 60 juta rubel. Pengeboran eksplorasi akan memakan biaya sekitar 40-50% dari biaya pengeboran.
1. Sejarah singkat perkembangan pengeboran
Berdasarkan penemuan dan penelitian arkeologi, telah ditetapkan bahwa sekitar 25 ribu tahun yang lalu, manusia primitif mengebor lubang di dalamnya untuk memasang pegangan dalam pembuatan berbagai alat. Sebuah bor batu berfungsi sebagai alat kerja.
Di Mesir kuno, pengeboran putar (drilling) digunakan dalam pembangunan piramida sekitar 6.000 tahun yang lalu.
Laporan pertama dari Cina sumur untuk ekstraksi air dan garam air asin terkandung dalam karya-karya filsuf Konfusius, yang ditulis sekitar 600 SM. Sumur-sumur tersebut dibangun dengan menggunakan pemboran perkusi dan mencapai kedalaman 900 m, ini menunjukkan bahwa sebelum ini, teknik pemboran telah berkembang setidaknya selama beberapa ratus tahun. Terkadang, saat mengebor, orang Cina menemukan minyak dan gas. Jadi dalam 221 ... 263 tahun. IKLAN di Sichuan, gas diekstraksi dari sumur dengan kedalaman sekitar 240 m, yang digunakan untuk menguapkan garam.
Bukti dokumenter tentang teknik pengeboran di Cina sangat langka. Namun, dilihat dari lukisan Tiongkok kuno, relief, permadani, panel, dan sulaman di atas sutra, teknik ini berada pada tahap perkembangan yang cukup tinggi.
Pengeboran sumur pertama di Rusia dimulai pada abad ke-9 dan dikaitkan dengan ekstraksi larutan garam umum di daerah Staraya Russa. Penambangan garam sangat berkembang pada abad XV..XVII, sebagaimana dibuktikan oleh jejak lubang bor yang ditemukan di sekitar kota Solikamsk. Kedalamannya mencapai 100 m dengan diameter sumur awal hingga 1 m.
Dinding sumur sering runtuh. Oleh karena itu, untuk pengikatannya, batang pohon berlubang atau pipa yang ditenun dari kulit pohon willow digunakan. Pada akhir abad XIX. dinding sumur mulai diperbaiki dengan pipa besi. Mereka ditekuk dari besi lembaran dan terpaku. Saat pendalaman sumur, pipa dimajukan setelah alat bor (bit); untuk ini mereka dibuat dengan diameter lebih kecil dari yang sebelumnya. Pipa-pipa ini kemudian disebut selubung. Desainnya ditingkatkan dari waktu ke waktu: alih-alih terpaku, mereka menjadi mulus dengan ujung berulir.
Sumur pertama di Amerika Serikat dibor untuk ekstraksi air asin di dekat kota Charleston di Virginia Barat pada tahun 1806. Kentucky tidak sengaja menemukan minyak.
Penyebutan pertama penggunaan pengeboran untuk eksplorasi minyak berasal dari tahun 30-an abad ke-19. Di Taman, sebelum menggali sumur minyak, mereka melakukan pengintaian awal dengan bor. Saksi mata meninggalkan keterangan sebagai berikut: “Ketika mereka berencana untuk menggali sumur di tempat baru, mereka pertama-tama mencoba bumi dengan bor, mendorongnya dan menambahkan sedikit air sehingga lebih mudah masuk dan setelah mengeluarkannya, akan ada minyak, maka di tempat ini mereka mulai menggali lubang segi empat".
Pada bulan Desember 1844, seorang anggota Dewan Administrasi Utama Wilayah Transkaukasia V.N. Semyonov mengirim laporan kepada pimpinannya, di mana ia menulis tentang perlunya ... memperdalam beberapa sumur dengan bor ... dan eksplorasi ulang minyak juga dengan bor antara sumur Balakhani, Baibat dan Kabristan. Sebagai V.N. Semenov, ide ini disarankan kepadanya oleh manajer ladang minyak dan garam Baku dan Shirvan, insinyur pertambangan N.I. Voskoboynikov. Pada tahun 1846, Departemen Keuangan mengalokasikan dana yang diperlukan dan pengeboran dimulai. Hasil pengeboran disebutkan dalam memorandum Gubernur Kaukasus, Count Vorontsov, tertanggal 14 Juli 1848: "... sebuah sumur dibor di Bibi-Heybat, di mana minyak ditemukan." Dulu sumur minyak pertama di dunia!
Sesaat sebelum ini, pada tahun 1846, insinyur Prancis Fauvel mengusulkan metode untuk pembersihan sumur secara terus menerus - mereka pencucian. Inti dari metode ini adalah bahwa dari permukaan bumi melalui pipa berlubang, air dipompa ke dalam sumur, membawa potongan-potongan batu ke atas. Metode ini mendapat pengakuan dengan sangat cepat, karena. tidak memerlukan pengeboran untuk dihentikan.
Sumur minyak pertama di Amerika Serikat dibor pada tahun 1859. Hal ini dilakukan di daerah Titesville, Pennsylvania oleh E. Drake, yang mengerjakan instruksi dari Seneca Oil Company. Setelah dua bulan bekerja terus menerus, para pekerja E. Drake berhasil mengebor sumur yang hanya sedalam 22 m, tetapi masih menghasilkan minyak. Sampai saat ini, sumur ini dianggap yang pertama di dunia, tetapi dokumen yang ditemukan tentang pekerjaan yang dipimpin oleh V.N. Semenov memulihkan keadilan sejarah.
Banyak negara menghubungkan kelahiran industri minyak mereka dengan pengeboran sumur pertama yang menghasilkan minyak industri. Jadi, di Rumania, penghitungan mundur telah dilakukan sejak 1857, di Kanada - sejak 1858, di Venezuela - sejak 1863. Di Rusia, untuk waktu yang lama diyakini bahwa sumur minyak pertama dibor pada tahun 1864 di Kuban di tepi sungai. dari sungai. Kudako di bawah pimpinan Kolonel A.N. Novosiltsev. Oleh karena itu, pada tahun 1964, peringatan 100 tahun industri perminyakan dalam negeri diperingati secara khidmat di negara kita, dan sejak itu setiap tahun “Hari Buruh Industri Minyak dan Gas Bumi” diperingati.
Jumlah sumur yang dibor di ladang minyak pada akhir abad ke-19 tumbuh pesat. Jadi di Baku pada tahun 1873 ada 17 di antaranya, pada tahun 1885 - 165, pada tahun 1890 - 356, pada tahun 1895 - 604, kemudian pada tahun 1901 - 1740. Pada saat yang sama, kedalaman sumur minyak meningkat secara signifikan. Jika pada tahun 1872 adalah 55 ... 65 m, maka pada tahun 1883 adalah 105 ... 125 m, dan pada akhir abad ke-19. mencapai 425...530 m.
Di akhir tahun 80-an. abad terakhir di dekat New Orleans (Louisiana, AS) diterapkan pengeboran putar untuk minyak dengan pembilasan sumur dengan larutan tanah liat. Di Rusia, pengeboran putar dengan pembilasan pertama kali digunakan di dekat kota Grozny pada tahun 1902 dan minyak ditemukan pada kedalaman 345 m.
Awalnya, pengeboran putar dilakukan dengan memutar mata bor bersama dengan seluruh tali bor langsung dari permukaan. Namun, pada kedalaman sumur yang besar, berat kolom ini sangat besar. Oleh karena itu, pada abad ke-19 proposal pertama untuk penciptaan motor lubang bawah, itu. motor ditempatkan di bagian bawah pipa bor tepat di atas mata bor. Sebagian besar dari mereka tetap tidak terealisasi.
Untuk pertama kalinya dalam praktik dunia, seorang insinyur Soviet (kemudian menjadi anggota Akademi Ilmu Pengetahuan Uni Soviet) M.A. Kapelyushnikov pada tahun 1922 ditemukan bor turbo, yang merupakan turbin hidrolik satu tahap dengan roda gigi planet. Turbin digerakkan oleh cairan pencuci. Pada tahun 1935...1939. desain turbodrill diperbaiki oleh sekelompok ilmuwan yang dipimpin oleh P.P. Shumilova. Turbodrill yang diusulkan oleh mereka adalah turbin multi-tahap tanpa gearbox.
Pada tahun 1899, itu dipatenkan di Rusia bor listrik, yang merupakan motor listrik yang dihubungkan dengan pahat dan digantungkan pada seutas tali. Desain modern bor listrik dikembangkan pada tahun 1938 oleh insinyur Soviet A.P. Ostrovsky dan N.V. Aleksandrov, dan sudah pada tahun 1940 sumur pertama dibor dengan bor listrik.
Pada tahun 1897, di Samudra Pasifik di daerah sekitar. Somerland (California, AS) pertama kali diimplementasikan pengeboran lepas pantai. Di negara kita, sumur lepas pantai pertama dibor pada tahun 1925 di Teluk Ilyich (dekat Baku) di pulau buatan. Pada tahun 1934 N.S. Timofeev tentang. Artem di Laut Kaspia dilakukan pengeboran sumur, di mana beberapa sumur (kadang-kadang lebih dari 20) dibor dari situs umum. Selanjutnya, metode ini menjadi banyak digunakan dalam pengeboran di ruang terbatas (di antara rawa-rawa, platform pengeboran lepas pantai, dll.).
Sejak awal tahun 60-an, untuk mempelajari struktur dalam Bumi, dunia mulai menggunakan pengeboran ultra-dalam.
2. Konsep sumur
Pengeboran- ini adalah proses membangun sumur dengan menghancurkan batu. dengan baik disebut pertambangan bagian bulat, dibangun tanpa orang mengaksesnya, di mana panjangnya berkali-kali lebih besar dari diameternya.
Bagian atas sumur disebut mulut, bawah - pembantaian, permukaan samping - dinding dan ruang yang dibatasi oleh dinding - lubang sumur. Panjang sumur adalah jarak dari mulut ke bawah sepanjang sumbu batang, dan kedalaman adalah proyeksi panjang ke sumbu vertikal. Panjang dan kedalaman secara numerik sama hanya untuk sumur vertikal. Namun, mereka tidak bertepatan untuk sumur yang menyimpang dan menyimpang.
Elemen desain sumur ditunjukkan pada gambar. 1. Bagian awal Saya sumur disebut arah. Karena kepala sumur terletak di zona batuan yang mudah tererosi, maka harus diperkuat. Dalam hal ini, arah dilakukan sebagai berikut. Pertama, sebuah lubang dibor - sebuah sumur hingga kedalaman batuan yang stabil (4 ... 8 m). Kemudian pipa dengan panjang dan diameter yang diperlukan dipasang di dalamnya, dan ruang antara dinding lubang dan pipa diisi dengan batu puing dan dituangkan dengan mortar semen 2.
Beras. 1. Desain sumur:
Bagian hilir sumur berbentuk silinder. Tepat di belakang arah, bagian dibor hingga kedalaman 50 hingga 400 m dengan diameter hingga 900 mm. Bagian sumur ini dipasang dengan pipa selubung 1 (terdiri dari pipa baja yang disekrup), yang disebut konduktor II.
Ruang annular konduktor disemen. Dengan bantuan konduktor, batuan yang tidak stabil, lunak dan retak diisolasi, yang mempersulit proses pengeboran.
Setelah pemasangan konduktor, tidak selalu mungkin untuk mengebor sumur hingga kedalaman desain karena melewati cakrawala rumit baru atau karena kebutuhan untuk menutupi formasi produktif yang tidak direncanakan untuk dioperasikan oleh sumur ini. Dalam kasus seperti itu, kolom lain dipasang dan disemen. AKU AKU AKU, ditelepon intermediat. Jika formasi produktif yang sumurnya dimaksudkan untuk dikembangkan terletak sangat dalam, maka jumlah kolom antara mungkin lebih dari satu.
Plot Terakhir IV perbaikan sumur kolom operasional. Ini dirancang untuk mengangkat minyak dan gas dari bawah ke kepala sumur atau untuk menyuntikkan air (gas) ke dalam formasi produktif untuk menjaga tekanan di dalamnya. Untuk menghindari tumpahan minyak dan gas di cakrawala di atasnya, dan air menjadi formasi produktif, ruang antara dinding selubung produksi dan dinding sumur diisi dengan mortar semen.
Untuk mengekstrak minyak dan gas dari reservoir, berbagai metode peralatan pembukaan dan lubang bawah digunakan. Dalam kebanyakan kasus, di bagian bawah string produksi, yang terletak di reservoir, tembak (lubangi) sejumlah lubang 4 di dinding casing dan selubung semen.
Pada batuan yang stabil, zona lubang dasar sumur dilengkapi dengan berbagai filter dan tidak disemen atau tali casing mereka diturunkan hanya ke atap formasi produktif, dan pengeboran dan operasinya dilakukan tanpa memperbaiki lubang sumur.
Kepala sumur, tergantung pada tujuannya, dilengkapi dengan alat kelengkapan (kepala kolom, katup, salib, dll.).
Saat mencari, mengeksplorasi dan mengembangkan ladang minyak dan gas, sumur referensi, parametrik, struktural, prospeksi, eksplorasi, produksi, injeksi, observasi, dan lainnya dibor.
sumur referensi diletakkan di daerah yang tidak dieksplorasi dengan pengeboran, dan berfungsi untuk mempelajari komposisi dan usia batuan yang menyusunnya.
Sumur parametrik diletakkan di daerah yang relatif dipelajari untuk memperjelas struktur geologi dan prospek potensi migas.
Sumur struktural dibor untuk mengidentifikasi area yang menjanjikan dan mempersiapkannya untuk pengeboran eksplorasi.
sumur eksplorasi mereka mengebor dengan tujuan menemukan deposit industri baru minyak dan gas.
sumur eksplorasi dibor di daerah dengan potensi minyak dan gas komersial yang mapan untuk mempelajari ukuran dan struktur deposit, memperoleh data awal yang diperlukan untuk menghitung cadangan minyak dan gas, serta merancang pengembangannya.
Sumur produksi diletakkan sesuai dengan skema pengembangan deposit dan digunakan untuk memperoleh minyak dan gas dari bagian dalam bumi
sumur injeksi mereka digunakan ketika berbagai agen bertindak pada formasi yang dieksploitasi (injeksi air, gas, dll.).
sumur observasi mereka mengebor untuk mengontrol perkembangan endapan (perubahan tekanan, posisi kontak air-minyak dan gas-minyak, dll.).
Selain itu, dalam pencarian, eksplorasi dan pengembangan lapangan minyak dan gas, pemetaan, seismik, sumur khusus dan lainnya dibor.
3. Klasifikasi metode pengeboran
Klasifikasi metode pengeboran minyak dan gas ditunjukkan pada gambar. 2.
Menurut metode tumbukan pada batu Bedakan antara pengeboran mekanis dan non-mekanis. Pada pemboran mekanis, alat pemboran langsung mempengaruhi batu, menghancurkannya, dan pada pemboran non-mekanik, pemusnahan terjadi tanpa kontak langsung dengan batu dari sumber tumbukan di atasnya. Metode non-mekanis(hidrolik, termal, elektrofisika) sedang dalam pengembangan dan saat ini tidak digunakan untuk pengeboran sumur minyak dan gas.
Metode mekanis pengeboran dibagi menjadi perkusi dan putar.
Beras. 2. Klasifikasi metode pengeboran sumur minyak dan gas
Selama pengeboran impak, penghancuran batu dilakukan dengan sedikit 1 yang tergantung pada tali (Gbr. 3). Alat bor juga mencakup batang kejut 2 dan kunci tali 3. Alat ini digantung pada tali 4, yang dilempar ke atas balok 5 yang dipasang pada tiang (tidak diperlihatkan secara konvensional). gerak bolak-balik alat pengeboran menyediakan mesin bor 6.
Beras. 3. Skema pengeboran perkusi:
1 - pahat; 2 - batang kejut; 3 - kunci tali;
4 - tali; 5 - blok; 6 - mesin bor.
Saat sumur semakin dalam, tali diperpanjang. Silinder sumur dipastikan dengan memutar bit selama operasi.
Untuk membersihkan bagian bawah dari batu yang hancur, alat bor dikeluarkan secara berkala dari sumur, dan diturunkan ke dalamnya. gayung, seperti ember panjang dengan katup di bagian bawah. Ketika bailer direndam dalam campuran cairan (formasi atau dituangkan dari atas) dan partikel batuan yang dibor, katup terbuka dan gayung diisi dengan campuran ini. Ketika gayung dinaikkan, katup menutup dan campuran diambil.
Setelah pembersihan lubang dasar selesai, alat pengeboran diturunkan lagi ke dalam sumur dan pengeboran dilanjutkan.
Untuk menghindari runtuhnya dinding sumur, pipa selubung diturunkan ke dalamnya, yang panjangnya bertambah saat lubang dasar semakin dalam.
Saat ini, ketika mengebor sumur minyak dan gas, pengeboran impak tidak digunakan di negara kita.
Sumur minyak dan gas dibangun dengan menggunakan pengeboran putar. Dengan metode ini, batuan tidak dihancurkan oleh tumbukan, tetapi dihancurkan oleh bit yang berputar, yang dikenai beban aksial. Torsi ditransmisikan ke bit atau dari permukaan dari rotator (rotor) melalui string bor (pengeboran putar) atau dari motor downhole (turbodrill, bor listrik, motor sekrup) yang dipasang langsung di atas bit.
Ini adalah turbin hidrolik yang digerakkan oleh cairan pengeboran yang disuntikkan ke dalam sumur. bor listrik adalah motor tahan cairan yang ditenagai oleh kabel dari permukaan. - ini semacam pembantaian mesin hidrolik, di mana mekanisme sekrup digunakan untuk mengubah energi aliran fluida pembilasan menjadi energi mekanik gerak rotasi.
Dengan sifat penghancuran batu di bagian bawah Bedakan antara pengeboran terus menerus dan inti. Pada kontinu pengeboran, penghancuran batu dilakukan di seluruh area wajah. Kolinsky pengeboran menyediakan penghancuran batu hanya di sepanjang cincin untuk mengekstrak inti- sampel batuan berbentuk silinder untuk seluruh atau sebagian panjang sumur. Dengan bantuan pengambilan sampel inti, sifat-sifat, komposisi dan struktur batuan, serta komposisi dan sifat-sifat fluida yang menjenuhkan batuan, dipelajari.
Semua mata bor diklasifikasikan menjadi tiga jenis:
- potongan-potongan tindakan pemotongan dan pemotongan, menghancurkan batu dengan pisau (blade bit);
- potongan-potongan tindakan penghancuran dan geser, menghancurkan batu dengan gigi yang terletak di kerucut (cone bit);
- bit tindakan pemotongan-abrasi, menghancurkan batu dengan butiran berlian atau pin paduan keras, yang terletak di bagian akhir bit (bit berlian dan paduan keras).
4. Rig pengeboran, peralatan dan peralatan
Pengeboran sumur dilakukan dengan bantuan rig pengeboran, peralatan dan perkakas.
Alat pengeboran
Sebagai motor lubang bawah saat mengebor, bor turbo, bor listrik, dan mesin sekrup digunakan, dipasang langsung di atas mata bor.
(Gbr. 15) adalah turbin multi-tahap (hingga 350 tahap), setiap tahap terdiri dari stator yang terhubung secara kaku ke badan turbodrill dan rotor yang dipasang pada poros turbodrill. Aliran fluida, mengalir turun dari bilah stator, mengalir ke bilah rotor, memberikan sebagian energinya untuk menciptakan torsi, kembali mengalir ke bilah stator, dll. Meskipun setiap tahap turbodrill berkembang relatif momen kecil, karena jumlahnya yang besar, daya total pada poros turbodrill cukup untuk mengebor batuan yang paling keras.
Beras. 15. Bor turbo:
a - pandangan umum; b - tahap turbodrill; 1 - poros; 2 - tubuh; 3 - rotor; 4 - stator.
Pada pengeboran turbin sebagai fluida kerja, digunakan fluida pembilas, bergerak dari permukaan bumi sepanjang drill string ke turbodrill. Sedikit terhubung dengan kaku ke poros turbodrill. Ini berputar secara independen dari string bor.
Saat mengebor menggunakan bor listrik motor listrik ditenagai melalui kabel yang dipasang di dalam pipa bor. Dalam hal ini, hanya poros motor yang berputar bersama dengan mata bor, sementara badan dan tali bor tetap diam.
Elemen utama mesin sekrup(Gbr. 16) adalah stator dan rotor. Stator dibuat dengan menerapkan karet khusus ke permukaan bagian dalam rumah baja. Permukaan bagian dalam stator memiliki bentuk permukaan heliks multi-start. Dan rotor terbuat dari baja dalam bentuk sekrup multi-start. Jumlah garis heliks adalah satu kurang dari stator.
Beras. 16. Motor sekrup:
a - pandangan umum; b - rongga yang terbentuk antara rotor (sekrup) dan stator;
1 - sub; 2 - badan bagian motor; 3 - stator; 4 - rotor;
5 - poros kardan; 6 - rumah spindel; 7 - segel ujung;
8 - bantalan kontak sudut multi-baris; 9 - karet radial
dukungan logam; 10 - poros spindel.
Rotor terletak di stator dengan eksentrisitas. Karena ini, dan juga karena perbedaan jumlah entri dalam garis heliks stator dan rotor, permukaan kontaknya membentuk serangkaian rongga tertutup - gerbang antara ruang tekanan tinggi di ujung atas rotor dan tekanan rendah. di ujung bawah. Pintu air memblokir aliran bebas cairan melalui motor, dan yang paling penting, di dalamnya tekanan fluida menciptakan torsi yang ditransmisikan ke bit.
alat pengeboran
Alat, digunakan dalam pengeboran, dibagi menjadi: dasar(bit) dan bantu(pipa bor, sambungan alat, pemusat):
pahat
/Alat pengeboran dasar/
pahat ada berbilah, kerucut, berlian dan karbida.
Mata pisau(Gbr. 17) tersedia dalam tiga tipe: two-blade, three-blade dan multi-blade. Di bawah aksi beban di bagian bawah, bilah mereka memotong batu, dan di bawah pengaruh torsi, mereka memotongnya. Ada lubang di badan mata bor di mana cairan dari tali bor diarahkan ke dasar sumur dengan kecepatan minimal 80 m/s. Mata pisau digunakan saat mengebor batuan lunak yang sangat plastis dengan kecepatan keliling terbatas (biasanya saat pengeboran putar).
Beras. 17. Pahat Dayung:
1 - kepala dengan utas penghubung; 2 - tubuh; 3 - bilah;
4 - lubang pembilasan; 5 - lapisan paduan keras;
6 - ujung tombak.
Bit rol(Gbr. 18) tersedia dengan satu, dua, tiga, empat dan bahkan enam pemotong. Namun, bit tricone yang paling banyak digunakan. Saat bit berputar, pemotong, berguling di sepanjang bagian bawah, melakukan gerakan rotasi yang rumit dengan geser. Pada saat yang sama, gigi pemotong menghantam batu, menghancurkan dan memotongnya. Bit rol berhasil digunakan dalam pengeboran putar batuan dengan berbagai macam sifat fisik dan mekanik. Mereka terbuat dari baja berkualitas tinggi dengan perawatan kimia-termal berikutnya dari bagian yang paling kritis dan aus, dan gigi itu sendiri terbuat dari paduan keras.
