Wiercenie to konstrukcja górniczego wyrobiska kierunkowego o małej średnicy i dużej głębokości. Ujście studni znajduje się na powierzchni ziemi, a dno znajduje się na dnie. Dziś wiercenie w poszukiwaniu ropy i studnie gazowe do wydobywania odpowiednich minerałów.
Zadania i cele wierceń dla ropy i gazu
Dziś ropę i gaz wydobywa się ze studni. Pomimo dużej liczby różnych sposobów wykonania studni, wciąż się rozwijają, opracowywane są nowe metody, aby przyspieszyć pracę i obniżyć koszty ich kosztów.
Nowoczesny proces wiercenia składa się z następujących etapów:
- tonięcie szybu
- Separacja warstw
- Dobrze rozwój i eksploatacja
Wiercenie studni dzieli się na dwa etapy, które powinny odbywać się równolegle do siebie: pogłębianie dna i oczyszczanie go ze skał ulegających zniszczeniu. Separacja skał odbywa się również w dwóch etapach: montaż rur osłonowych, ich łączenie i uszczelnianie ze sobą.
Pomimo tego, że w domu nikt nie wykona odwiertu przemysłowego na ropę i gaz, warto wiedzieć, ile kosztuje szyb naftowy i jakie metody są najczęściej stosowane.
Proces wiercenia ropy - wideo
Podstawowe metody wiercenia
Obecnie praktykowane są różne metody wiercenia. szyby naftowe, ale najczęstsze z nich to:
- Wiercenie obrotowe z kesonem do studni
- Wiercenie turbin
- Wiercenie śrub
Jedną z popularnych metod jest wiercenie obrotowe szybów naftowych. Dłuto, wchodząc w głąb skał gruntowych, obraca się razem z rurami wiertniczymi. Moment obrotowy takiego systemu zależy przede wszystkim od oporu napotykanych po drodze skał.
Obrotowe wiercenie studni swoją popularność zawdzięcza takim zaletom, jak odporność na duże wahania WOB, niezależność ustawień od czynników zewnętrznych oraz duży przelot w jednym przebiegu.
Wiercenie turbinowe odwiertów na ropę odbywa się za pomocą instalacji, w której świder współdziała z turbiną wiertniczą. Jednostka jest wprawiana w ruch obrotowy przez przepływ płynu, który krąży pod wysokim ciśnieniem przez system stojanów i wirników. Z tego powodu m.in. podnoszenie i pompowanie wody studziennej.
Moment obrotowy jest niezależny od głębokości odwiertu, właściwości skały, prędkości obrotowej i obciążenia osiowego. Jednocześnie współczynnik przenikania przy wiercenie turbiny o rząd wielkości wyższy niż w przypadku rotacji, ale koszt pracy jest większy ze względu na zapotrzebowanie na dużą ilość energii, nie ma możliwości szybkiej rekonfiguracji parametrów instalacji.
Wiercenie śrubowe odwiertów naftowych i gazowych polega na tym, że główny mechanizm roboczy składa się z dużej liczby mechanizmów śrubowych, dzięki czemu uzyskuje się optymalną częstotliwość obrotu wiertła. Pomimo wszystkich perspektyw, metoda ta nie została jeszcze odpowiednio rozpowszechniona, ale ma w tym ogromny potencjał.
Cena emisyjna
Po odkryciu, jak wierci się szyby naftowe, pytanie, ile trzeba wydać na wiercenie kolejnego metra lejka, z pewnością staje się interesujące.
Dziś koszt wiercenia szybu naftowego jest bardzo duży i zależy od wielu czynników:
- Głębokość studni
- Konieczność zakupu osłonki plastikowe rury do studni
- Warunki otoczenia
- Terminy
Jeśli mówimy o dokładnych liczbach, cena studni o głębokości 2000-3000 metrów wyniesie od 30 do 60 milionów rubli. Wiercenie poszukiwawcze będzie kosztować około 40-50% kosztów wiercenia.
1. Krótka historia rozwoju wiertnictwa
Na podstawie znalezisk i badań archeologicznych ustalono, że około 25 tysięcy lat temu prymitywny człowiek wiercił w nich otwory do mocowania uchwytów do produkcji różnych narzędzi. Jako narzędzie pracy służyło wiertło krzemienne.
W starożytnym Egipcie wiercenie obrotowe (wiercenie) było używane do budowy piramid około 6000 lat temu.
Pierwsze doniesienia Chińczyków studnie do wydobywania wody i solanek zawarte są w dziełach filozofa Konfucjusza, spisanych około 600 roku p.n.e. Odwierty wykonano metodą wierceń udarowych i osiągnęły głębokość 900 m. Wskazuje to, że wcześniej technika wiercenia rozwijała się przez co najmniej kilkaset lat. Czasami podczas wiercenia Chińczycy natrafiali na ropę i gaz. Tak więc za 221 ... 263 lata. OGŁOSZENIE w Syczuanie ze studni o głębokości ok. 240 m wydobywano gaz, który służył do waporyzacji soli.
Dokumentalne dowody na techniki wiercenia w Chinach są nieliczne. Jednak sądząc po starożytnym malarstwie chińskim, płaskorzeźbach, gobelinach, panelach i haftach na jedwabiu, technika ta znajdowała się na dość wysokim etapie rozwoju.
Wiercenie pierwszych studni w Rosji datuje się na IX wiek i wiąże się z wydobyciem roztworów soli kuchennej w rejonie Starej Russy. Wydobycie soli było bardzo rozwinięte w XV..XVII wieku, o czym świadczą odkryte ślady otworów wiertniczych w okolicach miasta Solikamsk. Ich głębokość sięgała 100 m przy początkowej średnicy studni do 1 m.
Często zawalały się ściany studni. Dlatego do ich mocowania używano albo pustych pni drzew, albo rur utkanych z kory wierzby. Pod koniec XIX wieku. ściany studni zaczęto mocować żelaznymi rurami. Zostały wygięte z blachy i nitowane. Podczas pogłębiania studni rury posuwano za narzędziem wiertniczym (wiertło); w tym celu zostały wykonane z mniejszej średnicy niż poprzednie. Te rury zostały później nazwane obudowa. Ich konstrukcja została z czasem ulepszona: zamiast nitowanych, stały się bezszwowe z gwintowanymi końcami.
Pierwsza studnia w Stanach Zjednoczonych została wywiercona w 1806 roku w pobliżu miasta Charleston w Zachodniej Wirginii. Kentucky przypadkowo znalazł olej.
Pierwsze wzmianki o wykorzystaniu odwiertów do poszukiwań ropy naftowej pochodzą z lat 30. XIX wieku. Na Tamanie, przed wykopaniem szybów naftowych, przeprowadzili wstępne rozpoznanie wiertłem. Naoczny świadek pozostawił następujący opis: „Gdy planują wykopać studnię w nowym miejscu, najpierw próbują ziemi wiertłem, wpychając ją i dodając trochę wody, aby łatwiej wchodziła i po wyjęciu, czy będzie olej, to w tym miejscu zaczną kopać czworokątną dziurę ”.
W grudniu 1844 r. członek Rady Administracji Głównej Terytorium Zakaukaskiego V.N. Siemionow wysłał raport do swojego kierownictwa, w którym pisał o potrzebie ... pogłębienia niektórych odwiertów za pomocą odwiertu ... i ponownych poszukiwań ropy również za pomocą odwiertu między odwiertami Bałachani, Bajbat i Kabristan. Jak V.N. Semenov, pomysł ten zasugerował mu kierownik pól naftowych i solnych w Baku i Shirvan, inżynier górnictwa N.I. Woskobojnikow. W 1846 r. Ministerstwo Finansów przyznało niezbędne fundusze i rozpoczęto wiercenia. Wyniki wierceń są wymienione w memorandum gubernatora Kaukazu hrabiego Woroncowa z dnia 14 lipca 1848 r.: „... w Bibi-Heybat wywiercono studnię, w której znaleziono ropę”. To było pierwszy na świecie szyb naftowy!
Krótko przed tym, w 1846 r., francuski inżynier Fauvel zaproponował metodę ciągłego czyszczenia studni - ich mycie. Istota metody polegała na tym, że z powierzchni ziemi przez wydrążone rury do studni pompowano wodę, unosząc kawałki skały w górę. Metoda ta bardzo szybko zyskała uznanie, bo. nie wymagał przerwania wiercenia.
Pierwszy szyb naftowy w Stanach Zjednoczonych wywiercił w 1859 r. Na terenie Titesville w Pensylwanii wykonał go E. Drake, który pracował na zlecenie Seneca Oil Company. Po dwóch miesiącach nieprzerwanej pracy pracownikom E. Drake'a udało się wywiercić studnię o głębokości zaledwie 22 m, ale i tak dawała ona ropę. Do niedawna studnia ta była uważana za pierwszą na świecie, ale znalezione dokumenty dotyczące pracy prowadzonej przez V.N. Semenov przywrócił sprawiedliwość historyczną.
Wiele krajów przypisuje narodziny swojego przemysłu naftowego wierceniu pierwszego odwiertu, który dostarczył komercyjnej ropy naftowej. Tak więc w Rumunii odliczanie odbywa się od 1857 r., W Kanadzie - od 1858 r., W Wenezueli - od 1863 r. W Rosji przez długi czas wierzono, że pierwszy szyb naftowy wywiercono w 1864 r. w Kubanie na brzegach na rzece. Kudako pod dowództwem pułkownika A.N. Nowosilcew. Dlatego w 1964 roku w naszym kraju uroczyście obchodzono 100-lecie krajowego przemysłu naftowego, a od tego czasu co roku obchodzony jest „Dzień Pracownika Przemysłu Naftowego i Gazowniczego”.
Liczba odwiertów wierconych na polach naftowych pod koniec XIX wieku gwałtownie rosła. Tak więc w Baku w 1873 r. było ich 17, w 1885 - 165, w 1890 - 356, w 1895 - 604, a następnie w 1901 - 1740. W tym samym czasie znacznie wzrosła głębokość szybów naftowych. Jeśli w 1872 r. Było to 55 ... 65 m, to w 1883 r. Było to 105 ... 125 m, a pod koniec XIX wieku. osiągnął 425...530 m.
Pod koniec lat 80-tych. ubiegłego wieku w okolicach Nowego Orleanu (Luizjana, USA) wiercenie obrotowe do oleju z płukaniem studni roztworem gliny. W Rosji wiercenie obrotowe z płukaniem po raz pierwszy zastosowano w pobliżu Groznego w 1902 r., a ropa została odkryta na głębokości 345 m.
Początkowo wiercenie obrotowe odbywało się poprzez obracanie świdra wraz z całym ciągiem wiertniczym bezpośrednio z powierzchni. Jednak przy dużej głębokości studni waga tej kolumny jest bardzo duża. Dlatego w XIX wieku pierwsze propozycje kreacji silniki wgłębne, tych. silniki umieszczone na dnie rur wiertniczych bezpośrednio nad wiertłem. Większość z nich pozostała niezrealizowana.
Po raz pierwszy w praktyce światowej radziecki inżynier (później członek korespondent Akademii Nauk ZSRR) mgr inż. Kapelyushnikov został wynaleziony w 1922 roku turbowiertarka, która była jednostopniową turbiną hydrauliczną z przekładnią planetarną. Turbina była napędzana cieczą myjącą. W latach 1935...1939. projekt turbowiertarki został ulepszony przez grupę naukowców kierowaną przez P.P. Szumiłowa. Proponowana przez nich turbowiertarka to wielostopniowa turbina bez skrzyni biegów.
W 1899 został opatentowany w Rosji wiertarka elektryczna, który jest silnikiem elektrycznym połączonym z dłutem i zawieszonym na linie. Nowoczesna konstrukcja wiertarki elektrycznej została opracowana w 1938 roku przez radzieckich inżynierów A.P. Ostrovsky i N.V. Aleksandrowa, a już w 1940 r. wywiercono pierwszą studnię wiertarką elektryczną.
W 1897 r. na Oceanie Spokojnym w rejonie około. Somerland (Kalifornia, USA) został wdrożony po raz pierwszy wiercenia na morzu. W naszym kraju pierwszy odwiert na morzu wykonano w 1925 r. w zatoce Iljicza (w pobliżu Baku) na sztucznie utworzonej wyspie. W 1934 r. N.S. Timofiejew na temat. Artem na Morzu Kaspijskim został przeprowadzony wiercenie studni, w którym kilka studni (czasem ponad 20) jest wierconych ze wspólnego miejsca. Następnie metoda ta znalazła szerokie zastosowanie w wierceniu w przestrzeniach zamkniętych (między bagnami, przybrzeżnymi platformami wiertniczymi itp.).
Od początku lat 60. świat zaczął używać w celu zbadania głębokiej struktury Ziemi bardzo głębokie wiercenie.
2. Pojęcie studni
Wiercenie- to proces budowy studni poprzez niszczenie skał. dobrze zwany górnictwem okrągły przekrój, skonstruowany bez dostępu ludzi, w którym długość jest wielokrotnie większa niż średnica.
Wierzchołek studni nazywa się usta, na dole - ubój, powierzchnia boczna - Ściana i przestrzeń ograniczona ścianą - studnia. Długość studni to odległość od ust do dna wzdłuż osi tułowia, oraz głębokość jest rzutem długości na oś pionową. Długość i głębokość są równe liczbowo tylko dla studni pionowych. Jednak nie pokrywają się one z odchylonymi i odchylonymi studniami.
Elementy projektu studni pokazano na ryc. 1. Sekcja początkowa I studnie nazywane są kierunek. Ponieważ głowica znajduje się w strefie łatwo erodujących skał, należy ją wzmocnić. W związku z tym kierunek jest wykonywany w następujący sposób. Najpierw wierci się dół - studnia na głębokość stabilnych skał (4 ... 8 m). Następnie instaluje się w nim rurę o wymaganej długości i średnicy, a przestrzeń między ścianami wykopu a rurą wypełnia się kamieniem gruzowym i wylewa zaprawą cementową 2.
Ryż. 1. Dobrze zaprojektuj:
Dolne sekcje odwiertu są cylindryczne. Zaraz za kierunkiem wiercony jest odcinek na głębokość od 50 do 400 m o średnicy do 900 mm. Ta część studni jest przymocowana rurą osłonową 1 (składającą się ze skręcanych rur stalowych), która nazywa się dyrygent II.
Pierścieniowa przestrzeń przewodnika jest zacementowana. Za pomocą przewodnika izoluje się niestabilne, miękkie i spękane skały, co komplikuje proces wiercenia.
Po zainstalowaniu przewodu nie zawsze jest możliwe wywiercenie odwiertu do projektowanej głębokości ze względu na przejście nowych skomplikowanych horyzontów lub ze względu na konieczność pokrycia formacji produkcyjnych, które nie są planowane do obsługi tego odwiertu. W takich przypadkach montuje się i cementuje kolejną kolumnę. III, nazywa mediator. Jeżeli formacja produkcyjna, dla której ma być wybudowana studnia, leży bardzo głęboko, to liczba kolumn pośrednich może być większa niż jedna.
