Dibawah modus pengeboran mengacu pada kombinasi parameter tertentu yang mempengaruhi kinerja pengeboran. Opsi ini meliputi:
2) frekuensi rotasi bit;
3) laju aliran massa cairan pembilasan yang dipompa;
4) kualitas cairan pembilasan (densitas, viskositas, kehilangan air, tegangan geser statis).
Kombinasi parameter ini, yang memungkinkan untuk memperoleh indikator kualitatif dan kuantitatif tertinggi dari pengeboran dengan peralatan teknis tertentu dari rig pengeboran, disebut mode pengeboran yang rasional (atau optimal).
Dalam praktiknya, selama proses pengeboran, seringkali perlu untuk mengambil inti, mengebor sumur dalam kondisi geologis yang tidak menguntungkan (zona yang rentan terhadap kehilangan sirkulasi, komplikasi yang terkait dengan pelanggaran integritas lubang sumur, dll.), mengebor jauh dari lubang sumur yang dibor sebelumnya, dll. Mode pengeboran yang digunakan dalam kasus seperti ini disebut mode khusus.
Efisiensi bit dievaluasi oleh dua parameter:
1) kecepatan pengeboran mekanis v m e x m/h;
2) mengemudi di bit h,m.
Saat memilih mode pengeboran, harus diperhitungkan bahwa dengan perubahan salah satu parameter, ROP dan penetrasi per bit tidak selalu meningkat. Untuk setiap formasi, terdapat kombinasi WOB, RPM, dan aliran fluida pemboran yang optimal.
Pada cara turbin pengeboran perubahan dalam satu parameter mode pengeboran menyebabkan perubahan otomatis pada yang lain. Dalam kasus peningkatan laju aliran fluida pengeboran pada beban konstan pada bit, kecepatan rotasi n poros turbodrill (bit) tumbuh dalam proporsi langsung. Jika beban pada mata bor dinaikkan, dan laju aliran fluida pemboran tetap konstan, maka kecepatan putar poros turbodrill (mata bor) akan berkurang.
Dalam praktik pengeboran sumur, laju aliran fluida pembilasan diatur dengan mempertimbangkan penyediaan kondisi operasi yang paling menguntungkan untuk turbodrill dan penghilangan cutting terbesar. Dengan pendalaman sumur karena penurunan diameternya, laju aliran fluida pembilasan berkurang dari interval ke interval.
Saat mengebor dalam interval di mana aliran fluida konstan diatur, dari tiga parameter mode pengeboran, hanya WOB yang dapat diubah, sehingga menyesuaikan frekuensi rotasinya. Yang terakhir, pada laju aliran konstan dari cairan pengeboran, mencapai maksimumnya ketika beban pada mata bor dihilangkan.
Saat membuat beban pada bit, kecepatan rotasi poros turbodrill (bit) berkurang, dan torsi meningkat. Pengoperasian turbodrill yang efisien akan dipastikan pada beban seperti itu pada bit, ketika daya pada poros turbodrill N mencapai nilai maksimumnya. Selama periode ini, kecepatan rotasi poros turbodrill adalah sekitar setengah kecepatan rotasi bit tanpa adanya beban di atasnya, dan torsi sekitar setengah torsi yang dikembangkan selama pengereman poros turbodrill. Pada daya maksimum pada poros turbodrill, turbin juga memiliki efisiensi maksimum.
Beban pada bit tergantung pada kekerasan permeabilitas batuan. Saat mengebor di batuan keras, untuk meningkatkan efisiensi bit, mereka menambah beban, dan saat mengebor di batuan lunak, mereka menguranginya. Pada saat yang sama, kecepatan bit dalam kasus pertama berkurang, dan yang kedua meningkat, yang diperlukan untuk mencapai kinerja yang baik.
Saat mengoperasikan turbodrill sesuai dengan kondisi yang dijelaskan, kinerja bit terbaik dipastikan, karena menambah dan mengurangi kecepatan bit mengarah ke mode operasi turbodrill yang tidak stabil.
Untuk pengeboran putar tidak ada hubungan yang jelas antara parameter mode pengeboran dan, akibatnya, pengaruhnya satu sama lain, seperti dalam kasus metode turbin. Oleh karena itu, Anda dapat mengatur kombinasi parameter mode pengeboran, mengontrolnya.
Laju aliran cairan pembilasan diatur dengan mempertimbangkan pembersihan lubang bawah berkualitas tinggi. Berat bit dan frekuensi rotasinya diatur untuk setiap horizon geologi, dengan mempertimbangkan kekerasan batuan yang ditembus.
Babak tali bor- gerakan vertikal di permukaan, yang dilakukan dengan menurunkan pipa terkemuka ke rotor dengan jumlah tertentu sebagai akibat dari pelepasan rem winch.
Tekanan mata bor pada lubang bawah sebagian disebabkan oleh berat senar bor, namun peningkatannya yang berlebihan dapat menyebabkan putusnya senar bor dan deformitas sumur. Untuk menghindari hal ini, bagian bawah tali bor diberi pemberat.
Saat bekerja dengan bagian bawah yang tertimbang, hanya 75% dari beratnya yang digunakan.
Untuk mengontrol tekanan seragam pada bit, alat yang disebut indikator berat digunakan. Tekanan fluida pemboran diukur dengan sensor yang dipasang pada pipa antara pompa atau pada riser saluran pembuangan pompa lumpur. Kecepatan rotor diukur dengan takometer dari berbagai desain. Selain itu, perangkat digunakan untuk menentukan kecepatan mekanis pengeboran, serta perangkat lain yang merekam dan menampilkan parameter pengeboran di bagian bawah (kecepatan poros turbodrill, posisi spasial bagian bawah sumur, dll.).
Baru-baru ini, transmisi parameter mode pengeboran jarak jauh telah semakin diperkenalkan. Ini memungkinkan untuk melengkapi ruang kontrol (bagian) dengan konsol khusus, di mana mereka memasang instrumen penunjuk dan perekaman parameter mode pengeboran setiap rig pengeboran. Dispatcher (site engineer) mendapat kesempatan untuk memantau pekerjaan rig pengeboran sepanjang waktu dan, jika perlu, segera melakukan penyesuaian yang diperlukan untuk proses pengeboran sumur.
Mode teknologi pengeboran adalah kombinasi dari sejumlah parameter set dasar yang mencirikan indikator kecepatan dan kualitas pengeboran yang terkait dengan penghancuran batuan di dasar sumur dan pemindahan stek bor ke permukaan.
Parameter utama dari mode pengeboran adalah:
Beban aksial pada alat pemotong batu;
Kecepatan rotasi alat pengeboran;
kuantitas dan kualitas cairan pembilasan;
Jenis alat pemotong batu.
Beban aksial pada alat pemotong batu mencirikan parameter mode pengeboran, yang menentukan gaya yang diterapkan di sepanjang sumbu tali bor ke alat pemotong batu.
WOB selama pengeboran dibuat oleh berat kerah bor dan tali bor.
Cara penghancuran volumetrik batuan dimungkinkan jika tekanan spesifik pada lubang dasar melebihi ketahanan batuan terhadap lekukan. Dengan demikian, beban aksial sebanding dengan kekuatan batuan. Oleh karena itu, hal-hal lain dianggap sama, beban terendah pada lubang dasar diperbolehkan saat mengebor batuan lunak, dengan peningkatan kekerasan batuan, beban aksial harus meningkat.
Dengan peningkatan beban aksial pada bit, kecepatan pengeboran mekanis meningkat ke nilai kritis tertentu. Pada awalnya, kecepatan meningkat secara intensif, dan kemudian pertumbuhannya secara bertahap melambat dan tiba saatnya pertumbuhan berhenti, dan kecepatan mulai berkurang. Dalam hal ini, pembersihan lubang bawah sangat penting.
Meningkatkan beban aksial meningkatkan penetrasi pada bit dan kecepatan mekanis, asalkan laju sirkulasi cairan pengeboran meningkat, yang diperlukan untuk pembersihan lengkap lubang bawah dari stek.
Saat mengebor untuk setiap kondisi tertentu, ada nilai kritis dari beban aksial pada bit, yang tidak dapat memberikan peningkatan lebih lanjut dalam kecepatan pengeboran. Nilai beban kritis tergantung pada sifat fisik dan mekanik batuan yang dibor, serta jenis mata bor.
Beban aksial optimal pada bit dipilih dengan mempertimbangkan hasil pengerjaan bit dengan beban aksial yang berbeda, tergantung pada kekerasan batuan, jenis dan ukuran bit, alat pengeboran dan metode pengeboran.