Beras. 18. Kerucut bit:
1 - tubuh dengan kepala berulir;
2 - cakar dengan dukungan; 3 - kerucut.
bit berlian(Gbr. 19) terdiri dari badan baja dan kepala pembawa intan yang terbuat dari muatan karbida bubuk. Bagian tengah bit adalah permukaan cekung berbentuk kerucut dengan saluran untuk mengalirkan cairan, dan zona perifer adalah permukaan bola, berubah menjadi silinder di sisinya.
Beras. 19. Pahat Berlian:
1 - tubuh; 2 - matriks; 3 - butir berlian.
Ada tiga jenis bit berlian: heliks, radial dan melangkah. Dalam berlian spiral bit, bagian kerja memiliki spiral yang dilengkapi dengan berlian dan lubang pembilasan. Bit jenis ini dirancang untuk pengeboran turbin batuan abrasif rendah dan sedang. Berlian radial bit memiliki permukaan kerja dalam bentuk tonjolan radial dalam bentuk sektor, dilengkapi dengan berlian; saluran pembilasan ditempatkan di antara mereka. Mata bor jenis ini dirancang untuk mengebor batuan abrasif rendah dengan kekerasan sedang dan batuan keras baik dengan metode pengeboran putar maupun turbin. berlian melangkah bit memiliki permukaan kerja berbentuk langkah. Mereka digunakan baik untuk metode pengeboran putar dan turbin saat menggerakkan batuan lunak dan keras dengan tingkat abrasif rendah.
Penggunaan mata bor berlian memberikan kecepatan pengeboran yang tinggi, mengurangi kelengkungan sumur. Tidak adanya bantalan gelinding dan ketahanan aus yang tinggi dari berlian meningkatkan masa pakainya hingga 200...250 jam operasi terus menerus. Ini mengurangi jumlah perjalanan. Satu mata bor berlian bisa mengebor sebanyak 15...20 mata bor kerucut.
pahat karbida berbeda dari berlian karena bukannya berlian, mereka diperkuat dengan paduan superhard.
Bor pipa, kunci, centralizer, dll.
/Alat bantu pengeboran/
Pengeboran pipa dirancang untuk mentransmisikan putaran ke mata bor (selama pengeboran putar) dan untuk merasakan momen reaktif mesin saat mengebor dengan motor lubang bawah, menciptakan beban pada mata bor, memberi makan cairan pengeboran ke dasar sumur untuk membersihkannya dari batu bor dan mendinginkan mata bor, angkat mata bor yang aus dari sumur dan turunkan yang baru, dll.
Pipa bor dicirikan oleh peningkatan ketebalan dinding dan, sebagai suatu peraturan, memiliki benang yang meruncing di kedua sisi. Pipa-pipa tersebut saling berhubungan dengan bantuan kunci bor (Gbr. 20). Untuk daya tahan koneksi berulir ujung pipa menebal. Menurut metode pembuatannya, pipa bisa padat (Gbr. 21) dan dengan ujung penghubung yang dilas (Gbr. 22). Untuk pipa padat, penebalan ujungnya dapat dilakukan dengan memasang ke dalam atau ke luar.
Beras. 20. Kunci bor:
a - kunci puting; b - penguncian kopling
Beras. 21. Bor pipa dengan ujung penghubung yang dilas
Beras. 22. Bor pipa dengan ujung yang tidak rata:
a - mendarat di dalam; b - mendarat di luar.
Untuk pengeboran dalam, digunakan pipa bor baja dan paduan ringan dengan diameter nominal 60, 73, 89.102.114.127 dan 140 mm. Ketebalan dinding pipa adalah dari 7 hingga 11 mm, dan panjangnya adalah 6, 8 dan 11,5 m.
Seiring dengan penggunaan biasa kerah bor(UBT). Tujuannya adalah untuk membuat bobot pada mata bor dan meningkatkan stabilitas bagian bawah tali bor.
Pipa timah dirancang untuk mentransfer rotasi dari rotor ke string bor (pengeboran putar) dan untuk mentransfer momen reaktif dari string bor ke rotor (saat pengeboran dengan motor downhole). Tabung ini biasanya berbentuk persegi dan melewati lubang persegi di rotor. Di satu ujung, Kelly terhubung ke putar, dan di ujung lainnya, ke pipa bor bundar konvensional.
Panjang permukaan kelly menentukan kemungkinan interval pengeboran sumur tanpa ekstensi pahat. Dengan panjang pipa utama yang kecil, jumlah ekstensi dan waktu yang dihabiskan untuk pengeboran sumur meningkat, dan dengan panjang yang panjang, transportasinya menjadi lebih sulit.
Kunci bor dirancang untuk menghubungkan pipa. Kunci terdiri dari puting kunci (Gbr. 20 a) dan selongsong kunci (Gbr. 20 b).
Sistem alat dan perlengkapan multi-tautan kontinu yang terletak di bawah putar (kelly, pipa bor dengan kunci, motor lubang bawah, dan mata bor) disebut tali bor. Elemen tambahannya adalah sub untuk berbagai keperluan, pelindung, pemusat, stabilisator, kalibrator, peredam kejut hampir-bit.
Subs digunakan untuk menghubungkan elemen dalam string bor dengan ulir dari berbagai profil, dengan ujung berulir yang sama (ulir puting susu, ulir kopling-kopling), untuk menghubungkan motor lubang bawah, dll. Menurut tujuannya, kapal selam dibagi menjadi kapal selam transisi, kopling dan puting.
pelindung dirancang untuk melindungi pipa bor dan kunci sambungan dari keausan permukaan, dan tali casing- dari menyeka saat memindahkan pipa bor di dalamnya. Biasanya, pelindung yang pas digunakan, yang merupakan cincin karet yang dikenakan pada tali bor di atas kunci. Diameter luar pelindung melebihi diameter kunci.
Sentralisasi digunakan untuk mencegah kelengkungan batang saat mengebor sumur. Elemen samping pemusat menyentuh dinding sumur, memastikan keselarasan tali bor dengannya. Sentralisasi terletak di string pipa bor di tempat-tempat tikungan yang diharapkan. Kehadiran pemusat memungkinkan penggunaan beban aksial yang lebih tinggi pada bit.
Stabilisator- ini adalah elemen pemusatan penyangga untuk menjaga keselarasan kaku dari string bor di lubang sumur di beberapa bagian yang paling kritis. Mereka berbeda dari pemusat dalam panjang yang lebih besar.
Kalibrator- sejenis alat pemotong batu untuk memproses dinding sumur dan mempertahankan diameter nominal batangnya jika mata bornya aus. Dalam string bor, kalibrator ditempatkan tepat di atas mata bor. Ini secara bersamaan bertindak sebagai pemusat dan meningkatkan kondisi operasi bit.
Peredam kejut sedikit(downhole damper) dipasang pada drill string antara mata bor dan kerah bor untuk meredam getaran frekuensi tinggi yang terjadi saat mata bor beroperasi di dasar sumur. Mengurangi beban getaran menyebabkan peningkatan umur bor dan mata bor. Ada dua jenis perangkat peredam: peredam kejut aksi mekanis, termasuk elemen elastis (pegas baja, cincin karet dan bola) dan peredam getaran aksi hidrolik atau hidromekanis.
Contoh tata letak tali bor
Contoh tata letak tali bor ditunjukkan pada gambar. 23.
Beras. 23. Tata letak tali bor:
1 - batang putar; 2 - utas delapan utas kiri; 3 - kapal selam putar; 4 - utas pengunci kiri; 5 - sub batang atas (PShV); 6 - pipa terkemuka; 7 - utas delapan utas kanan; 8 - sub batang bawah (PShN); 9 - utas pengunci kanan; 10 - kapal selam keselamatan (PBP); 11 - kunci utas; 12 - mengunci kopling; 13 - utas delapan poin; 14 - pipa bor sepanjang 6 m; 15 - kopling; 16 - kunci puting; 17 - cincin pengaman; 18 - pipa bor berat (DC); 19 - sub dua soket (PBM); 20 - pemusat; 21 - sub adaptor; 22 - kerah bor dekat-bit; 23 - pahat
5. Siklus konstruksi sumur
Siklus konstruksi sumur meliputi:
- pekerjaan persiapan;
- pemasangan menara dan peralatannya;
- persiapan untuk pengeboran;
- proses pengeboran;
- memperbaiki sumur dengan pipa selubung dan groutingnya;
- pembukaan formasi dan pengujian aliran masuk minyak dan gas.
Selama pekerjaan persiapan mereka memilih tempat untuk rig pengeboran, meletakkan jalan akses, menurunkan pasokan listrik, pasokan air dan sistem komunikasi. Jika medannya tidak rata, maka sebuah situs direncanakan.
Pemasangan menara dan peralatan diproduksi sesuai dengan skema penempatannya yang diadopsi untuk kondisi khusus ini. Mereka mencoba menempatkan peralatan sedemikian rupa untuk memastikan keamanan dalam pengoperasian, kemudahan perawatan, biaya konstruksi yang rendah dan pekerjaan instalasi dan kekompakan dalam penataan semua elemen rig pengeboran.
Dalam kasus umum (Gbr. 24), rotor 3 terletak di tengah rig pengeboran 1, dan winch 2 terletak di sebelahnya, dan mixer tanah liat 17. Di sisi berlawanan dari winch ada rak alat kecil 14, rak 5 untuk memasang pipa bor 4, menerima jembatan 12, platform untuk bit bekas 7 dan platform alat memancing 10 (digunakan untuk menghilangkan kecelakaan). Selain itu, stan utilitas 8, platform alat 6, sistem pembersihan 15 untuk cairan pengeboran bekas dan wadah cadangan 16 untuk menyimpan cairan pengeboran, bahan kimia dan air terletak di sekitar rig pengeboran.
Beras. 24. Tata letak peralatan yang khas,
alat, suku cadang dan bahan di rig pengeboran:
1 - rig pengeboran; 2 - derek; 3 - rotor; 4 - pipa bor;
5 - rak; 6 - platform alat; 7 - situs belanja
bit; 8 - stan utilitas; 9 - situs pertanian tanah liat; 10 - taman bermain
alat memancing; 11 - platform untuk bahan bakar dan pelumas;
12 - menerima jalan setapak; 13 - meja kerja tukang kunci; 14 - rak alat ringan;
15 - sistem pembersihan; 16 - wadah cadangan; 17 - pengaduk tanah liat;
18 - penggerak daya; 19 - pompa
Ada metode pemasangan rig pengeboran berikut: unit demi unit, blok kecil dan blok besar.
Dengan metode unit-bijaksana, rig pengeboran dirakit dari unit terpisah, untuk pengiriman yang digunakan transportasi jalan, kereta api atau udara.
Dengan metode blok kecil, rig pengeboran dirakit dari 16...20 blok kecil. Masing-masing adalah pangkalan di mana satu atau lebih unit instalasi dipasang.
Dengan metode blok besar, pemasangannya dirangkai dari 2...4 blok yang masing-masing menggabungkan beberapa unit dan unit rig pengeboran.
Metode blok memberikan tingkat pemasangan rig pengeboran yang tinggi dan kualitas pekerjaan pemasangan. Dimensi balok tergantung pada metode, kondisi, dan jarak pengangkutannya.
Setelah itu, blok perjalanan dengan blok mahkota, putar dan pipa terkemuka dipasang secara berurutan, dan selang tekanan dipasang ke putar. Selanjutnya, pemusatan menara diperiksa: pusatnya harus bertepatan dengan pusat rotor.
Persiapan pengeboran termasuk perangkat arah I (Gbr. 1) dan uji coba rig pengeboran.
Beras. 1. Desain sumur:
1 - pipa selubung; 2 - batu semen; 3 - lapisan;
4 - perforasi di selubung batu semen;
saya - arah; II - konduktor; III - kolom perantara;
IV - rangkaian produksi.
Tujuan dari arah dijelaskan di atas. Ujung atasnya terhubung ke sistem perawatan yang dirancang untuk menghilangkan serpihan dari cairan pengeboran yang berasal dari sumur, dan kemudian memasoknya ke tangki penerima pompa lumpur.
Kemudian lubang untuk pipa utama dibor dan pipa selubung diturunkan ke dalamnya.
Rig pengeboran dilengkapi dengan mata bor, pipa bor, tangan dan alat bantu, bahan bakar dan pelumas, pasokan air, tanah liat dan bahan kimia. Selain itu, tidak jauh dari rig terdapat ruangan untuk istirahat dan makan, pengering untuk overall dan ruangan untuk analisa fluida pemboran.
Selama pengeboran uji, kinerja semua elemen dan komponen rig pengeboran diperiksa.
Proses pengeboran mulailah dengan memasang pahat ke tabung persegi terdepan pada awalnya. Dengan memutar rotor, rotasi ditransmisikan ke bit melalui pipa terkemuka.
Selama pengeboran ada keturunan terus menerus (pengiriman) alat pengeboran sehingga bagian dari berat bagian bawahnya dipindahkan ke bit untuk memastikan penghancuran batu yang efektif.
Selama pengeboran, sumur secara bertahap diperdalam. Setelah kelly semua masuk ke dalam sumur, perlu untuk membangun string pipa bor. Ekstensi dilakukan sebagai berikut. Pertama berhenti mencuci. Selanjutnya alat bor diangkat keluar dari sumur sehingga Kelly benar-benar keluar dari rotor. Menggunakan pegangan baji pneumatik, pahat digantung di rotor. Selanjutnya, pipa utama dibuka dari tali bor dan, bersama dengan putar, diturunkan ke dalam lubang - sumur yang sedikit miring sedalam 15 ... 16 m, terletak di sudut rig pengeboran. Setelah itu, kait terputus dari putar, pipa lain yang sudah disiapkan sebelumnya digantung di kait, terhubung ke tali bor yang tergantung pada rotor, tali dilepas dari rotor, diturunkan ke dalam sumur dan digantung lagi di rotornya. Kait pengangkat dihubungkan lagi ke putar dan diangkat dengan pipa utama dari lubang. Kelly terhubung ke senar bor, yang terakhir dilepas dari rotor, pompa lumpur dihidupkan dan mata bor dengan hati-hati dibawa ke bawah. Setelah itu, pengeboran dilanjutkan.
Saat mengebor, bit secara bertahap aus dan perlu untuk menggantinya. Untuk melakukan ini, alat bor, seperti dalam kasus ekstensi, dinaikkan ke ketinggian yang sama dengan panjang kelly, tergantung pada rotor, kelly terputus dari senar dan diturunkan dengan putar ke dalam lubang. Kemudian senar bor dinaikkan ke ketinggian yang sama dengan panjang dudukan bor, senar digantung di rotor, dudukan dilepaskan dari senar dan ujung bawahnya dipasang pada platform khusus - kandil, dan bagian atas ujungnya ditempatkan pada braket khusus yang disebut jari. Dalam urutan ini, semua lilin diangkat dari sumur. Setelah itu, bit diganti dan penurunan alat bor dimulai. Proses ini dilakukan dengan urutan kebalikan dari pengangkatan alat bor dari sumur.
Memperbaiki sumur dengan pipa casing dan groutingnya dilakukan sesuai dengan skema yang ditunjukkan pada gambar. 1. Tujuan dari memasukkan anulus senar casing adalah untuk mengisolasi formasi produktif.
Meskipun formasi produktif sudah tersingkap selama proses pemboran, namun diisolasi dengan pipa selubung dan sumbat sehingga penetrasi minyak dan gas ke dalam sumur tidak mengganggu pemboran selanjutnya. Setelah selesai pengeboran untuk memastikan aliran minyak dan lapisan produktif gas dibuka kembali metode perforasi. Kemudian sumur sedang dikembangkan itu. menyebabkan masuknya minyak dan gas ke dalamnya. Mengapa mengurangi tekanan cairan pengeboran di bagian bawah dengan salah satu cara berikut:
- pembilasan- penggantian cairan pengeboran yang mengisi lubang sumur setelah pengeboran dengan cairan yang lebih ringan - air atau minyak;
- piston(swabing) - menurunkan level cairan di dalam sumur dengan menurunkan ke dalam tubing dan mengangkat piston khusus (swab) pada kabel baja. Piston memiliki katup yang terbuka saat turun dan memungkinkan cairan mengisi tabung melaluinya. Saat mengangkat, katup menutup, dan seluruh kolom cairan di atas piston dibawa ke permukaan.
Metode yang sebelumnya digunakan untuk mengurangi tekanan cairan pengeboran di bagian bawah, mendorong dengan gas terkompresi dan aerasi (jenuhnya larutan dengan gas) kini telah ditinggalkan karena alasan keamanan.
Dengan demikian, pengembangan sumur, tergantung pada kondisi tertentu, dapat memakan waktu dari beberapa jam hingga beberapa bulan.
Setelah munculnya minyak dan gas, sumur diterima oleh operator, dan derek dipindahkan beberapa meter untuk mengebor sumur berikutnya dari pad atau diseret ke pad berikutnya.
6. Mencuci sumur
Pembilasan sumur adalah salah satu operasi paling kritis yang dilakukan selama pengeboran. Awalnya, tujuan pembilasan terbatas pada pembersihan lubang dasar dari partikel stek dan pemindahannya dari sumur, serta mendinginkan mata bor. Namun, seiring berkembangnya industri pemboran, fungsi fluida pemboran pun semakin berkembang. Sekarang ini termasuk:
- penghapusan partikel stek dari sumur;
- transmisi daya ke turbodrill atau motor sekrup;
- pencegahan masuknya minyak, gas dan air ke dalam sumur;
- menjaga partikel batuan yang dibor dalam suspensi saat sirkulasi dihentikan;
- pendinginan dan pelumasan bagian-bagian bit yang digosok;
- pengurangan gesekan pipa bor terhadap dinding sumur;
- pencegahan runtuhnya batu dari dinding sumur;
- penurunan permeabilitas dinding sumur karena pengerasan kulit.
Dengan demikian, cairan pengeboran harus memenuhi: sejumlah persyaratan:
- melakukan fungsi yang ditugaskan;
- tidak memiliki efek berbahaya pada alat bor dan motor downhole (korosi, keausan abrasif, dll.);
- mudah dipompa dan dibersihkan dari lumpur dan gas;
- aman bagi petugas pelayanan dan lingkungan;
- nyaman untuk persiapan dan pembersihan;
- tersedia, murah, dan dapat digunakan kembali.
- Pemurnian cairan pengeboran
Jenis cairan pengeboran
Jenis cairan pengeboran
Dalam pengeboran putar sumur minyak dan gas, cairan berikut digunakan sebagai cairan pembilasan:
agen berbasis air (air proses, cairan pengeboran alami, tanah liat dan lumpur non-tanah liat);
agen berbasis hidrokarbon;
agen pengemulsi;
agen gas dan aerasi.
air teknis- cairan pembilasan yang paling mudah diakses dan murah. Memiliki viskositas rendah, mudah dipompa, dengan baik menghilangkan stek dari dasar sumur dan mendinginkan sedikit lebih baik daripada cairan lainnya. Namun, ia tidak dapat menahan partikel stek (terutama ketika sirkulasi dihentikan), tidak membentuk kerak yang mengeras di dinding sumur, diserap dengan baik oleh formasi bertekanan rendah, menyebabkan batuan lempung membengkak, dan memperburuk permeabilitas reservoir minyak dan gas. .
lumpur pengeboran alami disebut suspensi berair yang terbentuk di dalam sumur sebagai hasil dispersi potongan batuan yang dibor di atas air.
Keuntungan utama menggunakan cairan pengeboran alami adalah pengurangan yang signifikan dalam kebutuhan bahan impor untuk persiapan dan pemrosesannya, yang mengarah pada solusi yang lebih murah. Namun, kualitas dan sifat-sifatnya tergantung pada komposisi mineralogi dan sifat tanah liat yang dibor, metode dan cara pengeboran, dan jenis alat pemotong batu. Seringkali mereka mengandung kandungan partikel abrasif yang tinggi. Oleh karena itu, cairan pengeboran alami digunakan dalam kasus di mana kondisi geologi dan stratigrafi tidak memerlukan cairan pengeboran berkualitas tinggi.
Cairan pengeboran tanah liat paling banyak digunakan dalam pengeboran sumur. Untuk pengeboran, tiga kelompok mineral lempung paling menarik: bentonit (montmorillonit, beidellite, nontroit, saponit, dll.), kaolin (kaolinit, haloisit, nakrit, dll.) dan hidromikaseus (illit, braviasit, dll.). Montmorillonit dan mineral bentonit lainnya memiliki kualitas terbaik dalam hal persiapan cairan pengeboran. Jadi, dari 1 ton tanah liat bentonit, sekitar 15 m 3 larutan tanah liat berkualitas tinggi dapat diperoleh, sedangkan dari tanah liat kualitas sedang - 4 ... 8 m 3, dan dari tanah liat tingkat rendah - kurang dari 3 m 3 .
Solusi tanah liat melapisi dinding sumur, membentuk kerak padat tipis, yang mencegah penetrasi filtrat ke dalam formasi. Kepadatan dan viskositasnya sedemikian rupa sehingga lumpur menahan serbuk bor bahkan saat diam, mencegahnya mengendap di lubang dasar selama jeda dalam pembilasan. Solusi tanah liat tertimbang, menciptakan tekanan balik yang besar pada formasi, mencegah penetrasi air formasi, minyak dan gas ke dalam sumur dan mengalir terbuka selama pengeboran. Namun, untuk alasan yang sama, sulit untuk memisahkan partikel batuan dalam sistem sirkulasi fluida pemboran.
Cairan pengeboran berbasis air lainnya juga digunakan: low-clay (untuk mengebor lapisan atas batuan yang lapuk dan retak), saline (saat mengebor di lapisan tebal batuan yang mengandung garam), inhibited (diperlakukan dengan bahan kimia untuk mencegah pembengkakan pada lubang bor. batuan dan pengayaan berlebihan larutan dengan fase padat) dan lain-lain.
Ke bukan tanah liat termasuk cairan pengeboran yang disiapkan tanpa menggunakan tanah liat. Cairan Pengeboran Padat Kental Clayless disiapkan berbasis air. Fasa terdispersi di dalamnya diperoleh secara kimia, sebagai hasil interaksi ion magnesium dalam larutan dengan alkali NaOH atau Ca(OH)2. Reaksi kimia mengarah pada pembentukan partikel mikroskopis magnesium hidroksida Mg(OH) 2 dalam larutan. Solusinya memperoleh konsistensi seperti gel dan, setelah perawatan kimia, berubah menjadi sistem yang stabil terhadap sedimentasi. Solusi semacam itu mempertahankan sifat struktural dan mekaniknya dengan mineralisasi apa pun. Oleh karena itu, digunakan dalam kasus di mana diperlukan untuk memastikan stabilitas tinggi dinding sumur, tetapi sulit untuk mengontrol dan mengatur salinitas larutan.