Ostatnia fabuła IV naprawa studni kolumna operacyjna. Jest przeznaczony do podnoszenia ropy i gazu z dna do głowicy odwiertu lub do wstrzykiwania wody (gazu) do formacji produkcyjnej w celu utrzymania w niej ciśnienia. Aby uniknąć wycieków ropy i gazu w nad horyzontami, a woda w formacje produkcyjne, przestrzeń między ścianą obudowy produkcyjnej a ścianą studni jest wypełniona zaprawą cementową.
Do wydobycia ropy i gazu ze zbiorników stosuje się różne metody urządzeń do otwierania i odwiertów. W większości przypadków w dolnej części ciągu produkcyjnego, znajdującej się w zbiorniku, wystrzeliwuje się (przedziurawia) szereg otworów 4 w ścianie obudowy i osłonie cementowej.
W skałach stabilnych strefa dna odwiertu jest wyposażona w różne filtry i nie jest cementowana ani sznurek obudowy są one opuszczane tylko na dach formacji produkcyjnej, a jej wiercenie i eksploatacja odbywa się bez mocowania odwiertu.
Głowica w zależności od przeznaczenia wyposażona jest w armaturę (głowicę, zawory, krzyżak itp.).
Podczas poszukiwań, eksploracji i rozwoju złóż ropy i gazu wiercone są odwierty referencyjne, parametryczne, strukturalne, poszukiwawcze, poszukiwawcze, wydobywcze, zatłaczane, obserwacyjne i inne.
studnie referencyjne układane są na terenach niezbadanych wierceniem i służą do badania składu i wieku składających się na nie skał.
Studnie parametryczne układa się na stosunkowo zbadanych obszarach w celu wyjaśnienia ich budowa geologiczna oraz perspektywy potencjału naftowego i gazowego.
Studnie strukturalne są wiercone w celu zidentyfikowania obiecujących obszarów i przygotowania ich do odwiertów poszukiwawczych.
studnie poszukiwawcze wiercą w celu odkrycia nowych przemysłowych złóż ropy i gazu.
studnie poszukiwawcze są wiercone na obszarach o ustalonym komercyjnym potencjale ropy i gazu w celu zbadania wielkości i struktury złoża, uzyskania niezbędnych danych wstępnych do obliczania zasobów ropy i gazu oraz projektowania jego zagospodarowania.
Studnie produkcyjne ułożone zgodnie z planem zagospodarowania złoża i służą do pozyskiwania ropy i gazu z wnętrza ziemi
studnie wtryskowe stosuje się je, gdy na eksploatowaną formację działają różne środki (zatłaczanie wody, gazu itp.).
studnie obserwacyjne wiercą, aby kontrolować rozwój złóż (zmiany ciśnienia, położenie kontaktów woda-ropa, gaz-ropa itp.).
Ponadto w poszukiwaniu, eksploracji i rozwoju złóż ropy i gazu wiercone są odwierty mapowe, sejsmiczne, specjalne i inne.
3. Klasyfikacja metod wiercenia
Klasyfikację metod wiertniczych dla ropy i gazu przedstawiono na ryc. 2.
Zgodnie z metodą uderzenia w skały Rozróżnij wiercenie mechaniczne i niemechaniczne. W wierceniu mechanicznym narzędzie wiertnicze bezpośrednio oddziałuje na skałę, niszcząc ją, a przy wierceniu niemechanicznym zniszczenie następuje bez bezpośredniego kontaktu ze skałą ze źródła uderzenia w nią. Metody niemechaniczne(hydrauliczne, cieplne, elektrofizyczne) są w fazie rozwoju i nie są obecnie wykorzystywane do wiercenia szybów naftowych i gazowych.
Metody mechaniczne wiercenie dzieli się na udarowe i obrotowe.
Ryż. 2. Klasyfikacja metod wiercenia otworów na ropę i gaz
Podczas wiercenia udarowego niszczenie skał odbywa się za pomocą wiertła 1 zawieszonego na linie (rys. 3). Narzędzie wiertnicze zawiera również drążek uderzeniowy 2 i blokadę liny 3. Jest ono zawieszone na linie 4, która jest rzucana na klocek 5 zamontowany na maszcie (nie pokazanym konwencjonalnie). ruch posuwisto-zwrotny narzędzie do wiercenia zapewnia wiertarkę 6.
Ryż. 3. Schemat wiercenia udarowego:
1 - dłuto; 2 - pręt uderzeniowy; 3 - blokada liny;
4 - lina; 5 - blok; 6 - wiertarka.
W miarę pogłębiania się studni wydłuża się lina. Cylindryczność studni jest zapewniona przez obracanie wiertła podczas pracy.
Aby oczyścić dno ze zniszczonej skały, narzędzie wiertnicze jest okresowo usuwane ze studni i opuszczane do niego. strzał w poprzeczkę, jak długie wiadro z zaworem na dnie. Gdy doczepa jest zanurzona w mieszaninie cieczy (formacja lub wylewana z góry) i wywierconych cząstek skały, zawór otwiera się i wyciągarka zostaje napełniona tą mieszaniną. Gdy wyciągarka jest podniesiona, zawór zamyka się i mieszanina jest pobierana.
Po zakończeniu czyszczenia odwiertu narzędzie wiertnicze jest ponownie opuszczane do odwiertu i wiercenie jest kontynuowane.
Aby uniknąć zawalenia się ścian studni, obniża się do niej rurę osłonową, której długość zwiększa się w miarę pogłębiania się odwiertu.
Obecnie przy wierceniu szybów naftowych i gazowych w naszym kraju nie stosuje się wierceń udarowych.
Odwierty naftowe i gazowe budowane są przy użyciu wiercenie obrotowe. Dzięki tej metodzie skały nie są kruszone przez uderzenia, ale są niszczone przez obracający się świder, który jest poddawany obciążeniu osiowemu. Moment obrotowy przenoszony jest na świder lub z powierzchni z rotatora (rotora) poprzez przewód wiertniczy (wiercenie obrotowe) lub z silnika wiertniczego (turbodrill, wiertarka elektryczna, silnik śrubowy) zainstalowanego bezpośrednio nad wiertłem.
Jest to turbina hydrauliczna napędzana płynem wiertniczym wtryskiwanym do odwiertu. wiertarka elektryczna to silnik wodoszczelny zasilany przewodem z powierzchni. - to jest rodzaj rzezi maszyna hydrauliczna, w którym za pomocą mechanizmu śrubowego przekształca się energię przepływu płynu płuczącego w energię mechaniczną ruchu obrotowego.
Ze względu na niszczenie skał na dnie Rozróżnij wiercenie ciągłe i wiercenie rdzeniowe. Na ciągły wiercenie, niszczenie skał odbywa się na całej powierzchni twarzy. Kolinski wiercenie przewiduje niszczenie skał tylko wzdłuż pierścienia w celu wydobycia rdzeń- cylindryczna próbka skał na całej lub części długości odwiertu. Za pomocą próbkowania rdzenia badane są właściwości, skład i struktura skał, a także skład i właściwości płynu nasycającego skałę.
Wszystko wiertła wiertnicze dzieli się na trzy typy:
- kawałki tnące i ścinające, niszczące skałę ostrzami (wiórami ostrzy);
- kawałki o działaniu miażdżącym i ścinającym, niszczącym skałę zębami umieszczonymi na stożkach (stożkach);
- wiertła o działaniu tnąco-ściernym, niszczące skałę ziarnami diamentu lub szpilkami ze stopów twardych, które znajdują się w końcowej części świdra (bity diamentowe i ze stopów twardych).
4. Wiertnice, sprzęt i narzędzia
Wiercenie studni odbywa się za pomocą wiertnic, sprzętu i narzędzi.
Sprzęt wiertniczy
Jak silniki wgłębne podczas wiercenia używa się turbowiertarki, wiertarki elektrycznej i silnika śrubowego, instalowanych bezpośrednio nad wiertłem.
(rys. 15) to turbina wielostopniowa (do 350 stopni), której każdy stopień składa się ze stojana sztywno połączonego z korpusem turbowiertarki i wirnika zamontowanego na wale turbowiertarki. Strumień płynu, spływający z łopatek stojana, spływa na łopatki wirnika, oddając część swojej energii na wytworzenie momentu obrotowego, ponownie spływa na łopatki stojana itp. Chociaż każdy etap turbowiertarki rozwija się stosunkowo mała chwila, ze względu na ich dużą liczbę, całkowita moc na wale turbowiertarki jest wystarczająca do wiercenia najtwardszej skały.
Ryż. 15. Turbowiertarka:
a - widok ogólny; b - stopień turbowiertarki; 1 - wał; 2 - ciało; 3 - wirnik; 4 - stojan.
Na wiercenie turbiny jako płyn roboczy stosuje się płyn płuczący, przemieszczający się z powierzchni ziemi wzdłuż przewodu wiertniczego do turbowiertarki. Końcówka jest sztywno połączona z wałem turbowiertarki. Obraca się niezależnie od przewodu wiertniczego.
Podczas wiercenia za pomocą wiertarki elektrycznej silnik elektryczny zasilany jest kablem zamocowanym wewnątrz rur wiertniczych. W tym przypadku wraz z wiertłem obraca się tylko wał silnika, podczas gdy jego korpus i przewód wiertniczy pozostają nieruchome.
Główne elementy silnik śrubowy(rys. 16) to stojan i wirnik. Stojan wykonany jest poprzez nałożenie specjalnej gumy na wewnętrzną powierzchnię stalowej obudowy. Wewnętrzna powierzchnia stojana ma postać wielozwojowej powierzchni śrubowej. A wirnik jest wykonany ze stali w postaci śruby wielostartowej. Liczba linii śrubowych jest o jeden mniejsza niż stojana.
Ryż. 16. Silnik śrubowy:
a - widok ogólny; b - wnęki utworzone między wirnikiem (śrubą) a stojanem;
1 - podrzędny; 2 - korpus sekcji silnika; 3 - stojan; 4 - wirnik;
5 - wał kardana; 6 - obudowa wrzeciona; 7 - uszczelka końcowa;
8 - wielorzędowe łożysko skośne; 9 - guma radialna
metalowa podpora; 10 - wał wrzeciona.
Wirnik znajduje się w stojanie z mimośrodem. Z tego powodu, a także z powodu różnicy w ilości wejść w linie śrubowe stojana i wirnika, ich powierzchnie styku tworzą szereg zamkniętych wnęk - przepustów między komorami wysokiego ciśnienia na górnym końcu wirnika i niskiego ciśnienia na dolnym końcu. Śluzy blokują swobodny przepływ płynu przez silnik, a co najważniejsze, to w nich ciśnienie płynu wytwarza moment obrotowy przenoszony na wędzidło.
narzędzie do wiercenia
Narzędzie, stosowany w wierceniu, dzieli się na podstawowy(bity) i pomocniczy(rury wiertnicze, złącza narzędziowe, centralizatory):
Dłuta
/Podstawowe narzędzie do wiercenia/
Dłuta są ostrza, stożek, diament i węglik.
Bity ostrzy(rys. 17) są dostępne w trzech rodzajach: dwułopatkowe, trzyłopatkowe i wielołopatkowe. Pod wpływem obciążenia na dno ich ostrza wbijają się w skałę i pod wpływem momentu obrotowego kruszą ją. W korpusie świdra znajdują się otwory, przez które płyn z przewodu wiertniczego kierowany jest na dno odwiertu z prędkością co najmniej 80 m/s. Wiertła ostrzowe są używane podczas wiercenia w miękkich, wysoce plastycznych skałach z ograniczonymi prędkościami obwodowymi (zwykle podczas wiercenia obrotowego).
Ryż. 17. Dłuto wiosłowe:
1 - głowica z gwintem łączącym; 2 - ciało; 3 - ostrze;
4 - otwór do płukania; 5 - powłoka ze stopu twardego;
6 - krawędź tnąca.
Wiertła rolkowe(rys. 18) są dostępne z jednym, dwoma, trzema, czterema, a nawet sześcioma nożami. Jednak najczęściej używane bity tricone. Gdy wiertło się obraca, noże, tocząc się po dnie, wykonują złożony ruch obrotowy z przesuwaniem. Jednocześnie zęby frezów uderzają w skałę, miażdżą ją i kruszą. Wiertła rolkowe są z powodzeniem stosowane w obrotowym wierceniu skał o szerokiej gamie właściwości fizycznych i mechanicznych. Wykonane są z wysokiej jakości stali z późniejszą obróbką chemiczno-termiczną najbardziej krytycznych i zużywających się części, a same zęby wykonane są z twardego stopu.
Ryż. 18. Wiertło stożkowe:
1 - korpus z gwintowaną główką;
2 - łapa ze wsparciem; 3 - stożek.
bity diamentowe(rys. 19) składają się ze stalowego korpusu i głowicy nośnej diamentu wykonanej ze sproszkowanego wsadu węglikowego. Środkowa część świdra to powierzchnia wklęsła w kształcie stożka z kanałami na płyn spłukujący, a strefa peryferyjna to powierzchnia kulista, przechodząca po bokach w cylindryczną.
Ryż. 19. Dłuto diamentowe:
1 - ciało; 2 - macierz; 3 - ziarna diamentu.
Istnieją trzy rodzaje bitów diamentowych: spiralne, promieniowe i schodkowe. W spiralnym diamentie bity, część robocza posiada spirale wyposażone w diamenty i otwory do płukania. Wiertła tego typu przeznaczone są do wiercenia turbinowego w skałach mało i średnio ściernych. Diament promieniowy bity mają powierzchnię roboczą w postaci promieniowych występów w postaci sektora, wyposażonego w diamenty; pomiędzy nimi umieszczone są kanały spłukujące. Wiertła tego typu przeznaczone są do wiercenia w skałach mało ściernych o średniej twardości oraz skałach twardych zarówno metodą wiercenia obrotowego jak i turbinowego. Stopniowany diament bity mają powierzchnię roboczą o schodkowym kształcie. Stosowane są zarówno do wiercenia obrotowego, jak i turbinowego podczas wbijania skał miękkich i średnio twardych o niskiej ścieralności.
Zastosowanie wierteł diamentowych zapewnia duże prędkości wiercenia, zmniejszając krzywiznę odwiertów. Brak łożysk tocznych i wysoka odporność diamentów na zużycie zwiększają ich żywotność do 200...250 godzin ciągłej pracy. Zmniejsza to liczbę podróży. Jeden wiertło diamentowe może wywiercić aż 15...20 wierteł stożkowych.
Dłuta z węglików spiekanych różnią się od diamentowych tym, że zamiast diamentów są wzmocnione supertwardymi stopami.
Rury wiertnicze, zamki, centralizatory itp.
/Pomocnicze narzędzie do wiercenia/
Wiercenie rury są zaprojektowane tak, aby przenosić obrót na świder (podczas wiercenia obrotowego) i odbierać moment reakcji silnika podczas wiercenia silnikami wiertniczymi, tworząc obciążenie wiertła, podawanie płuczka wiertnicza na dno studni, aby oczyścić ją z wierconej skały i schłodzić wiertło, wyjąć zużytą wiertło ze studni i opuścić nową itp.