Peningkatan kecepatan mekanis dengan peningkatan beban aksial yang dibuat di lubang dasar oleh berat pipa bor tidak dapat diberikan tanpa menggunakan kerah bor. Dalam hal ini, pipa bor dibengkokkan karena beban berlebih, gelombang lentur berbatasan dengan dinding lubang bor, yang menyerap sebagian besar beban aksial dan tidak memberikan peningkatan kecepatan mekanis.
Untuk mendapatkan ROP dan penetrasi per bit yang lebih tinggi, dipraktikkan untuk menciptakan beban aksial tertinggi pada awal pengeboran mekanis. Proses pengeboran harus dilakukan sedemikian rupa sehingga selama pengoperasian mata bor, tekanan spesifik dipertahankan konstan, dan beban total berubah dalam batas yang disyaratkan. Alat bor harus diberi makan secara merata dan terus menerus dengan beban aksial yang diperlukan pada indikator berat.
Kecepatan rotasi bit
Saat memilih parameter mode pengeboran, diperhitungkan bahwa laju penetrasi meningkat sebanding dengan peningkatan kecepatan rotasi bit dengan peningkatan beban aksial secara simultan.
Dengan peningkatan kecepatan rotasi, keausan bit meningkat. Setelah RPM tertentu tercapai, keausan bit meningkat lebih cepat daripada peningkatan ROP. Pengaruh kecepatan putaran bit pada efisiensi penghancuran batuan tergantung pada beban aksial, derajat pembersihan lubang dasar, sifat fisik dan mekanik batuan dan kedalaman sumur.
Pengalaman pemboran pada batuan keras menunjukkan bahwa untuk meningkatkan laju penetrasi, perlu digunakan jumlah putaran yang lebih rendah sekaligus meningkatkan beban aksial pada alat pemotong batuan.
Disarankan untuk mengurangi kecepatan rotasi bit dengan peningkatan diameter bit, dengan peningkatan kekerasan dan abrasivitas batuan, dengan penurunan diameter pipa bor, serta saat mengebor formasi bergantian dengan ketebalan kecil dan ketika bergerak dari formasi dengan kekerasan yang lebih rendah ke formasi dengan kekerasan yang lebih besar. Untuk menghitung kecepatan putaran yang diizinkan untuk setiap ukuran pipa bor, gunakan rumus:
n - kecepatan rotasi yang diizinkan dalam rpm;
l - panjang pipa bor berputar dalam m;
E - modulus elastisitas;
g adalah percepatan gravitasi, sama dengan 9,8 m/s2;
q - berat 1 m pipa bor dalam kg.
Saat memilih kecepatan putaran bit, interval kedalaman pengeboran diperhitungkan. Dengan peningkatan kedalaman sumur, kecepatan rotasi bit dalam metode putar berkurang.
Pembilasan yang baik
Proses pembersihan dasar sumur dari stek dan pendinginan alat pemotong batu dengan cairan pemboran disebut dengan pembilasan sumur.
Praktek pengeboran dan studi khusus telah menetapkan pengaruh parameter cairan pengeboran pada indikator kualitas pengeboran.
Parameter utama pembilasan sumur yang mempengaruhi indikator kualitas pengeboran adalah: berat jenis, viskositas fluida pembilasan, serta jumlah fluida pembilasan yang dipasok ke lubang dasar dan laju aliran ke atas di anulus.
Peningkatan berat jenis cairan pengeboran menyebabkan penurunan kecepatan mekanik, dan, sebaliknya, ceteris paribus, tingkat penetrasi meningkat saat menggunakan cairan pembilasan dengan berat jenis lebih rendah.
Pembilasan cairan dengan viskositas lebih rendah lebih baik membersihkan lubang bawah dari partikel batuan yang dibor dan, tergantung pada peningkatan kecepatan gerakan di anulus, memastikan pengangkatannya secara intensif ke permukaan.
Dengan peningkatan jumlah cairan pembilasan yang dipasok ke lubang dasar, laju sirkulasi di anulus meningkat, dan dengan perubahan yang sesuai dalam parameter mode pengeboran, laju penetrasi meningkat. Pada saat yang sama, sifat fisik dan mekanik batuan, jenis dan ukuran mata bor, dan parameter kualitas cairan pengeboran memiliki dampak yang signifikan.
Dengan peningkatan kecepatan aliran ke atas cairan pembilasan di anulus, intensitas pembersihan bagian bawah sumur dari stek meningkat, pekerjaan bit di bagian bawah difasilitasi dan efisiensi pengeboran meningkat.
Selain membersihkan lubang bawah dari partikel yang dibor, cairan pengeboran berperan dalam penghancuran batuan melalui efek jet, yang merupakan dasar teknis untuk bit pembilasan jet.
Dengan peningkatan beban aksial, kecepatan rotasi dan diameter bit untuk pembersihan lubang dasar, maka perlu untuk meningkatkan jumlah cairan pemboran yang dipasok ke sumur. Dengan demikian, konsumsi fluida pemboran secara langsung tergantung pada volume batuan yang dibor per satuan waktu. Dengan intensitas pembilasan yang tidak mencukupi, pembersihan lubang dasar dari stek memburuk dan kecepatan mekanis pengeboran berkurang.
indikator kondisi normal pembilasan lubang bawah adalah kecepatan gerakan pancaran naik di ruang annular antara dinding lubang bor dan permukaan pipa bor, memiliki nilai dari 0,8 hingga 1,5 m/detik.
Bergantung pada laju sirkulasi cairan pembilasan di dalam sumur, kapasitas pompa yang diperlukan ditentukan oleh rumus:
Q - kapasitas pompa dalam m3/s;
V adalah laju aliran cairan pembilasan dalam m/s;
F - luas bagian annular sumur dalam m2.
Luas bagian annular sumur dihitung dengan rumus:
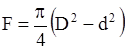
D - diameter sumur aktual dalam m;
d - diameter luar pipa bor dalam m.
Saat memilih parameter mode pengeboran, perlu untuk sepenuhnya menggunakan daya hidraulik yang dipasang dari rig pengeboran, untuk mengebor jumlah maksimum cairan pengeboran yang diizinkan sesuai dengan kondisi geologis dan teknis. Dalam hal ini, tekanan kerja yang diijinkan dari pompa lumpur dan peningkatan tahanan hidrolik dengan meningkatnya kedalaman sumur harus diperhitungkan.
Jenis alat pemotong batu
Alat yang dirancang untuk penghancuran batuan secara mekanis selama pengeboran adalah mata bor.
Tergantung pada sifat fisik dan mekanik dari batuan yang dibor, berbagai jenis dan desain bit digunakan. Bit untuk pengeboran putar berbeda dalam tujuan dan prinsip aksinya di atas batu.
Menurut tujuannya, mata bor dibagi menjadi tiga kelompok:
Mata bor terus menerus yang menghancurkan batu saat mengebor di sumur dengan lubang dasar terus menerus, di seluruh areanya;
Mata bor inti yang menghancurkan batu di dalam sumur dengan lubang bawah berbentuk lingkaran, meninggalkan kolom (inti) yang tidak dibor dari batu yang bisa dilewati di tengahnya;
Mata bor tujuan khusus yang digunakan untuk berbagai jenis pekerjaan di dalam sumur, tidak terkait langsung dengan proses pengeboran sumur (perluasan lubang bor, pengeboran batu semen, dll.).
Menurut prinsip dampak pada batu, mata bor dibagi menjadi dua kelompok: mata bor jenis pemotongan, yang menghancurkan batu terutama dengan memotong, mata bor jenis ini termasuk pemotong frais, berlian; bit jenis geser dan penghancuran, yang menghancurkan batu sebagai akibat dari dampak geser dan penghancuran, ini termasuk semua jenis bit kerucut.
Bit kerucut. Bit kerucut adalah bit yang menghancurkan batu dengan kerucut yang berguling-guling di permukaan. Kerucut adalah bagian pemotong batu dari bit kerucut yang berbentuk silinder atau kerucut. Permukaan sisi kerucut memiliki gigi atau sisipan paduan keras (pin) yang menghancurkan batu ketika bit berputar.