Jenis lain dari cairan pengeboran non-tanah liat adalah larutan biopolimer. Biopolimer diperoleh dengan memaparkan strain bakteri tertentu ke polisakarida. Sifat lumpur biopolimer mudah dikendalikan seperti lumpur bor bentonit terbaik. Namun, beberapa dari mereka memiliki efek flokulasi pada stek, sehingga mencegah pembentukan suspensi. Selain itu, larutan biopolimer stabil secara termal. Penggunaannya terhalang oleh biayanya yang relatif tinggi.
Cairan Pengeboran Berbasis Minyak adalah sistem multikomponen di mana media dispersi (pembawa) adalah minyak atau produk minyak bumi cair (biasanya bahan bakar diesel), dan fase terdispersi (tersuspensi) adalah bitumen teroksidasi, aspal atau tanah liat yang diperlakukan khusus (bentonit terhidrofobik).
Cairan pengeboran berbasis minyak tidak berdampak buruk pada sifat reservoir minyak dan gas, mereka memiliki pelumasan: ketika digunakan, konsumsi daya untuk rotasi idle string bor di lubang sumur berkurang dan keausan pipa bor dan bit berkurang berkurang. Namun, biaya persiapan cairan pengeboran tersebut cukup tinggi, mudah terbakar, dan sulit untuk dikeluarkan dari peralatan dan perlengkapan.
Cairan pengeboran berbasis minyak digunakan untuk meningkatkan efisiensi pengeboran di batuan reservoir dan mempertahankan pemulihan minyak dan gasnya pada tingkat awal, serta untuk pengeboran sumur dalam kondisi sulit saat mengebor paket tebal tanah liat yang membengkak dan garam yang larut.
Pada cairan pengeboran emulsi media pendispersinya adalah emulsi air dalam minyak, dan fase terdispersinya adalah tanah liat. Cairan pengeboran yang dibuat berdasarkan emulsi air dalam minyak disebut emulsi terbalik atau emulsi terbalik. Fase cair dari larutan semacam itu terdiri dari 60 ... 70% minyak atau produk minyak, sisanya adalah air. Namun, kadar air dalam emulsi terbalik dapat ditingkatkan hingga 80% atau lebih jika pengemulsi khusus dimasukkan ke dalamnya.
Cairan pengeboran emulsi digunakan saat pengeboran di deposit tanah liat dan strata garam. Mereka memiliki sifat pelumas yang baik dan membantu mencegah alat menempel di sumur.
Esensi pengeboran gas terletak pada kenyataan bahwa untuk membersihkan lubang bawah, menghilangkan stek ke permukaan, serta untuk mendinginkan bit, udara terkompresi, gas alam atau gas buang dari mesin pembakaran dalam. Penggunaan agen gas memungkinkan untuk memperoleh efek ekonomi yang besar: kecepatan mekanik meningkat (sebesar 10...12 kali) dan penetrasi per bit (sebesar 10 kali atau lebih). Karena kecepatan tinggi aliran ke atas di anulus, penghapusan partikel batuan yang dibor dipercepat. Penggunaan agen gas memfasilitasi pengamatan hidrogeologi di lubang bor. Selain itu, faktor pemulihan minyak dan gas dari formasi meningkat.
Cairan pengeboran aerasi adalah campuran gelembung udara dengan cairan pembilas (air, emulsi minyak, dll.) dengan perbandingan hingga 30:1. Untuk meningkatkan stabilitas larutan aerasi, reagen dimasukkan ke dalam komposisinya - surfaktan dan bahan pembusa.
Cairan pengeboran aerasi memiliki sifat yang sama dengan cairan dari mana mereka dibuat (untuk cairan tanah liat - mereka membentuk kue tanah liat, memiliki viskositas dan tegangan geser, dan mempertahankan permeabilitas alami dari zona pembentukan lubang bawah saat dibuka). Pada saat yang sama, keuntungan besar dari cairan aerasi adalah kemungkinan penggunaannya dalam kondisi pengeboran yang sulit, dengan kerugian besar cairan pengeboran, dan pembukaan formasi produktif dengan tekanan rendah.
Parameter dasar cairan pengeboran
Parameter utama cairan pengeboran adalah densitas, viskositas, indeks filtrasi, tegangan geser statis, stabilitas, lumpur harian, kadar pasir, pH.
Kepadatan cairan pembilasan bisa berbeda: untuk lumpur berbasis minyak adalah 89...980 kg/m3, untuk lumpur tanah liat rendah - 1050...1060 kg/m3, untuk lumpur pengeboran tertimbang - hingga 2200 kg/m3 dan lebih banyak lagi .
Pilihan cairan pengeboran harus memastikan bahwa tekanan hidrostatik kolom dalam sumur hingga kedalaman 1200 m melebihi tekanan formasi sebesar 10...15%, dan untuk sumur yang lebih dalam dari 1200 m - sebesar 5...10 %.
Viskositas mencirikan properti solusi untuk menahan gerakannya.
Tingkat filtrasi- kemampuan larutan dalam kondisi tertentu untuk memberikan air pada batuan berpori. Semakin banyak air bebas dalam larutan dan semakin sedikit partikel lempung, semakin banyak air yang menembus ke dalam formasi.
Tegangan geser statis mencirikan gaya yang diperlukan untuk membuat larutan keluar dari keadaan diam.
Stabilitas mencirikan kemampuan larutan untuk menahan partikel dalam suspensi. Ini ditentukan oleh perbedaan kerapatan antara bagian bawah dan atas volume satu sampel setelah didiamkan selama 24 jam.Untuk larutan biasa, nilainya tidak boleh lebih dari 0,02 g/cm3, dan untuk larutan berbobot, 0,06 g/ cm3.
Lumpur harian- jumlah air yang dilepaskan per hari dari larutan selama penyimpanannya yang tidak bergerak. Untuk solusi yang sangat stabil, nilai lumpur harian harus sama dengan nol.
Nilai pH pH mencirikan alkalinitas cairan pengeboran. Pada pH > 7 larutan bersifat basa, pada pH = 7 bersifat netral, pada pH< 7 - кислый.
Perawatan kimia cairan pengeboran
Perlakuan kimia dari cairan pengeboran terdiri dari memasukkan bahan kimia tertentu ke dalamnya untuk meningkatkan sifat-sifatnya tanpa mengubah densitas secara signifikan.
Sebagai hasil dari perawatan kimia, hasil positif berikut tercapai:
- meningkatkan stabilitas cairan pengeboran;
- mengurangi kemampuannya untuk menyaring, mengurangi ketebalan dan kelengketan kue di dinding sumur;
- pengaturan viskositas larutan ke arah kenaikan atau penurunannya;
- memberikannya sifat khusus (tahan panas, tahan garam, dll.).
Aditif pelumas dan penghilang busa juga dimasukkan ke dalam cairan pengeboran tanah liat. Berkat aditif pelumas, kondisi kerja string bor dan alat pemotong batu di sumur menjadi lebih baik. Pencegah busa mencegah pembentukan busa ketika fase gas dilepaskan dari cairan pencuci.
Persiapan cairan pengeboran
Preparasi fluida pemboran adalah penyiapan suatu fluida pemboran dengan sifat-sifat yang diperlukan sebagai hasil pengolahan bahan baku dan interaksi komponen-komponennya.
Organisasi kerja dan teknologi persiapan cairan pengeboran tergantung pada formulasinya, keadaan bahan baku dan peralatan teknis. Pertimbangkan mereka menggunakan contoh menyiapkan larutan tanah liat.
Solusi semacam itu disiapkan baik secara terpusat di pabrik tanah liat, atau langsung di rig pengeboran. Pasokan cairan pengeboran terpusat disarankan untuk pengeboran jangka panjang di lapangan besar dan lokasi rig pengeboran yang dekat, ketika cairan pengeboran dengan parameter yang sama atau serupa diperlukan untuk pengeboran sumur. Dalam hal ini, lebih lengkap dan ekonomis digunakan bahan sumber, lebih sedikit biaya energi yang dibutuhkan dibandingkan dengan persiapan lumpur di rig pengeboran, biaya lumpur lebih rendah, personel pengeboran dibebaskan dari pekerjaan yang berat dan memakan waktu.
Persiapan cairan pengeboran terpusat yang paling ekonomis dengan metode jet jet langsung di lubang tanah liat, yang terletak dekat dengan sekelompok besar rig pengeboran. Jika tidak ada kondisi seperti itu, maka pabrik tanah liat terletak di tengah area yang dibor, dan tanah liat bongkahan dikirim dari tambang melalui jalan darat, kereta api atau transportasi air. Di pabrik tanah liat dalam mixer hidrolik dengan volume 20 ... 60 m 3, 400 ... 1000 m 3 larutan tanah liat disiapkan per hari. Ini dikirim ke rig pengeboran melalui pipa, di truk tangki atau di kapal khusus.
Dengan dispersi besar rig pengeboran, kesulitan memberikan solusi akhir kepada mereka (medan berawa atau terjal, kondisi musim dingin, dll.), Kebutuhan solusi dengan parameter berbeda, disarankan untuk menyiapkan solusi tanah liat langsung di rig. Untuk melakukan ini, rig pengeboran saat ini dilengkapi dengan unit untuk menyiapkan lumpur pengeboran dari bahan bubuk.
Bubuk tanah liat disiapkan di pabrik khusus dari tanah liat berkualitas tinggi dengan pengeringan dan penggilingan selanjutnya di pabrik bola. Pada saat yang sama, kadar air tanah liat benjolan tidak berkurang di bawah 6%, dan partikel tanah liat tidak diperbolehkan untuk disinter. Pabrik bubuk tanah liat dibangun di atas endapan tanah liat berkualitas tinggi atau langsung di tempat konsumsi.
Unit persiapan cairan pengeboran dari bahan bubuk terdiri dari dua bunker dengan total volume 42 m 3 sistem pasokan bubuk tanah liat dan mixer hidrolik (Gbr. 25). Ketika air disuplai dengan kecepatan tinggi melalui pipa 10 di ruang pencampuran 2, ruang hampa dibuat dan bubuk tanah liat masuk dari corong 1 mixer hidrolik. Campuran yang dihasilkan memasuki tangki 6, dari mana ia dikirim ke tangki cadangan atau penerima untuk penyelesaian akhir larutan. Kapasitas pencampur hidrolik mencapai 80 m 3 larutan per jam.
Beras. 25. Mixer hidrolik MG:
1 - bunker berbentuk kerucut (corong); 2 - ruang pencampuran; 3 - menetas;
4 - penutup wadah; 5 - pipa pembuangan; 6 - wadah;
7 - bingkai yang dilas (kereta luncur); 8 - chipper (sepatu);
9 - pas; 10 - pipa untuk suplai cairan
Pemurnian cairan pengeboran
Cairan pengeboran siap melalui selang tekanan yang melekat pada bagian tetap dari putar, itu dipompa ke dalam string bor dengan pompa bor. Setelah melewati pipa bor, ia melewati dengan kecepatan tinggi melalui lubang di bit ke dasar sumur, menangkap partikel batuan, dan kemudian naik di antara dinding sumur dan pipa bor. Tidak layak secara ekonomi untuk menolak menggunakannya kembali, dan tidak dapat digunakan lagi tanpa pembersihan, karena. jika tidak, terjadi keausan abrasif yang intensif pada peralatan dan alat pengeboran, kapasitas penahanan cairan pengeboran menurun, dan kemungkinan membawa fragmen batuan besar baru berkurang.
Juga perlu untuk melewatkan larutan tanah liat yang baru disiapkan melalui sistem pembersihan, karena mereka mungkin mengandung gumpalan tanah liat yang tidak ditiup, bahan kimia yang tidak bereaksi dan bahan lainnya.
Pembersihan cairan pembilasan Ini dilakukan baik karena pengendapan alami partikel batuan di talang dan tangki, dan secara paksa di perangkat mekanis (layar getar, hidrosiklon, dll.). Fluida pemboran bekas (Gbr. 14) dari kepala sumur 1 melalui sistem palung 2 memasuki vibrating screen 3, terletak pada grid miring dan bergetar. . Untuk pembersihan lebih lanjut, cairan pengeboran dipompa melalui 4 hidrosiklon dengan bantuan pompa lumpur 7, di mana dimungkinkan untuk memisahkan partikel batuan hingga ukuran 10 ... 20 mikron. Pembersihan akhir larutan dari partikel batuan tersuspensi terkecil dilakukan dalam tangki 6 dengan bantuan reagen kimia, di mana partikel yang sangat kecil tampaknya saling menempel, setelah itu mengendap.
Beras. 14. Sistem sirkulasi lumpur:
1 - kepala sumur; 2 - selokan; 3 - saringan bergetar; 4 - hidrosiklon;
5 - unit persiapan cairan pengeboran; 6 - kapasitas; 7 - pompa lumpur;
8 - tangki penerima; 9 - pompa pengeboran; 10 - pipa pembuangan.
Saat mengendap di tangki 6 dan 8, pelepasan gas terlarut dari larutan terjadi secara bersamaan.
Cairan pemboran yang telah dibersihkan diumpankan kembali ke dalam sumur oleh pompa 9 melalui pipa injeksi 10. Jika diperlukan, sejumlah tambahan larutan yang baru disiapkan dari blok 5 dimasukkan ke dalam sistem.
7. Komplikasi selama pengeboran
Dalam proses pemboran sumur, berbagai macam komplikasi yang mungkin terjadi, khususnya: runtuhnya batuan, penyerapan cairan pembilasan, intrusi minyak, gas dan air, kecelakaan, kelengkungan sumur.
longsoran batu
longsoran batu timbul karena ketidakstabilannya (retak, kecenderungan membengkak di bawah pengaruh air). Tanda-tanda khas keruntuhan adalah:
- peningkatan tekanan yang signifikan pada pelepasan pompa pengeboran;
- peningkatan tajam dalam viskositas cairan pembilasan;
- penghapusan olehnya sejumlah besar fragmen batuan yang runtuh, dll.
Penyerapan Cairan
Penyerapan Cairan- fenomena di mana cairan yang disuntikkan ke dalam sumur sebagian atau seluruhnya diserap oleh formasi. Ini biasanya terjadi ketika melewati formasi dengan porositas dan permeabilitas tinggi, ketika tekanan formasi lebih kecil dari tekanan kolom fluida pemboran di dalam sumur.
Intensitas penyerapan bisa dari lemah hingga bencana, ketika pelepasan cairan ke permukaan benar-benar berhenti.
Metode berikut digunakan untuk mencegah penyerapan:
- pembilasan dengan cairan ringan;
- penghapusan penyerapan dengan penyumbatan saluran yang menyerap cairan (karena penambahan pengisi inert ke dalamnya - asbes, mika, sekam padi, gambut tanah, serbuk gergaji, plastik; menuangkan campuran pengaturan cepat, dll.);
- meningkatkan sifat struktural dan mekanik cairan pencuci (dengan menambahkan gelas cair, garam meja, kapur, dll.).
Pertunjukan minyak, gas, dan air
Pertunjukan gas, minyak dan air terjadi ketika pemboran sumur melalui formasi dengan tekanan yang relatif tinggi melebihi tekanan fluida pemboran. Di bawah aksi tekanan air, limpahan atau semburannya terjadi, dan di bawah aksi tekanan minyak atau gas, semburan terus menerus atau emisi berkala terjadi.
Langkah-langkah untuk menghindari intrusi gas, minyak dan air meliputi:
- pilihan kepadatan cairan pembilasan yang benar;
- pencegahan menurunkan levelnya selama naiknya tali bor dan selama penyerapan cairan.
Klem alat pengeboran
Klem alat pengeboran terjadi karena alasan berikut:
- pembentukan kerak yang tebal dan lengket di dinding sumur, tempat alat bor menempel saat tidak bergerak;
- kemacetan alat bor di bagian lubang sumur yang menyempit atau dalam kasus kelengkungan sumur yang tajam, jika terjadi keruntuhan batuan yang tidak stabil, dalam kasus pengendapan batu bor jika terjadi penghentian sirkulasi.
Penghapusan lengket adalah operasi yang kompleks dan memakan waktu. Oleh karena itu, perlu untuk mengambil semua tindakan yang mungkin untuk menghindarinya.
kecelakaan
kecelakaan, timbul selama pengeboran dapat dibagi menjadi empat kelompok:
- kecelakaan dengan mata bor (melepas mata bor saat menurunkan pahat karena pemasangannya tidak mencukupi, mata bor putus karena kelebihan beban, dll.);
- kecelakaan dengan pipa bor dan kunci (kerusakan pipa di sepanjang tubuh; pengupasan ulir pipa, kunci dan kapal selam, dll.);
- kecelakaan dengan motor lubang bawah (buka tutup; putusnya poros atau rumahan, dll.);
- kecelakaan dengan tali selubung (penghancurannya; penghancuran koneksi berulir; jatuhnya masing-masing bagian pipa ke dalam sumur, dll.).
Untuk menghilangkan kecelakaan, khusus alat memancing(Gbr. 26): slip, bel, keran, router magnetik, laba-laba, dan lainnya. Namun, yang terbaik adalah mencegah kecelakaan dengan secara ketat mematuhi aturan pengoperasian peralatan, melakukan deteksi cacat, pencegahan, dan penggantian tepat waktu.
Beras. 26. Alat memancing:
a - tergelincir; b - bel; c - ketuk; g - pemotong penggilingan magnetik; d - laba-laba
Kelengkungan sumur
Saat mengebor sumur vertikal dengan cara berputar, spontan kelengkungan sumur, itu. penyimpangan batang mereka dari vertikal. Kelengkungan sumur vertikal menimbulkan sejumlah masalah: pelanggaran jaringan yang direncanakan untuk pengembangan ladang minyak dan gas, peningkatan keausan pipa bor, penurunan kualitas pekerjaan isolasi, ketidakmungkinan menggunakan pompa batang selama operasi sumur, dll. .
Penyebab kelengkungan sumur adalah faktor geologi, teknis dan teknologi. Geologi - termasuk adanya lapisan yang mencelupkan secara curam di bagian sumur; seringnya perubahan batuan dengan kekerasan yang berbeda; kehadiran di bebatuan yang dilalui sumur, retakan dan gua-gua. Faktor teknis yang berkontribusi terhadap kelengkungan sumur adalah ketidaksesuaian sumbu rig pengeboran dengan pusat rotor dan sumbu sumur; posisi miring dari meja rotor; penggunaan pipa bor melengkung, dll. Faktor teknologi yang menyebabkan kelengkungan sumur termasuk penciptaan beban aksial yang terlalu tinggi pada mata bor; ketidaksesuaian antara jenis mata bor, kuantitas dan kualitas cairan pemboran dan sifat batuan yang dilewati.
Sesuai dengan faktor-faktor di atas, langkah-langkah diambil untuk mencegah kelengkungan sumur. Dalam kondisi geologis yang sulit, tata letak khusus bagian bawah tali bor digunakan, termasuk kalibrator dan pemusat. Selain itu, Anda membutuhkan:
- pemasangan peralatan dilakukan sesuai dengan spesifikasi teknis;
- memilih jenis bit sesuai dengan jenis batuan;
- mengurangi WOB, dll.
8. Sumur menyimpang
Sumur di mana proyek menyediakan deviasi tertentu dari lubang bawah dari vertikal, dan lubang sumur dilakukan di sepanjang lintasan yang telah ditentukan, disebut diarahkan secara miring.
Sumur miring dibor ketika lapisan produktif terletak di bawah perairan laut, danau, sungai, di bawah wilayah pemukiman, fasilitas industri, di lahan basah, serta untuk mengurangi biaya pembangunan fasilitas pengeboran.
Jenis profil sumur arah yang dikembangkan saat ini dibagi menjadi dua kelompok: profil tipe konvensional (mewakili garis lengkung yang terletak pada bidang vertikal) dan profil tipe spasial (dalam bentuk kurva spasial).
Jenis profil sumur terarah dari jenis biasa ditunjukkan pada gambar. 27. Profil tipe A terdiri dari tiga bagian: vertikal 1, bagian kemiringan lubang sumur 2 dan bagian miring bujursangkar 3. Direkomendasikan untuk digunakan saat mengebor sumur dangkal di bidang lapisan tunggal, jika perpindahan lubang dasar yang besar diharapkan .
Beras. 27. Jenis profil sumur terarah:
1 - bagian miring; 2 - bagian dari set sudut kemiringan batang;
3 - bagian miring bujursangkar; 4 - bagian untuk mengurangi sudut kemiringan batang
Profil tipe B berbeda dari yang sebelumnya karena alih-alih bagian miring bujursangkar, ia memiliki bagian 4 dari penurunan alami dalam sudut kemiringan. Profil ini direkomendasikan untuk kedalaman yang luar biasa sumur.
Profil tipe B terdiri dari lima bagian: vertikal 1, bagian peningkatan sudut lubang sumur 2, bagian miring bujursangkar 3, bagian penurunan sudut kemiringan 4 dan lagi - vertikal 1. Disarankan untuk digunakan saat mengebor sumur dalam yang memotong beberapa formasi produktif.
Profil tipe-G berbeda dari yang sebelumnya di bagian 3 dan 4 diganti dengan bagian spontan penurunan sudut kemiringan 4. Profil ini direkomendasikan untuk pengeboran sumur dalam di mana penyimpangan mungkin terjadi di bagian bawah lubang sumur.
Tipe profil D terdiri dari bagian vertikal 1 dan bagian dari set sudut batang 2. Ini ditandai dengan panjang bagian kedua yang besar. Profil direkomendasikan, jika perlu, untuk mempertahankan sudut masuk tertentu ke dalam reservoir dan membukanya dengan daya maksimum.
Seperti yang dapat dilihat dari gambar. 27, semua jenis profil memiliki bagian vertikal di awal. Kedalamannya harus setidaknya 40 ... 50 m. Ujung bagian vertikal diatur ke bebatuan yang stabil, di mana Anda bisa mendapatkan sudut zenith 5 ... 6 derajat dalam satu penerbangan.
Untuk menyimpang sumur dari vertikal, perangkat defleksi khusus digunakan: pipa bor melengkung, sub melengkung, puting eksentrik, dan deflektor dari berbagai jenis.
Dalam beberapa tahun terakhir, sumur vertikal dan miring dengan ujung horizontal panjang menjadi lebih luas. Ini dilakukan untuk meningkatkan luas permukaan di mana minyak memasuki sumur dan, karenanya, meningkatkan laju aliran. Pada saat yang sama, menjadi mungkin untuk memulihkan minyak pada skala industri, yang sebelumnya dianggap tidak dapat dipulihkan, karena daya rendah dan permeabilitas reservoir yang rendah. Selain itu, ujung horizontal sumur terletak di formasi di atas air dasar, yang memungkinkan untuk memperpanjang periode operasi kering.