Rury wiertnicze charakteryzują się zwiększoną grubością ścianki i z reguły mają gwinty stożkowe po obu stronach. Rury są połączone za pomocą zamków wiertniczych (ryc. 20). Dla trwałości połączenia gwintowane końce rur są pogrubione. Zgodnie z metodą produkcji rury mogą być lite (ryc. 21) i ze spawanymi końcówkami łączącymi (ryc. 22). W przypadku rur litych pogrubienie końców może być zapewnione przez spęczenie do wewnątrz lub na zewnątrz.
Ryż. 20. Blokada wiertła:
a - smoczek blokujący; b - sprzęgło blokujące
Ryż. 21. Rury wiertnicze ze spawanymi końcówkami łączącymi
Ryż. 22. Rury wiertnicze ze spękanymi końcami:
a - lądowanie w środku; b - lądowanie na zewnątrz.
Do głębokiego wiercenia stosuje się rury wiertnicze stalowe i ze stopów lekkich o średnicach nominalnych 60, 73, 89,102,114,127 i 140 mm. Grubość ścianek rur wynosi od 7 do 11 mm, a ich długość to 6, 8 i 11,5 m.
Wraz ze zwykłym użyciem kołnierze wiertnicze(UBT). Ich celem jest stworzenie ciężaru na świdrach i zwiększenie stabilności dolnej części przewodu wiertniczego.
Ołowiana rura przeznaczony do przenoszenia obrotu z wirnika na przewód wiertniczy (wiercenie obrotowe) oraz do przenoszenia momentu reaktywnego z przewodu wiertniczego na wirnik (przy wierceniu silnikiem wiertniczym). Ta rura ma zwykle przekrój kwadratowy i przechodzi przez kwadratowy otwór w wirniku. Z jednej strony Kelly jest podłączony do krętlika, a z drugiej do konwencjonalnej okrągłej rury wiertniczej.
Długość powierzchni Kelly określa możliwy interwał wiercenia studni bez przedłużenia narzędzia. Przy małej długości rury prowadzącej zwiększa się liczba przedłużeń i czas poświęcony na wiercenie studni, a przy dużej długości ich transport staje się trudniejszy.
Zamki wiertnicze przeznaczony do łączenia rur. Zamek składa się z nypla zamka (rys. 20 a) i tulei zamka (rys. 20 b).
Nazywany jest ciągły wielowahaczowy system narzędzi i sprzętu znajdującego się poniżej krętlika (kelly, rury wiertnicze z blokadami, silnik wiertniczy i bit) przewód wiertniczy. Jego elementami pomocniczymi są okręty podwodne o różnym przeznaczeniu, ochraniacze, centralizatory, stabilizatory, kalibratory, amortyzatory zbliżeniowe.
Subs służą do łączenia elementów w przewodzie wiertniczym z gwintami o różnych profilach, z takimi samymi końcówkami gwintowanymi (gwint nyplowo-nyplowy, gwint sprzęgłowo-sprzęgłowy), do podłączenia silnika wiertniczego itp. Zgodnie z ich przeznaczeniem, subwoofery dzielą się na przejściowe, sprzęgające i nyplowe.
ochraniacze przeznaczony do ochrony rur wiertniczych i zamków złączy przed zużyciem powierzchni oraz sznurek obudowy- przed wycieraniem podczas przenoszenia w nim rur wiertniczych. Zazwyczaj stosuje się ciasne ochraniacze, które są gumowym pierścieniem noszonym na przewodzie wiertniczym nad zamkiem. Zewnętrzna średnica ochraniacza przekracza średnicę zamka.
Centralizatorzy służy do zapobiegania skrzywieniu pnia podczas wiercenia studni. Boczne elementy centralizatora dotykają ścian studni, zapewniając wyrównanie z nią przewodu wiertniczego. Centralizatory znajdują się w ciągu rur wiertniczych w miejscach spodziewanego zakrętu. Obecność centralizatorów pozwala na zastosowanie wyższych obciążeń osiowych na wiertle.
Stabilizatory- są to elementy centrujące podporę w celu utrzymania sztywnego ustawienia przewodu wiertniczego w otworze wiertniczym na niektórych najbardziej krytycznych odcinkach. Różnią się od centralizatorów większą długością.
Kalibrator- rodzaj narzędzia do cięcia skały do obróbki ścian studni i utrzymania nominalnej średnicy jego trzonu w przypadku zużycia wiertła. W przewodzie wiertniczym kalibrator jest umieszczony bezpośrednio nad wiertłem. Działa jednocześnie jako centralizator i poprawia warunki pracy wędzidła.
Amortyzator bitowy(tłumik wiertniczy) jest instalowany w przewodzie wiertniczym między świdrem a kołnierzami wiertniczymi w celu tłumienia wibracji o wysokiej częstotliwości, które występują, gdy świder pracuje na dnie odwiertu. Zmniejszenie obciążeń wibracyjnych prowadzi do wydłużenia żywotności przewodu wiertniczego i wiertła. Istnieją dwa rodzaje urządzeń tłumiących: amortyzatory o działaniu mechanicznym, zawierające elementy sprężyste (stalowe sprężyny, gumowe pierścienie i kulki) oraz amortyzatory drgań o działaniu hydraulicznym lub hydromechanicznym.
Przykład układu sznurka wiertniczego
Przykładowy układ przewodu wiertniczego pokazano na ryc. 23.
Ryż. 23. Układ sznurka wiertniczego:
1 - obrotowy bagażnik; 2 - lewy ośmiowątkowy wątek; 3 - obrotowy sub; 4 - lewy wątek blokujący; 5 - sub górny pręt (PShV); 6 - prowadząca rura; 7 - prawy ośmiowątkowy wątek; 8 - sub dolny pręt (PShN); 9 - prawy wątek blokujący; 10 - podrzędny bezpieczeństwa (PBP); 11 - wątek zamka; 12 - sprzęgło blokujące; 13 - ośmiopunktowy gwint; 14 - rura wiertnicza o długości 6 m; 15 - sprzęgło; 16 - smoczek blokujący; 17 - pierścień bezpieczeństwa; 18 - rury wiertnicze wagowe (DC); 19 - sub dwugniazdowy (PBM); 20 - centralizator; 21 - adapter podrzędny; 22 - prawie bitowy kołnierz wiertła; 23 - dłuto
5. Cykl budowy studni
Cykl budowy studni obejmuje:
- Praca przygotowawcza;
- montaż wieży i wyposażenia;
- przygotowanie do wiercenia;
- proces wiercenia;
- mocowanie studni rurami osłonowymi i jej fugowanie;
- otwarcie formacji i testowanie dopływu ropy i gazu.
W trakcie Praca przygotowawcza wybierają miejsce na wiertnicę, układają drogę dojazdową, wyłączają systemy zasilania, wodociągów i łączności. Jeśli teren jest nierówny, planowana jest strona.
Montaż wieży i urządzeń jest produkowany zgodnie z przyjętym dla tych szczególnych warunków schematem ich rozmieszczenia. Starają się rozmieścić sprzęt w taki sposób, aby zapewnić bezpieczeństwo w eksploatacji, łatwość konserwacji, niski koszt budowy oraz Roboty instalacyjne i zwartość w rozmieszczeniu wszystkich elementów wiertnicy.
W ogólnym przypadku (ryc. 24) pośrodku wiertnicy 1 znajduje się wirnik 3, a obok niego wciągarka 2. i mieszalnik gliny 17. Po przeciwnej stronie wciągarki znajduje się stojak na małe narzędzia 14, stojaki 5 do układania rur wiertniczych 4, pomosty odbiorcze 12, platforma na zużyte bity 7 i platforma narzędzi rybackich 10 (służy do eliminacji wypadków). Ponadto wokół wiertnicy znajduje się kabina 8, platforma narzędziowa 6, system czyszczenia 15 na zużytą płuczkę wiertniczą oraz zapasowe pojemniki 16 do przechowywania płuczki wiertniczej, chemikaliów i wody.
Ryż. 24. Typowy układ wyposażenia,
narzędzia, części zamienne i materiały na wiertnicy:
1 - wiertnica; 2 - wciągarka; 3 - wirnik; 4 - rury wiertnicze;
5 - stojaki; 6 - platforma narzędziowa; 7 - miejsce zużytych
bity; 8 - budka narzędziowa; 9 - teren gospodarstwa glinianego; 10 - plac zabaw
narzędzie wędkarskie; 11 - platforma na paliwa i smary;
12 - odbieranie chodników; 13 - stół ślusarski; 14 - lekki stojak na narzędzia;
15 - system czyszczenia; 16 - zapasowe pojemniki; 17 - mieszalnik gliny;
18 - napęd mocy; 19 - pompy
Istnieją następujące metody montażu wiertnic: jednostka po jednostce, mały blok i duży blok.
W metodzie jednostkowej wiertnica składana jest z oddzielnych jednostek, do dostawy których wykorzystywany jest transport drogowy, kolejowy lub lotniczy.
W metodzie małych bloków wiertnica składa się z 16...20 małych bloków. Każdy z nich to podstawa, na której montowana jest jedna lub więcej jednostek instalacji.
W metodzie wielkoblokowej instalacja składa się z 2...4 bloków, z których każdy łączy kilka jednostek i jednostek wiertnicy.
Metody blokowe zapewniają wysokie wskaźniki instalacji platform wiertniczych i jakość prac instalacyjnych. Wymiary bloków zależą od metody, warunków i odległości ich transportu.
Następnie blok jezdny z blokiem koronowym, krętlik i prowadząca rura są kolejno montowane, a wąż ciśnieniowy jest przymocowany do krętlika. Następnie sprawdzane jest centrowanie wieży: jej środek musi pokrywać się ze środkiem wirnika.
Przygotowanie do wiercenia obejmuje urządzenie kierunkowe I (rys. 1) oraz próbny ruch wiertnicy.
Ryż. 1. Dobrze zaprojektuj:
1 - rury osłonowe; 2 - kamień cementowy; 3 - warstwa;
4 - perforacja w obudowie z kamienia cementowego;
ja - kierunek; II - dyrygent; III - kolumna pośrednia;
IV - ciąg produkcyjny.
Cel kierunku został opisany powyżej. Jej górny koniec połączony jest z układem oczyszczania przeznaczonym do usuwania zwiercin z płuczki wiertniczej pochodzącej z odwiertu, a następnie doprowadzania jej do zbiorników odbiorczych pomp płuczkowych.
Następnie wiercony jest otwór na rurę prowadzącą i opuszczane są do niego rury osłonowe.
Wiertnica wyposażona jest w wiertła, rury wiertnicze, narzędzia ręczne i pomocnicze, paliwa i smary, zapas wody, gliny i chemikaliów. Ponadto niedaleko od platformy znajduje się pomieszczenie do odpoczynku i jedzenia, suszarka do kombinezonów oraz pomieszczenie do analizy płuczki wiertniczej.
Podczas próbnych odwiertów sprawdzana jest sprawność wszystkich elementów i podzespołów wiertnicy.
Proces wiercenia zacznij od wstępnego przykręcenia dłuta do prowadzącej kwadratowej rury. Obracając wirnik, obrót przenoszony jest na świder przez prowadzącą rurę.
Podczas wiercenia występuje ciągłe opadanie (dostawa) narzędzie do wiercenia tak, że część ciężaru jego dolnej części jest przenoszona na wędzidło, aby zapewnić skuteczne niszczenie skały.
Podczas wiercenia studnia jest stopniowo pogłębiana. Po tym, jak kelly wejdzie do studni, konieczne jest zbudowanie ciągu rury wiertniczej. Rozszerzenie odbywa się w następujący sposób. Najpierw zatrzymaj mycie. Następnie narzędzie wiertnicze jest wyciągane z odwiertu, dzięki czemu Kelly jest całkowicie wyjęty z wirnika. Za pomocą pneumatycznego uchwytu klinowego narzędzie zawiesza się na wirniku. Następnie rura prowadząca jest odkręcana od przewodu wiertniczego i wraz z krętlikiem opuszczana do wykopu - lekko pochylona studnia o głębokości 15 ... 16 m, znajdująca się w rogu wiertnicy. Następnie hak odłącza się od krętlika, na haku zawiesza się kolejną przygotowaną rurę, łączy się ją z przewodem wiertniczym zawieszonym na wirniku, przewód wyjmuje się z wirnika, opuszcza do studni i zawiesza ponownie na wirnik. Hak podnoszący jest ponownie połączony z krętlikiem i podnoszony z prowadzącą rurą z otworu. Kelly jest podłączony do przewodu wiertniczego, ten ostatni jest usuwany z wirnika, pompa błotna jest włączana, a wiertło jest ostrożnie sprowadzane na dno. Następnie wiercenie trwa.
Podczas wiercenia wiertło stopniowo się zużywa i konieczna jest jego wymiana. W tym celu narzędzie wiertnicze, podobnie jak w przypadku przedłużenia, podnosi się na wysokość równą długości kelly, zawiesza się na wirniku, kelly odłącza się od sznurka i opuszcza za pomocą krętlika do dołu. Następnie sznur wiertniczy unosi się na wysokość równą długości stojaka wiertniczego, sznurek zawiesza się na wirniku, stojak odłącza się od sznurka, a jego dolny koniec montuje się na specjalnej platformie – świeczniku, a górny Koniec umieszczany jest na specjalnym wsporniku zwanym palcem. W tej kolejności wszystkie świece są podnoszone ze studni. Następnie wiertło jest wymieniane i rozpoczyna się opuszczanie narzędzia wiertniczego. Proces ten odbywa się w odwrotnej kolejności do podnoszenia narzędzia wiertniczego ze studni.
Mocowanie studni rurami osłonowymi i jej fugowanie przeprowadzone zgodnie ze schematem pokazanym na ryc. 1. Celem zaślepiania pierścienia strun osłonowych jest izolacja formacji wytwórczych.
Chociaż formacje produkcyjne były już odsłonięte w trakcie wiercenia, odizolowano je rurami osłonowymi i zatkaniem, aby penetracja ropy i gazu do odwiertu nie przeszkadzała w dalszym wierceniu. Po zakończeniu wiercenia w celu zapewnienia przepływu oleju i warstwy gazotwórcze są ponownie otwierane metoda perforacji. Odtąd studnia jest rozwijana tych. spowodować napływ do niego ropy i gazu. Po co zmniejszać ciśnienie płynu wiertniczego na dnie na jeden z następujących sposobów:
- spłukiwanie- wymianę płynu wiertniczego wypełniającego odwiert po wykonaniu wiercenia lżejszą cieczą - wodą lub olejem;
- tłok(swabing) – obniżenie poziomu płynu w studni poprzez opuszczenie do wężyka i podniesienie specjalnego tłoka (wymazówki) na stalowej kablu. Tłok posiada zawór, który otwiera się podczas opadania i umożliwia napełnienie przez niego rurki płynem. Podczas podnoszenia zawór zamyka się, a cała kolumna cieczy nad tłokiem jest wynoszona na powierzchnię.
Ze względów bezpieczeństwa zrezygnowano z dotychczas stosowanych metod obniżania ciśnienia płuczki wiertniczej na dnie, przepychania sprężonym gazem i napowietrzania (nasycania roztworu gazem).
Tak więc zagospodarowanie studni, w zależności od konkretnych warunków, może trwać od kilku godzin do kilku miesięcy.