Bit rol dirancang untuk pengeboran putar sumur dengan pembilasan lubang bawah dengan cairan atau hembusan udara. Bit ini digunakan untuk mengebor batuan dengan sifat fisik dan mekanik yang berbeda. Tergantung pada batuan yang akan dibor, delapan jenis mata bor kerucut berikut untuk pengeboran dengan dasar padat diproduksi:
M - untuk yang paling lembut dan paling kental;
MS - untuk batuan lunak dengan lapisan batuan dengan kekerasan sedang;
C - untuk batuan dengan kekerasan sedang;
ST - untuk batuan dengan kekerasan sedang dengan interlayers dari batuan keras dan abrasif;
T - untuk batuan keras dan abrasif;
TK - untuk batuan keras dengan interlayer batuan keras dan abrasif;
K - untuk batuan yang kuat, rapuh dan abrasif;
OK - untuk batuan yang paling keras dan paling abrasif.
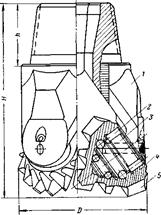
Gambar 2.6 - Pahat tricone
Tergantung pada jumlah bit kerucut, bit satu kerucut, dua, tiga, empat dan lima kerucut diproduksi.
Bit tricone (Gbr. 2.6), yang memiliki pemotong berbentuk kerucut dan sangat efisien, paling umum digunakan saat mengebor sumur produksi. Oleh rancangan tricone bit dibagi menjadi uncased (sectional) dan casing.
Pahat badan terbuka terdiri dari tiga bagian yang dilas menjadi satu. Setiap bagian terdiri dari cakar 1 dengan trunnion 3, di mana kerucut 4 dengan gigi 5 dipasang, berputar bebas pada bantalan gelinding 2. Bit telanjang memiliki ulir pengunci penghubung, yang dipotong setelah pengelasan cakar. Bit tanpa cangkang tersedia dalam diameter dari 76 hingga 346 mm.
pahat kasus diameter besar memiliki bodi cor baja dengan pelat pembilasan, di alur yang cakarnya dilengkapi dengan pemotong dilas. Kerucut, tergantung pada jumlah permukaan kerucut, dibagi menjadi satu, dua, dan tiga kerucut. Pemotong dua dan tiga kerucut dapat membersihkan sendiri.
Dalam bit jenis yang dapat membersihkan sendiri, tepi bergigi dari satu pemotong masuk ke alur di antara tepi pemotong lain, yang memastikan pembersihan sendiri dari stek. Dalam bit ini, salah satu pemotong memiliki kerucut penuh, yang bagian atasnya melampaui garis tengah bit, dan dua lainnya memiliki kerucut terpotong.
Bit tricone, digunakan tergantung pada sifat fisik dan mekanik batuan yang dibor, berbeda satu sama lain tidak hanya dalam diameter, tetapi juga dalam bentuk pemotong, pitch dan bentuk gigi, sudut kemiringan sumbu pemotong ke sumbu bit, perangkat pembilasan dan ukuran ulir penghubung.
Bantalan kerucut adalah salah satu komponen utama bit. Untuk mendapatkan kekuatan dan ketahanan aus, penyangga dibuat dengan presisi dan kekuatan tinggi dari baja paduan tinggi dengan perlakuan termokimia. Struktur bantalan kerucut tergantung pada jenis dan ukuran bit dan dibuat dalam berbagai versi menggunakan bantalan gelinding (bola, rol silinder) atau bantalan gelinding dan bantalan geser.
Perangkat pembilasan bit memiliki efek penting pada pembersihan bagian bawah sumur dan gigi pemotong dari batu yang dibor, pada tingkat pendinginan penyangga dan pemotong.
Tergantung pada jenis dan ukuran pahat tricone, perangkat pembilasan berbeda satu sama lain. Dalam beberapa jenis bit - pembilasan sentral dengan satu saluran mengarahkan aliran cairan pembilasan sepanjang sumbu bit ke pusat lubang bawah; di yang lain - dengan tiga saluran yang terletak di cakar dan mengarahkan aliran cairan pembilasan ke dasar sumur di antara pemotong; di yang ketiga - dengan tiga saluran yang terletak di cakar atau piring cuci dan mengarahkan aliran cairan pencuci - ke kerucut. Ada sekelompok bit dengan pembilasan gabungan, di mana aliran cairan pembilasan diarahkan antara pemotong dan ke pemotong.
Bit dengan ukuran berbeda tersedia dengan fitting plug-in dan tanpa fitting plug-in.
Bit, di mana semburan cairan pembilasan disuplai ke dasar sumur dan diarahkan melalui alat kelengkapan khusus (nozel), laju aliran fluida yang meningkat secara signifikan, disebut jet. Nozel untuk pahat jet terbuat dari mineral-keramik dan logam-keramik. Elemen penyegelan digunakan untuk menutup celah antara nozel dan saluran pembilasan.
Saat membuat mata bor tanpa alat kelengkapan, lubang dibuat di badan mata bor. Dalam hal ini, saluran pembilasan dibentuk sesuai dengan bentuk permukaan bagian dalam cakar dengan bagian: bulat, segitiga dan seperti celah.
Pin bit dimaksudkan untuk pengeboran pada formasi keras dan abrasif dengan ketahanan kompresi tinggi, di mana penetrasi bit dengan struktur pemotongan pemotong konvensional dapat diabaikan. Persenjataan pemotong bit ini dibuat dalam bentuk gigi plug-in - pin, memiliki permukaan kerja dalam bentuk belahan bumi.
Pahat dari jenis pemotongan. Pahat yang menghancurkan batuan dengan cara dipotong dan dikikis disebut pahat potong. Untuk mengebor batuan lunak, sedang dan keras yang berselang-seling, mata bor jenis pemotongan telah tersebar luas dalam beberapa tahun terakhir. Pahat dari jenis pemotongan abrasif terdiri dari benda padat, enam bilah dilas padanya, di mana tiga bagian bawah memiliki ketinggian normal, dan tiga bagian atas memiliki yang lebih pendek. Setiap bilah pendek dilas di antara dua bilah dengan ketinggian normal. Tepi tajam bilah dibuat miring dan diperkuat dengan pin silinder yang terbuat dari paduan logam-keramik. Celah antara pin dan tepi depan semua bilah diperkuat dengan paduan keras granular. Di bagian bawah tubuh, tergantung pada ukuran bit, ada dua hingga enam saluran pembilasan, yang arahnya menyediakan pembilasan wajah dengan semburan cairan pembilasan. Bit tipe jet memiliki tiga saluran pembilasan di mana nozel mineral-keramik dimasukkan. Nozel dipasang di badan bit dengan cincin pegas dan disegel dengan cincin karet.
Pahat berlian. Bit berlian adalah bit pemotongan yang diperkuat dengan berlian. Bit berlian dirancang untuk pengeboran sumur putar dan turbin di bebatuan dengan berbagai kekerasan, di mana efisiensi penggunaan bit tricone berkurang. Praktek pengeboran menegaskan bahwa dengan meningkatnya kedalaman sumur, efisiensi penggunaan bit tricone berkurang, dan konsumsinya meningkat. Bit berlian banyak digunakan saat mengebor interval sumur dalam yang lebih rendah. Penggunaan bit berlian memungkinkan untuk meningkatkan penetrasi per bit, mengurangi operasi tersandung, dan mendapatkan kecepatan pengeboran yang tinggi. Pahat berlian bekerja berdasarkan prinsip pemotongan mikro dan abrasi. Intensitas proses penghancuran batuan saat pengeboran dengan bit intan tergantung pada kecepatan linier kontak antara intan dan batuan, tekanan aksial dan jumlah cairan pembilasan yang diberikan.
Bit berlian terdiri dari kepala bantalan berlian paduan keras berbentuk - matriks dan badan baja dengan ulir penghubung.
Kinerja dan stabilitas mata bor berlian terutama tergantung pada sifat dan ukuran intan yang digunakan, susunan butir intan pada bagian kerja mata bor, dan kualitas mata bor itu sendiri.
Bit berlian spiral dirancang untuk pengeboran turbin. Bagian ujung bit terdiri dari tiga permukaan bulat yang dilengkapi dengan berlian. Tiga lubang flush mengarah ke saluran spiral bola yang berjalan dari bagian tengah kepala ke pinggiran bit.
Bit berlian radial digunakan dalam pengeboran putar dan turbin. Bagian kerja bit dibuat dalam bentuk enam tepian sektor yang dilengkapi dengan berlian, tiga sektor kecil mencapai lubang flush, dan tiga yang besar terhubung di bagian kerucut pusat bit. Di antara tiga tepian sektor besar ada tiga lubang untuk cairan pembilasan, melewati bagian periferal ke enam saluran pembilasan untuk mengalirkan cairan pembilasan.
Bit berlian radial dirancang untuk mengebor batuan abrasif rendah dengan kekerasan sedang.