9. Sumur super dalam
Sumur minyak Amerika pertama menghasilkan minyak dari kedalaman sekitar 20 m. Di Rusia, sumur minyak pertama memiliki kedalaman kurang dari 100 m. Sangat cepat, kedalamannya mencapai beberapa ratus meter. Pada akhir 60-an di Uni Soviet, kedalaman rata-rata sumur untuk produksi minyak dan gas adalah 1710 m. Deposit minyak terdalam di negara kita ditemukan di wilayah Grozny pada kedalaman 5300 m, dan gas industri diperoleh di depresi Kaspia dari kedalaman 5370 m.
Reservoir pembawa gas terdalam di Eropa di lapangan Magossa (Italia Utara) terletak pada kedalaman 6100 m. Kedalaman terbesar di dunia dari mana produksi gas komersial dilakukan adalah 7460 m (Texas, AS).
Tren umum produksi minyak dan gas dari cakrawala yang semakin dalam dapat diilustrasikan oleh gambar-gambar berikut. Bahkan 20 tahun yang lalu, produksi minyak utama (66%) dilakukan dari batuan Kenozoikum termuda. Dari batuan Mesozoikum yang lebih tua, 19% minyak diekstraksi, dan dari batuan Paleozoikum paling kuno - 15%. Sekarang situasinya telah berubah: batuan Mesozoikum telah menjadi pemasok utama minyak, diikuti oleh batuan Paleozoikum.
Dengan demikian, salah satu tugas pengeboran sumur ultra-dalam adalah mencari cakrawala bantalan minyak dan gas pada kedalaman yang sangat dalam. Hanya pengeboran ultra-dalam yang dapat mengakhiri perselisihan antara pendukung hipotesis organik dan anorganik tentang asal usul minyak. Akhirnya, pengeboran ultra-dalam diperlukan untuk studi yang lebih rinci tentang interior bumi. Memang, hari ini kita tahu lebih banyak tentang ruang yang jauh daripada tentang apa yang ada di bawah kita beberapa puluh kilometer jauhnya.
Pengeboran sumur ultra-dalam dikaitkan dengan kesulitan besar. Tekanan dan suhu meningkat dengan kedalaman. Jadi, pada kedalaman 7000 m, bahkan tekanan hidrostatik adalah 70 MPa, 8000 m -80 MPa, dst. Dan di reservoir bisa dua kali lipat. Bagaimana cara menyimpan "jin" ini di dalam "botol"? Pompa bertekanan tinggi diperlukan untuk memasok cairan pembilasan. Seperti apa seharusnya cairan ini jika suhu di dasar lubang mencapai 250 °C? Bagaimana cara memutar string pipa bor multi-kilometer? Bagaimana cara menggunakan pipa bor sama sekali, jika pipa besi menahan beratnya hingga kedalaman 10 km?
Beberapa pertanyaan sudah dijawab. Untuk pengeboran sumur ultra-dalam, cairan pemboran berbobot digunakan sehingga "menyumbat" sumur dengan bobotnya sendiri. Sumur ultra-dalam dibor menggunakan motor downhole, dan pipa bor terbuat dari paduan aluminium yang ringan dan tahan lama.
Era pengeboran dalam dimulai pada tahun 1961 dengan dilaksanakannya proyek American Mohol. Sumur itu diletakkan di dasar Samudra Pasifik dekat pulau Guadelupe di bawah lapisan air sepanjang empat kilometer. Diasumsikan bahwa sumur, setelah melewati 150 m batuan dasar yang longgar dan 5,5 km batuan dasar yang kokoh, akan jatuh ke dalam mantel - lapisan berikutnya dari planet kita setelah kerak. Namun, pengeboran berhenti setelah 36 meter pertama. Alasannya adalah bahwa setelah ekstraksi inti pertama, mulut sumur yang sudah dimulai tidak dapat ditemukan, meskipun menggunakan alat pencarian paling modern.
Pada tahun 1968, serangan kedua pada mantel dilakukan dari kapal pengeboran yang dilengkapi secara khusus (Gbr. 28). Namun, pada tahun 1975, ketika lapisan basaltik atas dasar laut tersingkap, pengeboran dihentikan karena kesulitan teknis.
Beras. 28. Pandangan umum dari kapal pengeboran:
1 - kapal; 2 - derek kargo; 3 - helikopter
daerah; 4 - rig pengeboran
Selanjutnya, sumur ultra-dalam dibor di darat. Pada tahun 1970, sumur 1-SL-5407 dibor di Louisiana dengan kedalaman 7803 m.
Representasi visual dari sumur ultra-dalam modern dan peralatannya dapat diperoleh dengan contoh salah satu sumur terdalam di dunia. 1-Beiden, dibor di negara bagian Okhlacoma. Kedalaman sumur adalah 9159 m. Pengeboran dimulai pada tahun 1970 dan berlangsung selama 1,5 tahun. Ketinggian rig pengeboran adalah 43,3 m, kapasitas angkat adalah 908 ton, kekuatan drawworks adalah 2000 kW, dan masing-masing dari dua pompa lumpur adalah 1000 kW. Total kapasitas tanah sistem sirkulasi untuk bubur 840 m\ Kepala sumur dilengkapi dengan katup anti-ledakan yang dirancang untuk tekanan 105,5 MPa.
Secara struktural sumur terdiri dari arah poros dengan diameter 0,9 m sampai kedalaman 18 m, penghantar dengan diameter 0,5 m sampai kedalaman 1466 m, pipa casing sampai kedalaman 7130 m dan produksi string. Secara total, sekitar 2.200 ton pipa selubung baja, 1.705 ton semen dan 150 bit berlian digunakan untuk sumur tersebut. Total biaya pengeboran sumur adalah $6 juta.
Pada awal 1975, ada sepuluh sumur di Uni Soviet, yang kedalamannya melebihi 6 km. Ini termasuk Aral-Sorskaya di dataran rendah Kaspia dengan kedalaman 6,8 km, Biikzhalskaya di Azerbaijan dengan kedalaman 6,7 km, Sinevidnaya (7,0 km) dan Shevchenkovskaya (7,52 km) di Ukraina Barat, Burunnaya (7,5 km ) di Kaukasus Utara , dll. Sumur terdalam di dunia, sumur Kola, melintasi garis 12 km.
10. Pengeboran sumur lepas pantai
Saat ini, pangsa minyak yang diekstraksi dari ladang lepas pantai menyumbang sekitar 30 . % dari semua produksi dunia, dan bahkan lebih banyak gas. Bagaimana orang mendapatkan kekayaan ini?
Solusi paling sederhana adalah dengan mendorong tumpukan di perairan dangkal, memasang platform di atasnya, dan rig pengeboran dan peralatan yang diperlukan sudah ditempatkan di atasnya.
Cara lain adalah dengan "memperpanjang" pantai dengan mengisi air dangkal dengan tanah. Jadi, pada tahun 1926, teluk Bibi-Heybat di wilayah Baku diisi dan sebuah ladang minyak dibuat di tempatnya.
Setelah penemuan deposit minyak dan gas dalam jumlah besar di Laut Utara lebih dari setengah abad yang lalu, sebuah proyek berani untuk mengeringkannya lahir. Faktanya adalah bahwa kedalaman rata-rata sebagian besar Laut Utara hampir tidak melebihi 70 m, dan beberapa bagian dasarnya hanya ditutupi oleh lapisan air setinggi empat puluh meter. Oleh karena itu, penulis proyek menganggapnya bijaksana dengan bantuan dua bendungan - melintasi Selat Inggris di wilayah Dover, serta antara Denmark dan Skotlandia (panjang lebih dari 700 km) - untuk memotong sebagian besar Utara Laut dan pompa air dari sana. Untungnya, proyek ini hanya tinggal di atas kertas.
Pada tahun 1949, sumur minyak pertama di Uni Soviet dibor di laut terbuka di Laut Kaspia, 40 km dari pantai. Maka dimulailah penciptaan sebuah kota di atas tumpukan baja, yang disebut "Batu Minyak". Namun, pembangunan jalan layang yang membentang berkilo-kilometer dari pantai sangat mahal. Selain itu, konstruksi mereka hanya mungkin dilakukan di perairan dangkal.
Saat mengebor sumur minyak dan gas di laut dalam dan samudera, secara teknis sulit dan tidak menguntungkan secara ekonomi untuk menggunakan platform stasioner. Untuk kasus ini, telah diciptakan rig pengeboran apung yang mampu mengubah area pengeboran secara mandiri atau dengan bantuan kapal tunda.
Ada platform pengeboran jack-up, platform pengeboran semi-submersible dan platform pengeboran tipe gravitasi.
Platform pengeboran jack-up(Gbr. 29) adalah ponton apung 1 dengan potongan, di atasnya ada rig pengeboran. Ponton memiliki bentuk tiga, empat atau poligonal. Ini menampung peralatan pengeboran dan tambahan, kabin bertingkat dengan kabin untuk kru dan pekerja, pembangkit listrik dan gudang. Kolom dukungan multi-meter 2 dipasang di sudut platform.
Beras. 29. Platform pengeboran jack-up dalam posisi transportasi:
1 - ponton mengambang; 2 - dukungan pengangkatan; 3 - rig pengeboran;
4 - derek putar (kargo); 5 - kompartemen hidup; 6 - landasan helikopter;
7 - portal yang ditinggikan; 8 - dek utama
Pada titik pengeboran dengan dongkrak hidrolik kolom turun, mencapai dasar, beristirahat di tanah dan masuk jauh ke dalamnya, dan platform naik di atas permukaan air. Setelah pengeboran selesai di satu tempat, platform dipindahkan ke tempat lain.
Keandalan pemasangan anjungan pemboran jack-up bergantung pada kekuatan tanah yang membentuk dasar di lokasi pemboran.
Platform pengeboran semi-submersible(Gbr. 30) digunakan pada kedalaman 300 ... 600 m, di mana platform jack-up tidak dapat diterapkan. Mereka tidak beristirahat di dasar laut, tetapi mengapung di atas lokasi pengeboran dengan ponton besar. Platform semacam itu dijaga agar tidak bergerak dengan jangkar seberat 15 ton atau lebih. Tali baja menghubungkannya ke derek otomatis yang membatasi perpindahan horizontal relatif terhadap titik pengeboran.
Beras. 30 Platform pengeboran semi-submersible:
1 - ponton selam; 2 - kolom stabilisasi; 3 - tubuh bagian atas;
4 - rig pengeboran; 5 - derek kargo; 6 - landasan helikopter.
Platform semi-submersible pertama tidak self-propelled, dan mereka dikirim ke area kerja dengan bantuan kapal tunda. Selanjutnya, platform dilengkapi dengan baling-baling yang digerakkan oleh motor listrik dengan total kapasitas 4,5 ribu kW.
Kerugian dari platform semi-submersible adalah kemungkinan pergerakannya relatif terhadap titik pengeboran di bawah pengaruh gelombang.
lebih stabil platform pengeboran tipe gravitasi. Mereka dilengkapi dengan dasar beton yang kuat bertumpu di dasar laut. Basis ini tidak hanya mengakomodasi kolom pemandu untuk pengeboran, tetapi juga sel-reservoir untuk menyimpan minyak yang diproduksi dan bahan bakar diesel yang digunakan sebagai pembawa energi, dan banyak pipa. Elemen dasar dikirim ke lokasi pemasangan dalam bentuk balok besar.
Dasar laut di lokasi platform gravitasi harus disiapkan dengan hati-hati. Bahkan sedikit kemiringan dasar mengancam untuk mengubah rig pengeboran menjadi Menara Miring Pisa, dan adanya tonjolan di bagian bawah dapat menyebabkan perpecahan di pangkalan. Oleh karena itu, sebelum mengatur pengeboran "pada titik", semua batu yang menonjol dihilangkan, dan retakan dan lekukan di bagian bawah ditutup dengan beton.
Semua jenis anjungan pengeboran harus tahan terhadap tekanan gelombang setinggi 30 m, meskipun gelombang tersebut terjadi setiap 100 tahun sekali.
Skema pengeboran umum
Untuk pengeboran sumur minyak dan gas, metode putar eksklusif digunakan. Dengan metode ini, sumur seolah-olah dibor dengan mata bor yang berputar. Partikel batuan yang dibor dibawa ke permukaan oleh aliran sirkulasi fluida pengeboran. Tergantung pada lokasi mesin, pengeboran putar dibagi menjadi: putar ketika mesin berada di permukaan dan menggerakkan bit ke bawah melalui putaran seluruh rangkaian bor dan pengeboran lubang bawah (menggunakan turbin atau bor listrik) ketika mesin terletak dekat dengan bagian bawah lubang di atas bit.
Proses pengeboran terdiri dari operasi berikut:
tersandung (turunnya pipa bor dengan sedikit ke dalam sumur ke bawah dan mengangkatnya dengan bit bekas) dan pengeboran itu sendiri - pekerjaan bit di bagian bawah (penghancuran batu sedikit demi sedikit).
Operasi ini secara berkala terputus untuk menjalankan pipa selubung ke dalam sumur, yang digunakan untuk melindungi dinding sumur dari keruntuhan dan pemisahan cakrawala minyak.
Pada saat yang sama, sejumlah pekerjaan tambahan dilakukan selama proses pengeboran;pengambilan sampel inti, persiapan lumpur pengeboran, penebangan, pengukuran kelengkungan lubang bor, pengujian atau pengembangan sumur untuk tujuan menginduksi aliran minyak, dll.
Siklus konstruksi sumur penuh terdiri dari proses berikut:
satu). Pemasangan menara, peralatan pengeboran, pengaturan situs.
2). proses pengeboran.
empat). Pengungkapan dan pemisahan lapisan (casing running dan cementing).
5) Pengujian sumur untuk aliran masuk minyak atau gas (pengembangan).
6). Pembongkaran peralatan
Diagram skematik umum penempatan peralatan pengeboran di sumur ditunjukkan pada gambar. nomor 1.
Alat pengeboran
Rig pengeboran.
Rig pengeboran dirancang untuk mengangkat dan menurunkan tali bor dan pipa selubung ke dalam sumur, menahan tali bor selama pengeboran, serta menempatkan di dalamnya sistem perjalanan, pipa bor dan bagian dari peralatan yang diperlukan untuk pengeboran. proses.
Saat mengebor minyak dan gas, derek logam jenis menara dan tiang digunakan. menara tiang digunakan lebih sering daripada yang menara. Mereka lebih mudah dan lebih cepat untuk dipasang, tetapi menara menara lebih menahan beban dan lebih tinggi. Menara lebih sering digunakan di sumur eksplorasi dalam, dan yang tiang digunakan dalam pengeboran produksi.
Rig pengeboran berbeda dalam hal kapasitas beban dan ketinggian. Praktik telah menetapkan bahwa ketika mengebor sumur hingga kedalaman 1200-1300m, disarankan untuk menggunakan menara dengan ketinggian 28m, sumur dengan kedalaman 133-3500m - ketinggian 41-42m, sumur dengan kedalaman lebih dari 3500m - ketinggian 53m atau lebih.
Saat ini, menara tipe tiang berbentuk A banyak digunakan (lihat Gambar No. 1). Mereka terdiri dari dua kolom yang terhubung di bagian atas di blok mahkota dengan ikatan dan dipasang di bagian bawah ke engsel pendukung. Pada jarak tertentu dari engsel, menara memiliki penyangga yang kaku - penyangga.
Drawworks
Drawworks dirancang untuk menurunkan dan menaikkan tali bor, memasang dan melepaskan pipa, menurunkan tali selubung, menahan tali tetap menurut beratnya atau perlahan-lahan menurunkan (memberi makan) selama pengeboran.
Dalam beberapa kasus, drawworks digunakan untuk mentransfer daya dari mesin ke rotor, beban tarik dan pekerjaan bantu lainnya.
Drawwork diproduksi dalam berbagai jenis, berbeda satu sama lain dalam skema dan desain kinematik.
Sistem perjalanan
Sistem kerekan (poly-spast) dari rig pengeboran dirancang untuk mengubah gerakan rotasi drum winch menjadi gerakan translasi (vertikal) kail dan mengurangi beban pada cabang-cabang tali.
Sebuah tali berjalan baja dilewatkan melalui katrol tali dari blok mahkota dan blok perjalanan dalam urutan tertentu, salah satu ujungnya ("mati") melekat pada balok rangka menara, dan yang lainnya, disebut berjalan (terkemuka ) satu, ke drum winch.
Menurut daya dukung dan jumlah cabang tali di peralatan, sistem perjalanan dibagi menjadi beberapa ukuran. Dalam rig pengeboran dengan daya dukung 50-75 ton, digunakan sistem perjalanan dengan jumlah puli 2\3 dan 3\4; dalam instalasi dengan kapasitas angkat 100-300t - sistem perjalanan dengan jumlah katrol 3\4, 4\5, 5\6 dan 6\7. Dalam penunjukan sistem tali-temali, digit pertama menunjukkan jumlah berkas tali dari blok perjalanan, dan yang kedua - jumlah berkas tali dari blok mahkota.
blok mahkota mewakili bingkai di mana as dan penyangga dengan katrol dipasang. Terkadang bingkai dibuat menjadi satu kesatuan dengan bagian atas menara.
blok perjalanan adalah rumah yang dilas di mana katrol dan rakitan bantalan ditempatkan. seperti pada blok mahkota.
Tali perjalanan adalah baja bulat, tali enam baris dari struktur kabel persilangan. Untaian yang dipelintir menjadi tali di sekitar inti organik atau logam terbuat dari baja karbon tinggi dan mangan tinggi berkekuatan tinggi dengan sejumlah kabel dari 19 hingga 37. Dengan mempertimbangkan titik pemasangan ujung tali yang berjalan di arah belitannya pada drum, tali kawat tangan kanan dengan diameter 25 digunakan untuk drawworks , 28, 32, 35, 38 mm. Tali yang paling umum dengan diameter inti organik dan plastik 28 dan 32 mm. Pada kedalaman lebih dari 4000 m, tali inti logam digunakan, yang memiliki kekuatan putus yang meningkat dan kekakuan melintang yang tinggi, yang karenanya ketahanannya terhadap penghancuran meningkat.
Kait bor dan blok pengait dirancang untuk penangguhan alat pengeboran dan elevator di atasnya selama operasi tersandung.
blok kait (kait yang terhubung ke blok berjalan) memiliki sejumlah keunggulan: tinggi keseluruhan lebih rendah daripada gabungan blok dan kait berjalan, desain yang lebih kompak. Kerugiannya termasuk massanya yang besar.
Kait tersedia dengan kapasitas angkat 75, 130, 200.225t (masing-masing, memungkinkan jangka pendek, kapasitas angkat maksimum -110, 160, 250 dan 300t).
Kapasitas angkat yang dinilai dari blok kait adalah 75, 125 dan 200t (kapasitas angkat maksimum adalah 100, 160 dan 250t).
Pengeboran sling - ini adalah tautan yang menghubungkan kait ke lift, di mana alat bor atau tali selubung ditangguhkan. Kapasitas angkat sling adalah 25,50,75,125,200 dan 300t. Link dengan kapasitas angkat 25, 50 dan 75 ton dirancang untuk pengerjaan ulang sumur, tetapi juga dapat digunakan untuk rig pengeboran dengan kapasitas angkat yang sesuai.
Mekanisme dan alat yang digunakan untuk produksi operasi tripping
Mengangkat dan menurunkan pipa bor untuk mengganti mata bor bekas terdiri dari operasi berulang yang sama. Untuk produksi operasi tripping, peralatan dan peralatan khusus digunakan. Ini termasuk: elevator, baji, kunci pas melingkar, kunci mesin ("laba-laba"), tong pengeboran otomatis (ABK), gripper baji putar pneumatik(RCP).
Tangga berjalan, dirancang untuk mencengkeram dan menahan beban pada rangkaian pipa bor atau pipa selubung selama operasi tersandung. Elevator dari berbagai jenis digunakan, berbeda dalam ukuran tergantung pada diameter pipa bor atau casing, kapasitas beban, rancangan dan bahan untuk pembuatannya.
Wedges untuk pipa bor digunakan untuk menggantung alat bor di meja rotor. Mereka dimasukkan ke dalam lubang kerucut antara pipa dan liner rotor. Penggunaan wedges mempercepat pekerjaan pada operasi tersandung. Casing wedges digunakan untuk menjalankan string casing yang berat. Wedges dipasang pada bantalan khusus di atas kepala sumur. Gripper baji putar pneumatik (RCP), dibangun ke dalam rotor dan dirancang untuk menaikkan dan menurunkan baji.
Berbagai kunci pas digunakan untuk memasang dan melepaskan pipa bor dan pipa selubung. Beberapa di antaranya dimaksudkan untuk memasang sekrup, dan yang lain untuk mengencangkan dan melepaskan sambungan berulir kolom. Biasanya lingkaran cahaya kunci untuk pemasangan awal pipa dirancang untuk kunci dengan diameter yang sama, dan kunci mesin berat untuk mengencangkan dan melepaskan koneksi berulir - untuk dua, dan terkadang lebih banyak ukuran pipa bor dan kunci. Operasi pengikatan dan pelonggaran koneksi berulir dilakukan oleh dua kunci mesin: satu kunci (penahan) diperbaiki, dan yang kedua (mengsekrup atau melonggarkan) dapat dipindahkan. Kunci digantung dalam posisi horizontal dan dilekatkan pada tali baja untuk memudahkan gerakannya. Pekerjaan menurunkan dan mengangkat sangat difasilitasi saat menggunakan baterai untuk tong pengeboran otomatis dipasang di antara winch dan rotor (Gbr. No. 2) Untuk menghindari selip kunci, kerupuk dengan takik dimasukkan ke dalam rahang.
Peralatan pengeboran sumur.
Saat mengebor dengan metode putar, perlu alat penghancur (bit) diberikan gerakan rotasi dan beban yang memberikan tekanan yang cukup pada interval untuk dihancurkan. Selain itu, kondisi diperlukan untuk menghilangkan partikel materi (batuan) yang hancur. Oleh karena itu, sumur dilengkapi dengan rotor, putar dengan selang bor, pompa lumpur dan tali bor. Jika bit tidak berputar dari permukaan bumi (rotor), tetapi langsung di bagian bawah, selain peralatan yang terdaftar, turbodrill atau bor listrik digunakan.
Rotor
Rotor (Gbr. 2,3) dirancang untuk mentransfer gerakan rotasi ke string bor selama pengeboran, mendukung beratnya saat operasi tersandung dan pekerjaan tambahan. Rotor adalah gearbox yang mentransmisikan rotasi ke string bor yang ditangguhkan secara vertikal dari poros transmisi horizontal. Kecepatan rotor dapat diubah menggunakan roda gigi winch atau dengan mengganti sprocket.
|
Menurut tujuannya, mata bor diklasifikasikan menjadi tiga kelompok:
satu). Pahat yang menghancurkan batu dengan pembantaian terus menerus.
2). Bit yang menghancurkan batu dengan pemotongan melingkar (core bit).
3). Pahat untuk keperluan khusus (runcing, berlubang, reamers, pemotong frais, dll.).
Baik untuk pengeboran padat dan inti, bit telah dibuat yang memungkinkan penghancuran batu sesuai dengan salah satu dari empat prinsip tindakan yang tercantum. Hal ini memudahkan pemilihan jenis bit sesuai dengan sifat fisik dan mekanik dari batuan yang diberikan.