Po pojawieniu się ropy i gazu odwiert jest akceptowany przez operatorów, a żuraw jest przesuwany o kilka metrów w celu wykonania kolejnego odwiertu na platformie lub przeciągany na kolejny pad.
6. Mycie studni
Płukanie studni jest jedną z najbardziej krytycznych operacji wykonywanych podczas wiercenia. Początkowo płukanie ograniczało się do oczyszczenia otworu dennego z cząstek zrzezów i ich usunięcia ze studni oraz schłodzenia wędzidła. Jednak wraz z rozwojem branży wiertniczej rozszerzyły się funkcje płuczki wiertniczej. Teraz obejmuje to:
- usuwanie cząstek sadzonek ze studni;
- przeniesienie mocy do turbowiertarki lub silnika śrubowego;
- zapobieganie przedostawaniu się ropy, gazu i wody do studni;
- utrzymywanie cząstek wierconej skały w zawiesinie po zatrzymaniu cyrkulacji;
- chłodzenie i smarowanie części trących wierteł;
- zmniejszenie tarcia rur wiertniczych o ściany studni;
- zapobieganie zawaleniom skał ze ścian studni;
- zmniejszenie przepuszczalności ścian studni z powodu zaskorupiania.
W związku z tym płuczki wiertnicze muszą spełniać szereg wymagań:
- wykonywać przypisane funkcje;
- nie mają szkodliwego wpływu na narzędzie wiertnicze i silniki wgłębne (korozja, zużycie ścierne itp.);
- łatwe do pompowania i czyszczenia z szlamu i gazu;
- być bezpiecznym dla personelu serwisowego i środowiska;
- być wygodnym do przygotowania i czyszczenia;
- być dostępne, niedrogie i wielokrotnego użytku.
- Oczyszczanie płuczek wiertniczych
Rodzaje płuczek wiertniczych
Rodzaje płuczek wiertniczych
W wierceniu obrotowym szybów naftowych i gazowych jako płyny płuczące stosuje się następujące płyny:
środki na bazie wody (woda procesowa, naturalne płuczki wiertnicze, błota gliniaste i niegliniaste);
środki na bazie węglowodorów;
środki emulgujące;
środki gazowe i gazowane.
woda techniczna- najbardziej dostępny i tani płyn do płukania. Dzięki niskiej lepkości jest łatwo pompowalny, dobrze usuwa sadzonki z dna studni i chłodzi nieco lepiej niż inne płyny. Jednak słabo zatrzymuje cząstki zrębków (zwłaszcza przy zatrzymaniu cyrkulacji), nie tworzy twardniejącej skorupy na ścianie studni, jest dobrze wchłaniana przez formacje niskociśnieniowe, powoduje pęcznienie skał ilastych i pogarsza przepuszczalność złóż ropy i gazu .
naturalne płuczki wiertnicze nazywana zawiesiną wodną powstałą w studni w wyniku dyspersji zwiercin skalnych wierconych na wodzie.
Główną zaletą stosowania naturalnych płuczek wiertniczych jest znaczne zmniejszenie zapotrzebowania na importowane materiały do ich przygotowania i obróbki, co prowadzi do tańszych rozwiązań. Jednak ich jakość i właściwości zależą od składu mineralogicznego i charakteru wierconych iłów, metody i trybu wiercenia oraz rodzaju narzędzia do cięcia skał. Często zawierają dużą zawartość cząstek ściernych. Dlatego też naturalne płuczki wiertnicze są stosowane w przypadkach, gdy warunki geologiczne i stratygraficzne nie wymagają wysokiej jakości płuczki wiertniczej.
Płyny wiertnicze do gliny najczęściej stosowany w wierceniu studni. W przypadku wiercenia największe zainteresowanie wzbudzają trzy grupy minerałów ilastych: bentonit (montmorylonit, beidellit, nontroit, saponit itp.), kaolin (kaolinit, haloizyt, nakryt itp.) oraz hydromicace (illit, braviasyt itp.). Montmorylonit i inne minerały bentonitowe mają najlepsze właściwości pod względem przygotowania płuczki wiertniczej. Tak więc z 1 tony gliny bentonitowej można uzyskać około 15 m 3 wysokiej jakości roztworu gliny, natomiast z gliny średniej jakości - 4 ... 8 m 3, a z glin niskogatunkowych - mniej niż 3 m 3 .
Roztwory gliny gliniają ściany studni, tworząc cienką gęstą skorupę, która zapobiega przenikaniu filtratu do formacji. Ich gęstość i lepkość są takie, że płuczki utrzymują zwierciny nawet w spoczynku, zapobiegając ich osiadaniu na dnie podczas przerw w płukaniu. Obciążone roztwory gliny, tworząc duże ciśnienie wsteczne na formacjach, zapobiegają wnikaniu wód złożowych, ropy i gazu do odwiertu oraz otwartemu przepływowi podczas wiercenia. Jednak z tych samych powodów trudno jest oddzielić cząstki skały w układzie obiegu płuczki wiertniczej.
Wykorzystywane są również inne płuczki wiertnicze na bazie wody: niskogliniaste (do wiercenia górnych warstw zwietrzałych i spękanych skał), solankowe (przy wierceniu w grubych warstwach skał solnonośnych), zahamowane (poddane działaniu środków chemicznych, aby zapobiec pęcznieniu wierconych skały i nadmierne wzbogacenie roztworu w fazę stałą) itp.
Do bez gliny obejmują płuczki wiertnicze przygotowane bez użycia gliny. Bezglinowy płyn wiertniczy do skondensowanych ciał stałych przygotowany na bazie wody. Fazę rozproszoną w nim uzyskuje się chemicznie, w wyniku oddziaływania jonów magnezu w roztworze z alkalicznym NaOH lub Ca (OH) 2. Reakcja chemiczna prowadzi do powstania mikroskopijnych cząstek wodorotlenku magnezu Mg(OH) 2 w roztworze. Roztwór nabiera żelowej konsystencji, a po obróbce chemicznej zamienia się w układ stabilny sedymentacji. Takie rozwiązanie zachowuje swoje właściwości strukturalne i mechaniczne przy każdej mineralizacji. Dlatego jest stosowany w przypadkach, gdy wymagane jest zapewnienie wysokiej stabilności ścian studni, ale trudno jest kontrolować i regulować zasolenie roztworu.
Innym rodzajem nieglinianych płuczek wiertniczych są: roztwory biopolimerowe. Biopolimery otrzymuje się poprzez ekspozycję niektórych szczepów bakterii na polisacharydy. Właściwości płuczek biopolimerowych są tak łatwe do kontrolowania, jak najlepszych płuczek bentonitowych. Jednak niektóre z nich działają flokulująco na sadzonki, zapobiegając w ten sposób tworzeniu się zawiesiny. Ponadto roztwory biopolimerowe są stabilne termicznie. Ich stosowanie jest utrudnione ze względu na ich stosunkowo wysoki koszt.
Płyny wiertnicze na bazie oleju są układami wieloskładnikowymi, w których medium dyspersyjnym (nośnikowym) jest olej lub płynne produkty ropopochodne (zwykle olej napędowy), a fazą rozproszoną (zawieszoną) jest utleniony bitum, asfalt lub specjalnie przetworzona glina (hydrofobizowany bentonit).
Płyny wiertnicze na bazie ropy naftowej nie wpływają niekorzystnie na właściwości zbiorników ropy i gazu, mają właściwości smarne: podczas ich stosowania zmniejsza się pobór mocy na jałowy obrót przewodu wiertniczego w odwiercie oraz zużycie rur wiertniczych i wierteł. zredukowany. Jednak koszt przygotowania takich płuczek wiertniczych jest dość wysoki, są one łatwopalne i trudne do usunięcia z narzędzi i sprzętu.
Płuczki wiertnicze na bazie ropy naftowej służą do zwiększenia efektywności wiercenia w skałach zbiornikowych i utrzymania ich wydobycia ropy i gazu na początkowym poziomie, a także do wiercenia studni w trudnych warunkach przy wierceniu grubych okładów iłów pęczniejących i soli rozpuszczalnych.
Na emulsyjne płuczki wiertnicze ośrodek dyspersyjny jest emulsją typu woda w oleju, a fazą rozproszoną jest glina. Płuczka wiertnicza przygotowana na bazie emulsji woda w oleju nazywana jest emulsją odwróconą lub emulsją odwróconą. Faza ciekła takiego roztworu składa się z 60 ... 70% oleju lub produktów naftowych, reszta to woda. Jednak zawartość wody w emulsji inwertowanej można zwiększyć do 80% lub więcej, jeśli zostaną do niej wprowadzone specjalne emulgatory.
Wiertła emulsyjne są używane podczas wiercenia w złożach gliny i warstwach soli. Posiadają dobre właściwości smarne i zapobiegają zakleszczaniu się narzędzia w zagłębieniu.
Istota wiercenie gazowe polega na tym, że do czyszczenia dna, usuwania sadzonek na powierzchnię, a także do chłodzenia wędzidła, skompresowane powietrze, gaz ziemny lub spaliny z silników spalinowych. Zastosowanie środków gazowych pozwala na uzyskanie świetnego efektu ekonomicznego: zwiększa się prędkość mechaniczna (od 10 do 12 razy) i penetracja na bit (od 10 razy). Ze względu na duże prędkości przepływu w górę w pierścieniu, usuwanie przewierconych cząstek skalnych jest przyspieszone. Zastosowanie czynników gazowych ułatwia prowadzenie obserwacji hydrogeologicznych w otworach wiertniczych. Ponadto wzrasta współczynnik odzysku ropy i gazu z formacji.
Napowietrzane płuczki wiertnicze to mieszaniny pęcherzyków powietrza z płynami płuczącymi (woda, emulsje olejowe itp.) w stosunku do 30:1. Aby zwiększyć stabilność napowietrzonych roztworów, do ich składu wprowadza się odczynniki - środki powierzchniowo czynne i środki pieniące.
Napowietrzone płuczki wiertnicze mają takie same właściwości jak płyny, z których są przygotowywane (dla płynów ilastych - tworzą ciasto gliniaste, mają lepkość i naprężenia ścinające, a po otwarciu zachowują naturalną przepuszczalność strefy formowania dennego). Jednocześnie dużą zaletą płynów napowietrzonych jest możliwość ich zastosowania w trudnych warunkach wiertniczych, z katastrofalnymi stratami płynów wiertniczych i otwieraniem utworów produkcyjnych przy niskim ciśnieniu.
Podstawowe parametry płynów wiertniczych
Główne parametry płynów wiertniczych to gęstość, lepkość, wskaźnik filtracji, statyczne naprężenie ścinające, stabilność, dobowy osad, zawartość piasku, pH.
Gęstość płyny płuczące mogą być różne: dla płuczek olejowych wynosi 890...980 kg/m3, dla płuczek niskogliniastych - 1050...1060 kg/m3, dla płuczek obciążonych - do 2200 kg/m3 i więcej.
Dobór płuczki powinien zapewnić, że ciśnienie hydrostatyczne kolumny w studni o głębokości do 1200 m przewyższa ciśnienie złożowe o 10...15%, a dla studni głębszych niż 1200 m - o 5...10 %.
Lepkość charakteryzuje właściwość rozwiązania polegającą na przeciwstawianiu się jego ruchowi.
Szybkość filtracji- zdolność roztworu w określonych warunkach do nadawania wody porowatym skałom. Im więcej wolnej wody w roztworze i mniej cząstek gliny, tym więcej wody wnika do formacji.
Statyczne naprężenie ścinające charakteryzuje siłę, która jest wymagana do zastosowania, aby wyprowadzić rozwiązanie z równowagi.
Stabilność charakteryzuje zdolność roztworu do zatrzymywania cząstek w zawiesinie. Wyznacza się ją różnicą gęstości między dolną i górną połową objętości jednej próbki po odstawieniu przez 24 h. Dla zwykłych roztworów jej wartość nie powinna przekraczać 0,02 g/cm3, a dla roztworów odważonych 0,06 g/ cm3.
Dzienny osad- ilość wody uwalnianej dziennie z roztworu podczas jego nieruchomego przechowywania. W przypadku wysoce stabilnych roztworów wartość dobowego osadu powinna być równa zeru.
Wartość pH pH charakteryzuje alkaliczność płynu wiertniczego. Przy pH > 7 roztwór jest zasadowy, przy pH = 7 obojętny, przy pH< 7 - кислый.
Obróbka chemiczna płuczek wiertniczych
Obróbka chemiczna płuczki wiertniczej polega na wprowadzeniu do niej określonych środków chemicznych w celu polepszenia jej właściwości bez znaczącej zmiany gęstości.
W wyniku obróbki chemicznej uzyskuje się następujące pozytywne wyniki:
- poprawa stabilności płynu wiertniczego;
- zmniejszenie jego zdolności do filtrowania, zmniejszenie grubości i lepkości placka na ściance odwiertu;
- regulacja lepkości roztworu w kierunku jego wzrostu lub spadku;
- nadając mu specjalne właściwości (odporność na ciepło, odporność na sól itp.).
Dodatki smarne i odpieniacze są również wprowadzane do glinianych płuczek wiertniczych. Dzięki dodatkom smarującym poprawiają się warunki pracy przewodu wiertniczego i narzędzia do cięcia skał w odwiercie. Odpieniacze zapobiegają tworzeniu się piany, gdy faza gazowa jest uwalniana z płynu myjącego.
Przygotowanie płynu wiertniczego
Przygotowanie płuczki wiertniczej to przygotowanie płuczki wiertniczej o wymaganych właściwościach w wyniku obróbki surowców i współdziałania składników.
Organizacja pracy i technologia przygotowania płynu wiertniczego zależą od jego receptury, stanu surowców i wyposażenia technicznego. Rozważ je na przykładzie przygotowania roztworu gliny.
Takie rozwiązanie jest przygotowywane albo centralnie w fabryce gliny, albo bezpośrednio na platformie wiertniczej. Scentralizowane zaopatrzenie w płyn wiertniczy wskazane jest przy długotrwałym wierceniu dużych pól i bliskiej lokalizacji urządzeń wiertniczych, gdy do odwiertów potrzebne są płuczki wiertnicze o takich samych lub zbliżonych parametrach. W tym przypadku pełniej i ekonomiczniej wykorzystywane materiały źródłowe, wymagane są mniejsze koszty energii w porównaniu do przygotowania płuczki na platformach wiertniczych, koszt płuczki jest niższy, personel wiertniczy jest zwolniony z ciężkiej i czasochłonnej pracy.
Najbardziej ekonomicznie scentralizowane przygotowanie płuczki metodą jet jet bezpośrednio w wyrobisku gliny, zlokalizowane w pobliżu dużej grupy urządzeń wiertniczych. Jeśli nie ma takich warunków, to glinniarz znajduje się w centrum wierconego terenu, a glinę w kawałkach dostarcza się z kamieniołomu transportem drogowym, kolejowym lub wodnym. W zakładach glinianych w mieszarkach hydraulicznych o objętości 20 ... 60 m 3 przygotowuje się 400 ... 1000 m 3 roztworu gliny dziennie. Dostarczana jest na platformy wiertnicze rurociągami, autocysternami lub na specjalnych statkach.