Pahat berlian dengan pemotong PDC. Bit ini dirancang untuk mengebor minyak vertikal, terarah, horizontal dan sumur gas dalam batuan abrasif rendah dengan pencucian dengan air atau larutan tanah liat. Bit yang diperkuat dengan gigi PDC memiliki ketahanan dan kinerja aus yang tinggi, dan juga memberikan peningkatan berganda dalam penetrasi per slotting, sekaligus meningkatkan kecepatan pengeboran mekanis. Tidak adanya bagian yang bergerak dan berputar memperpanjang umur mata bor berlian dibandingkan dengan mata bor kerucut.
bit bisentris. Bit bicentric dirancang untuk pengeboran dengan reaming simultan dari lubang sumur di batuan lunak dan menengah tingkat rendah. Mereka digunakan untuk memperluas sidetracks dari sumur yang dibor sebelumnya, serta untuk memperluas dalam interval produktif untuk meningkatkan laju aliran sumur.
Bit bisentris telah memberikan kemampuan untuk mengebor lubang berdiameter lebih besar daripada yang biasanya dimungkinkan dengan diameter tertentu yang dijalankan sebelumnya tali casing. Keuntungan utama bit bisentris: kemungkinan perluasan sumur; operasi penyemenan casing yang lebih baik; biaya pengeboran yang lebih rendah. Penggunaan bit bicentric saat pengeboran sumur vertikal, directional atau horizontal adalah tingkat baru dalam pengembangan kemajuan teknis.
Mata bor. Mata bor adalah alat pemotong batu yang dirancang untuk menghancurkan batu selama pengeboran dengan coring. Mata bor yang diperkuat dengan pemotong paduan keras disebut karbida, dan mata bor yang diperkuat dengan berlian disebut mata bor berlian.
Mata bor terdiri dari cincin mahkota, dari ujungnya pemotong paduan keras dicetak dengan penyolderan berikutnya dengan kuningan. Cincin mahkota dibuat dari tabung, pipa bor atau tabung kosong dengan ukuran yang sesuai.
Pemotong karbida yang dipasang di cincin mahkota harus menutupi seluruh area pantat dan menonjol di luar permukaan sisi luar dan dalam dan di atas pantat mahkota. Pemotong yang menonjol di luar permukaan luar mata bor membentuk celah antara mata bor dan dinding lubang bor selama pengeboran. Gigi seri menonjol dari Permukaan dalam mahkota, saat memperdalam, membentuk celah antara inti dan permukaan bagian dalam laras inti. Pemotong karbida yang menonjol di atas ujung bawah bit menghancurkan batu di dasar annular sumur secara langsung selama pengeboran.
Tergantung pada kekerasan batu yang akan dibor, mata bor tersedia untuk mengebor batuan lunak, batuan keras sedang, dan batuan keras.
Faktor penting yang menentukan desain mata bor untuk mengebor batuan dengan berbagai kekerasan adalah: ukuran pemotong melampaui permukaan luar dan dalam tubuh dan di atas permukaan ujung cincin mahkota, sudut penajaman pemotong , bentuk dan lokasi pemotong.
Untuk pengeboran di batuan keras, nilai gigi seri yang masuk dan keluar dari mahkota adalah 0,5-1,0 mm, dan di atas ujungnya 1,5-2,5 mm.
Lokasi gigi seri relatif terhadap permukaan ujung cincin mahkota dapat berada pada tingkat yang sama atau melangkah. Pada mahkota berundak, gigi seri terletak baik di permukaan ujung maupun di permukaan samping pada jarak 20-30 mm dari ujung. Hal ini dilakukan untuk menghindari pelebaran interval lubang sumur setelah coring saat melakukan bit.
Penggilingan bit. Mata bor dirancang untuk melakukan pekerjaan bantu dalam proses pengeboran dan selama pekerjaan darurat di dalam sumur.
Tergantung pada tujuannya, bit penggilingan memiliki berbagai bentuk permukaan kerja dan secara struktural dilakukan sebagai annular, wajah, berbentuk. Mereka digunakan untuk pengeboran katup periksa, untuk abrasi benda logam yang terletak di dasar sumur, untuk menggiling ujung alat bor yang patah selama pekerjaan darurat, untuk menggiling bagian yang rusak dari senar casing dan pekerjaan lainnya.
Jenis penggilingan pahat FR banyak digunakan. Ini terdiri dari tubuh yang memiliki ulir pengunci penghubung di bagian atas. Tubuh ramping di bagian bawahnya memiliki tiga tonjolan, diperkuat dari permukaan ujung dan samping dengan pemotong karbida. Di bagian bawah rumahan, saluran pembilasan pusat terhubung ke saluran tambahan, di mana cairan pembilasan disuplai ke berbagai bagian bagian ujung router.
Parameter utama dari mode pengeboran diringkas dalam Tabel 2.4.
Tabel 2.4 - Parameter utama mode pengeboran
Interval, m |
Kecepatan putaran, rpm |
Konsumsi cairan pengeboran, l/s |
Jenis bit |
||
laras percontohan |
|||||
III 444,5 M-HLV R146 |
|||||
III 295.3 S-GV |
|||||
Interval, m |
Kecepatan putaran, rpm |
Konsumsi cairan pengeboran, l/s |
Jenis bit |
||
III 295.3 M-CGV R187 |
|||||
III 295.3 S-GV |
|||||
III 295.3 S-GV |
|||||
III 295.3 S-GV |
|||||
III 215.9 C-HLG |
|||||
III 215.9 C-HLG |
|||||
poros horisontal |
|||||
Mode pengeboran Ke Kategori: Alat pengeboran Mode pengeboran Data umum tentang mode pengeboran Cara pemboran ditentukan oleh kapasitas pemboran batuan (kecepatan pemboran mekanis) dan penetrasi per bit. Modus pengeboran dinyatakan oleh lima besaran utama: Tekanan bit lubang dasar dihasilkan oleh bagian dari berat string bor, namun, peningkatan beban yang berlebihan dapat menyebabkan kerusakan pahat dan kelengkungan lubang bor. Untuk menghindari kelengkungan sumur dan kecelakaan, bagian bawah tertimbang dipasang di bagian bawah tali bor. Saat bekerja dengan bagian bawah yang tertimbang, bobotnya hanya digunakan sebesar 75%. Nilai set WOB dikendalikan oleh indikator bobot hidrolik. Indikator berat GIV-2 Indikator berat GIV-2 terdiri dari transformator tekanan yang dipasang di ujung buntu tali kerekan, perangkat penunjuk dan vernier, perangkat perekam, tabung tembaga yang menghubungkan transformator tekanan dengan perangkat penunjuk dan perekam, reservoir untuk cadangan cairan, pompa tangan dan katup penutup. Seluruh sistem diisi dengan cairan: di musim panas, air atau larutan asam kromat 1% dalam air untuk melindungi dari korosi, dan di musim dingin, dengan cairan yang tidak membeku - campuran air dengan alkohol atau gliserin. Perangkat penunjuk adalah pengukur tekanan dengan pegas tubular, skala perangkat penunjuk dibagi menjadi 100 bagian. Vernier 8 digunakan untuk lebih akurat menentukan WOB. Skala vernier menempati seluruh keliling dan dibagi menjadi 40 divisi tanpa menunjukkan angka. Ketika beban yang bekerja di garis pengeboran berubah ke nilai maksimum yang sesuai dengan 100 divisi perangkat, jarum vernier membuat lima putaran. Jadi, satu pembagian vernier sesuai dengan setengah pembagian instrumen. Contoh. Tentukan harga satu divisi (dalam kg) dengan menggunakan alat penunjuk penunjuk berat dengan vernier (GIV-2), jika berat alat bor pada mata kail adalah 56 divisi. Setiap indikator berat memiliki sertifikat kalibrasi untuk kabel yang berfungsi dengan diameter 1", I1/8" atau 13/4", yang harus tersedia saat menghitung harga satu divisi. Menghitung. Dalam penunjukan alat penunjuk indikator berat GIV-2, menurut sertifikat kalibrasi pada tali dengan diameter i1 / 8 ", gaya (dalam kg) di salah satu ujung pada 50 divisi adalah 5415 kg, dan di 60 divisi 6650 kg. Perbedaan pembacaan usaha antara 50 dan 60 divisi akan ditentukan oleh 6650 - 5415 = 1235 kg. Indikator berat putar RIG-1 Indikator berat putar hidraulik dirancang untuk mengontrol pengoperasian mekanisme pengumpanan bit lubang bawah dengan mengubah berat pahat dalam proses pengeboran sumur dua dan tiga sisi dengan dua set pipa bor. Saat menggunakan mekanisme umpan downhole alat pengeboran ditangguhkan dengan menggunakan baji yang dipasang di rotor. Berat pahat ditransmisikan melalui rotor ke sensor piston hidrolik yang dipasang di bawah rotor dalam pemotongan batang putar; dalam hal ini, tekanan dibuat di sensor, yang diukur dengan pengukur tekanan pegas. Pada saat mekanisme lubang bawah dipicu ke