Dalam proses pemboran sumur eksplorasi dan terkadang sumur produksi, batuan diseleksi secara berkala berupa pilar-pilar utuh (inti) untuk menyusun penampang stratigrafi, mempelajari karakteristik litologi batuan yang dilewati, mengidentifikasi kandungan minyak atau gas di dalam sumur. pori-pori batuan yang dilewati, dll.
Untuk mengekstrak inti ke permukaan, bit khusus digunakan, yang disebut berbentuk kolom. Saat mengebor, inti memasuki bagian dalam sedikit dan naik ke permukaan pada waktu yang tepat.
Dikabarkan bit inti dua jenis - dengan pembawa tanah yang dapat dilepas dan tanpa pembawa tanah yang dapat dilepas. Saat mengebor dengan mata bor inti tanpa pembawa tanah yang dapat dilepas, seluruh tali bor harus diangkat untuk membawa inti ke permukaan. Saat bekerja dengan bit inti dengan kapal keruk yang dapat dilepas, yang terakhir, dengan bantuan tali khusus, winch dan penangkap tambahan kecil, ditarik ke permukaan tanpa mengangkat pipa.
Tali bor
Tali bor terdiri dari kelly, pipa bor, sambungan alat, kapal selam, kerah bor, pemusat tali bor.
Ini dimaksudkan untuk tujuan berikut:
1) transmisi rotasi dari rotor ke bit (selama pengeboran putar);
2) pasokan cairan pembilasan ke turbodrill (dalam hal pengeboran turbin), ke bit dan lubang bawah (untuk semua metode pengeboran);
3) membuat WOB;
4) mengangkat dan menurunkan mata bor, bor turbo, bor listrik;
5) melakukan pekerjaan tambahan (perluasan dan pembilasan sumur, memancing, memeriksa kedalaman sumur, dll.).
Pipa timah(Gbr. No. 3) dalam banyak kasus memiliki bagian persegi. Torsi dari rotor ditransmisikan ke pipa terkemuka melalui liner yang dimasukkan ke dalam rotor. Liner yang sesuai digunakan untuk setiap ukuran pipa, memungkinkannya bergerak bebas di sepanjang sumbu sumur.
Karena dalam praktiknya, menara yang paling umum adalah 41 m, yang memungkinkan Anda memiliki lilin dengan panjang sekitar 25 m, pipa bor dibuat dengan panjang 6,8 dan 11,5 m. Oleh karena itu, sebuah lilin dapat dipasang dari empat pipa yang panjangnya masing-masing 6m, tiga pipa yang panjangnya 8m, atau dua pipa yang panjangnya 11,5m.
Saat merakit dudukan dari tiga pipa bor sepanjang 8 m, digunakan dua kopling atau satu kopling dan satu kunci. Dua buah pipa bor sepanjang 11,5 m dihubungkan dengan menggunakan kunci bor. Lilin yang dirakit juga disekrup menggunakan kunci bor.
Kerah bor dipasang di atas mata bor (turbodrill, bor listrik) untuk meningkatkan kekakuan bagian bawah senar bor. Penggunaannya memungkinkan Anda untuk membuat beban pada bit dengan satu set pendek pipa berdinding tebal yang saling berhubungan, yang meningkatkan kondisi kerja string bor.
Subs dirancang untuk menghubungkan elemen string bor dengan berbagai jenis dan ukuran ulir.
Pipa Bor Paduan Ringan digunakan untuk mengurangi berat tali bor. Mereka disekrup bersama dengan bantuan kunci pengeboran dengan desain khusus. Penggunaan pipa bor paduan ringan memungkinkan untuk mengurangi berat kolom sekitar 2 kali.
kolom operasional.
Saat ini, string produksi dengan diameter 127, 146 dan 168 mm adalah yang paling umum.
Untuk menjalankan tali selubung dengan sukses ke kedalaman target, serta penyemenan sumur berikutnya, bagian bawah tali selubung dilengkapi secara khusus dengan beberapa detail (Gbr. No. 13): steker pemandu 1, sepatu 2, nozel sepatu 3, katup periksa 4.
Steker pemandu terbuat dari kayu, semen atau besi tuang,
Di mulut sumur bor, di mana ledakan mungkin terjadi, dipasang peralatan BOP, yang terdiri dari pencegah dari satu jenis atau lainnya (ram, universal, berputar), peralatan untuk remote dan kontrol manual mereka, sistem perpipaan dengan katup atau katup gerbang bertekanan tinggi.
Pencegah universal (Gbr. No. 15) menutup kepala sumur dengan rapat di hadapan pipa dengan berbagai diameter dan jenis.
Penyumbatan (penyemenan) sumur.
Tujuan dari sumbat sumur adalah untuk mendapatkan cincin kuat dari bahan penyumbat yang terletak di anulus, yang sepanjang seluruh ketinggian harus memastikan pemisahan dan isolasi cakrawala produktif dan zona komplikasi yang ditemukan oleh sumur (Gbr. No. 12).
Tergantung pada karakteristik bagian geologi dan kondisi pengeboran, semen tertimbang digunakan untuk menyiapkan bubur semen (dengan kepadatan cairan pengeboran hingga 2,2 g/cm zona penyerapan cairan pencuci), dll.
Unit grouting dirancang untuk persiapan (jika mesin pencampur tidak digunakan) dan injeksi bubur semen ke dalam sumur dan untuk mendorongnya ke dalam anulus. Unit-unit ini juga digunakan untuk pengujian tekanan senar casing dan pekerjaan bantu lainnya.
mesin pencampur dirancang untuk persiapan solusi dari bahan bubuk.
Memasukkan kepala dirancang untuk memompa grouting dan memeras bubur selama plugging, serta menyiram bubur saat menyiram sumur dalam proses menjalankan string dan operasi teknis lainnya.
Mengisi colokan digunakan untuk pengeboran sumur. Steker atas dirancang untuk mencegah penetrasi cairan pembilasan ke dalam bubur semen ketika yang terakhir dipaksa ke dalam anulus dan untuk mengontrol injeksi yang benar ke dalam anulus, dan sumbat bawah untuk pembersihan Permukaan dalam casing dari sisa-sisa bubur semen.
Saat mengebor sumur, grouting satu tahap dari string casing terutama digunakan.
Inti dari metode ini adalah sebagai berikut. Setelah casing diturunkan, kepala grouting disekrup ke bagian atasnya, sumur disiram, dan kemudian jumlah bubur grouting yang dihitung dipompa.
Selanjutnya, sumbat karet penyegelan sendiri dilepaskan di kepala sumbat dan larutan pemerasan dipompa dari atas. Segera setelah steker duduk di cincin dorong, tekanan naik tajam di kolom. Lompatan pada jarum pengukur tekanan akan menunjukkan bahwa bubur semen telah benar-benar keluar dari tali ke dalam anulus, mis. pada akhir proses penyambungan.
Saat penyemenan di sumur dalam, perlu untuk memompa bubur semen dan cairan pemerasan dalam jumlah yang cukup besar dalam waktu yang sangat terbatas, ditentukan oleh saat bubur semen mulai mengeras. Dalam kondisi seperti itu, penyemenan dua tahap digunakan: bubur semen dipompa ke dalam string dan dipaksa masuk ke anulus dalam dua bagian. Bagian pertama ditekan di belakang tali melalui sepatu, dan yang kedua dipaksa melalui lubang di lengan casting yang dipasang di tali selubung pada jarak yang cukup jauh dari sepatu.
Setelah dicolokkan ke dalam sumur, ujung atas senar casing diikat dengan kepala senar, yang dipasang langsung ke pipa casing.
Menyemen kolom kehabisan operasi dasar proses konstruksi sumur. Ini diikuti oleh pengembangan dan pengoperasian sumur. Pemasangan dan pembongkaran peralatan pengeboran, kontrol teknologi dan survei geofisika di dalam sumur, perforasi kolom, pengujian reservoir dan stimulasi aliran masuk, pengerjaan ulang sumur dan penghapusan kecelakaan selama pengeboran tidak dipertimbangkan dalam referensi dan manual metodologi ini.
Penting untuk dicatat bahwa pengeboran sumur minyak dan gas hanya dapat dilakukan dengan kepatuhan yang ketat terhadap semua aturan dan persyaratan. Dan ini sama sekali tidak mengejutkan, karena Anda harus bekerja dengan bahan yang agak berbahaya dan sensitif, yang ekstraksinya membutuhkan pendekatan yang kompeten. Dan untuk memahami semua aspek bekerja dengan itu, pertama-tama perlu untuk mempertimbangkan semua dasar-dasar kasus ini dan komponennya.
Jadi, sebuah sumur disebut pekerjaan tambang, yang dibuat tanpa memerlukan akses ke dalam seseorang dan memiliki bentuk silinder - panjangnya berkali-kali lebih besar dari diameternya. Awal sumur disebut mulut, permukaan kolom silinder disebut batang atau dinding, dan bagian bawah benda disebut bagian bawah. Panjang benda diukur dari mulut ke bawah, sedangkan kedalaman diukur dengan proyeksi sumbu ke vertikal. Diameter awal benda semacam itu maksimal tidak melebihi 900 mm, sedangkan diameter akhir dalam kasus yang jarang terjadi kurang dari 165 mm - ini adalah kekhususan proses yang disebut pengeboran sumur minyak dan gas, dan fitur-fiturnya.
Fitur pengeboran sumur minyak dan gas
Pembuatan sumur sebagai proses terpisah sebagian besar terdiri dari pengeboran, dan pada gilirannya, didasarkan pada operasi berikut:
- Proses pendalaman saat menghancurkan batuan dengan alat bor,
- Penghapusan batu hancur dari sumur,
- Memperkuat poros dengan senar selubung saat tambang semakin dalam,
- Kinerja pekerjaan geologi dan geofisika untuk mencari cakrawala produktif,
- Semen tali produksi.
Klasifikasi sumur minyak dan gas
Diketahui bahwa bahan yang diperlukan, yang direncanakan untuk ditambang, dapat terjadi pada kedalaman yang berbeda. Dan oleh karena itu, pengeboran juga dapat dilakukan pada kedalaman yang berbeda, dan pada saat yang sama, jika kita berbicara tentang kedalaman hingga 1500 meter, pengeboran dianggap dangkal, hingga 4500 - sedang, hingga 6000 - dalam. Hingga saat ini, pengeboran sumur minyak dan gas dilakukan di cakrawala yang sangat dalam, lebih dalam dari 6000 meter - dalam hal ini, sumur Kola sangat indikatif, kedalamannya adalah 12650 meter. Jika kita mempertimbangkan metode pengeboran, dengan fokus pada metode penghancuran batuan, maka di sini kita dapat menyebutkan sebagai contoh metode mekanis, misalnya, rotasi, yang diimplementasikan menggunakan bor listrik dan motor downhole tipe sekrup. Ada juga metode perkusi. Dan mereka juga menggunakan metode non-mekanik, di antaranya elektropulse, eksplosif, elektrik, hidrolik dan lain-lain. Semuanya tidak banyak digunakan.
Bekerja sambil mengebor minyak atau gas
PADA versi klasik saat mengebor minyak atau gas, mata bor digunakan untuk memecahkan batu, dan aliran fluida pembilasan terus-menerus membersihkan lubang bawah. Dalam kasus yang jarang terjadi, reagen kerja jenis gas digunakan untuk pembersihan. Pengeboran dalam hal apa pun dilakukan secara vertikal, pengeboran miring diterapkan hanya bila diperlukan, juga pengeboran cluster, directional, double-lateral atau multilateral juga digunakan. Pendalaman sumur dilakukan dengan atau tanpa pengambilan sampel inti, opsi pertama digunakan saat bekerja di sepanjang pinggiran, dan yang kedua - di seluruh area. Jika inti diambil, itu diperiksa untuk lapisan batuan yang dilewati, secara berkala mengangkatnya ke permukaan.
Pengeboran minyak dan gas saat ini dilakukan baik di darat maupun di lepas pantai, dan pekerjaan tersebut dilakukan dengan menggunakan rig pengeboran khusus yang menyediakan pengeboran putar menggunakan pipa bor khusus yang dihubungkan dengan sambungan ulir soket dan kunci. Juga, terkadang pipa fleksibel kontinu digunakan, yang dililitkan pada drum dan dapat memiliki panjang sekitar 5 ribu meter atau lebih. Dengan demikian, karya-karya seperti itu tidak dapat disebut sederhana dengan cara apa pun - mereka sangat spesifik dan kompleks, dan penekanan khusus di sini harus diberikan pada teknologi baru, yang studinya dapat menjadi tugas yang sulit bahkan bagi para profesional di industri ini.
Teknologi baru untuk pengeboran sumur minyak dan gas di pameran Neftegaz
Berbagi informasi dan belajar tentang inovasi dapat memastikan kemajuan yang optimal, dan oleh karena itu kebutuhan seperti itu tidak dapat diabaikan begitu saja. Jika Anda memutuskan untuk bergabung dengan pencapaian modern dan terjun ke lingkungan profesional, acara profesional diadakan untuk tujuan ini, dan Anda harus ikut serta di salah satunya. Kita berbicara tentang pameran yang diadakan setiap tahun di Expocentre Fairgrounds dan mengumpulkan ratusan dan ribuan spesialis di area ini selama hari pembukaan. Di sini Anda dapat dengan mudah mengakses perkembangan baru, mempelajari teknologi canggih dan pada saat yang sama memperoleh kontak yang berguna dalam volume yang diperlukan, menemukan klien dan mitra. Peluang seperti ini tidak boleh dilewatkan, karena tidak sering datang dan dapat membuat perbedaan besar jika dilakukan dengan benar!
Baca artikel kami yang lain.
Saya . Bagian teknis. Karakteristik dan deskripsi singkat perangkat.
Rig dan struktur pengeboran……………………………………………….…………………………4
Sistem perjalanan……………………………………………………………………………….………..5
Drawworks………………………………………………..……………………………………………… 6
Rotor………………………………………………………………..………………………….7
Pompa lumpur dan peralatan sistem sirkulasi………………………………………………8
Memutar………………………………………………………………..………………………………………9
Penggerak daya rig pengeboran ………………………………………………………………………….9
Peralatan penyegelan kepala sumur……………………..………………………………10
II . Bagian teknologi.
1. Pengeboran sumur minyak dan gas…………………………….……..14
Pembiasaan dengan metode pengumpanan bit manual, pengeboran
dengan pengontrol bit, belajar mengebor dengan rotor………………………………………………..14
Pembiasaan dengan metodologi pengembangan rasional
Kavling……………………………………………………………………………………………………… 15
Melakukan pekerjaan dasar dalam perangkat lunak open source dengan bantuan khusus
peralatan………………………………………………………………………………….16
Persiapan pipa untuk menyeret, pemasangan lift
pada rotor, melepasnya dari rotor, menanam pipa pada baji………………………………………...17
Memeriksa ulir kunci, memasang BT dengan kunci pas
yang baterainya, pemasangan kembali dan pelepasan koneksi kuncinya dengan
menggunakan kunci UMK……………………………………………………………………………………………………………………… ……………………………………………………………………………………………………………………………………… ……………………………………………………………………………………………………………………………………… ………………………………………………………………………………………………………
Pemeriksaan dan pengukuran BT dan UBT, pemasangan BT pada candlestick, on-
memutar dan memutar bit……………………………………………………………………… 19
Pembilasan sumur…………………………………………………………………………………………….20
BHA dan regulasi rezim pengeboran untuk memerangi self-pro-
kelengkungan sumur yang sewenang-wenang…………………………………………………………………………….22
2. Pembiasaan pengeboran sumur dengan semak-semak…………………………….23
3. Menjalankan dan menyemen senar casing……………….……………..24
4. Pembukaan dan pengujian cakrawala minyak……………….………..26
5. Pekerjaan darurat di sumur………………………………………………..27
6. Likuidasi GNVP dan emisi……………………………….…….…….28
Saya . Bagian teknis
Karakteristik dan deskripsi singkat perangkat
Rig dan fasilitas pengeboran
Proses pemboran disertai dengan menurunkan dan mengangkat tali bor ke dalam sumur, serta mempertahankan bobotnya. Massa alat yang diperlukan untuk beroperasi dalam hal ini mencapai ratusan kilonewton. Untuk mengurangi beban pada tali dan mengurangi daya terpasang mesin, peralatan pengangkat digunakan (Gbr. 2.2), yang terdiri dari menara, drawwork, dan sistem tekel (polyspast). Sistem perjalanan, pada gilirannya, terdiri dari bagian tetap - blok mahkota (blok katrol tetap) yang dipasang di bagian atas lentera menara, dan bagian yang bergerak - blok perjalanan (blok katrol bergerak), tali perjalanan, kait dan sling . Peralatan pengangkat merupakan bagian integral dari setiap rig pengeboran, terlepas dari metode pengeborannya.
Rig pengeboran dirancang untuk mengangkat dan menurunkan tali bor dan pipa selubung ke dalam sumur, menahan tali bor selama pengeboran, serta menempatkan di dalamnya sistem perjalanan, pipa bor dan beberapa peralatan yang diperlukan untuk proses pengeboran. . Bahaya paling serius saat bekerja di rig pengeboran adalah kehancuran sebagian atau seluruhnya. Alasan utama yang menyebabkan jatuh atau hancurnya menara adalah pengawasan yang tidak memadai terhadap kondisinya selama operasi jangka panjang. Untuk alasan ini, perubahan diperkenalkan dalam aturan keselamatan yang menyediakan pemeriksaan berkala wajib menara, termasuk pembongkaran lengkap dan revisi bagian-bagiannya, serta pengujian dengan pemuatan menara rakitan.
Selain itu, mesin derek harus diperiksa dan diperiksa secara menyeluruh setiap kali sebelum pengeboran, sebelum menjalankan tali selubung, melepaskan tali bor atau tali selubung yang macet, jika terjadi kecelakaan dan setelah angin kencang(15 m/s untuk area terbuka, 21 m/s untuk area hutan dan taiga, serta ketika menara dibangun di dalam lubang). Menara tipe tiang dipasang dalam posisi horizontal, dan kemudian dinaikkan ke posisi vertikal menggunakan perangkat khusus. Pengangkutan menara dilakukan dalam bentuk rakitan bersama dengan platform pekerja berkuda dalam posisi horizontal pada perangkat transportasi khusus. Pada saat yang sama, sistem perjalanan tidak dibongkar bersama dengan menara. Jika tidak mungkin karena kondisi medan untuk mengangkut menara secara keseluruhan, maka menara dibongkar menjadi beberapa bagian dan diangkut sebagian dengan transportasi universal.Dalam praktik pengeboran, selain menara tipe tiang, menara tipe menara masih digunakan, yang dirakit menggunakan metode top-down. Sebelum memulai pemasangan, lift dipasang di dasar menara. Setelah perakitan menara selesai, lift dibongkar.
Bersamaan dengan pemasangan rig pengeboran dan pemasangan derek, konstruksi struktur dekat sumur sedang dilakukan. Ini termasuk struktur berikut: 1) Gudang peredam (agregat), dirancang untuk melindungi mesin dan mekanisme transmisi winch. Itu terpasang ke menara dari sisi panel belakangnya ke arah yang berlawanan dengan jalan setapak. Dimensi gudang gigi ditentukan oleh jenis pemasangan. 2) Gudang pompa untuk menampung pompa pengeboran dan peralatan listrik. Itu dibangun baik sebagai perpanjangan ke sisi lentera menara gudang roda gigi, atau secara terpisah ke sisi menara. Dinding dan atap roda gigi dan gudang pompa, tergantung pada kondisi spesifik, dilapisi dengan papan, besi bergelombang, pelindung buluh, kain karet atau film polietilen. Penggunaan beberapa rig pengeboran memerlukan kombinasi roda gigi dan gudang pompa. 3) Jembatan penerima yang dirancang untuk meletakkan selubung pengeboran dan pipa-pipa lain serta peralatan bergerak, perkakas, material dan suku cadang di sepanjangnya. Menerima jembatan horisontal dan miring. Ketinggian pemasangan jembatan penerima diatur oleh ketinggian pemasangan rangka rig pengeboran. Lebar jembatan penerima hingga 1,5...2 m, panjang hingga 18 m 4) Sistem perangkat untuk membersihkan lumpur bor, serta gudang bahan kimia dan bahan curah. 5) Sejumlah struktur tambahan selama pengeboran: pada penggerak listrik - platform transformator, pada mesin pembakaran internal (ICE) - platform tempat wadah bahan bakar dan pelumas berada, dll.
Sistem perjalanan
Dalam proses pengeboran sumur, sistem pengangkatan melakukan berbagai operasi. Dalam satu kasus, digunakan untuk tersandung untuk mengganti mata bor yang aus, menurunkan, mengangkat dan menahan beban senar bor selama coring, memancing atau pekerjaan lain di dalam sumur, serta untuk menurunkan pipa selubung. Dalam kasus lain, ini memberikan penciptaan gaya yang diperlukan pada kait untuk mengekstrak tali bor yang macet dari sumur atau jika terjadi kecelakaan dengannya. Untuk memastikan efisiensi tinggi dalam berbagai pekerjaan ini, sistem pengangkatan memiliki dua jenis kecepatan kait pengangkat: teknis untuk tersandung dan teknologi untuk operasi lainnya.
![]() |
Karena perubahan berat tali bor selama pengangkatan, untuk menjaga waktu minimum, sistem pengangkatan harus dapat mengubah kecepatan pengangkatan sesuai dengan beban. Ini juga berfungsi untuk menahan tali bor yang diturunkan ke dalam sumur selama pengeboran.
Sistem pengangkat instalasi (Gbr. III.1) adalah mekanisme kerekan rantai, yang terdiri dari blok mahkota 4, blok perjalanan (bergerak) 2, tali baja 3, yang merupakan koneksi fleksibel antara drawworks 6 dan mekanisme 7 untuk mengencangkan ujung tali yang tetap. blok mahkota 4 dipasang di platform atas rig pengeboran 5. ujung bergerak TETAPI tali 3 melekat pada drum winch 6, dan ujung tetap B- melalui perlengkapan 7 ke dasar menara. Sebuah kait terpasang ke blok perjalanan 1 , di mana lift untuk pipa atau putar ditangguhkan pada tautan. Saat ini, blok perjalanan dan kait pengangkat dalam banyak kasus digabungkan menjadi satu mekanisme - blok kait.
Drawworks
Winch adalah mekanisme utama sistem pengangkatan rig pengeboran. Ini dimaksudkan untuk melakukan operasi berikut: menurunkan dan mengangkat pipa bor dan pipa selubung; menahan tali pipa pada beban selama pengeboran atau pembilasan sumur; mengangkat tali bor dan pipa selama perpanjangan ; transmisi rotasi ke rotor; make-up dan break-out pipa; pekerjaan tambahan untuk menarik alat, peralatan, pipa, dll. ke dalam rig pengeboran; mengangkat menara rakitan ke posisi vertikal.