Przy dużym rozproszeniu wiertnic, trudności w dostarczeniu do nich gotowego rozwiązania (teren bagienny lub nierówny, warunki zimowe itp.), potrzebie rozwiązań o różnych parametrach, wskazane jest przygotowanie roztworów glinianych bezpośrednio na platformie. W tym celu wiertnie są obecnie wyposażone w agregat do przygotowania płuczki wiertniczej z materiałów sproszkowanych.
Proszki gliniane są przygotowywane w specjalnych fabrykach z wysokiej jakości glinek poprzez suszenie, a następnie mielenie w młynach kulowych. Jednocześnie zawartość wilgoci w glinach grudkowych nie spada poniżej 6%, a cząstki gliny nie ulegają spiekaniu. Wytwórnie proszków glinianych budowane są na złożach wysokiej jakości glin lub bezpośrednio w miejscach konsumpcji.
Zespół przygotowania płuczki wiertniczej z materiałów sproszkowanych składa się z dwóch bunkrów o łącznej objętości 42 m3 układu podawania proszku gliniastego oraz mieszadła hydraulicznego (rys. 25). Gdy woda jest dostarczana z dużą prędkością przez rurę 10 w komorze mieszania 2, powstaje próżnia i proszek gliniany dostaje się do niego z lejka 1 mieszalnika hydraulicznego. Powstała mieszanina wchodzi do zbiornika 6, skąd jest wysyłana do zbiorników zapasowych lub odbiorczych w celu ostatecznego wykończenia roztworu. Wydajność mieszalników hydraulicznych sięga 80 m 3 roztworu na godzinę.
Ryż. 25. Mieszadło hydrauliczne MG:
1 - bunkier stożkowy (lejek); 2 - komora mieszania; 3 - właz;
4 - pokrywa pojemnika; 5 - rura spustowa; 6 - pojemnik;
7 - spawana rama (sanie); 8 - rębak (but);
9 - dopasowanie; 10 - rura doprowadzająca płyn
Oczyszczanie płuczek wiertniczych
Gotowa płuczka wiertnicza przez wąż ciśnieniowy przymocowany do nieruchomej części krętlika jest pompowany do przewodu wiertniczego za pomocą pomp wiertniczych. Po przejściu rur wiertniczych przechodzi z dużą prędkością przez otwory w świrze na dno studni, wyłapuje cząstki skały, a następnie unosi się między ścianami studni a rurami wiertniczymi. Odmowa ponownego użycia jest ekonomicznie nieopłacalna i nie można jej ponownie użyć bez czyszczenia, ponieważ. w przeciwnym razie dochodzi do intensywnego zużycia ściernego urządzeń i narzędzi wiertniczych, zmniejsza się zdolność zatrzymywania płynu wiertniczego i zmniejsza się możliwość wykonywania nowych dużych odłamków skalnych.
Niezbędne jest również przepuszczanie nowo przygotowanych roztworów gliny przez system czyszczący, ponieważ mogą zawierać grudki niewydmuchanej gliny, nieprzereagowane chemikalia i inne materiały.
Czyszczenie płynu do płukania Odbywa się to zarówno w wyniku naturalnego wytrącania się cząstek skalnych w rynnach i zbiornikach, jak i na siłę w urządzeniach mechanicznych (przesiewacze wibracyjne, hydrocyklony itp.). Zużyta płuczka wiertnicza (rys. 14) z głowicy 1 przez system rynien 2 wchodzi do sita wibracyjnego 3, umieszczonego na pochyłej i wibrującej siatce. W celu dalszego czyszczenia płyn wiertniczy jest pompowany przez 4 hydrocyklony za pomocą pompy szlamowej 7, w której można oddzielić cząstki skał o wielkości do 10 ... 20 mikronów. Ostateczne czyszczenie roztworu z najmniejszych zawieszonych cząstek skały odbywa się w zbiorniku 6 za pomocą odczynników chemicznych, pod działaniem których bardzo małe cząstki wydają się sklejać, po czym wytrącają się.
Ryż. 14. System obiegu błota:
1 - głowica odwiertu; 2 - rynna; 3 - sito wibracyjne; 4 - hydrocyklon;
5 - jednostka przygotowania płuczki wiertniczej; 6 - pojemność; 7 - pompa gnojowicy;
8 - zbiornik odbiorczy; 9 - pompa wiertnicza; 10 - rurociąg tłoczny.
Podczas osadzania się w zbiornikach 6 i 8 uwalnianie rozpuszczonych gazów z roztworu następuje jednocześnie.
Oczyszczona płuczka wiertnicza jest ponownie wprowadzana do odwiertu przez pompę 9 przez rurociąg wtryskowy 10. W razie potrzeby do systemu wprowadzana jest dodatkowa ilość świeżo przygotowanego roztworu z bloku 5.
7. Powikłania podczas wiercenia
W procesie wiercenia studni możliwe są różnego rodzaju komplikacje, w szczególności: zawalenia skał, absorpcja płynu płuczącego, wtargnięcia ropy, gazu i wody, wypadki, krzywizny studni.
lawiny skalne
lawiny skalne powstają z powodu ich niestabilności (pękanie, skłonność do pęcznienia pod wpływem wody). Charakterystyczne oznaki zawaleń to:
- znaczny wzrost ciśnienia na wylocie pomp wiertniczych;
- gwałtowny wzrost lepkości płynu spłukującego;
- usuwanie przez nią dużej liczby fragmentów zawalonych skał itp.
Absorpcja płynów
Absorpcja płynów- zjawisko polegające na tym, że płyn wstrzykiwany do odwiertu jest częściowo lub całkowicie wchłaniany przez formację. Zwykle ma to miejsce podczas przechodzenia formacji o dużej porowatości i przepuszczalności, gdy ciśnienie formacji jest mniejsze niż ciśnienie kolumny płuczki wiertniczej w odwiercie.
Intensywność wchłaniania może być od słabej do katastrofalnej, gdy uwalnianie cieczy na powierzchnię całkowicie ustaje.
Aby zapobiec wchłanianiu, stosuje się następujące metody:
- płukanie lekkimi płynami;
- eliminacja wchłaniania przez zablokowanie kanałów wchłaniających ciecz (dzięki dodaniu do niej obojętnych wypełniaczy - azbestu, miki, łusek ryżowych, torfu mielonego, trocin, celofanu; wylewanie szybkowiążących mieszanek itp.);
- zwiększenie właściwości strukturalnych i mechanicznych płynu myjącego (poprzez dodanie płynnego szkła, soli kuchennej, wapna itp.).
Pokazy ropy, gazu i wody
Pokazy gazu, ropy i wody występują podczas wiercenia studni przez formacje o stosunkowo wysokim ciśnieniu przewyższającym ciśnienie płynu wiertniczego. Pod działaniem ciśnienia wody następuje jej przelew lub wytryski, a pod działaniem ciśnienia ropy lub gazu następuje ciągłe wytryskiwanie lub okresowe emisje.
Środki mające na celu uniknięcie wtargnięcia gazu, ropy i wody obejmują:
- prawidłowy dobór gęstości cieczy płuczącej;
- zapobieganie obniżaniu się jego poziomu podczas podnoszenia przewodu wiertniczego i podczas wchłaniania cieczy.
Zaciski narzędzia wiertniczego
Zaciski narzędzia wiertniczego występują z następujących powodów:
- tworzenie grubej i lepkiej skorupy na ścianach studni, do której przykleja się narzędzie wiertnicze, gdy się nie porusza;
- zakleszczenie narzędzia wiertniczego w zwężonych częściach odwiertu lub w przypadku ostrej krzywizny odwiertu, w przypadku zawałów niestabilnych skał, w przypadku osiadania wierconej skały w przypadku ustania cyrkulacji.
Eliminacja sklejania to skomplikowana i czasochłonna operacja. Dlatego konieczne jest podjęcie wszelkich możliwych środków, aby ich uniknąć.
Wypadki
Wypadki, powstające podczas wiercenia można podzielić na cztery grupy:
- wypadki z bitami (odkręcenie bitu podczas opuszczania narzędzia z powodu jego niewystarczającego zamocowania, złamanie bitu w wyniku przeciążenia itp.);
- wypadki z rurami wiertniczymi i zamkami (pękanie rury wzdłuż korpusu; usuwanie gwintów rur, zamków i łodzi podwodnych itp.);
- wypadki z silnikami wgłębnymi (odkręcenie; pęknięcie wału lub obudowy itp.);
- wypadki z strunami osłonowymi (ich zgniecenie; zniszczenie połączeń gwintowanych; wpadnięcie poszczególnych odcinków rur do studni itp.).
Aby wyeliminować wypadki, specjalne narzędzia wędkarskie(rys. 26): zrazy, dzwonek, kran, router magnetyczny, pająk i inne. Najlepiej jednak zapobiegać wypadkom, ściśle przestrzegając zasad obsługi sprzętu, przeprowadzając jego wykrywanie wad, zapobieganie i wymianę w odpowiednim czasie.
Ryż. 26. Narzędzia wędkarskie:
a - poślizgnięcia; b - dzwonek; c - dotknij; g - frez magnetyczny; d - pająk
Dobrze krzywizna
Podczas wiercenia studni pionowych w sposób obrotowy, spontaniczny dobrze krzywizna, tych. odchylenie ich tułowia od pionu. Krzywizna studni pionowych pociąga za sobą szereg problemów: naruszenie planowanej sieci do zagospodarowania złóż ropy naftowej i gazu, zwiększone zużycie rur wiertniczych, pogorszenie jakości prac izolacyjnych, niemożność zastosowania pomp żerdziowych podczas eksploatacji odwiertu itp. .
Przyczynami skrzywienia odwiertu są czynniki geologiczne, techniczne i technologiczne. Geologiczne - obejmują obecność stromo zapadających się warstw na odcinku wiertniczym; częsta zmiana skał o różnej twardości; obecność w skałach, przez które przechodzi studnia, pęknięcia i jaskinie. Czynnikami technicznymi, które wpływają na krzywiznę odwiertów, są niedopasowanie osi wiertnicy do środka wirnika i osi odwiertu; pochylona pozycja stołu wirnika; użycie zakrzywionych rur wiertniczych itp. Czynniki technologiczne, które powodują krzywiznę studni, obejmują powstawanie nadmiernie dużych obciążeń osiowych na wiertle; rozbieżność między rodzajem wiertła, ilością i jakością płuczki wiertniczej oraz rodzajem przepuszczanych skał.
Zgodnie z powyższymi czynnikami podejmowane są środki zapobiegające skrzywieniu studni. W trudnych warunkach geologicznych stosuje się specjalny układ dna przewodu wiertniczego, w tym kalibratory i centralizatory. Dodatkowo potrzebujesz:
- instalacja sprzętu odbywa się zgodnie ze specyfikacją techniczną;
- wybierz rodzaj wędzidła zgodnie z rodzajem skał;
- zmniejszyć WOB itp.
8. Odchylone studnie
Nazywane są studnie, dla których projekt przewiduje pewne odchylenie dolnego otworu od pionu, a odwiert prowadzony jest po z góry określonej trajektorii ukośnie skierowany.
Nachylone studnie wierci się, gdy warstwy produkcyjne leżą pod wodami mórz, jezior, rzek, pod terytoriami osad, obiekty przemysłowe, na terenach podmokłych, a także do obniżenia kosztów budowy obiektów wiertniczych.
Obecnie opracowywane typy profili do studni kierunkowych dzielą się na dwie grupy: profile typu konwencjonalnego (reprezentujące linię krzywą leżącą w płaszczyźnie pionowej) oraz profile typu przestrzennego (w postaci krzywych przestrzennych).
Rodzaje profili studni kierunkowych zwykłego typu pokazano na ryc. 27. Profil typu A składa się z trzech odcinków: pionowego 1, odcinka skarpy odwiertu 2 i prostoliniowego odcinka nachylonego 3. Zaleca się stosować przy wierceniu płytkich odwiertów na polach jednowarstwowych, jeśli przewiduje się duże przemieszczenie odwiertu .
Ryż. 27. Rodzaje profili studni kierunkowych:
1 - nachylona sekcja; 2 - przekrój zestawu kąta nachylenia tułowia;
3 - prostoliniowy odcinek nachylony; 4 - sekcja do zmniejszania kąta nachylenia pnia
Profil typu B różni się od poprzedniego tym, że zamiast prostoliniowego odcinka nachylonego ma odcinek 4 o naturalnym spadku kąta nachylenia. Ten profil jest zalecany dla wielkie głębokości studnie.
Profil typu B składa się z pięciu odcinków: pionowego 1, odcinka podwyższenia kąta odwiertu 2, prostoliniowego odcinka nachylonego 3, odcinka obniżenia kąta nachylenia 4 i ponownie - pionowego 1. Zaleca się stosowanie podczas wiercenia głębokich studni przecinających kilka formacji produkcyjnych.
Profil typu G różni się od poprzedniego tym, że sekcje 3 i 4 zostały zastąpione sekcją spontaniczny zmniejszenie kąta nachylenia 4. Profil ten zalecany jest do wiercenia głębokich odwiertów, w których możliwe są odchylenia w dolnej części odwiertu.
Profil typu D składa się z odcinka pionowego 1 oraz odcinka o nastawionym kącie pnia 2. Charakteryzuje się dużą długością drugiego odcinka. Profil jest zalecany, jeśli to konieczne, aby zachować zadany kąt wejścia do zbiornika i otworzyć go na maksymalną moc.
Jak widać na ryc. 27 wszystkie typy profili mają na początku przekrój pionowy. Jego głębokość powinna wynosić co najmniej 40...50 m. Koniec odcinka pionowego jest zsynchronizowany z stabilnymi skałami, gdzie w jednym locie można uzyskać kąt zenitalny 5...6 stopni.
Aby odchylić studnię od pionu, stosuje się specjalne urządzenia odchylające: zakrzywioną rurę wiertniczą, zakrzywioną podporę, mimośrodową złączkę i deflektory różnych typów.
W ostatnich latach upowszechniły się studnie pionowe i skośne z długimi poziomymi zakończeniami. Odbywa się to w celu zwiększenia powierzchni, przez którą olej wpływa do studni, a tym samym zwiększenia natężenia przepływu. Jednocześnie stało się możliwe odzyskiwanie ropy naftowej na skalę przemysłową, która wcześniej była uważana za niemożliwą do wydobycia, ze względu na małą moc i niską przepuszczalność złoża. Dodatkowo poziome zakończenie studni znajduje się w formacji powyżej wód dennych, co pozwala na wydłużenie okresu eksploatacji na sucho.
9. Super głębokie studnie
Pierwszy amerykański szyb naftowy wydobywał ropę z głębokości około 20 m. W Rosji pierwsze szyby naftowe miały głębokość poniżej 100 m. Bardzo szybko ich głębokość sięgała kilkuset metrów. Pod koniec lat 60. w ZSRR średnia głębokość odwiertów do produkcji ropy naftowej i gazu wynosiła 1710 m. Najgłębsze złoże ropy naftowej w naszym kraju odkryto w rejonie Groznego na głębokości 5300 m, a uzyskano gaz przemysłowy w depresji kaspijskiej z głębokości 5370 m.