seluruh panjang langkah batang, karena tergantung pada tali bor dan pelepasan mata bor dari bawah, berat alat meningkat, yang dicatat oleh jarum pengukur tekanan. Sensor indikator berat putar adalah blok 11 piston yang ditempatkan di lubang bodi persegi panjang. Piston dilengkapi dengan karet self-sealing ring yang mencegah cairan mengalir keluar dari rongga silinder. Silinder berkomunikasi satu sama lain dan diisi dengan cairan melalui fitting umum. Berat terukur terbesar dari alat ini adalah 130 ton. Tekanan dalam sistem hidrolik pada berat maksimum pahat adalah 120 kg/cm2. Dimensi sensor: tinggi 78 mm, lebar 94 mm, panjang 1060 mm. Dimensi kabinet instrumen: tinggi 430 mm, lebar 660 mm, kedalaman 170 mm. Berat sensor adalah 28 kg, dan kabinet instrumen adalah 17 kg. Revolusi kecil Seperti yang ditunjukkan oleh praktik pengeboran putar, jumlah putaran bit tricone yang optimal, di mana hasil terbaik dalam hal kecepatan mekanis dan penetrasi per bit diperoleh, berada di kisaran 200-220 rpm saat pengeboran di interval atas. dari sumur. Konsumsi cairan pencuci Jumlah cairan yang dipompa tergantung pada kekuatan kelompok pemompaan alat pengeboran dan alat bor yang digunakan. Pompa kuat modern dalam operasi berpasangan memungkinkan pemompaan cairan dalam jumlah 60 l / s atau lebih. Namun, ada kekhawatiran bahwa peningkatan berlebihan dalam kecepatan cairan yang dipompa di sumur yang terdiri dari batuan lemah akan menyebabkan washout lubang sumur. Pengukur aliran solusi Glypist RGR-1 Perangkat ini dirancang untuk mengukur dan merekam aliran lumpur pada keluaran pompa lumpur selama pengeboran sumur. Pengukur aliran terdiri dari sensor dan perangkat sekunder. Prinsip pengoperasian perangkat Dalam pipa di mana aliran terukur dari aliran lumpur mengalir, disk dipasang dengan tepi aliran, yang dipasang secara eksentrik pada sumbu. Ketika fluida bergerak, kepala kecepatan aliran bekerja pada piringan dan cenderung untuk memutarnya. Momen yang berlawanan dengan rotasi disk dibuat oleh pegas spiral yang terhubung ke sumbu tempat disk dipasang. Pada saat yang sama, ketika sumbu unit pengukur diputar, penggeser, yang terhubung dengan kuat ke sumbu, bergerak di sepanjang reochord, mengubah resistansi. Beras. 1. Pengukur aliran lumpur tanah liat RGR-1. Flow meter termasuk dalam skema jembatan keseimbangan elektronik otomatis EMD-207, yang digunakan untuk mengukur dan merekam aliran lumpur. Mode pengeboran turbin Mode pengeboran turbin ditentukan oleh nilai beban aksial *, laju aliran fluida pembilasan dan jumlah putaran bit. Dalam pengeboran turbin, peningkatan daya dan torsi pada poros turbodrill dikaitkan dengan peningkatan laju aliran fluida pengeboran. Dengan peningkatan jumlah cairan yang dipompa, bersama dengan peningkatan karakteristik daya turbodrill, pembersihan lubang dasar yang lebih baik dari stek tercapai dan kondisi kerja mata bor di lubang dasar ditingkatkan. Dengan peningkatan beban aksial pada bit, jumlah putaran poros turbodrill berkurang, dan torsi meningkat dan, pada jumlah putaran yang sama dengan nol, mencapai nilai maksimumnya. Dengan secara bertahap mengubah beban aksial pada bit, seseorang dapat menemukan sejumlah putaran di mana daya dan efisiensi yang dikembangkan oleh turbin, serta ROP akan maksimum. Beban yang dipilih, bahkan ketika mengebor di batu yang sama, karena keausan bit, harus diperiksa secara berkala dengan mengubah beban pada bit. Turbodrill desain modern memungkinkan untuk bekerja dengan WOB hingga 30 ton dan lebih. Revolusi kecil Jumlah putaran bit dalam pengeboran turbin tergantung pada jumlah cairan yang dipompa dan besarnya beban aksial. Dengan sedikit desain modern, jumlah putaran yang paling menguntungkan adalah 300-600 rpm. Saat bekerja di batuan keras, perlu untuk menambah beban pada bit, dan di batuan lunak - untuk mengurangi. Persyaratan disiplin teknologi dalam pengeboran Solusi mencuci Lumpur tanah liat, lumpur berbasis minyak, dan air industri digunakan sebagai cairan pembilas saat mengebor sumur minyak dan gas. Air industri banyak digunakan di wilayah minyak timur negara kita, yang memungkinkan untuk meningkatkan kondisi kerja pompa lumpur dan mengurangi konsumsi suku cadang, meningkatkan pembersihan cairan pengeboran dari stek, meningkatkan kinerja pompa pada operasi yang lebih rendah tekanan di outlet, meningkatkan kekuatan turbodrill (sebagai akibatnya menjadi menangani beban berat). Pengeboran pada bit dan ROP juga meningkat; jumlah alat angkat dan konsumsi bit berkurang, yang memungkinkan untuk meningkatkan kecepatan pengeboran komersial. Saat menggunakan air sebagai cairan pembilas, kondisi berikut harus diperhatikan: Saat beralih dari air ke larutan tanah liat, untuk menghindari lengketnya alat, perlu untuk memantau dengan cermat keadaan kualitas larutan tanah liat, mencegah parameternya memburuk. Bubuk tanah liat bentonit Saat mengebor sumur minyak dan gas sebagai aditif untuk solusi tanah liat struktural yang dibuat dari tanah liat lokal, serta bahan utama untuk persiapan cairan pengeboran dengan berat jenis rendah dan sifat tiksotropik tinggi saat pengeboran di area yang menyerap cairan pengeboran konvensional (air atau larutan tanah liat), aplikasikan bedak dari tanah liat bentonit. Bubuk bentonit dibuat dari tanah liat bentonit yang tidak mengandung gipsum, napal, pasir dan kotoran berbahaya lainnya. Kualitas bubuk ditentukan oleh parameter larutan yang disiapkan berdasarkan air suling, dan kehalusan tanah liat bentonit ditentukan oleh residu pada saringan (4900 lubang per 1 cm2), yang tidak boleh melebihi 5%. Karakteristik larutan tanah liat yang dibuat dari bubuk tanah liat bentonit harus sebagai berikut. Instrumen untuk menentukan kualitas larutan tanah liat Hydrometer AG-1 untuk mengukur berat jenis larutan tanah liat. Untuk menentukan berat jenis larutan tanah liat, perlu untuk melepaskan kaca dari pelampung dan mengisinya dengan larutan. Maka Anda harus memasukkan pelampung ke dalamnya, setelah itu hidrometer harus diturunkan ke dalam ember berisi air. Nilai berat jenis ditentukan oleh skala. Hydrometer AG-1 dapat mengukur berat jenis larutan tertimbang; untuk ini, perlu untuk melepaskan beban yang dapat dilepas, dan untuk membaca berat jenis pada skala kedua. Beras. 2. Hidrometer AG-1. Beras. 3. Viskometer medan standar SPV-5. Viskometer SPV-5 Dalam praktiknya, pengukuran dilakukan sebagai berikut. Bergantian, 500 dan 200 cm3 larutan tanah liat dituangkan ke dalam corong, menutup ujung bawah tabung dengan jari. Untuk pembacaan yang benar, larutan harus disaring melalui jaring yang sebelumnya dimasukkan ke dalam corong. Mengganti cangkir di bawah corong, jauhkan jari Anda dari ujung tabung, dan dengan tangan yang lain tandai waktu pada stopwatch. Waktu keluar 500 cm3 air dari viskometer dengan tabung b-mm adalah 15 detik. Nilai viskositas diukur dengan waktu habisnya 500 cmg larutan dalam hitungan detik. Mesin otomatis untuk pendaftaran parameter lumpur tanah liat APGR-1 Mesin otomatis APGR-1 dirancang untuk pengukuran berkelanjutan dan pencatatan berat jenis dan viskositas larutan tanah liat. Mesin terdiri dari enam unit terpisah yang dirakit pada kerangka umum: Melalui pompa sentrifugal sistem sirkulasi mengantarkan larutan tanah liat ke kameiu yang bersirkulasi. kelebihan lumpur mengalir keluar melalui pipa pembuangan 16. Tujuan pipa saluran air mempertahankan tingkat konstan dalam ruang dan kecepatan konstan solusi dalam kompartemen pengukuran. Dua tabung piezometrik direndam dalam kompartemen pengukuran, di mana udara disuplai. Udara dari blower melalui pengatur tekanan disuplai ke cangkir kontrol. Laju aliran udara diatur dengan menyesuaikan sekrup, biasanya jumlah udara 120-140 gelembung, yang sesuai