Drawwork terdiri dari rangka yang dilas di mana poros pengangkat dan transmisi, gearbox, sistem rem, termasuk rem utama (pita) dan bantu (penyetelan), dan panel kontrol dipasang. Semua mekanisme ditutupi dengan pelindung keselamatan. Poros pengangkat winch, menerima rotasi dari gearbox, mengubah gerakan rotasi penggerak daya menjadi gerakan translasi tali perjalanan, ujung yang dapat digerakkan dipasang pada drum poros pengangkat. Kait yang dimuat naik dengan konsumsi daya, tergantung pada berat pipa yang diangkat, dan turun di bawah aksi berat sendiri dari pipa atau blok perjalanan, kait dan lift, ketika lift turun untuk lilin berikutnya.
Derek dilengkapi dengan perangkat untuk memasok daya saat mengangkat tali dan perangkat pengereman untuk menyerap energi yang dilepaskan saat menurunkannya. Untuk meningkatkan efisiensi selama pengangkatan kait dengan elevator yang tidak dimuat atau kolom dengan berat variabel, derek atau penggeraknya memiliki kecepatan ganda. Perpindahan dari kecepatan tinggi ke kecepatan rendah dan sebaliknya dilakukan dengan kopling operasional gesekan, memberikan penyalaan yang mulus dan waktu yang dihabiskan untuk operasi ini minimal. Selama pengangkatan kolom dengan berbagai bobot, kecepatan di kotak roda gigi dialihkan secara berkala. Kontrol kecepatan operasional kotak tidak diperlukan.
Daya yang ditransmisikan ke winch mencirikan sifat operasional dan teknis utamanya dan merupakan parameter klasifikasi.
Rotor dirancang untuk memutar tali bor yang digantung secara vertikal atau untuk menyerap torsi reaktif saat mengebor dengan motor lubang bawah. Mereka juga berfungsi untuk menopang berat tali bor atau selubung yang dipasang di atas mejanya, di lift atau baji. Rotor juga digunakan dalam breakout pipa dan make-up dalam operasi tersandung, memancing, dan darurat. Rotor, seolah-olah, adalah peredam roda gigi bevel, roda bevel yang digerakkan yang dipasang pada busing yang terhubung ke meja. Sumbu vertikal meja terletak di sepanjang sumbu sumur.
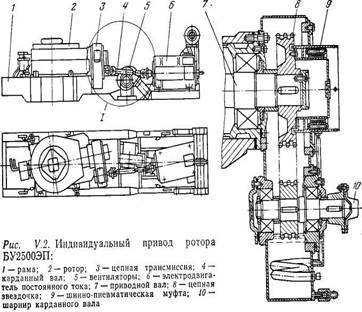
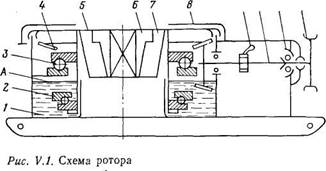
di 3 utama dan bantu 2 mendukung dipasang di perumahan 1, yang secara bersamaan membentuk penangas oli untuk melumasi transmisi dan bantalan.
Bagian atas meja dilindungi oleh pagar. 8. poros penggerak kecepatan tinggi 10 terletak horizontal pada bantalan 11, menerima beban radial dan horizontal. Batang 10 didorong: dalam rotasi dari sproket rantai 12 atau dengan menggunakan kuk poros kardan yang terletak di ujung poros. Rotor dilengkapi dengan stopper 9, saat diaktifkan, rotasi tabel menjadi tidak mungkin. Fiksasi meja rotor diperlukan selama trip dan pengeboran dengan motor downhole untuk persepsi torsi reaktif.
Pompa Lumpur dan Peralatan Sistem Sirkulasi
Pompa lumpur dan sistem sirkulasi melakukan fungsi-fungsi berikut:
Injeksi cairan pengeboran ke dalam string bor untuk memastikan sirkulasi di dalam sumur selama pengeboran dan pembersihan yang efektif dari lubang bawah dan bit dari pemotongan, pembilasan, likuidasi kecelakaan, menciptakan laju kenaikan cairan di anulus yang cukup untuk membawa batu ke permukaan;
Catu daya hidraulik ke bit, memberikan laju aliran tinggi (hingga 180 m / s) larutan dari nozelnya untuk penghancuran sebagian batu dan membersihkan lubang bawah dari partikel yang dibor;
Catu daya ke motor downhole hidrolik.
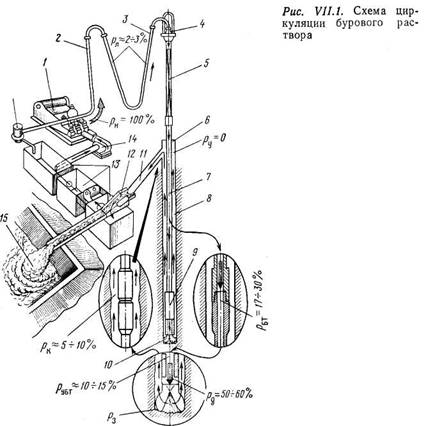
Selama proses pengeboran, dalam banyak kasus, larutan bersirkulasi dalam sirkuit tertutup. Dari tank 13 solusi yang dibersihkan dan disiapkan memasuki pompa booster 14, yang diumpankan ke pompa pengeboran /. Yang terakhir memompa larutan di bawah tekanan tinggi (hingga 30 MPa) melalui saluran pembuangan, melalui riser 2, lengan fleksibel 3, memutar 4, Kelly 5 k kepala sumur 6. Bagian dari tekanan pompa digunakan untuk mengatasi hambatan dalam sistem tanah. Selanjutnya, cairan pengeboran melewati string bor 7 (pipa bor, kerah bor dan motor downhole 9) sedikit 10. Pada jalur ini, tekanan larutan berkurang karena pengeluaran energi untuk mengatasi hambatan hidrolik.
Kemudian cairan pengeboran, karena perbedaan tekanan di dalam pipa bor dan di dasar sumur, keluar dari nozel bit dengan kecepatan tinggi, membersihkan bagian bawah dan bit dari stek. Sisa energi fluida dihabiskan untuk mengangkat stek dan mengatasi hambatan di annulus annulus 8.
Diangkat ke permukaan ke mulut 6 solusi yang dihabiskan melewati selokan 11 ke unit kebersihan 12, di mana dari itu dipindahkan ke gudang 15 stek, pasir, lumpur, gas dan kotoran lainnya masuk ke tangki 13 dengan perangkat 16 untuk mengembalikan parameternya dan dikirim lagi ke pompa booster.Jalur injeksi terdiri dari pipa bertekanan tinggi yang membawa larutan dari pompa / ke riser 2 dan lengan fleksibel 3, menghubungkan riser 2 dengan putar 4. Garis tekanan dilengkapi dengan katup dan instrumentasi. Untuk pekerjaan di daerah dengan iklim dingin, sistem pemanas pipa disediakan.
Sistem pembuangan dilengkapi dengan perangkat untuk pembersihan dan persiapan cairan pengeboran, tangki, saluran hisap, filter, injeksi pompa sentrifugal, katup dan wadah untuk menyimpan larutan.
memutar
Putar adalah penghubung antara blok perjalanan yang bergerak secara progresif dengan pengait, selongsong bor dan tali bor yang berputar, yang dihubungkan melalui pipa utama ke poros putar dengan menggunakan ulir pengunci. Untuk memastikan pasokan cairan atau gas pengeboran, swivel yang bergerak dihubungkan ke saluran tekanan menggunakan selang pengeboran yang fleksibel, yang salah satu ujungnya dipasang ke outlet putar, dan ujung lainnya ke riser.
Putar memiliki perangkat untuk mengisi, mengalirkan minyak dan mengontrol levelnya, serta pernapasan untuk menyeimbangkan dengan tekanan uap atmosfer di dalam tubuh, yang dibuat selama pemanasan selama operasi. Perangkat ini tidak membocorkan oli saat memindahkan swivel dalam posisi horizontal.
Ukuran putar ditentukan oleh beban dinamis yang dapat diambil selama rotasi string bor, beban statis yang diizinkan dan kecepatan rotasi, tekanan operasi maksimum dari cairan pengeboran yang dipompa, berat dan dimensi keseluruhan. Setiap putar memiliki ulir pengunci lancip kiri standar untuk sambungan ke pipa utama dalam dua hingga tiga ukuran. Badan swivel dibuat dalam bentuk streamline agar tidak menempel pada bagian-bagian menara saat bergerak. Putar disesuaikan untuk transportasi dengan alat transportasi apa pun tanpa kemasan.
Penggerak daya rig pengeboran
Penggerak rig pengeboran adalah seperangkat mesin dan transmisi yang mengatur operasinya dan perangkat yang mengubah energi panas atau listrik menjadi energi mekanik, mengontrol energi mekanik dan mentransfernya ke peralatan penggerak - pompa, rotor, winch, dll. Daya penggerak (pada input ke transmisi) mencirikan konsumen utamanya dan sifat teknisnya dan merupakan parameter klasifikasi (utama).
Tergantung pada sumber energi utama yang digunakan, drive dibagi menjadi otonom, independen dari sistem catu daya, dan non-otonom, tergantung pada sistem catu daya, didukung oleh jaringan listrik industri. Penggerak otonom mencakup mesin pembakaran internal (ICE) dengan transmisi mekanis, hidraulik, atau elektrik. Penggerak non-otonom meliputi: motor listrik arus searah didukung oleh jaringan AC industri.
Sesuai dengan kinematika instalasi, drive dapat memiliki tiga versi utama: individu, grup dan gabungan atau campuran.
Drive individu- setiap aktuator (winch, pompa atau rotor) digerakkan oleh motor listrik atau mesin pembakaran internal secara independen satu sama lain. Jenis penggerak ini lebih banyak digunakan dengan motor listrik. Saat menggunakannya, kemampuan manuver yang tinggi dicapai dalam tata letak dan penempatan peralatan pengeboran di pangkalan selama pemasangan.
Drive grup- beberapa mesin dihubungkan oleh transmisi penjumlahan dan menggerakkan beberapa aktuator. Ini digunakan dalam mesin pembakaran internal.
Drive gabungan- penggunaan drive individu dan grup dalam satu instalasi. Misalnya, pompa digerakkan oleh mesin individual, sedangkan winch dan rotor digerakkan oleh mesin biasa. Dalam semua kasus, karakteristik drive harus sepenuhnya memenuhi karakteristik aktuator yang diperlukan.
Konsumen energi rig pengeboran adalah:
dalam proses pengeboran - pompa lumpur, rotor (dalam hal pengeboran putar), perangkat untuk menyiapkan dan membersihkan cairan pengeboran dari stek; kompresor, pompa air, dll .;
saat menurunkan dan menaikkan tali pipa - winch, kompresor, pompa air, dan kunci mekanis.
Drive juga dibagi menjadi drive utama (drive winch, pompa dan rotor) dan drive tambahan (drive perangkat lain dan mekanisme pemasangan). Daya yang dikonsumsi oleh perangkat tambahan tidak melebihi 10-15% dari daya yang dikonsumsi oleh peralatan utama.
Karakteristik fleksibilitas- kemampuan penggerak daya untuk secara otomatis atau dengan partisipasi operator dalam proses cepat beradaptasi dengan perubahan beban dan kecepatan rotasi aktuator. Fleksibilitas karakteristik tergantung pada koefisien kemampuan beradaptasi, rentang pengaturan frekuensi rotasi poros penggerak daya dan respons throttle engine.
Faktor fleksibilitas karakteristik ditentukan oleh rasio perubahan kecepatan dengan penyimpangan torsi beban yang disebabkan olehnya. Ini sebanding dengan rasio roda gigi dan berbanding terbalik dengan faktor kelebihan beban.
ambil disebut intensitas pelaksanaan transien, yaitu, waktu di mana mesin dan penggerak daya merespons perubahan beban dan perubahan kecepatan.
Kemampuan beradaptasi- properti penggerak daya untuk mengubah torsi dan kecepatan tergantung pada momen resistensi. Kemampuan beradaptasi sendiri - properti mesin untuk beradaptasi dengan beban eksternal. Kemampuan beradaptasi buatan - properti transmisi untuk menyesuaikan karakteristik mesin dengan perubahan beban eksternal.
Peralatan penyegelan kepala sumur
Saat ini, ketika pengeboran tidak hanya eksplorasi, tetapi juga sumur produksi, peralatan penyegelan kepala sumur banyak digunakan. Sebelumnya, peralatan ini terutama digunakan untuk mengontrol emisi cair dan gas selama AHRP. Sehubungan dengan penggunaan cairan pemboran yang lebih ringan, maka tekanan di dalam sumur selama proses pemboran diatur dengan menggunakan pencegah. Persyaratan untuk perlindungan lingkungan dan perut bumi telah berubah.
Untuk menutup kepala sumur, tiga jenis pencegah digunakan: ram - tuli atau tembus untuk sepenuhnya memblokir lubang atau ruang annular, jika ada tali pipa di dalam sumur; universal - untuk menutup lubang di sumur, jika ada bagian dari string bor: kunci, pipa, Kelly; berputar - untuk menyegel kepala sumur dengan pipa berputar di dalamnya atau pipa terkemuka. Baik ram maupun pencegah universal tidak dirancang untuk memutar senar jika benar-benar tertutup.
Ram BOP
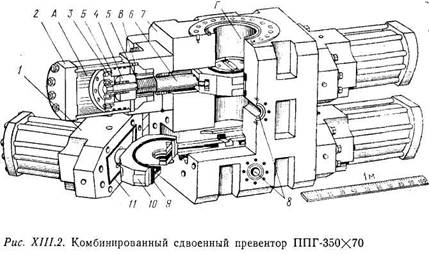
Piston bantu 4 juga bergerak ke kanan, dan di posisi terakhir dia menekan cincin kait 5 dan dengan demikian memperbaiki dadu 10 dalam keadaan tertutup, yang tidak termasuk pembukaan spontannya. Untuk membuka lubang G barel, Anda perlu memindahkan mati ke kiri. Untuk melakukan ini, cairan kontrol harus disuplai di bawah tekanan ke rongga B, yang menggerakkan piston bantu 4 berdasarkan stok 6 ke kiri dan membuka kait 5. Piston ini, setelah mencapai pemberhentian di piston utama 3, memindahkannya ke kiri, sehingga mengungkapkan dadu. Dalam hal ini, cairan kontrol, yang terletak di rongga £, diperas ke dalam sistem kontrol.
Meninggal 10 pencegah dapat diganti tergantung pada diameter pipa yang akan disegel. Ujung cetakan di sekitar keliling disegel dengan manset karet 9, penutup 1 - paking //. Masing-masing pencegah dikendalikan secara independen, tetapi kedua domba jantan dari masing-masing pencegah beroperasi secara bersamaan. lubang 8 di housing 7 digunakan untuk menghubungkan pencegah ke manifold. Ujung bawah selubung terpasang ke flensa kepala sumur, dan pencegah universal dipasang ke ujung atasnya.
Seperti yang Anda lihat, BOP ram yang dikontrol secara hidraulik harus memiliki dua jalur kontrol: satu untuk mengontrol fiksasi posisi ram, yang kedua untuk memindahkannya. BOP yang dikontrol secara hidraulik terutama digunakan dalam pengeboran lepas pantai. Dalam beberapa kasus, pencegah yang lebih rendah dilengkapi dengan domba jantan dengan pisau geser untuk memotong tali pipa di dalam sumur.
Pencegah universal
Pencegah universal dirancang untuk meningkatkan keandalan penyegelan kepala sumur. Elemen kerja utamanya adalah segel elastis annular yang kuat, yang, ketika pencegah terbuka, memungkinkan tali bor lewat, dan ketika pencegah ditutup, itu dikompresi, akibatnya segel karet menekan pipa (kelly , kunci) dan menyegel ruang annular antara string bor dan selubung. Elastisitas segel karet memungkinkan untuk menutup pencegah pada pipa dengan berbagai diameter, pada kunci dan kerah bor. Penggunaan pencegah universal memungkinkan untuk memutar dan menjalankan tali dengan celah annular yang disegel.
Cincin-O dikompresi baik oleh gaya hidraulik langsung yang bekerja pada elemen penyegelan atau oleh gaya yang bekerja pada segel melalui piston annular khusus.
Pencegah universal dengan elemen penyegelan bulat dan dengan penyegelan kerucut diproduksi oleh VZBT.
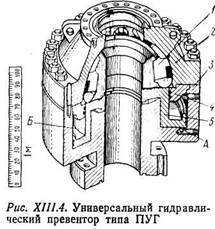
Saat melamar cairan kerja bawah plunger 5 melalui lubang di badan pencegah, plunger bergerak ke atas dan menekan segel / sekitar bola sehingga mengembang ke tengah dan menekan pipa di dalam segel cincin. Dalam hal ini, tekanan fluida pemboran di dalam sumur akan bekerja pada plunger dan menekan seal. Jika tidak ada kolom di dalam sumur, segel benar-benar menutupi lubang. Ruang atas B berfungsi untuk membuka pencegah. Ketika minyak disuntikkan ke dalamnya, plunger bergerak ke bawah, memindahkan cairan dari ruang A ke saluran pembuangan.
Pencegah putar
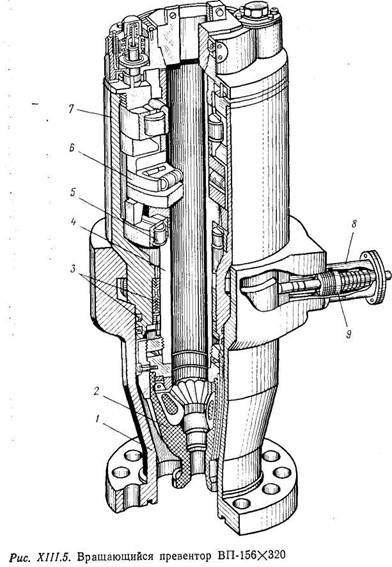
Sebuah rotary preventer digunakan untuk menutup kepala sumur selama pengeboran selama rotasi dan timbal balik dari string bor, serta selama tersandung dan peningkatan tekanan di dalam sumur. Pencegah ini menyegel kelly, mengunci atau mengebor pipa, memungkinkan Anda untuk menaikkan, menurunkan atau memutar string bor, mengebor dengan backflushing, dengan lumpur aerasi, dengan pembersihan agen gas, dengan sistem keseimbangan tekanan hidrostatik pada formasi, menguji formasi di proses pertunjukan gas.
II . Bagian teknologi
1. Pengeboran sumur minyak dan gas
Pembiasaan dengan metode pengumpanan bit manual, pengeboran dengan pengatur pengumpanan bit, pelatihan pengeboran dengan rotor.
Ketika bit diumpankan ke bawah, perlu untuk membuat beban tertentu di atasnya. Operasi ini dilakukan dari konsol pengebor. Pengebor, menggunakan apa yang disebut poker, menurunkan alat, dan kemudian secara bertahap, dengan sangat perlahan menurunkan beban dari pengait ke mata bor. Beban pada wireline ditentukan oleh indikator berat. Pada indikator, harga pembagian bisa berbeda. Ketika sistem perjalanan ditangguhkan, tetapi pengait tidak dimuat, indikator berat akan menunjukkan nilai yang sesuai dengan berat sistem perjalanan.
WOB harus sama dengan tidak lebih dari 75% dari berat tali kerah bor. Misalnya, ada tata letak: 100 m kerah bor dan 1000 m pipa bor. Misalkan berat tali UBT adalah 150 kN, dan berat tali BT adalah 300 kN. Berat total BC dalam hal ini adalah 450 kN. Kira-kira 2/3 dari berat kerah bor harus diumpankan ke penyembelihan, mis. dalam hal ini 100 kN. Untuk melakukan ini, tali diturunkan dengan mulus sebesar 9 m (panjang pipa yang dapat ditumpuk) ke bawah. Momen kontak bit dengan bagian bawah ditentukan oleh indikator berat: panah menunjukkan penurunan berat pada kait. Setelah itu, perlu untuk melepaskan winch dengan sangat perlahan dan memuat bit secara bertahap sampai panah pada indikator berat menunjukkan 35 ton. pada indikator massa, osilasi panah mungkin tidak selalu terlihat. Ini menunjukkan berapa banyak divisi yang telah dilewati panah pada indikator bobot, mis. 3 divisi Werner sama dengan 1 divisi indikator massa.
Rotor digunakan untuk mentransmisikan putaran ke string bor selama pengeboran, untuk menahannya selama perjalanan pulang pergi dan pekerjaan bantu.
Rotor adalah gearbox yang mentransmisikan rotasi ke kolom yang ditangguhkan secara vertikal dari poros transmisi horizontal. Rangka rotor menerima dan mentransfer ke dasar semua beban yang terjadi selama operasi pengeboran dan tripping. Rongga internal tempat tidur adalah penangas minyak. Di ujung luar poros rotor, pada kuncinya, mungkin ada sproket atau setengah kopling poros kardan. Saat membuka mata bor atau untuk mencegah rotasi tali bor dari aksi momen tidak aktif, rotor dikunci dengan gerendel atau mekanisme pengunci. Ketika rotasi ditransmisikan ke rotor dari mesin melalui winch, rotor kecepatan diubah menggunakan mekanisme transmisi winch atau dengan mengganti roda sproket. Agar tidak menghubungkan pekerjaan winch dengan pekerjaan rotor, dalam beberapa kasus, saat pengeboran putar, drive individual ke rotor digunakan, yaitu, tidak terhubung dengan winch.
2 sisipan dimasukkan ke dalam lubang melalui rotor. Kemudian, tergantung pada diameter pipa, irisan yang sesuai ditempatkan pada rotor, yang dipasang pada empat paralel. Paralel, pada gilirannya, digerakkan dengan bantuan RCC (baji rotor pneumatik), yang dipasang di sisi berlawanan dari poros rotor. Menggunakan pedal, yang terletak di konsol, juru bor menaikkan atau menurunkan irisan.
Saat pengeboran dimulai, irisan dikeluarkan dari rotor, sehingga membebaskan lubang persegi liner. Kemudian apa yang disebut kelbush dipasang di lubang ini - mur dipasang secara bergerak pada pipa utama, yang bergerak naik dan turun di sepanjang itu. Selanjutnya, dengan bantuan transmisi, putaran rotor yang diperlukan diatur, dan digerakkan dari konsol bor.
Pembiasaan dengan metodologi pengembangan rasional bit.
Untuk mengerjakan bit secara rasional, perlu untuk memenuhi tingkat penetrasi. Saat lubang dasar semakin dalam, alat pemotong batu aus, dan untuk mencegah keausan terjadi sebelumnya, perlu untuk mengamati mode pengeboran.
Mode pengeboran termasuk RPM motor rotor atau downhole, WOB dan tekanan pompa (pada riser). Jadi, untuk pengembangan mata bor yang benar, beban di atasnya harus lebih dari 75% dari berat tali kerah bor. Membebani bit yang berlebihan dapat mengakibatkan keausan dini atau kerusakan kerucut, dan beban yang kurang dapat menyebabkan penurunan penetrasi. Kecepatan rotor dan tekanan pada riser diatur sesuai dengan garis geologis dan teknis.