Najgłębszy zbiornik gazonośny w Europie na złożu Magossa (północne Włochy) leży na głębokości 6100 m. Największa głębokość na świecie, z której prowadzona jest komercyjna produkcja gazu to 7460 m (Teksas, USA).
Ogólny trend wydobycia ropy i gazu z coraz głębszych horyzontów ilustrują poniższe dane. Jeszcze 20 lat temu główne wydobycie ropy (66%) prowadzono z najmłodszych skał kenozoiku. Ze starszych mezozoicznych skał wydobyto 19% ropy, a z najstarszych skał paleozoicznych 15%. Teraz sytuacja się zmieniła: głównymi dostawcami ropy naftowej stały się skały mezozoiczne, a następnie skały paleozoiczne.
Jednym z zadań wiercenia ultragłębokich odwiertów jest więc poszukiwanie na dużych głębokościach horyzontów roponośnych i gazonośnych. Dopiero ultragłębokie wiercenie może zakończyć spór między zwolennikami organicznej i nieorganicznej hipotezy o pochodzeniu ropy. Wreszcie, do dokładniejszego zbadania wnętrza Ziemi konieczne są bardzo głębokie wiercenie. Rzeczywiście, dzisiaj wiemy wielokrotnie więcej o odległej przestrzeni niż o tym, co znajduje się pod nami kilkadziesiąt kilometrów dalej.
Wiercenie ultragłębokich studni wiąże się z dużymi trudnościami. Ciśnienie i temperatura wzrastają wraz z głębokością. Tak więc na głębokości 7000 m nawet ciśnienie hydrostatyczne wynosi 70 MPa, 8000 m -80 MPa itd. A w zbiorniku może być dwa razy więcej. Jak trzymać tego „dżina” w „butelce”? Do dostarczania płynu do płukania wymagane są pompy wysokociśnieniowe. Jaka powinna być ta ciecz, jeśli temperatura na dnie osiągnie 250 °C? Jak obrócić wielokilometrowy ciąg rur wiertniczych? Jak w ogóle korzystać z rur wiertniczych, jeśli stalowe rury wytrzymać ich ciężar do głębokości 10 km?
Na niektóre pytania udzielono już odpowiedzi. Do wiercenia bardzo głębokich studni stosuje się obciążoną płuczkę wiertniczą, która „zatyka” studnię własnym ciężarem. Ultragłębokie studnie wiercone są za pomocą silników wiertniczych, a rury wiertnicze wykonane są z lekkiego i wytrzymałego stopu aluminium.
Era głębokich wierceń rozpoczęła się w 1961 roku wraz z realizacją amerykańskiego projektu Mohol. Studnia została ułożona na dnie Oceanu Spokojnego w pobliżu wyspy Gwadelupa pod czterokilometrową warstwą wody. Założono, że studnia, po przejściu 150 m luźnych skał dna i 5,5 km solidnych skał leżących pod spodem, zanurzy się w płaszczu - kolejnej warstwie naszej planety po skorupie. Wiercenie ustało jednak po pierwszych 36 metrach. Powodem było to, że po wydobyciu pierwszego rdzenia nie udało się znaleźć ujścia już rozpoczętej studni, pomimo zastosowania najnowocześniejszych narzędzi wyszukiwania.
W 1968 r. przeprowadzono drugi atak na płaszcz ze specjalnie wyposażonego statku wiertniczego (ryc. 28). Jednak w 1975 roku, kiedy odsłonięto górne bazaltowe warstwy dna oceanicznego, wiercenia przerwano z powodu trudności technicznych.
Ryż. 28. Widok ogólny statku wiertniczego:
1 - statek; 2 - dźwig towarowy; 3 - helikopter
powierzchnia; 4 - wiertnica
Następnie na lądzie wiercono ultragłębokie studnie. W 1970 roku w Luizjanie wykonano odwiert 1-SL-5407 o głębokości 7803 m.
Wizualne przedstawienie nowoczesnej ultragłębokiej studni i jej wyposażenia można uzyskać na przykładzie jednej z najgłębszych studni na świecie. 1-Beiden, wywiercony w stanie Okhlacoma. Głębokość odwiertu wynosi 9159 m. Wiercenie rozpoczęto w 1970 roku i trwało 1,5 roku. Wysokość wiertni wynosi 43,3 m, udźwig 908 t. Moc ciągów to 2000 kW, a każda z dwóch pomp płuczących 1000 kW. Całkowita pojemność gruntu system cyrkulacji dla gnojowicy 840 m\ Głowica wyposażona jest w zawory przeciwwybuchowe zaprojektowane na ciśnienie 105,5 MPa.
Konstrukcyjnie odwiert składa się z szybu kierunkowego o średnicy 0,9 m do głębokości 18 m, przewodu o średnicy 0,5 m do głębokości 1466 m, rur osłonowych do głębokości 7130 m oraz ciągów produkcyjnych. Łącznie do odwiertu zużyto około 2200 ton stalowych rur osłonowych, 1705 ton cementu i 150 wierteł diamentowych. Całkowity koszt odwiertu wyniósł 6 milionów dolarów.
Na początku 1975 roku w ZSRR było dziesięć studni, których głębokość przekraczała 6 km. Należą do nich Aral-Sorskaya na nizinie kaspijskiej o głębokości 6,8 km, Biikzhalskaya w Azerbejdżanie o głębokości 6,7 km, Sinevidnaya (7,0 km) i Shevchenkovskaya (7,52 km) na zachodniej Ukrainie, Burunnaya (7,5 km) na Kaukazie Północnym itd. Najgłębsza studnia świata, studnia Kola, przekroczyła linię 12 km.
10. Wiercenie studni na morzu
Obecnie udział ropy naftowej wydobywanej ze złóż podmorskich wynosi około 30 % całej światowej produkcji, a jeszcze więcej gazu. Jak ludzie dostają się do tego bogactwa?
Najprostszym rozwiązaniem jest wbijanie pali w płytkiej wodzie, zainstalowanie na nich platformy, na której jest już posadowiona wiertnica i niezbędny sprzęt.
Innym sposobem jest „wydłużenie” wybrzeża poprzez wypełnienie płytkiej wody ziemią. Tak więc w 1926 r. Zatoka Bibi-Heybat w rejonie Baku została wypełniona, a na jej miejscu powstało pole naftowe.
Po odkryciu ponad pół wieku temu dużych złóż ropy i gazu na Morzu Północnym narodził się śmiały projekt jego osuszenia. Faktem jest, że średnia głębokość większości Morza Północnego ledwie przekracza 70 m, a niektóre odcinki dna pokrywa tylko czterdziestometrowa warstwa wody. Dlatego autorzy projektu uznali za celowe za pomocą dwóch zapór – przez kanał La Manche w rejonie Dover, a także między Danią a Szkocją (o długości ponad 700 km) – odcięcie ogromnego odcinka Północy. Morze i wypompuj stamtąd wodę. Na szczęście ten projekt pozostał tylko na papierze.
W 1949 r. na otwartym morzu na Morzu Kaspijskim, 40 km od wybrzeża, wykonano pierwszy w ZSRR szyb naftowy. W ten sposób rozpoczęło się tworzenie miasta na stalowych palach, zwanego „Skałami Naftowymi”. Jednak budowa wiaduktów ciągnących się na wiele kilometrów od wybrzeża jest bardzo kosztowna. Ponadto ich budowa jest możliwa tylko na płytkiej wodzie.
Podczas wiercenia szybów naftowych i gazowych na głębokich morzach i oceanach stosowanie platform stacjonarnych jest trudne technicznie i ekonomicznie nieopłacalne. W tym przypadku stworzono pływające platformy wiertnicze, które są zdolne do zmiany obszarów wiercenia samodzielnie lub za pomocą holowników.
Istnieją platformy wiertnicze podnośnikowe, platformy wiertnicze półzanurzalne oraz platformy wiertnicze grawitacyjne.
Podnośna platforma wiertnicza(rys. 29) to pływający ponton 1 z wycięciem, nad którym znajduje się wiertnica. Ponton ma kształt trój-, cztero- lub wielokątny. Mieści się w nim sprzęt wiertniczy i pomocniczy, piętrowa kabina z kabinami dla załogi i pracowników, elektrownia i magazyny. Wielometrowe kolumny wsporcze 2 są zainstalowane w rogach platformy.
Ryż. 29. Podnośnik podnośnika w pozycji transportowej:
1 - pływający ponton; 2 - podpórka do podnoszenia; 3 - wiertnica;
4 - żuraw obrotowy (towarowy); 5 - przedział mieszkalny; 6 - lądowisko dla helikopterów;
7 - podwyższony portal; 8 - główny pokład
W miejscu wiercenia z podnośniki hydrauliczne kolumny schodzą, sięgają dna, opierają się na ziemi i wchodzą w nią głęboko, a platforma unosi się nad powierzchnią wody. Po zakończeniu wiercenia w jednym miejscu platforma jest przenoszona w inne.
Niezawodność instalacji podnośnych platform wiertniczych zależy od wytrzymałości gruntu tworzącego dno w miejscu wiercenia.
Półzanurzalne platformy wiertnicze(rys. 30) stosowane są na głębokościach 300…600 m, gdzie platformy podnośnikowe nie mają zastosowania. Nie spoczywają na dnie morskim, ale unoszą się nad miejscem odwiertu na ogromnych pontonach. Takie platformy są powstrzymywane przez kotwice o wadze 15 ton lub więcej. Liny stalowe łączą je z wciągarkami automatycznymi, które ograniczają przemieszczenia poziome względem punktu wiercenia.
Ryż. 30 Półzanurzalna platforma wiertnicza:
1 - zatapialny ponton; 2 - kolumna stabilizacyjna; 3 - górna część ciała;
4 - wiertnica; 5 - dźwig towarowy; 6 - lądowisko dla helikopterów.
Pierwsze półzanurzalne platformy nie były samobieżne, a na teren prac dostarczano je za pomocą holowników. Następnie platformy zostały wyposażone w śmigła napędzane silnikami elektrycznymi o łącznej mocy 4,5 tys. kW.
Wadą platform półzanurzalnych jest możliwość ich przemieszczania się względem punktu wiercenia pod wpływem fal.
są bardziej stabilne platformy wiertnicze typu grawitacyjnego. Wyposażone są w mocną betonową podstawę spoczywającą na dnie morskim. W bazie tej mieszczą się nie tylko kolumny prowadzące do wiercenia, ale także ogniwa-zbiorniki do przechowywania wyprodukowanej ropy naftowej i oleju napędowego wykorzystywanego jako nośnik energii oraz liczne rurociągi. Elementy podstawy dostarczane są na miejsce montażu w postaci dużych bloków.
Dno morskie w miejscu położenia platform grawitacyjnych musi być starannie przygotowane. Nawet niewielkie nachylenie dna grozi zamienieniem wiertnicy w Krzywą Wieżę w Pizie, a obecność występów na dnie może spowodować pęknięcie podstawy. Dlatego przed ustawieniem wiercenia „na punkt” wszystkie wystające kamienie są usuwane, a pęknięcia i zagłębienia na dnie są uszczelniane betonem.
Wszystkie typy platform wiertniczych muszą wytrzymać napór fal o wysokości do 30 m, chociaż fale takie występują raz na 100 lat.
Ogólny schemat wiercenia
Do wiercenia szybów naftowych i gazowych stosuje się wyłącznie metodę obrotową. Dzięki tej metodzie studnia jest niejako wiercona obrotowym wiertłem. Wywiercone cząstki skały są wynoszone na powierzchnię przez krążący strumień płuczki wiertniczej. W zależności od umiejscowienia silnika wiercenie obrotowe dzieli się na obrotowy gdy silnik znajduje się na powierzchni i wbija wiertło w dół poprzez obrót całego przewodu wiertniczego i wiercenie wgłębne (za pomocą turbiny lub wiertarki elektrycznej), gdy silnik znajduje się blisko dna otworu nad wiertłem.
Proces wiercenia składa się z następujących operacji:
zatykanie się (zejście rur wiertniczych świdrem do studni na dno i podnoszenie ich zużytym wiertłem) i samo wiercenie - praca świdra na dnie (niszczenie skały przez świder).
Operacje te są okresowo przerywane w celu wprowadzenia rur osłonowych do odwiertu, które służą do ochrony ścian studni przed zawaleniami i oddzieleniem horyzontów naftowych.
Jednocześnie podczas procesu wiercenia wykonywanych jest szereg prac pomocniczych;pobieranie próbek rdzenia, przygotowanie płuczki wiertniczej, rejestracja, pomiary krzywizny otworu wiertniczego, badanie lub zagospodarowanie odwiertu w celu wywołania przepływu ropy itp.
Pełny cykl budowy studni składa się z następujących procesów:
jeden). Montaż wieży, sprzęt wiertniczy, aranżacja terenu.
2). proces wiercenia.
cztery). Odsłanianie i rozdzielanie warstw (bieganie i cementowanie obudowy).
5) Badanie studni pod kątem dopływu ropy lub gazu (zagospodarowanie).
6). Demontaż sprzętu
Ogólny, schematyczny schemat rozmieszczenia sprzętu wiertniczego w odwiercie przedstawiono na ryc. Nr 1.
Sprzęt wiertniczy
Wiertnice.
Wiertnica przeznaczona jest do podnoszenia i opuszczania przewodu wiertniczego i rur okładzinowych do studni, utrzymywania przewodu wiertniczego w stanie zawieszenia podczas wiercenia, a także umieszczania w nim układu jezdnego, rur wiertniczych i części osprzętu niezbędnego do wiercenia proces.
Podczas wiercenia w poszukiwaniu ropy i gazu stosuje się metalowe żurawie typu wieżowego i masztowego. Wieże masztowe są używane częściej niż wieże. Są łatwiejsze i szybsze w montażu, ale wieże wieżowe są bardziej nośne i wyższe. Wieża coraz częściej wykorzystywane są w głębokich otworach poszukiwawczych, a masztowe w wierceniach produkcyjnych.
Wiertnice różnią się nośnością i wysokością. Praktyka ustaliła, że przy wierceniu studni na głębokość 1200-1300m wskazane jest stosowanie wież o wysokości 28m, studni o głębokości 133-3500m - o wysokości 41-42m, studni o głębokości większej niż 3500m - wysokość 53m lub więcej.
Obecnie szeroko stosowane są wieże masztowe w kształcie litery A (patrz rys. nr 1). Składają się z dwóch kolumn połączonych u góry w bloku koronowym za pomocą wiązań i przymocowanych u dołu do zawiasów wsporczych. W pewnej odległości od zawiasów wieża ma sztywne podpory - rozpórki.
Drawworks
Ciągnik przeznaczony jest do opuszczania i podnoszenia przewodu wiertniczego, wkręcania i odkręcania rur, opuszczania przewodów osłonowych, utrzymywania stałego ciężaru przewodu lub powolnego opuszczania (podawania) go podczas wiercenia.
W niektórych przypadkach do przenoszenia mocy z silnika na wirnik, ciągnięcia ładunków i innych prac pomocniczych stosuje się wyciągi.