dengan laju aliran 0,7-0,8 l / jam melalui setiap tabung. Beras. Gambar 4. Skema mesin untuk merekam parameter larutan tanah liat APGR-1. Berat jenis larutan ditentukan oleh perbedaan tekanan, yang diukur dengan pengukur tekanan diferensial pelampung yang merekam sendiri yang terhubung secara paralel ke tabung. Viskositas larutan diukur dengan viskometer medan standar tipe SPV-5, di mana tiga elektroda diturunkan. Setiap 10 menit. pengatur waktu menutup sirkuit kumparan katup solenoida, yang, ketika diaktifkan, membuka akses ke solusi ke viskometer. Ketika level larutan dalam corong menyentuh elektroda atas, yang sesuai dengan volume 800-1000 cm3, katup akan menutup secara otomatis dan aliran larutan akan berhenti. Tingkat larutan dalam viskometer akan mulai turun. Ketika 700 cm3 slurry tetap berada di viskometer, elektroda tengah tidak lagi menyentuh levelnya dan jam listrik 8 akan menyala.Ketika 200 cm3 slurry tertinggal di viskometer, elektroda bawah tidak akan lagi menyentuh level dan aliran waktu akan berhenti merekam. Setelah 3 menit. setelah dimulainya siklus pengukuran viskositas, katup 6 akan terbuka, air akan mengalir ke viskometer untuk menyiram perangkat. Pembilasan perangkat berlangsung 30-40 detik. Siklus pengukuran berikutnya dimulai setelah 6 menit. setelah akhir yang sebelumnya. Rentang pengukuran berat jenis 1,0-2,0 g/cm3, batas pengukuran viskositas 50-100 detik. Kesalahan pengukuran berat jenis ±0,02g/cm3, pengukuran viskositas ±1 detik. Kecepatan pergerakan diagram disk alat perekam 1 sekitar / hari. Catu daya mesin: arus bolak-balik tegangan 220 V, daya 300 VA. Dimensi keseluruhan mesin 780 X 450 X 750 mm. Berat 130kg. Sump OM-1 Beras. 5. Alat TsS-1 untuk menentukan kestabilan larutan lempung. 50 cm3 larutan tanah liat dituangkan ke dalam bak, yang kemudian diencerkan dengan air hingga volume 500 cm3. Isinya sangat terguncang, setelah itu perangkat ditempatkan dalam posisi vertikal selama 3 menit. Waktu ini cukup untuk pengendapan pasir, karena dalam hal ini semua partikel yang lebih besar dari 0,02 mm memiliki waktu untuk mengendap. Partikel yang belum sempat mengendap adalah debu dan praktis tidak berpengaruh terhadap kualitas larutan lempung. Penentuan stabilitas bubur Stabilitas diukur sebagai berikut. Sebuah bejana berbentuk silinder diisi dengan larutan tanah liat dan dibiarkan selama 24 jam. Jika pada mulanya larutan di dalam bejana itu homogen, kemudian setelah didiamkan, sifat-sifatnya di bagian atas dan bawah bejana menjadi berbeda. Setelah pengendapan 24 jam, larutan tanah liat dikeringkan dari bagian atas bejana melalui saluran keluar samping yang dilengkapi dengan tabung karet dan penjepit, dan dari bagian bawah melalui saluran keluar bawah. Ukur berat jenis kedua bagian larutan dengan hidrometer. Perbedaan berat jenis dilambangkan dengan huruf C dan diambil sebagai ukuran stabilitas larutan lempung. Beras. 6. Wadah logam OM-1- Contoh. Berat jenis larutan tanah liat di bagian atas bejana adalah 1,20, dan di bagian bawah adalah 1,24 g/cm3; dalam hal ini, stabilitasnya akan sama dengan C = 1,24 - 1,20 = 0,04 g/cm3. Semakin tinggi angka yang menunjukkan stabilitas, semakin buruk kualitas lumpurnya. Untuk larutan lempung tak berbobot, stabilitasnya tidak boleh lebih dari 0,02, dan untuk yang tertimbang, tidak lebih dari 0,06 g/cm3. Lumpur harian Untuk menentukan lumpur harian, larutan tanah liat dituangkan ke dalam gelas kimia dan dibiarkan selama 24 jam. Kemudian volume lapisan cairan ringan yang dilepaskan dari larutan diukur sebagai persentase volume volume larutan tanah liat. Untuk larutan lempung yang baik, sedimen harian adalah nol; secara umum, tidak boleh lebih tinggi dari 2-4%. Penentuan tegangan geser statis Tegangan geser statis adalah kekuatan struktur spasial kaku yang terjadi dalam larutan lempung dalam keadaan diam akibat adhesi partikel lempung. Karena kekuatan struktur bubur meningkat dengan waktu yang berlalu sejak akhir pencampuran, ditemukan bahwa pengukuran harus dilakukan setelah 1 menit. dan setelah 10 menit. setelah akhir pencampuran; dalam hal ini, tegangan geser statis dilambangkan dengan vr dan 010. Pengukuran tegangan geser statis pada perangkat SNS-1 dilakukan dengan cara sebagai berikut. Solusi tanah liat dituangkan ke dalam gelas yang dipasang di atas meja berputar. Rotasi meja ditransmisikan melalui pegas melingkar 3 dari motor listrik kecil. Setelah pencampuran yang kuat dari larutan dalam gelas, sebuah silinder yang tergantung pada braket pada benang baja elastis tipis direndam di dalamnya. Setelah jeda 1 atau 10 menit. nyalakan mesin, kaca mulai berputar dengan kecepatan satu putaran dalam 5 menit. Selama struktur dalam bubur tidak hancur, rotasi dari kaca ditransmisikan melalui lapisan bubur, seolah-olah melalui benda padat, ke silinder, yang berputar dengan kaca. Pada saat yang sama, ulir 2 dipelintir dan resistensi terhadap puntiran lebih lanjut meningkat. Tetapi ada saatnya ketika hambatan benang mengatasi kekuatan struktur larutan tanah liat di dinding silinder dan silinder berhenti. Dalam posisi ini, sudut puntir terbesar dari ulir dari posisi awal diperhatikan, dan menurut data yang tersedia di paspor perangkat, nilai tegangan geser statis yang sesuai dengan sudut puntir ini dihitung. Untuk membaca sudut putaran, dial dipasang pada perangkat. Beras. 7. Alat CHG -1 untuk menentukan tegangan geser statis larutan lempung. Untuk pembobotan, larutan lempung dianggap cocok memiliki tegangan geser statis dalam kisaran s = 30 4 - m - 50 mg / cm2. Penentuan kehilangan air mortar tanah liat Pengukuran kehilangan air pada rig pengeboran dilakukan dengan menggunakan instrumen VM-6. Contoh larutan tanah liat dengan volume 120 cm3 dituang ke dalam gelas saring 1. Bagian bawah gelas mewakili Beras. 8. Perangkat VM-6 untuk menentukan kehilangan air dari larutan tanah liat. kisi untuk aliran keluar cairan yang dipisahkan. Kertas saring ditempatkan pada jeruji ini sebagai partisi berpori. Tekanan berlebih pada larutan tanah liat dibuat oleh berat plunger dan casing dengan cincin beban, dipilih dengan perhitungan pembuatan tekanan berlebih dalam 1kg/cm2. Tekanan plunger pada slurry ditransmisikan melalui oli mesin yang mengisi silinder. Volume air yang diperas keluar dari lumpur ditentukan dengan menurunkan plunger di dalam silinder. Untuk referensi, tanda dibuat pada silinder, dan skala dilampirkan pada casing, bagian yang menunjukkan jumlah kehilangan air. Penutup bawah memiliki katup penutup, terdiri dari cakram baja dengan gasket karet di bagian atas dan sekrup tekanan. Katup penutup ini digunakan untuk memastikan bahwa air tidak keluar dari bubur selama perakitan dan penyetelan instrumen sebelum pengukuran. Perangkat VM-6 memungkinkan Anda mengukur kehilangan air secara langsung hingga 40 cm3. Ke Kategori: - Peralatan pengeboran Efisiensi pengeboran tergantung pada faktor kompleks: beban aksial pada bit, kecepatan rotasi bit, laju aliran pengeboran solusi dan parameter kualitas pengeboran mortar, jenis bit, kondisi geologi, sifat mekanik batuan. Opsi mode sorot pengeboran, yang dapat diubah dari konsol pengebor selama pengoperasian mata bor di lubang dasar, dan faktor yang ditetapkan pada tahap desain konstruksi sumur, beberapa di antaranya tidak dapat diubah dengan cepat. Yang pertama disebut dikelola. Kombinasi tertentu dari mereka, di mana mekanik pengeboran sumur, disebut mode pengeboran. Mode pengeboran yang memberikan kinerja terbaik dalam kondisi tertentu pengeboran, disebut optimal. Terkadang dalam proses pengeboran tugas khusus juga harus diselesaikan - mengebor sumur melalui lapisan penyerap, memastikan kelengkungan sumur minimal, pemulihan inti maksimum, pembukaan lapisan produktif berkualitas