Untuk pengembangan bit yang rasional, perlu untuk memasukkannya ke bawah tanpa rotasi dan menyalakan putaran hanya setelah kontak dengan bagian bawah. Tetapi sebelum mulai mengebor, mata bor harus "masuk" selama 30-40 menit agar bisa masuk. Pada saat yang sama, berat bit harus kecil - sekitar 3-5 ton Saat mengebor dengan turbodrill atau motor lubang bawah sekrup, mata bor diumpankan ke lubang bawah yang sudah berputar. Dalam hal ini, Anda dapat menghentikan pembilasan dan menurunkan bit ke bawah, atau, tanpa menghentikan pembilasan, secara bertahap memuat bit ke nilai yang diperlukan.
Pengkodean keausan bit kerucut:
B - memakai senjata (setidaknya satu mahkota)
B1 - pengurangan tinggi gigi sebesar 0,25%
B2 - pengurangan ketinggian gigi sebesar 0,5%
B3 - pengurangan tinggi gigi sebesar 0,75%
B4 - keausan total pada gigi
C - chip gigi dalam%
P - keausan penyangga (setidaknya satu pemotong)
P1 - permainan radial pemotong relatif terhadap sumbu trunnion untuk bit
diameter kurang dari 216 mm 0-2 mm; untuk bit yang lebih besar dari
216mm 0-4mm
P2 - permainan radial pemotong relatif terhadap sumbu trunnion untuk bit
diameter kurang dari 216 mm 2-5 mm; untuk bit yang lebih besar dari
216 mm 4-8 mm
P3 - permainan radial pemotong relatif terhadap sumbu trunnion untuk bit
diameter kurang dari 216 mm lebih dari 5 mm; untuk bit yang lebih besar dari
216 mm lebih dari 8 mm
P4 - penghancuran elemen bergulir
K - kemacetan pemotong (nomornya ditunjukkan dalam tanda kurung)
D - pengurangan diameter bit (mm)
A - keausan darurat (jumlah pemotong dan cakar yang tersisa ditunjukkan dalam tanda kurung)
AB (A1) - kerusakan dan meninggalkan bagian atas kerucut di bagian bawah
ASh (A2) - dalam kerusakan dan meninggalkan kerucut di bagian bawah
AC (A3) - meninggalkan cakar di bagian bawah
Penyebab keausan yang tidak normal dari bit kerucut:
1) Sejumlah besar gigi patah:
Pilihan bit yang salah
Pembobolan bit yang salah
Kecepatan berlebih
Kerja logam
2) Keausan yang kuat pada diameter:
Kecepatan tinggi
Meremas kerucut sebagai akibat turun ke batang dengan diameter yang dikurangi
3) Erosi tubuh kerucut:
Konsumsi besar cairan pembilasan
4) Keausan bantalan yang berlebihan:
Kurangnya stabilizer di atas mata bor atau di antara kerah bor
Kecepatan tinggi
Waktu pengeboran mekanis yang signifikan
5) Penyumbatan ruang antar-mahkota di pemotong dengan batu bor dan fase padat:
Konsumsi pankreas yang tidak mencukupi
Pahat dirancang untuk formasi yang lebih keras
Bit diturunkan ke zona lubang bawah yang diisi dengan stek
6) Sejumlah besar gigi yang hilang:
Erosi tubuh kerucut
Waktu pengeboran mekanis yang signifikan
Melakukan pekerjaan dasar dengan perangkat lunak open source menggunakan peralatan khusus
Unit utama dalam pelaksanaan trip adalah drawworks, yang digerakkan oleh power drive. Untuk penggunaan daya terbaik selama pengangkatan kait beban variabel, transmisi penggerak winch atau penggerak winch harus multi-kecepatan. Winch harus dengan cepat beralih dari kecepatan pengangkatan tinggi ke kecepatan rendah dan sebaliknya, memastikan penyalaan terencana dengan jumlah waktu minimum yang dihabiskan untuk operasi ini. Dalam kasus pelekatan dan pengencangan senar, gaya tarikan selama pengangkatan harus ditingkatkan dengan cepat. Kecepatan switching untuk mengangkat kolom dengan massa yang berbeda dilakukan secara berkala.
Derek bantu dan pneumobrancher digunakan untuk melakukan pekerjaan menarik beban dan memasang sekrup pada pipa selama SPO.
Pemutus pneumatik dirancang untuk membuka sambungan alat pipa bor. Pneumobrancher terdiri dari silinder di mana piston dengan batang bergerak. Silinder ditutup di kedua ujungnya dengan tutup, salah satunya memiliki segel batang. Kabel logam dipasang pada batang di sisi berlawanan dari piston, ujung lainnya diletakkan pada kunci mesin. Di bawah aksi udara terkompresi, piston bergerak dan memutar kunci mesin melalui kabel. Gaya maksimum yang dikembangkan oleh silinder pneumatik pada tekanan udara tekan 0,6 MPa adalah 50...70 kN. Langkah piston (batang) silinder pneumatik adalah 740 ... 800 mm.
Kompleks mekanisme ASP dirancang untuk mekanisasi dan otomatisasi parsial dari operasi tripping. Ini menyediakan:
- kombinasi saat mengangkat dan menurunkan tali pipa dan lift yang diturunkan dengan operasi memasang dudukan pada dudukan, melepaskannya dari dudukan, serta memasang atau memasang dudukan dengan tali bor;
- mekanisasi pemasangan lilin pada kandil dan pemindahannya ke tengah, serta penangkapan atau pelepasan tali pipa bor dengan lift otomatis.
Mekanisme ASP meliputi: mekanisme pengangkatan (menaikkan dan menurunkan lilin yang diputar secara terpisah); mekanisme pencengkeraman (menangkap dan menahan lilin yang tidak dibuka saat mengangkat, menurunkan, memindahkannya dari rotor ke kandil dan sebaliknya); mekanisme penempatan (memindahkan lilin dari tengah sumur dan kembali); centralizer (memegang bagian atas lilin di tengah menara selama pemasangan dan pemasangan); elevator otomatis (pengambilan dan pelepasan otomatis kolom BT selama penurunan dan pendakian); majalah dan kandil (memegang lilin yang tidak dibuka dalam posisi vertikal).
Dalam pekerjaan mekanisme yang kompleks seperti ASP-ZM1, ASP-ZM4. ASP-ZM5 dan ASP-ZM6 menggunakan kunci AKB-ZM2 dan pegangan baji pneumatik BO-700 (kecuali untuk ASP-ZM6, yang digunakan pegangan PKRBO-700).
Mempersiapkan pipa untuk diseret, memasang elevator pada rotor, melepaskannya dari rotor, menempatkan pipa pada baji
Sebelum menarik pipa ke rig, perlu dilakukan inspeksi visual terhadap badan pipa dan ulirnya. Untuk analisis yang akurat, tim pendeteksi cacat dipanggil, yang, dengan menggunakan instrumen, menentukan kesesuaian pipa untuk digunakan pada rig pengeboran. Selain itu, perlu, jika perlu, untuk membersihkan sambungan berulir pipa, dan kemudian melumasinya dengan minyak grafit atau gemuk. Setelah itu, pipa dikirim ke jembatan penerima.
Selama pengeboran, pipa bor diseret satu per satu dari trotoar ke rotor dengan bantuan winch tambahan. Kemudian pipa yang dikirim disekrup ke tali, dan lubang bawah semakin dalam dengan panjang pipa yang diperpanjang.
Mengangkat dan menurunkan pipa bor untuk mengganti mata bor yang aus terdiri dari operasi berulang yang sama. Selain itu, mesin termasuk operasi mengangkat lilin dari sumur dan lift kosong. Semua operasi lainnya adalah mesin-manual atau manual yang membutuhkan upaya fisik yang besar. Ini termasuk:
· saat mengangkat: pendaratan kolom di lift; membuka koneksi berulir; memasang lilin pada kandil; penurunan lift kosong; transfer tautan ke lift yang dimuat dan pengangkatan kolom ke ketinggian lilin;
· saat turun: penarikan lilin dari belakang jari dan dari kandil; memasang lilin ke kolom; menurunkan tali ke dalam sumur; pendaratan kolom di lift; transfer link ke lift gratis. Perangkat untuk mencengkeram dan menggantung kolom bervariasi dalam ukuran dan kapasitas beban.
Biasanya peralatan ini diproduksi untuk pipa bor dengan ukuran 60, 73, 89, 114, 127, 141, 169 mm dengan kapasitas beban pengenal 75, 125, 140, 170, 200, 250, 320 ton. pipa dengan diameter 194 hingga 426 mm, irisan dalam empat ukuran: 210, 273, 375 dan 476 mm, dirancang untuk kapasitas angkat dari 125 hingga 300 ton.
Lift digunakan untuk menangkap dan menahan berat pipa bor (casing) selama operasi tripping dan pekerjaan lain di rig pengeboran. Berbagai jenis elevator digunakan, berbeda ukurannya tergantung pada diameter pipa bor atau selubung, kapasitas beban, penggunaan konstruktif, dan bahan untuk pembuatannya. Lift ditangguhkan dari kait pengangkat dengan bantuan sling.
Potongan pipa bor digunakan untuk menggantung alat bor di meja rotor. Mereka dimasukkan ke dalam lubang kerucut rotor. Penggunaan wedges mempercepat pekerjaan pada operasi tersandung. Baru-baru ini, pegangan baji otomatis dengan penggerak pneumatik tipe PKR telah banyak digunakan (dalam hal ini, baji dimasukkan ke dalam rotor tidak secara manual, tetapi dengan bantuan penggerak khusus, yang dikendalikan oleh konsol pengebor).
Untuk menurunkan senar casing yang berat, digunakan wedges dengan bodi non-split. Mereka dipasang pada bantalan khusus di atas kepala sumur. Baji terdiri dari tubuh besar yang menerima berat pipa casing. Di dalam tubuh ada cetakan yang dirancang untuk menangkap pipa selubung dan menahannya dalam keadaan tersuspensi. Mengangkat dan menurunkan cetakan dilakukan dengan memutar pegangan ke satu arah atau lainnya di sekitar baji, yang dicapai dengan adanya guntingan koreksi miring di tubuh, di mana rol cetakan digulung dengan bantuan tuas.
Memeriksa ulir pengunci, memasang BT dengan bantuan kunci baterai, memasang kembali dan melepaskan sambungan kunci dengan bantuan kunci UMK
Dalam proses SPO, pipa perlu disekrup dan dibuka berulang kali. Untuk menyederhanakan operasi ini, rig pengeboran dilengkapi dengan peralatan khusus. Sebuah alat khusus digunakan untuk membuat dan membuka tutup pipa bor dan pipa casing. Berbagai kunci digunakan sebagai alat tersebut. Beberapa di antaranya dimaksudkan untuk memasang sekrup, dan yang lainnya - untuk mengencangkan dan melepaskan sambungan berulir kolom. Biasanya, kunci pas pra-make-up serba ringan dirancang untuk kunci dengan satu diameter, dan kunci pas mesin berat untuk sambungan pengikat dan tidak berulir dirancang untuk dua, dan terkadang lebih banyak ukuran pipa bor dan kunci.
Kunci rantai digunakan untuk memutar pipa secara manual. Ini terdiri dari pegangan dan rantai dengan perangkat pemasangan. Untuk menangkap pipa, rantai membungkusnya dan dipasang di bagian atas pegangan. Bekerja dengan kunci pas rantai sangat memakan waktu, jadi peralatan lain digunakan.
Tong pengeboran otomatis baterai dirancang untuk sekrup mekanis dan sekrup pipa. Panel kontrol terletak di stasiun bor dan dilengkapi dengan dua tuas: salah satunya mengontrol pergerakan kunci itu sendiri ke rotor dan belakang dan mekanisme pencengkeram pipa, dan dengan bantuan yang lain, pipa disekrup bersama. . AKB sangat menyederhanakan proses perangkat lunak open source.
Pengoperasian pengikatan dan pelepasan sambungan ulir dari senar bor dan selubung dilakukan oleh dua kunci mesin UMK; sementara satu kunci (penundaan) diperbaiki, dan yang kedua (sekrup) dapat dipindahkan. Kunci ditangguhkan dalam posisi horizontal. Untuk melakukan ini, rol logam diperkuat pada "jari" khusus di dekat geladak dan tali pengikat baja atau satu untai tali keliling dilemparkan melaluinya. Salah satu ujung tali ini dilekatkan pada gantungan kunci dan ujung lainnya dipasang pada counterweight yang menyeimbangkan kunci dan memudahkan untuk memindahkan kunci ke atas atau ke bawah.
Saat menurunkan pipa bor dan kerah bor ke dalam sumur, sambungan berulir harus dikencangkan dengan mesin dan kunci pas otomatis, mengontrol celah antara elemen penghubung dan mengamati, menurut pengukur torsi, nilai torsi yang diizinkan yang ditetapkan oleh instruksi saat ini.
Pemeriksaan dan pengukuran BT dan collar, pemasangan BT pada candlestick, memasang dan melepas pahat
Sebelum memulai pengeboran, perlu untuk memeriksa semua pipa yang terletak di rig pengeboran. Perhatian khusus harus diberikan untuk memeriksa koneksi berulir. Benang pada pipa bor aus selama operasi, sehingga panjang benang dan diameternya harus diukur secara berkala. Ini dilakukan dengan bantuan pita pengukur. Penyimpangan yang diizinkan dalam ukuran ulir adalah 3-4 mm. Template khusus digunakan untuk memeriksa ukuran pipa. Diameter setiap template sesuai dengan diameter pipa tertentu.
Dalam proses pendalaman lubang dasar, string bor terus tumbuh. Untuk melakukan ini, pipa bor diseret dari jembatan dengan bantuan winch tambahan ke rotor, dihubungkan oleh lift dan kemudian disekrup ke ulir pipa yang dipasang pada irisan.
Bila perlu untuk mengangkat tali, pipa dibuka dengan lilin untuk mengurangi waktu perjalanan. Dalam hal ini, perlu untuk menaikkan ujung atas pipa di atas meja rotor, meletakkannya di baji dan memperbaikinya di lift. Kemudian kolom naik ke ketinggian lilin, duduk di atas irisan, lilin dibuka dengan kunci baterai, digulung oleh jari pekerja berkuda dan setengah terpasang dan ditempatkan di kandil. Setelah operasi yang diperlukan telah dilakukan (perubahan bit, BHA), senar diturunkan dengan lilin ke kedalaman yang dibor.
Memasang dan membuka mata kerucut dilakukan dengan bantuan sandaran tangan. Pahat dipasang secara manual atau dengan bantuan winch tambahan di sandaran tangan. Di dalamnya ada 3 tonjolan yang masuk di antara pemotong. Kemudian chuck ditempatkan pada liner rotor, dan mata bor disekrup ke kerah bor atau sub. Bit dayung dipasang pada rotor menggunakan dudukan khusus sehingga hanya satu ulir yang tersisa di atas meja, dan kemudian disekrup ke pipa.
Pembilasan dengan baik
Pembilasan sumur adalah bagian utama dari pengeboran. Seberapa baik sumur akan dibawa ke kedalaman desain tergantung pada formulasi solusi yang dipilih dengan benar.
Dalam praktek pemboran sumur, berbagai metode teknologi digunakan untuk penyiapan fluida pemboran.
Diagram alir paling sederhana (Gbr. 7.2) termasuk wadah untuk mencampur komponen fluida pengeboran 1, dilengkapi dengan agitator mekanik dan hidrolik 9, mixer jet hidro 4, dilengkapi dengan corong pemuatan 5 dan pintu geser 8, pompa sentrifugal atau piston 2 (biasanya salah satu pompa booster) dan manifold.
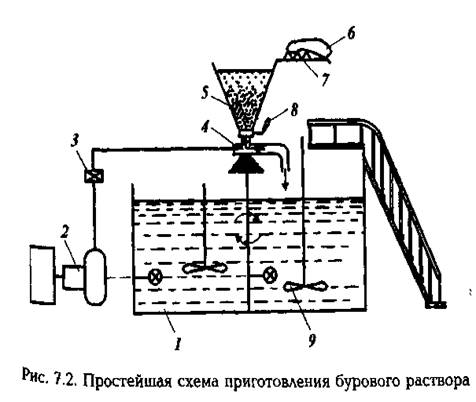
Menurut skema ini, persiapan solusi dilakukan sebagai berikut. dalam wadah 1 mengisi jumlah media dispersi yang dihitung (biasanya 20-30 m 3) dan menggunakan pompa 2 melalui saluran pembuangan dengan katup 3 itu diumpankan melalui mixer hidro-ejector 4 dalam lingkaran tertutup. Tas 6 detik bahan tepung diangkut dengan lift bergerak atau konveyor ke platform tangki, dari mana bahan tersebut diumpankan ke platform 7 dengan bantuan dua pekerja dan dipindahkan secara manual ke lingkungan corong 5. Suspensi dikeringkan ke dalam wadah, di mana dicampur secara menyeluruh dengan mixer mekanis atau hidrolik 9. Laju pengumpanan material ke dalam ruang pencampur ejektor dikendalikan oleh pintu geser 8, dan kevakuman di dalam ruang dikendalikan oleh yang dapat diganti nozel paduan keras.
Kerugian utama dari teknologi yang dijelaskan adalah mekanisasi kerja yang buruk, pasokan komponen yang tidak merata ke zona pencampuran, dan kontrol yang buruk terhadap proses. Menurut skema yang dijelaskan, tingkat maksimum persiapan larutan tidak melebihi 40 m 3 / jam.
Saat ini, dalam praktik domestik, teknologi progresif untuk persiapan solusi pengeboran dari bahan bubuk banyak digunakan. Teknologi ini didasarkan pada penggunaan peralatan yang tersedia secara komersial: unit persiapan solusi (BPR), mixer hidro-ejektor eksternal, penyebar hidraulik, tangki CS, mixer mekanis dan hidraulik, dan pompa piston.
Untuk membersihkan cairan pengeboran dari stek, kompleks berbagai perangkat mekanis digunakan: saringan getar, pemisah lumpur hidrosiklon (pemisah pasir dan lumpur), pemisah, sentrifugal. Selain itu, dalam kondisi yang paling tidak menguntungkan, sebelum dibersihkan dari stek, lumpur pengeboran diperlakukan dengan reagen flokulan, yang memungkinkan untuk meningkatkan efisiensi perangkat pembersih.
Terlepas dari kenyataan bahwa sistem pembersihan itu rumit dan mahal, dalam banyak kasus penggunaannya hemat biaya karena peningkatan yang signifikan dalam kecepatan pengeboran, pengurangan biaya pengaturan sifat-sifat cairan pengeboran, pengurangan tingkat komplikasi lubang sumur, dan pemenuhan persyaratan perlindungan lingkungan.
Sebagai bagian dari sistem sirkulasi, perangkat harus dipasang dalam urutan yang ketat. Dalam hal ini, pola aliran solusi harus sesuai dengan rantai teknologi berikut: sumur - pemisah gas - blok pembersihan kasar dari lumpur (saringan bergetar) - degasser - blok untuk pembersihan halus lumpur (pemisah pasir dan lumpur, pemisah) - blok untuk mengontrol konten dan komposisi fase padat (centrifuge, pemisah tanah liat hidrosiklon).
Tentu saja, dengan tidak adanya gas dalam cairan pengeboran, langkah-langkah degassing dikecualikan; saat menggunakan larutan tidak berbobot, sebagai aturan, pemisah tanah liat dan sentrifugal tidak digunakan; saat membersihkan cairan pengeboran berat, pemisah lumpur hidrosiklon (pemisah pasir dan lumpur) biasanya tidak disertakan. Dengan kata lain, setiap peralatan dirancang untuk melakukan fungsi yang cukup spesifik dan tidak universal untuk semua kondisi pengeboran geologis dan teknis. Oleh karena itu, pemilihan peralatan dan teknologi untuk membersihkan cairan pengeboran dari stek didasarkan pada kondisi spesifik sumur pengeboran. Dan untuk membuat pilihan yang tepat, Anda perlu mengetahui kemampuan teknologi dan fungsi dasar peralatan.
BHA dan kontrol rezim pengeboran untuk memerangi kelengkungan spontan sumur
Alasan teknis dan teknologi menyebabkan kelengkungan spontan sumur karena fakta bahwa mereka menyebabkan pembengkokan bagian bawah tali bor dan misalignment sumbu bit relatif terhadap pusat sumur. Untuk mengecualikan proses ini atau mengurangi kemungkinan terjadinya, perlu:
1. meningkatkan kekakuan bagian bawah tali bor;
2. mengecualikan celah antara pemusat dan dinding lubang bor;
3. mengurangi WOB;
4. dalam hal pengeboran dengan motor downhole putar tali bor secara berkala.
Untuk memenuhi dua kondisi pertama, perlu untuk memasang setidaknya dua pemusat berukuran penuh: di atas mata bor dan di badan kerah bor dekat mata bor (atau di RD). Pemasangan 2 - 3 pemusat ukuran penuh memungkinkan untuk meningkatkan kekakuan BHA dan mengurangi kemungkinan pembengkokan bahkan tanpa mengurangi WOB.
Dalam beberapa kasus, rakitan pilot digunakan ketika sumur dibor dengan cara bertahap: pilot - mata bor berdiameter kecil - ekstensi - mata bor - alat untuk membesarkan lubang - kerah bor - tali bor. Diinginkan untuk menggunakan kerah dengan diameter sebesar mungkin. Hal ini meningkatkan kekakuan BHA dan mengurangi celah antara pipa dan dinding lubang bor.
2. Pembiasaan dengan pengeboran pad
Sekelompok sumur adalah pengaturan seperti itu ketika mulut dekat satu sama lain pada platform teknologi yang sama, dan bagian bawah sumur berada di simpul jaringan pengembangan reservoir.
Saat ini, sebagian besar sumur produksi dibor secara berkelompok. Hal ini dijelaskan oleh fakta bahwa pengeboran cluster deposit dapat secara signifikan mengurangi ukuran area yang ditempati oleh pengeboran dan kemudian sumur produksi, jalan, saluran listrik, dan jaringan pipa.
Keuntungan ini sangat penting selama konstruksi dan pengoperasian sumur di tanah subur, di cadangan, di tundra, di mana lapisan permukaan bumi yang terganggu dipulihkan setelah beberapa dekade, di daerah rawa, yang memperumit dan sangat meningkatkan biaya pekerjaan konstruksi dan pemasangan fasilitas pengeboran dan operasional. Pengeboran pad juga diperlukan ketika diperlukan untuk membuka deposit minyak di bawah struktur industri dan sipil, di bawah dasar sungai dan danau, di bawah zona paparan dari pantai dan jalan layang. Tempat khusus ditempati oleh pembangunan cluster sumur di wilayah Tyumen, Tomsk dan wilayah lain di Siberia Barat, yang memungkinkan untuk berhasil melakukan pembangunan sumur minyak dan gas di pulau-pulau penimbunan di daerah terpencil, berawa dan berpenduduk. wilayah.