Rysunki produkowane są w różnych typach, różniących się między sobą schematami kinematycznymi i konstrukcją.
Systemy podróżne
System wiertnic podnośnikowych (poly-spast) służy do zamiany ruchu obrotowego bębna wciągarki na ruch translacyjny (pionowy) haka i zmniejszenia obciążenia gałęzi liny.
Stalowa lina jezdna przechodzi przez krążki linowe bloku koronowego i bloku jezdnego w określonej kolejności, której jeden koniec („martwy”) jest przymocowany do belki ramy wieży, a drugi, zwany biegiem (prowadzącym). ) jeden, do bębna wciągarki.
W zależności od nośności i liczby odgałęzień liny w sprzęcie, systemy jezdne są podzielone na różne rozmiary. W platformach wiertniczych o nośności 50-75 ton stosuje się system jezdny z liczbą krążków 2\3 i 3\4; w instalacjach o udźwigu 100-300t - układ jezdny z liczbą krążków 3\4, 4\5, 5\6 i 6\7. W oznaczeniu układu olinowania pierwsza cyfra oznacza liczbę krążków liny bloku jezdnego, a druga liczbę krążków liny zblocza koronowego.
blok korony przedstawia ramę, na której zamontowane są osie i podpory z kołami pasowymi. Czasami rama jest wykonana jako jeden element ze szczytem wieży.
blok podróżny to spawana obudowa, w której umieszczone są koła pasowe i zespoły łożyskowe. jak w blokach koronowych.
Liny podróżne to stalowe okrągłe, sześciorzędowe liny o konstrukcji linowej o ułożeniu krzyżowym. Splotki skręcone w linę wokół organicznego lub metalowego rdzenia wykonane są z wysokowytrzymałej stali wysokowęglowej i wysokomanganowej z liczbą drutów od 19 do 37. kierunek jego nawijania na bęben, do ciągadeł stosuje się liny prawoskrętne o średnicy 25 mm, 28, 32, 35, 38 mm. Najczęściej spotykane liny o średnicach rdzenia organicznego i plastikowego 28 i 32 mm. Na głębokościach powyżej 4000 m stosuje się liny z rdzeniem metalowym, które mają zwiększoną siłę zrywającą i dużą sztywność poprzeczną, dzięki czemu wzrasta ich odporność na zgniatanie.
Haki wiertnicze oraz zblocza hakowe są przeznaczone do zawieszania na nich narzędzi wiertniczych i podnośników podczas operacji wyzwalania.
bloki hakowe (haki połączone z klockiem jezdnym) mają szereg zalet: mniejsza wysokość całkowita niż w połączeniu klocek jezdny i hak, bardziej kompaktowa konstrukcja. Wady to ich duża masa.
Dostępne są haki o udźwigu 75, 130, 200,225t (odpowiednio, co pozwala na krótkotrwały, maksymalny udźwig -110, 160, 250 i 300t).
Znamionowy udźwig zbloczy hakowych to 75, 125 i 200t (maksymalny udźwig to 100, 160 i 250t).
Zawiesia wiertnicze - są to ogniwa łączące hak z podnośnikiem, na którym zawieszone jest narzędzie wiertnicze lub linka osłonowa. Udźwig zawiesi wynosi 25,50,75,125,200 i 300t. Ogniwa o udźwigu 25, 50 i 75 ton przeznaczone są do odwiertów, ale mogą być również stosowane do wiertnic o odpowiednim udźwigu.
Mechanizmy i narzędzia używane do produkcji operacji wyzwalania
Podnoszenie i opuszczanie rur wiertniczych w celu wymiany zużytego wiertła składa się z tych samych powtarzających się operacji. Do produkcji operacji wyzwalania używa się specjalnego sprzętu i narzędzi. Obejmują one: winda, kliny, klucz tarczowy, klucze do maszyn ("pająki"), kleszcz wiertarski automatyczny (ABK), pneumatyczny obrotowy chwytak klinowy(RCP).
Winda, przeznaczony do chwytania i utrzymywania ciężaru ciągu rur wiertniczych lub osłonowych podczas operacji wyzwalania. Stosowane są elewatory różnego typu, różniące się wielkością w zależności od średnicy rury wiertniczej lub osłonowej, nośności, projekt i materiał do ich produkcji.
Kliny do rur wiertniczych służą do zawieszenia narzędzia wiertniczego na stole wirnika. Wkłada się je w stożkowy otwór między rurą a wkładkami wirnika. Zastosowanie klinów przyspiesza prace przy operacjach wyzwalania. Kliny osłonowe służą do prowadzenia ciężkich sznurów osłonowych. Kliny są instalowane na specjalnych podkładkach nad głowicą odwiertu. Pneumatyczny obrotowy chwytak klinowy (RCP), wbudowany w rotor i przeznaczony do podnoszenia i opuszczania klinów.
Do wykręcania i odkręcania rur wiertniczych i rur osłonowych używa się różnych kluczy. Niektóre z nich przeznaczone są do skręcania, a inne do mocowania i odłączania połączeń gwintowych słupa. Zwykle lekki okrągły Klucze do wstępnego skręcania rur są przeznaczone do zamków o tej samej średnicy, oraz ciężkie klucze maszynowe do mocowania i odkręcania połączeń gwintowanych - na dwa, a czasem więcej rozmiarów rur wiertniczych i zamków. Operacja mocowania i luzowania połączeń gwintowanych odbywa się za pomocą dwóch kluczy maszynowych: jeden klucz (zatrzymujący) jest stały, a drugi (wkręcanie lub luzowanie) jest ruchomy. Klucze zawieszone są w pozycji poziomej i przymocowane do stalowych lin ułatwiających ich przemieszczanie. Prace związane z opuszczaniem i podnoszeniem są znacznie ułatwione podczas używania bateria do automatycznego kleszczy wiertniczych montowany pomiędzy wyciągarką a wirnikiem (rys. nr 2) W celu uniknięcia ześlizgnięcia się klucza w szczęki wkładane są krakersy z nacięciem.
Sprzęt do wiercenia studni.
Przy wierceniu metodą obrotową konieczne jest, aby narzędzie niszczące (wiertło) otrzymało ruch obrotowy i obciążenie zapewniające wystarczający nacisk na niszczoną przerwę. Ponadto konieczne są warunki do usunięcia zniszczonych cząstek materii (skały). Dlatego studnia wyposażona jest w wirnik, krętlik z wężem wiertniczym, pompy płuczkowe i przewód wiertniczy. Jeśli świdry nie obracają się z powierzchni ziemi (wirnik), ale bezpośrednio przy dnie, oprócz wymienionego sprzętu stosuje się turbowiertarki lub wiertarki elektryczne.
Wirnik
Wirniki (rys. 2,3) są przeznaczone do przenoszenia ruchu obrotowego na przewód wiertniczy podczas wiercenia, podpierając go ciężarem, gdy operacje wyzwalania i prace pomocnicze. Wirnik to przekładnia, która przenosi obrót na pionowo zawieszony przewód wiertniczy z poziomego wału napędowego. Prędkość wirnika można zmieniać za pomocą kół zębatych wciągarki lub zmieniając koła łańcuchowe.
|
Zgodnie z przeznaczeniem wiertła dzielą się na trzy grupy:
jeden). Dłuta, które niszczą skałę nieustanną rzezią.
2). Bity, które niszczą skałę za pomocą uboju pierścieniowego (bity rdzeniowe).
3). Dłuta do celów specjalnych (szpiczaste, rowkowe, rozwiertaki, frezy itp.).
Zarówno do wiercenia w litym, jak i rdzeniowym stworzono wiertła, które umożliwiają niszczenie skały zgodnie z dowolną z wymienionych czterech zasad działania. Ułatwia to dobór rodzaju świdra zgodnie z właściwościami fizycznymi i mechanicznymi danej skały.
W procesie wiercenia otworu poszukiwawczego, a czasem wydobywczego, skały są okresowo selekcjonowane w postaci nienaruszonych filarów (rdzeni) w celu wykonania przekroju stratygraficznego, zbadania cech litologicznych przepuszczonych skał, identyfikacji zawartości ropy lub gazu w pory mijanych skał itp.
Do wyciągnięcia rdzenia na powierzchnię używa się specjalnych bitów, zwanych kolumnowy. Podczas wiercenia rdzeń wchodzi do wnętrza takiego wiertła i w odpowiednim momencie unosi się na powierzchnię.
Wydany bity rdzeniowe dwa typy - z wyjmowanym nośnikiem gleby i bez wyjmowanego nośnika gleby. Podczas wiercenia koronkami wiertniczymi bez zdejmowanego nośnika gruntu należy podnieść cały przewód wiertniczy, aby wyprowadzić rdzeń na powierzchnię. Podczas pracy z wiertłami wiertniczymi za pomocą wyjmowanej pogłębiarki, ta ostatnia za pomocą specjalnej liny, małej pomocniczej wciągarki i łapacza jest wyciągana na powierzchnię bez podnoszenia rur.
Wiertarka
Wiertarka zawiera kelly, rury wiertnicze, przeguby narzędziowe, podpory, kołnierze wiertnicze, centralizatory przewodu wiertniczego.
Przeznaczony jest do następujących celów:
1) przeniesienie obrotu z wirnika na świder (podczas wiercenia obrotowego);
2) doprowadzenie płynu płuczącego do turbowiertarki (w przypadku wiercenia turbinowego), do świdra i dolnego otworu (dla wszystkich metod wiercenia);
3) tworzenie WOB;
4) podnoszenie i opuszczanie świdra, turbowiertarki, wiertarki elektrycznej;
5) prowadzenie prac pomocniczych (rozbudowa i płukanie studni, łowienie ryb, sprawdzanie głębokości studni itp.).
Ołowiana rura(Rys. nr 3) w większości przypadków ma przekrój kwadratowy. Moment obrotowy z wirnika przenoszony jest na rurę prowadzącą przez wkładki włożone do wirnika. Dla każdego rozmiaru rury stosowane są odpowiednie wykładziny, które pozwalają na swobodne poruszanie się wzdłuż osi studni.
Ponieważ w praktyce najczęstsza wieża ma wysokość 41 m, co pozwala na posiadanie świec o długości około 25 m, rury wiertnicze wykonuje się w długościach 6,8 i 11,5 m. Dlatego świecę można złożyć z czterech rur o długości 6m każda, trzech rur o długości 8m lub dwóch rur o długości 11,5m.
Przy montażu stojaka z trzech rur wiertniczych o długości 8 m stosuje się dwie złączki lub jedną złączkę i jedną blokadę. Dwie rury wiertnicze o długości 11,5 m łączy się za pomocą zamków wiertniczych. Zmontowane świece są również przykręcane za pomocą zamków wiertarskich.
Kołnierze wiertnicze montowany nad wiertłem (turbodrill, wiertarka elektryczna) w celu zwiększenia sztywności dolnej części przewodu wiertniczego. Ich zastosowanie pozwala na wytworzenie obciążenia świdra za pomocą krótkiego zestawu połączonych ze sobą rur grubościennych, co poprawia warunki pracy przewodu wiertniczego.
Subs przeznaczony do łączenia elementów przewodu wiertniczego o różnych typach i rozmiarach gwintów.
Rury wiertnicze ze stopów lekkich służy do zmniejszenia ciężaru przewodu wiertniczego. Są skręcane za pomocą zamków wiertniczych o specjalnej konstrukcji. Zastosowanie rur wiertniczych ze stopów lekkich umożliwiło około 2-krotne zmniejszenie ciężaru kolumn.
Kolumna operacyjna.
Obecnie najczęściej spotykane są sznurki produkcyjne o średnicach 127, 146 i 168 mm.
W celu pomyślnego doprowadzenia sznura okładzinowego na docelową głębokość, a następnie zacementowania studni, dno sznura okładzinowego jest specjalnie wyposażone w pewne detale (rys. nr 13): korek prowadzący 1, trzewik 2, dysza do butów 3, zawór zwrotny 4.
korek prowadzący z drewna, cementu lub żeliwa,
Przy ujściu studni wiertniczej, gdzie możliwe są wydmuchy, zainstalowany jest sprzęt BOP, składający się z prezerwatywy tego czy innego typu (taran, uniwersalny, obrotowy), sprzętu do zdalnego i sterowanie ręczne je, systemy rurociągów z wysokociśnieniowymi zasuwami lub zaworami.
Prewenator uniwersalny (rys. nr 15) hermetycznie zamyka głowicę w obecności rur o różnych średnicach i typach.
Zatykanie (cementowanie) studni.
Celem zatykania odwiertu jest uzyskanie silnego pierścienia środka zatykającego zlokalizowanego w pierścieniu, który na całej wysokości powinien zapewnić separację i izolację poziomów produkcyjnych oraz stref powikłań odkrywanych przez odwiert (ryc. nr 12).
W zależności od charakterystyki odcinka geologicznego i warunków wiercenia do przygotowania zaczynu cementowego stosuje się cementy obciążone (o gęstości płuczki do 2,2 g/cm w strefach absorpcji cieczy płuczącej) itp.
Jednostki do fugowania przeznaczony do przygotowania (jeśli nie jest używana mieszarka) i wtłaczania zaczynu cementowego do studni oraz do wtłaczania jej do pierścienia. Jednostki te są również wykorzystywane do prób ciśnieniowych ciągów osłonowych i innych prac pomocniczych.
maszyna do mieszania przeznaczony do przygotowywania roztworów z materiałów proszkowych.
Podłączanie głowic przeznaczone są do pompowania gnojowicy iniekcyjnej i wyciskowej podczas korkowania, a także płukania gnojowicy przy płukaniu studni w procesie prowadzenia sznurka i innych operacji technicznych.
Korki wlewowe służy do wiercenia studni. Górny korek jest przeznaczony do zapobiegania przenikaniu płynu płuczącego do zawiesiny cementowej, gdy ta ostatnia jest wciskana do pierścienia i do kontrolowania prawidłowego wstrzykiwania jej do pierścienia, a dolny korek służy do czyszczenia wewnętrzna powierzchnia obudowa z resztek szlamu cementowego.
Podczas wiercenia studni stosuje się głównie jednoetapowe spoinowanie rur osłonowych.
Istota tej metody jest następująca. Po opuszczeniu obudowy na jej górną część nakręca się głowicę iniekcyjną, studzienkę płucze się, a następnie pompuje się obliczoną ilość zaczynu.
Ponadto w głowicy zatykającej zostaje zwolniony samouszczelniający korek gumowy i od góry pompowany jest roztwór do wyciskania. Gdy tylko korek osadzi się na pierścieniu oporowym, ciśnienie w kolumnie gwałtownie wzrasta. Skok igły manometru będzie wskazywał, że zaczyn cementowy całkowicie wycisnął się ze sznurka do pierścienia, tj. pod koniec procesu podłączania.
Przy cementowaniu w studniach głębinowych konieczne jest przepompowanie dość dużej objętości zaczynu cementowego i płynu wyciskającego w bardzo ograniczonym czasie, określanym przez moment, w którym zaczyn cementowy zaczyna twardnieć. W takich warunkach stosuje się cementowanie dwuetapowe: zaczyn cementowy jest wpompowywany do sznurka i wtłaczany do pierścienia w dwóch porcjach. Pierwsza część jest wciskana za sznurkiem przez trzewik, a druga przeciskana jest przez otwory w tulei odlewniczej, zainstalowanej w sznurku osłonowym w znacznej odległości od trzewika.