tinggi. Mode pengeboran, yang masalah tersebut diselesaikan, disebut khusus. Setiap parameter mode pengeboran mempengaruhi efisiensi penghancuran batuan, dan pengaruh satu parameter tergantung pada tingkat yang lain, yaitu, ada faktor yang saling mempengaruhi. Indikator kinerja utama berikut dibedakan: pengeboran minyak dan gas sumur: pengeboran pada kecepatan bit, mekanis, dan trip pengeboran. Pengeboran per bit Hd (m) adalah indikator yang sangat penting yang menentukan konsumsi bit per pengeboran sumur dan kebutuhannya berdasarkan area dan ROP secara keseluruhan, jumlah perjalanan, keausan pengangkatan peralatan, masukan tenaga kerja pengeboran, kemungkinan beberapa komplikasi. Penetrasi per bit sangat tergantung pada abrasivitas batuan, daya tahan bit, ketepatan pemilihannya, mode pengeboran dan kriteria untuk mengerjakan bit. Kecepatan mekanik (Vm): Vm = Hd / Tm di mana Hd - penetrasi per bit, m; Tm - durasi penghancuran mekanis batuan di bagian bawah atau waktu penetrasi interval, h. Jadi, Vm- kecepatan rata-rata lubang bawah. Itu dapat ditentukan oleh bit terpisah, interval terpisah, seluruh sumur Lc, oleh RBR, dll .: Vm = Lc / Tm Alokasikan kecepatan mekanis saat ini (seketika): Vm = dh / dt Dengan sifat-sifat batuan yang diketahui, kecepatan mekanis mencirikan efisiensi penghancurannya, pemilihan dan pengembangan bit yang benar, metode pengeboran dan parameter operasi, jumlah daya yang disuplai ke lubang dasar dan penggunaannya. Jika di batuan dan interval yang sama di satu sumur, lajunya lebih rendah daripada di sumur lain, perlu untuk memperbaiki rezim. Perubahan kecepatan mekanik saat ini dikaitkan dengan keausan bit, pergantian batuan dalam hal kekerasan, perubahan parameter rezim dalam proses pengerjaan bit, yang menunjukkan kelayakan mengangkat bit. kecepatan jelajah Vp = Hd / (Tm + Sdt) di mana Hd - penetrasi per bit, m; m – durasi operasi bit di lubang dasar, h; sp adalah durasi bit descending dan rise, tool build-up, h. Kecepatan jelajah menentukan laju pendalaman sumur, hal ini menunjukkan bahwa laju penetrasi lubang sumur tidak hanya bergantung pada perkembangan mata bor, tetapi juga pada volume dan kecepatan perjalanan. Jika Anda bekerja dengan bit yang aus untuk waktu yang lama atau menaikkan bit sebelum waktunya, maka Vp berkurang. Mata bor, dinaikkan saat mencapai kecepatan perjalanan maksimum, memberikan penetrasi bagasi tercepat. Kecepatan perjalanan rata-rata untuk sumur dinyatakan sebagai: Vр = Lс / (Тm + sp) 5.1. PENGARUH PARAMETER MODE PADA INDIKATOR PENGEBORAN 5.1.1. EFEK BEBAN AKSIAL Penghancuran batuan di dasar lubang dengan cara mekanis tidak mungkin dilakukan tanpa menimbulkan beban aksial pada mata bor. pada gambar. 5.1. menunjukkan ketergantungan kecepatan mekanik pengeboran Vm dari beban aksial G pada bit tricone saat mengemudi batuan lunak (kurva 1), keras sedang (kurva 2), keras (kurva 3) dan keras (kurva 4) pada kecepatan rotasi rendah konstan (hingga 60 rpm) dan cukup pembilasan untuk waktu yang singkat ketika keausan bit dapat diabaikan. Seperti dapat dilihat dari gambar, kecepatan mekanik terus meningkat dengan meningkatnya beban aksial, tetapi laju pertumbuhannya untuk batuan lunak lebih cepat, karena lebih mendalam perendaman gigi di bawah beban yang sama. Pada kondisi tegakan dan lapangan, terjadi perubahan laju pertumbuhan Vm dari G selama transisi dari penghancuran batuan oleh abrasi pada beban aksial kecil ke penghancuran batuan di daerah kelelahan dan volumetrik pada umumnya. Jika kecepatan rotasi bit tidak berubah dan kebersihan lubang dasar yang memadai dipastikan, nilai reses per satu putaran dу meningkat dengan peningkatan beban aksial spesifik Rud, seperti yang ditunjukkan pada Gambar. 5.2. (kurva OABS). Pada beban yang sangat rendah, tegangan pada bidang kontak gigi pemotong dengan batu kurang dari batas kelelahan yang terakhir; oleh karena itu, hanya deformasi elastis batuan yang terjadi selama lekukan (bagian OA). Penghancuran batuan di zona ini, yang biasa disebut sebagai area destruksi permukaan, dapat terjadi karena abrasi dan, kemungkinan, micro-splitting kekasaran permukaan ketika gigi slip. Jika beban lebih tinggi (bagian AB), maka tekanan pada bidang kontak gigi dengan lubang bawah melebihi batas kelelahan, tetapi lebih kecil dari kekuatan tarik batuan. Oleh karena itu, pada tumbukan pertama gigi di daerah ini, batuan mengalami deformasi, mungkin saja microcracks awal terbentuk, tetapi penghancurannya belum terjadi. Dengan pukulan berulang pada gigi di tempat yang sama, retakan mikro awal berkembang secara mendalam sampai pukulan berikutnya pecah. Semakin besar gaya yang bekerja pada gigi, semakin sedikit tumbukan yang diperlukan untuk penghancuran. Zona ini disebut area kegagalan volume-fatigue. Pada beban yang lebih tinggi, penghancuran batu terjadi dengan setiap benturan gigi. Oleh karena itu, daerah di sebelah kanan titik B disebut daerah pemusnahan volumetrik efektif batuan. Di wilayah OA, pendalaman per satu putaran dу kecil dan meningkat sangat lambat, sebanding dengan beban spesifik pada bit Rud. Di bawah beban spesifik, pahami rasio beban pada bit G dengan diameternya. Di daerah kegagalan kelelahan, depresi tumbuh lebih cepat daripada peningkatan beban spesifik, dan hubungan di antara mereka memiliki karakter power-law. Di area penghancuran volumetrik batuan yang efektif, depresi per putaran meningkat dengan cepat - kira-kira sebanding dengan beban spesifik (atau agak lebih cepat), jika pembersihan lubang dasar yang cukup disediakan. Sifat hubungan antara pendalaman per satu putaran bit dу dan beban spesifik Rud berubah secara signifikan segera setelah pembersihan lubang bawah menjadi tidak mencukupi dan partikel yang sebelumnya terkelupas menumpuk di atasnya, yang tidak punya waktu untuk pindah ke bit dekat daerah. Partikel tersebut juga dihancurkan dengan dampak baru dari gigi pemotong di bagian bawah. Oleh karena itu, dengan memburuknya pembersihan lubang dasar, peningkatan pendalaman per satu putaran mata bor akan berkurang dengan peningkatan beban spesifik. Jadi, menurut kurva OAVDE yang diperoleh dengan pengeboran dengan aliran kedua cairan pembilasan Q1, reses per 1 putaran meningkat dengan cepat, sampai beban spesifik tidak melebihi P111sp. Pada beban di atas P111ud, pertumbuhan pendalaman pertama-tama melambat, dan kemudian (di sebelah kanan titik F) pendalaman per satu putaran berkurang karena memburuknya pembersihan lubang dasar. Dalam kasus peningkatan konsumsi kedua ke Q2, efek pembersihan lubang dasar yang memburuk menjadi nyata pada beban spesifik yang lebih tinggi (di sebelah kanan titik G pada kurva ABGH). 5.1.2. EFEK KECEPATAN BIT Dengan perubahan frekuensi rotasi bit, jumlah lesi lubang dasar oleh gigi bit kerucut berubah. Pada frekuensi putaran bit yang rendah, periode waktu di mana retakan pada batuan tetap terbuka, yang terbentuk selama lekukan gigi, cukup bagi filtrat untuk menembus retakan ini. pengeboran solusi (atau solusi itu sendiri). Tekanan pada partikel dari atas dan bawah praktis sama, dan retakan tidak dapat menutup setelah gigi dipisahkan dari batu. Dalam hal ini, pelepasan partikel terkelupas dari bawah dan pemindahannya difasilitasi. Dengan peningkatan frekuensi rotasi, interval waktu di mana retakan dibuka berkurang, dan filtrat dapat mengisinya. Jika celah ini menjadi sangat kecil, filtrat tidak akan punya waktu untuk menembus celah, retakan akan menutup setelah gigi pemotong terlepas dari batu, dan gaya tekan dan kue filter akan menahan partikel dan mencegahnya dikeluarkan. dari lubang bawah. Oleh karena itu, lapisan partikel yang terkelupas, tetapi tidak dihilangkan akan tetap berada di lubang bawah, yang akan digiling ulang oleh gigi mata bor.