Lokasi sumur di well pad tergantung pada kondisi medan dan sarana komunikasi yang diusulkan antara well pad dan pangkalan. Semak-semak yang tidak terhubung dengan jalan permanen ke pangkalan dianggap lokal. Dalam beberapa kasus, semak-semak bisa menjadi dasar ketika mereka berada di jalan raya. Pada well pad lokal, sebagai aturan, mereka diatur dalam bentuk kipas ke segala arah, yang memungkinkan untuk memiliki jumlah sumur maksimum di well pad.
Peralatan pemboran dan alat bantu dipasang sedemikian rupa sehingga ketika alat pemboran dipindahkan dari satu sumur ke sumur lainnya, pompa pemboran, lubang penerima dan bagian dari peralatan untuk pembersihan, perawatan kimia dan persiapan cairan pembilas tetap tidak bergerak sampai selesainya pekerjaan. konstruksi semua (atau sebagian) sumur di well pad ini.
Jumlah sumur dalam satu cluster dapat bervariasi dari 2 hingga 20-30 atau lebih. Selain itu, daripada lebih banyak sumur di pad, semakin besar deviasi bagian bawah dari kepala sumur, panjang lubang sumur meningkat, panjang lubang sumur meningkat, yang mengarah pada peningkatan biaya pengeboran sumur. Selain itu, ada bahaya pertemuan batang. Oleh karena itu, menjadi perlu untuk menghitung jumlah sumur yang dibutuhkan dalam sebuah cluster.
Dalam praktek pemboran pad, kriteria utama untuk menentukan jumlah sumur dalam pad adalah total laju alir sumur dan faktor gas minyak. Indikator-indikator ini menentukan bahaya kebakaran sumur selama aliran terbuka dan tergantung pada tingkat teknis peralatan pemadam kebakaran.
Mengetahui perkiraan jumlah sumur di pad, mereka melanjutkan untuk membangun rencana pad. Rencana well pad adalah representasi skema dari proyeksi horizontal sumur dari semua sumur yang dibor dari well pad tertentu. Rencana bantalan mencakup tata letak kepala sumur, urutan pengeborannya, arah pergerakan mesin, azimuth desain dan offset lubang dasar. Tugas diselesaikan dengan membangun skema sarang.
3. Menjalankan dan menyemen senar casing
Setelah interval batuan yang diperlukan telah dibor, perlu untuk menurunkan tali selubung ke dalam sumur. Tali selubung digunakan untuk memperkuat dinding sumur, untuk mengisolasi lapisan penyerap dan akuifer.
Tali selubung terbuat dari pipa pada soket, sambungan ulir atau sambungan las tanpa lengan dan diturunkan ke bagian sumur demi bagian atau dalam satu langkah dari mulut ke bawah. Dalam satu langkah, tali diturunkan jika stabilitas dinding sumur cukup dan kapasitas angkat sistem perjalanan. Saat memperbaiki sumur dalam, ulir tanpa lengan atau sambungan las OKE.
Intermediate OK terdiri dari beberapa jenis:
1) padat - tumpang tindih seluruh lubang sumur dari bawah ke kepala sumur, terlepas dari dukungan interval sebelumnya;
2) liner - untuk memperbaiki hanya interval terbuka sumur dengan tumpang tindih bagian bawah OK sebelumnya dengan jumlah tertentu;
3) kolom rahasia - QAP khusus, yang hanya berfungsi untuk menutupi interval komplikasi dan tidak memiliki hubungan dengan kolom sebelumnya.
Pengerjaan penampang senar casing dan pengikatan sumur dengan liner muncul, pertama, sebagai solusi praktis untuk masalah menjalankan string casing berat dan, kedua, sebagai solusi untuk masalah penyederhanaan desain sumur, pengurangan diameter casing, serta sebagai celah antara senar dan dinding sumur, mengurangi konsumsi logam dan bahan sumbat.
Untuk penyemenan yang berhasil dan untuk penurunan yang lebih efisien, OK digunakan peralatan teknologi. Peralatan meliputi perangkat berikut: kepala penyemenan, sumbat penyemenan pemisah, katup periksa, sepatu kolom, nozel pemandu, pemusat, pengikis, turbulizer, nozel sepatu panjang 1,2-1,5 m dengan lubang dengan diameter 20-30 mm dalam bentuk spiral, annular pengemas hidrolik tipe PDM, lengan penyemenan bertahap, dll.
KEPALA SEMEN
Kepala penyemenan dirancang untuk membuat hubungan yang erat antara tali selubung dan jalur injeksi unit penyemenan. Ketinggian kepala penyemenan harus memungkinkan mereka untuk ditempatkan di tautan pengangkat dari sistem perjalanan dan, dengan peralatan yang sesuai, digunakan untuk penyemenan dengan reaming tali selubung.
MEMISAHKAN TEMBOK SEMEN
Squeezing plugs dirancang untuk memisahkan slurry semen dari cairan pemerasan ketika dipaksa masuk ke dalam anulus sumur.Ada modifikasi dari plugs, di mana benang untuk plug dibuat di bagian atas tubuh di bagian dalam. permukaan, yang tanpanya sumbat ini dapat digunakan sebagai sumbat bagian. Sumbat bawah dimasukkan ke dalam selubung kolom tepat sebelum bubur semen dipompa untuk mencegahnya bercampur dengan cairan pengeboran, dan sumbat atas setelah seluruh volume bubur semen telah dipompa. Saluran pusat di steker bawah diblokir oleh diafragma karet, yang pecah saat mendarat di "cincin penghenti" dan membuka saluran untuk mendorong mortar semen.
PERIKSA KATUP
Katup periksa TsKOD dirancang untuk mengisi sendiri string casing dengan cairan pengeboran secara terus-menerus saat diturunkan ke dalam sumur, serta untuk mencegah aliran balik bubur semen dari anulus dan menghentikan sumbat penyemenan pemisah. Katup jenis TsKOD diturunkan ke dalam sumur dengan tali selubung tanpa bola penutup, yang dipompa ke tali setelah diturunkan ke kedalaman yang telah ditentukan. Bola, melewati washer split dan diafragma, mengambil posisi kerja yang diameternya lebih kecil dari diameter bola, yang terakhir dijatuhkan ke dalam tali sebelum pipa bor dihubungkan ke bagian. Dalam hal ini, pengisian sendiri string dengan cairan dikecualikan, dan saat menurunkan string, perlu menambahkan cairan pengeboran ke dalamnya sesuai dengan persyaratan rencana kerja. Bagian atas katup memiliki permukaan ujung penopang internal yang berfungsi sebagai "cincin penghenti" untuk menghentikan sumbat semen yang memisahkan. Dalam hal ini, pemasangan cincin dorong tidak diperlukan.
SEPATU KOLOM
Sepatu kolom digunakan untuk melengkapi bagian bawah string casing yang terbuat dari pipa dengan diameter 114-508 mm dan dirancang untuk memandu string di sepanjang lubang sumur dan melindunginya dari kerusakan saat turun dalam proses casing sumur minyak dan gas di lubang bawah suhu hingga 250 °C.
SENTRATOR
Pemusat dirancang untuk memastikan penempatan string selubung yang konsentris di dalam sumur untuk mencapai isolasi formasi berkualitas tinggi selama penyemenan. Selain itu, mereka memfasilitasi berjalannya casing string dengan mengurangi gaya gesekan antara string dan dinding sumur, membantu meningkatkan tingkat perpindahan cairan pengeboran oleh lumpur semen karena beberapa turbulensi aliran di sumur. area pemasangannya, memudahkan pekerjaan menggantung senar tersembunyi dan memasang bagian karena memusatkan ujung atasnya di dalam sumur.
- PENGIKIS
Scraper digunakan untuk memecahkan kue tanah liat di dinding sumur untuk meningkatkan daya rekat bubur semen ke batu, terutama saat menyemen sumur dengan reaming.
Selama penurunan sumur, mungkin perlu menyiram sumur. Dalam hal ini, sub flush disekrup ke kelly dengan ulir pengunci di atas dan ulir trapesium di bagian bawah. Kemudian, ketika operasi yang diperlukan selesai, kepala penyemenan disekrup ke casing.
Setelah sumur dijalankan, cairan pemboran masih tertinggal di dalam sumur. Untuk mengeluarkannya dari laras, digunakan cairan penyangga. Itu dipompa melalui kepala penyemenan. Kemudian perkiraan jumlah semen dipompa ke dalam kolom. Setelah itu, cairan perpindahan disuplai ke ruang intrapipe agar semen naik ke ketinggian desain. Pada saat yang sama, sumbat dilepas dari penahan dan dibawa ke bawah oleh cairan perpindahan. Pendaratan sumbat pada cincin penghenti katup, menyebabkan lonjakan tekanan pada pompa, menandakan akhir dari proses penyemenan.
Durasi pengerasan mortar semen untuk konduktor diatur ke 16 jam, dan untuk string menengah dan produksi - 24 jam Durasi pengerasan berbagai campuran penyemenan (bentonit, terak, dll.) diatur tergantung pada data pendahuluannya pengujian, dengan mempertimbangkan suhu di dalam lubang sumur.
Proses penyemenan sumur dilakukan oleh kompleks peralatan khusus, yang ditempatkan sesuai dengan skema yang dikembangkan sebelumnya.
Unit penyemenan dirancang untuk menyuntikkan bubur semen dan cairan perpindahan ke dalam sumur, serta untuk memasok cairan penutup ke perangkat pencampur selama persiapan larutan. Selain itu, mereka digunakan untuk mencuci dan meremas sumbat pasir, pengujian tekanan pipa, kolom, manifold, pencampuran bubur hidrolik, dll.
Mesin pencampur semen dirancang untuk persiapan mortar semen untuk sumur penyemenan, berbagai campuran sumbat; mereka dapat digunakan untuk menyiapkan cairan pengeboran normal dan tertimbang dari bubuk tanah liat.
Sesuai dengan tujuan dan sifat pekerjaannya, mesin pencampur dipasang pada mobil atau trailer. Komponen utama mesin pencampur adalah hopper, mekanisme bongkar muat dan alat pencampur untuk menyiapkan larutan.
4. Pembukaan dan pengujian cakrawala minyak
Pengeboran sumur diakhiri dengan pembukaan reservoir minyak, yaitu komunikasi reservoir minyak dengan sumur. Tahap ini sangat bertanggung jawab karena beberapa alasan. Campuran minyak dan gas di reservoir berada di bawah tekanan besar, yang nilainya mungkin tidak diketahui sebelumnya. Pada tekanan yang melebihi tekanan kolom cairan yang mengisi sumur, cairan dapat dikeluarkan dari lubang sumur dan terjadi aliran terbuka. Masuknya cairan pembilas (dalam banyak kasus itu adalah larutan tanah liat) ke dalam reservoir minyak menyumbat salurannya, mengganggu aliran minyak ke dalam sumur.
Ledakan dapat dihindari dengan memasang pencegah di kepala sumur atau dengan menggunakan cairan pembilasan berdensitas tinggi. Mencegah penetrasi larutan ke dalam reservoir minyak dicapai dengan memasukkan berbagai komponen ke dalam larutan, yang memiliki sifat serupa dengan cairan reservoir, misalnya, emulsi berbasis minyak.
Karena setelah reservoir minyak dibuka, casing string diturunkan ke dalam sumur dan disemen, sehingga menutup reservoir minyak juga, maka reservoir perlu dibuka kembali. Ini dicapai dengan menembak melalui kolom dalam interval formasi dengan perforator. Mereka diturunkan ke dalam sumur dengan kabel-tali oleh layanan geofisika.
Saat ini, beberapa metode perforasi sumur telah dikuasai dan digunakan:
1) Perforasi peluru
Perforasi peluru sumur terdiri dari penurunan ke dalam sumur pada tali kabel perangkat khusus - perforator, di mana muatan bubuk dengan peluru dibangun. Menerima impuls listrik dari permukaan, muatan meledak, memberikan peluru kecepatan tinggi dan daya tembus yang besar. Ini menyebabkan penghancuran logam kolom dan cincin semen. Jumlah lubang di kolom dan lokasinya di sepanjang ketebalan formasi dihitung terlebih dahulu, oleh karena itu, terkadang karangan bunga perforator diturunkan.
2) Perforasi torpedo
Perforasi torpedo pada prinsipnya mirip dengan perforasi peluru, hanya saja bobot muatannya dinaikkan dan laras horizontal digunakan dalam perforator.
3) Perforasi kumulatif
Perforasi kumulatif - pembentukan lubang karena gerakan terarah dari pancaran muatan panas yang keluar dari perforator dengan kecepatan 6 ... 8 km / s di bawah tekanan 20 ... 30 GPa. Dalam hal ini, saluran dibentuk dengan kedalaman hingga 350 mm dan diameter 8 ... 14 mm. Ketebalan maksimum formasi, dibuka oleh perforator kumulatif untuk penurunan hingga 30 m, dengan torpedo - hingga 1 m, dengan peluru - hingga 2,5 m Jumlah muatan bubuk - hingga 50 g.
4) Perforasi hidro-sandblasting
Saat menggunakan perforasi hydro-sand-jet, lubang terbentuk di kolom karena aksi abrasif dari campuran pasir-cair yang mengalir dengan kecepatan hingga 300 m/s dari nozel yang dikalibrasi pada tekanan 15...30 MPa .
Pengembangan sumur minyak adalah suatu rangkaian pekerjaan yang dilakukan setelah pemboran, dengan tujuan untuk menimbulkan aliran minyak dari reservoir ke dalam sumur. Faktanya, dalam proses pembukaan, seperti yang disebutkan sebelumnya, dimungkinkan untuk masuknya cairan dan air pengeboran ke reservoir, yang menyumbat pori-pori reservoir dan mendorong minyak keluar dari sumur. Oleh karena itu, aliran minyak secara spontan ke dalam sumur tidak selalu memungkinkan. Dalam kasus seperti itu, mereka menggunakan panggilan masuk buatan, yang terdiri dari melakukan pekerjaan khusus.
Inflow dapat disebabkan oleh penggantian fluida yang densitasnya lebih tinggi di dalam lubang sumur dengan fluida yang densitasnya lebih rendah. Dalam hal ini, tekanan yang diberikan oleh kolom cairan pada formasi berkurang, dan dengan demikian menyebabkan masuknya minyak dari sumur. Metode ini sederhana dan ekonomis, tetapi efektif jika kontaminasi formasi rendah.
Jika penggantian larutan dengan air tidak membawa hasil, maka masuknya disebabkan menggunakan kompresor. Udara yang dikompresi oleh kompresor dimasukkan ke dalam laras. Pada saat yang sama, dimungkinkan untuk mendorong kolom cairan menjauh dari sepatu tabung, sehingga mengurangi tekanan balik pada formasi ke nilai yang signifikan. Dalam beberapa kasus, mungkin efektif untuk secara berkala memasok udara dengan kompresor dan cairan oleh unit pompa, menciptakan semburan udara berturut-turut. Jumlah bagian gas seperti itu bisa beberapa, dan mereka, mengembang, mengeluarkan cairan dari laras. Untuk meningkatkan efisiensi perpindahan sepanjang tali pipa, lubang katup start-up dipasang di mana udara terkompresi, ketika bergerak melalui ruang pipa, memasuki KZP dan mulai menaikkan cairan baik di anulus maupun di tabung .
Aliran masuk juga bisa disebabkan oleh metode swabbing. Metodenya terdiri dari menjalankan piston-swab khusus yang dilengkapi dengan katup periksa ke dalam pipa. Bergerak ke bawah, piston melewati cairan melalui dirinya sendiri, ketika naik, katup menutup, dan seluruh kolom cairan yang ada di atasnya dipaksa naik dengan piston, dan kemudian dikeluarkan dari sumur. Karena kolom cairan yang diangkat dapat berukuran besar (sampai 1000 m), penurunan tekanan pada formasi dapat menjadi signifikan. Proses swabbing dapat diulang berkali-kali, yang memungkinkan pengurangan tekanan yang signifikan.
Ketika tubing belum masuk ke dalam sumur, aliran masuk dapat disebabkan oleh metode ledakan. Jika bejana berisi udara bertekanan diturunkan ke dalam sumur, kemudian secara langsung menghubungkan bejana ini dengan lubang sumur, maka udara yang dilepaskan akan bergerak dari zona bertekanan tinggi ke zona bertekanan rendah, menarik cairan dan dengan demikian menciptakan penurunan tekanan pada sumur. pembentukan. Efek serupa dapat dicapai jika pemompaan dan kerja kompresor yang sebelumnya dikosongkan cairan diturunkan ke dalam sumur dan cairan sumur langsung dialirkan ke dalamnya. Dalam hal ini, tekanan balik pada formasi akan berkurang dan aliran fluida yang masuk dari formasi akan meningkat. Stimulasi masuk disertai dengan penghilangan kotoran mekanis yang dibawa ke sana dari reservoir, mis. pembersihan formasi.
5. Pekerjaan darurat di sumur
Untuk pekerjaan darurat, alat memancing digunakan. Desain alat pancing sangat beragam. Namun, menurut prinsip penangkapan, mereka dapat dibagi menjadi tiga kelompok utama:
a) Alat tangkap datar yang beroperasi dengan prinsip menjepit objek di luar atau di dalam penangkap;
b) Alat penangkap ikan bersenapan, bekerja berdasarkan prinsip memotong ulir pada objek dengan sekrup penangkap secara simultan di atasnya;
c.Alat lainnya.
Pertimbangkan beberapa jenis alat memancing.
Pipa luar dirancang untuk menangkap pipa, batang, atau benda lain di dalam sumur dengan badan atau selongsong. Ini adalah pegangan sisir split yang ditempatkan di tubuh dan dipasang di pipa. Benda yang akan ditangkap ditutup dengan alat tangkap, yang ketika masuk ke atas, memperbesar diameter lubang, melewati benda ke dalam penangkap. Ketika diregangkan, slip itu turun, dan giginya memotong tubuh objek, menjepitnya di penangkap.
Tombak bagian dalam dirancang untuk diturunkan ke pipa penangkap. Ini terdiri dari badan tempat pelat dipasang, dihubungkan dengan batang dan cincin bergerak. Tubuh dimasukkan ke dalam pipa penangkap, sementara mati naik, mengurangi diameter penangkap, dan menciptakan kondisi untuk masuk. Saat diregangkan, dadu turun, meningkatkan diameter tubuh penangkap dan membuat pipa macet.
Overshot operasional dimaksudkan untuk menangkap pipa atau batang dengan kopling dengan bantuan pegas datar yang dipasang pada permukaan bagian dalam bodi. Ketika mendekati suatu objek, pegas menyimpang, melewatinya di dalam penangkap, dan kemudian bertemu.
Katup untuk menangkap batang digunakan untuk menangkap batang dengan kopling. Ini terdiri dari tubuh di mana pegas drop-down mati diperbaiki. Dies terbuka, melewati objek, dan kemudian bertemu.
Pemotong frais dengan gigi bagian dalam digunakan untuk menggiling ujung atas pipa atau batang darurat agar dapat berfungsi sebagai penangkap pengaman. Ini terdiri dari tubuh di mana gigi memanjang dipotong.
Keran operasional dirancang untuk memancing dengan ulir internal pipa atau kopling. Ini terdiri dari tubuh, di mana ada utas di bagiannya yang terpotong. Itu bisa diiris pada item yang bisa ditangkap dan kemudian ditangkap.
Bel dimaksudkan untuk menangkap pipa untuk benang eksternal. Lonceng adalah pipa cabang, di permukaan bagian dalam di mana benang kunci dipotong. Panjang benang kurang lebih 35 cm.
6. Penghapusan minyak gas dan emisi
Ada dua metode:
metode tekanan reservoir seimbang
Ketika manifestasi dihilangkan dengan metode pertama, tekanan lubang dasar dipertahankan sedikit lebih tinggi dari tekanan formasi di seluruh proses. Dalam hal ini, aliran fluida akan berhenti sampai redaman lengkap.
Ada empat cara untuk menerapkan metode ini:
1) metode pembunuhan sumur terus menerus: proses pencucian dan pembunuhan
mulai melakukan segera pada solusi dengan kepadatan yang diperlukan untuk melakukan
kondisi - R zab > R reservoir. Dengan metode ini, yang terendah
tekanan, oleh karena itu, ini adalah yang paling aman. Namun, untuk implementasinya
perlu memiliki persediaan bahan penimbangan dan sediaan instan yang memadai
Lumpur pengeboran.
2) Metode menunggu pembobotan: setelah mendeteksi manifestasi ditutup
dengan baik dan lanjutkan untuk menyiapkan solusi dengan kepadatan yang dibutuhkan dan
volume yang dibutuhkan. Jaga agar tekanan tetap konstan saat menyiapkan larutan.
pipa bor, yang memastikan tekanan reservoir konstan selama pendakian
paket cairan. Kerugian dari metode ini adalah kebutuhan untuk benar
kontrol tekanan paket cairan mengambang, yaitu, sehingga tekanan tidak
melebihi peralatan yang diizinkan, dan juga memungkinkan untuk menempelkan pengeboran
alat, karena sumur tetap tanpa sirkulasi. Keuntungan dari metode ini
dari yang sebelumnya adalah kita bisa menyiapkan solusi yang sama
kepadatan, serta dengan metode ini, maksimum terkecil
tekanan, karena ketika gas belum mendekati mulut dan larutan berat dimulai
isi KZP, kami semakin membuka choke, oleh karena itu,
gas pack membentang lebih dan kehilangan tekanan saat mendekati mulut.
3) Metode pembunuhan sumur dua tahap. Pada tahap pertama, itu adalah
dengan mencuci cairan dari sumur pada larutan yang sama di mana manifestasi diperoleh.
Pada saat yang sama, mereka mulai menyiapkan solusi dengan kepadatan yang diperlukan untuk
baik membunuh. Pada tahap kedua pembunuhan, injeksi ke dalam sumur dilakukan
solusi tertimbang. Metode ini lebih sederhana dari dua sebelumnya, relatif
aman, tetapi selama implementasinya, tekanan tertinggi tercipta di
dengan baik.
4) Metode perpanjangan dua tahap. Pada tahap pertama dengan tekanan balik
pencucian cairan sumur yang masuk dilakukan pada solusi yang sama, di mana manifestasi diperoleh. Setelah cairan formasi dicuci, tanpa menghentikan sirkulasi, densitas larutan yang bersirkulasi ditingkatkan hingga densitas yang diperlukan, dan dengan demikian formasi yang berkembang dimatikan. Metode ini digunakan tanpa adanya wadah yang diperlukan untuk persiapan larutan.
metode pembunuhan sumur langkah-demi-langkah:
Penggunaan metode ini digunakan ketika, ketika menggunakan metode sebelumnya, tekanan muncul melebihi tekanan yang diizinkan di kepala sumur.
Bibliografi
1. Korshak A.A. Shammazov A.M./Dasar-dasar bisnis minyak dan gas
2. Peralatan ladang minyak. Direktori.
3. Ilsky A.L. Shmidt A.P./Mesin dan mekanisme pengeboran
4. Popov A.N. Spivak A.I./Teknologi pengeboran sumur minyak dan gas
harga air sumur per meter