5.1.3. DAMPAK ALIRAN PENGEBORAN LARUTAN Sirkulasi terus menerus pengeboran solusi di pengeboran harus memastikan kebersihan lubang sumur dan lubang dasar, mendinginkan bit, berkontribusi pada penghancuran batu yang efektif, dan mencegah komplikasi. Pengaruh laju aliran larutan pada kecepatan mekanik pengeboran ditunjukkan pada gambar. 5.4. Seperti dapat dilihat dari gambar, pada beban aksial konstan dan frekuensi rotasi bit dengan peningkatan laju aliran kedua pengeboran larutan meningkatkan pembersihan lubang dasar dan meningkatkan kecepatan penetrasi mekanis. Namun, peningkatan larutan kedua hanya efektif sampai mencapai nilai Qd tertentu, pada Qmax, laju penetrasi mekanis menjadi stabil. Nilai Qd tergantung pada desain mata bor, skema pembersihan lubang dasar, beban aksial spesifik, kecepatan putar, kekerasan batuan dan sifat-sifatnya. pengeboran larutan.
5.1.4. PENGARUH SIFAT LUMPUR PENGEBORAN Untuk kecepatan mekanik pengeboran kepadatan, viskositas, filtrasi, kandungan pasir dan sejumlah parameter lainnya mempengaruhi pengeboran larutan. Kepadatan memiliki efek paling signifikan pengeboran larutan. Efek ini terutama disebabkan oleh peningkatan tekanan hidrostatik pada lubang bawah dan peningkatan penurunan tekanan antara sumur dan formasi yang dibor, akibatnya kondisi pembentukan retakan memburuk, partikel terkelupas ditekan ke massa. Oleh karena itu, efek r paling signifikan di bidang penghancuran volumetrik batuan, dan pada pengeboran di bidang penghancuran dan abrasi permukaan, itu tidak signifikan. Dengan penurunan kepadatan, efek kompresi serba tidak merata lebih terasa, yang memfasilitasi penghancuran batuan. Semakin tinggi permeabilitas batuan dan semakin besar kehilangan air (filtrasi), semakin rendah viskositas filtrat, semakin rendah frekuensi putaran, semakin lama waktu kontak, semakin lemah pengaruh densitas larutan, karena tekanan di dasar lubang dan di kedalaman tusukan punya waktu untuk menyamakan. 5.2. FITUR MODE ROTASI PENGEBORAN. Peningkatan beban aksial dan kecepatan, peningkatan kepadatan, viskositas dan konsentrasi partikel padat, penurunan konsumsi di bawah Qd, serta kapasitas panas, konduktivitas termal dan pelumasan pengeboran solusi, umpan bit yang tidak rata (tersentak), getaran memanjang dan melintang dari bagian bawah string bor, suhu tinggi di bagian bawah - semua ini mengurangi waktu produktif bit di bagian bawah. Namun, tujuan utamanya bukanlah untuk meningkatkan durasi tinggal bit di bagian bawah, tetapi untuk mendapatkan lebih banyak penetrasi per bit dalam waktu sesingkat mungkin. Oleh karena itu, jika perubahan pada beberapa parameter menyebabkan pengurangan durasi bit di bagian bawah, tetapi pada saat yang sama kecepatan mekanik meningkat dan penetrasi per bit meningkat, maka disarankan. Sejak pengaturan mode pengeboran saling berhubungan, maka yang paling efektif pengeboran dicapai hanya dengan kombinasi optimal dari parameter ini, yang tergantung pada sifat fisik dan mekanik batuan, desain mata bor, kedalaman batuan yang akan dibor, dan faktor lainnya. Peningkatan salah satu parameter mode, misalnya, beban aksial, meningkatkan efisiensi pengeboran hanya sampai mencapai nilai optimal untuk kombinasi parameter lain yang diberikan. Meningkatkan parameter yang dipertimbangkan di atas nilai optimal ini dapat lebih meningkatkan efisiensi. pengeboran hanya jika semua atau beberapa parameter lain diubah pada saat yang sama (misalnya, peningkatan aliran fluida pembilasan, penurunan kecepatan). Kombinasi yang diubah dari parameter mode lainnya sesuai dengan nilai optimal baru dari yang sedang dipertimbangkan. Mengubah parameter mode hanya dimungkinkan dalam batas tertentu, yang bergantung pada kekuatan bit, fitur metode pengeboran, Parameter teknik pengeboran pengaturan dan sejumlah faktor lainnya. Mengatur aliran pengeboran lumpur dapat dilakukan dengan tiga cara: dengan mengganti busing satu diameter dalam silinder pompa lumpur dengan busing dengan diameter berbeda, dengan mengubah jumlah pompa lumpur yang beroperasi secara paralel, dengan mengubah jumlah pukulan ganda piston di pompa . Dengan dua metode pertama, laju aliran larutan hanya dapat diubah secara bertahap, dengan yang ketiga, perubahan halus juga dimungkinkan. Yang kedua dari metode di atas digunakan, sebagai suatu peraturan, dalam kasus perubahan diameter bit: ketika pengeboran dari bagian atas sumur dengan bit berdiameter besar, dua pompa yang beroperasi secara bersamaan digunakan. Saat pindah ke pengeboran bagian berikutnya dengan bit berdiameter lebih kecil, salah satu pompa sering dimatikan. Bushing hanya dapat diganti saat pompa tidak bekerja. Oleh karena itu, dalam banyak kasus, laju aliran fluida selama pengoperasian mata bor di lubang dasar tetap praktis tidak berubah. Jika durasi perjalanan panjang (beberapa puluh jam), laju aliran pada akhir perjalanan mungkin sedikit berkurang karena peningkatan kebocoran pada pompa karena keausan piston. Tenaga hidrolik downhole dapat disesuaikan dengan mengubah salah satu aliran pengeboran solusi, atau diameter nozel jet dalam bit, atau jumlah nozel tersebut. Jelas, diameter nozel hanya dapat diubah saat menyiapkan bit baru untuk dimasukkan ke dalam sumur. Jumlah nozel yang beroperasi juga dapat dikurangi selama periode operasi bit di bagian bawah, jika aliran fluida masuk pengeboran pipa, jatuhkan bola dengan diameter yang sesuai, itu akan memblokir saluran masuk di salah satu nozel dan mematikannya dari pekerjaan. Pada saat yang sama, kecepatan jet dan penurunan tekanan di nozel kerja yang tersisa akan meningkat, dan daya hidraulik di lubang bawah akan meningkat. Metode pengaturan daya hidrolik di bagian bawah ini dapat digunakan ketika tekanan operasi di dalam pompa kurang dari maksimum yang diizinkan untuk diameter tertentu dari busing di dalamnya. |