Po zatkaniu studni górne końce sznurków osłonowych są wiązane głowicą sznurkową, która jest mocowana bezpośrednio do rury osłonowej.
Cementowanie kolumny kończą się podstawowe operacje dobrze proces budowy. Następnie następuje rozwój i eksploatacja studni. Montaż i demontaż sprzętu wiertniczego, kontrola technologiczna i badania geofizyczne w odwiercie, perforacja kolumn, badania zbiorników i stymulacja dopływu, rekonstrukcje odwiertów i eliminacja wypadków podczas wiercenia nie są uwzględnione w niniejszej instrukcji referencyjno-metodologicznej.
Należy zauważyć, że wiercenie odwiertów naftowych i gazowych może odbywać się tylko przy najściślejszym przestrzeganiu wszystkich zasad i wymagań. I wcale nie jest to zaskakujące, ponieważ trzeba pracować z dość niebezpiecznym i wrażliwym materiałem, którego wydobycie i tak wymaga kompetentnego podejścia. Aby zrozumieć wszystkie aspekty pracy z takimi, należy przede wszystkim wziąć pod uwagę wszystkie podstawy tej sprawy i jej elementów.
Tak więc studnia nazywana jest wyrobiskiem górniczym, która powstaje bez konieczności dostępu do wnętrza człowieka i ma kształt cylindryczny - jej długość jest wielokrotnie większa niż średnica. Początek studni nazywa się ujściem, powierzchnia cylindrycznej kolumny nazywa się pniem lub ścianą, a dno obiektu nazywa się dnem. Długość obiektu mierzy się od ust do dna, natomiast głębokość mierzy się rzutem osi na pion. Średnica początkowa takiego przedmiotu maksymalnie nie przekracza 900 mm, natomiast średnica końcowa w rzadkich przypadkach jest mniejsza niż 165 mm – to specyfika procesu, który nazywamy wiercenie szybów naftowych i gazowych i jego funkcje.
Cechy wiercenia szybów naftowych i gazowych
Tworzenie odwiertów jako odrębny proces polega głównie na wierceniu, a to z kolei opiera się na następujących operacjach:
- Proces pogłębiania podczas niszczenia skał narzędziem wiertniczym,
- Usuwanie pokruszonej skały ze studni,
- Wzmocnienie szybu strunami obudowy w miarę pogłębiania się kopalni,
- Wykonywanie prac geologicznych i geofizycznych w celu poszukiwania horyzontów produkcyjnych,
- Cementowanie sznurka produkcyjnego.
Klasyfikacja odwiertów naftowych i gazowych
Wiadomo, że niezbędne materiały, które planuje się wydobywać, mogą występować na różnych głębokościach. A zatem wiercenie można wykonywać również na różnych głębokościach, a jednocześnie, jeśli mówimy o głębokości do 1500 metrów, wiercenie uważa się za płytkie, do 4500 - średnie, do 6000 - głębokie. Do tej pory wiercenie odwiertów naftowych i gazowych odbywa się na bardzo głębokich horyzontach, głębszych niż 6000 metrów - pod tym względem odwiert Kola jest bardzo orientacyjny, którego głębokość wynosi 12650 metrów. Jeśli rozważymy metody wiercenia, skupiając się na metodzie niszczenia skał, to tutaj jako przykład możemy przytoczyć metody mechaniczne, np. rotacyjne, które są realizowane za pomocą wiertarki elektrycznej i silników wiertniczych typu śrubowego. Istnieją również metody perkusyjne. Wykorzystują również metody niemechaniczne, między innymi elektropulsowe, wybuchowe, elektryczne, hydrauliczne i inne. Wszystkie z nich nie są szeroko stosowane.
Działa podczas wiercenia w poszukiwaniu ropy lub gazu
W wersja klasyczna podczas wiercenia w poszukiwaniu ropy lub gazu do kruszenia skały używa się wierteł, a płyn do płukania stale czyści otwór dna. W rzadkich przypadkach do oczyszczania stosuje się odczynnik roboczy typu gazowego. Wiercenie w każdym przypadku odbywa się w pionie, pochylone wiercenie stosuje się tylko wtedy, gdy jest to konieczne, stosuje się również wiercenie klastrowe, kierunkowe, dwustronne lub wielostronne. Pogłębianie studni odbywa się z próbkowaniem rdzenia lub bez, pierwsza opcja jest stosowana podczas pracy na obrzeżach, a druga - na całym obszarze. Jeśli rdzeń jest pobierany, jest badany pod kątem przepuszczonych warstw skalnych, okresowo unosząc go na powierzchnię.
Wiercenie w poszukiwaniu ropy i gazu odbywa się dziś zarówno na lądzie, jak i na morzu, a takie prace są wykonywane przy użyciu specjalnych platform wiertniczych, które zapewniają wiercenie obrotowe za pomocą specjalistycznych rur wiertniczych, które są łączone za pomocą połączeń gwintowanych typu „kielich-zamek”. Czasami stosuje się również ciągłe elastyczne rury, które są nawinięte na bębny i mogą mieć długość około 5 tysięcy metrów lub więcej. Takich prac nie można więc nazwać prostymi – są one bardzo specyficzne i złożone, a szczególny nacisk należy tu położyć na nowe technologie, których badanie może być trudnym zadaniem nawet dla profesjonalistów z tej branży.
Nowe technologie wiercenia szybów naftowych i gazowych na wystawie Neftegaz
Dzielenie się informacjami i poznawanie innowacji może zapewnić optymalny postęp, dlatego takiej potrzeby po prostu nie można pominąć. Jeśli zdecydujesz się połączyć nowoczesne osiągnięcia i zanurzyć się w środowisku zawodowym, w tym celu organizowane są profesjonalne wydarzenia i zdecydowanie powinieneś wziąć udział w jednym z nich. Mówimy o wystawach, które corocznie odbywają się na terenie Targów Expocentre i gromadzą setki i tysiące specjalistów w tej dziedzinie podczas dni otwarcia. Tutaj możesz łatwo uzyskać dostęp do nowych rozwiązań, studiować zaawansowane technologie, a jednocześnie pozyskiwać przydatne kontakty w wymaganej liczbie, znajdować klientów i partnerów. Takich okazji nie można przegapić, ponieważ nie pojawiają się one zbyt często i mogą mieć duże znaczenie, jeśli zostaną wykonane prawidłowo!
Przeczytaj nasze inne artykuły.
I . Część techniczna. Charakterystyka i krótki opis urządzeń.
Platformy i konstrukcje wiertnicze……………………………………………….………………………………4
System podróży………………………………………………………………………………….………..5
Rysunki………………………………………………………..………………...……...6
Wirniki………………………………………………………………………..……………………………….7
Pompy szlamowe i wyposażenie układu cyrkulacyjnego…………..………………………...………8
Krętliki………………………………………………………………..………………….…………9
Napędy wiertnic ………………………………………………………………...…….9
Sprzęt do uszczelniania głowic……………………..………………...………10
II . Część technologiczna.
1. Wiercenie szybów naftowych i gazowych………………………………….……..14
Zapoznanie się z metodami ręcznego posuwu wierteł, wiercenia
z kontrolerem wiertła, nauka wiercenia z rotorem………………………………………………..14
Zapoznanie z metodologią racjonalnego rozwoju
Partia………………………………………………………………………………………………………15
Wykonywanie podstawowych prac w oprogramowaniu open source za pomocą specjalnego
sprzęt……………………………………………………………………………………….16
Przygotowanie rury do przeciągania, montaż windy
na wirniku, wyjęcie go z wirnika, posadzenie rur na klinach………………………………………...17
Sprawdzenie gwintu zamka, przykręcenie BT kluczem
którego bateria, ponowne zamocowanie i odpięcie połączeń zamka za pomocą
za pomocą kluczy UMK……………………………………………………………………………………………………………………… ………………………………………………………………………………………………………………………………………… ………………………………………………………………………………………………………………………………………… …………………………………………………………………………………………
Inspekcja i pomiary BT i UBT, montaż BT na świeczniku, na-
toczenie i toczenie bitów………………………………………………………………………19
Dobrze spłukiwanie………………………………………………………………………………...…….20
BHA i regulacja reżimu odwiertów w celu zwalczania samopro-
dowolna krzywizna studni………………………………………………………………...…….22
2. Zapoznanie się z wierceniem studni z krzakami……………………………….23
3. Uruchamianie i cementowanie ciągów osłonowych……………….………..24
4. Otwieranie i testowanie horyzontów naftowych……………….………..26
5. Praca awaryjna w studni……………………………………….………..27
6. Likwidacja GNVP i emisje……………………………….…….…….28
I . Część techniczna
Charakterystyka i krótki opis urządzeń
Wiertnice i urządzenia wiertnicze
Procesowi wiercenia towarzyszy opuszczanie i podnoszenie przewodu wiertniczego do odwiertu oraz utrzymywanie go na wadze. Masa narzędzia, za pomocą którego trzeba w tym przypadku działać, sięga wielu setek kiloniutonów. W celu zmniejszenia obciążenia liny i zmniejszenia mocy zainstalowanej silników stosuje się sprzęt podnoszący (rys. 2.2), składający się z wieży, zaciągu i systemu wielokrążkowego (polyspastu). System jezdny z kolei składa się z części stałej – zblocza koronowego (bloki stałe) montowanego na szczycie latarni wieży oraz części ruchomej – zblocza jezdnego (bloczka ruchomego), liny jezdnej, haka i zawiesi . Sprzęt do podnoszenia jest integralną częścią każdej platformy wiertniczej, niezależnie od metody wiercenia.
Wiertnica przeznaczona jest do podnoszenia i opuszczania przewodu wiertniczego i rur okładzinowych do studni, utrzymywania przewodu wiertniczego w stanie zawieszenia podczas wiercenia, a także umieszczania w nim układu jezdnego, rur wiertniczych i części osprzętu niezbędnego do procesu wiercenia . Najpoważniejszym zagrożeniem podczas pracy na platformach wiertniczych jest ich częściowe lub całkowite zniszczenie. Główną przyczyną upadku lub zniszczenia wież jest niedostateczny nadzór nad ich stanem podczas długotrwałej eksploatacji. Z tych powodów wprowadzono zmiany w zasadach bezpieczeństwa przewidujące obowiązkowe przeglądy okresowe wież, w tym całkowity demontaż i rewizję ich części, a także testy z obciążeniem zmontowanych wież.
Ponadto żuraw musi być dokładnie sprawdzany i sprawdzany każdorazowo przed wierceniem, przed uruchomieniem ciągów okładzinowych, uwolnieniem zablokowanego przewodu wiertniczego lub przewodu okładzinowego, w razie wypadku i po silne wiatry(15 m/s dla terenów otwartych, 21 m/s dla terenów leśnych i tajgi, a także przy budowie wieży w wykopie). Wieże typu masztowego montuje się w pozycji poziomej, a następnie podnosi do pozycji pionowej za pomocą specjalnych urządzeń. Transport wieży odbywa się w postaci zmontowanej wraz z platformą jeźdźca w pozycji poziomej na specjalnym urządzeniu transportowym. Jednocześnie system jezdny nie jest demontowany razem z wieżą. Jeżeli ze względu na warunki terenowe nie jest możliwe przetransportowanie wieży w całości, to jest ona demontowana na sekcje i transportowana w częściach transportem uniwersalnym.W praktyce wiertniczej oprócz wież typu masztowego nadal używane, które są montowane metodą odgórną. Przed rozpoczęciem instalacji na podstawie wieży montowana jest winda. Po zakończeniu montażu wieży winda jest demontowana.
Równolegle z montażem wiertnicy i montażem żurawia trwa budowa konstrukcji przyodwiertowych. Należą do nich następujące konstrukcje: 1) Wiata reduktora (agregatu), przeznaczona do osłony silników i mechanizmów przekładni wciągarki. Jest on przymocowany do wieży od strony jej tylnego panelu w kierunku przeciwnym do chodników. Wymiary szopy zębatej zależą od rodzaju instalacji. 2) Wiata pompowa na pompy wiertnicze i urządzenia energetyczne. Jest zbudowany albo jako przedłużenie do boku latarni wieży szopowej, albo osobno do boku wieży. Ściany i dach wiaty przekładniowej i pompowej w zależności od konkretnych warunków osłonięte są płytami, tekturą falistą, osłonami z trzciny, tkaninami gumowymi lub folią polietylenową. Korzystanie z niektórych platform wiertniczych wymaga połączenia szopy z przekładnią i pomp. 3) Most odbiorczy przeznaczony do układania rur wiertniczych i innych rur oraz przemieszczania po nim sprzętu, narzędzi, materiałów i części zamiennych. Mosty przyjmujące są poziome i nachylone. Wysokość montażu pomostów odbiorczych jest regulowana przez wysokość montażu ramy wiertnicy. Szerokość mostów odbiorczych do 1,5...2 m, długość do 18 m. 4) System urządzeń do oczyszczania płuczki wiertniczej oraz magazyny chemii i materiałów sypkich. 5) Szereg konstrukcji pomocniczych podczas wiercenia: na napędzie elektrycznym – platformy transformatorowe, na silnikach spalinowych (ICE) – platformy, na których znajdują się zbiorniki na paliwa i smary itp.
System podróżny
W procesie wiercenia studni system podnoszenia wykonuje różne operacje. W jednym przypadku służy do potykania się w celu wymiany zużytego wiertła, opuszczania, podnoszenia i utrzymywania ciężaru przewodów wiertniczych podczas drążenia, łowienia lub innych prac w studni, a także do opuszczania rur osłonowych. W innych przypadkach zapewnia wytworzenie na haku siły niezbędnej do wyciągnięcia zablokowanego przewodu wiertniczego ze studni lub w razie wypadku z nim. Aby zapewnić wysoką wydajność w tych różnych pracach, system podnoszący ma dwa rodzaje prędkości haka podnoszącego: techniczną do wyzwalania i technologiczną do innych operacji.
![]() |
Ze względu na zmianę ciężaru przewodu wiertniczego podczas podnoszenia, aby skrócić czas do minimum, system podnoszenia musi mieć możliwość zmiany prędkości podnoszenia w zależności od obciążenia. Służy również do przytrzymywania przewodu wiertniczego opuszczonego do studni podczas wiercenia.
System podnoszenia instalacji (rys. III.1) to mechanizm wciągnika łańcuchowego, składający się z bloku koronowego 4, blok podróżny (ruchomy) 2, Stalowa lina 3, co jest elastycznym połączeniem między wyciągami 6 oraz mechanizm 7 do mocowania nieruchomego końca liny. blok korony 4 zainstalowany na górnej platformie wiertnicy 5. ruchomy koniec ALE lina 3 przymocowany do bębna wyciągarki 6, i stały koniec B- przez mocowanie 7 do podstawy wieży. Do bloku jezdnego przymocowany jest hak 1 , na którym na linkach zawieszona jest winda na rury lub krętlik. Obecnie zblocze jezdne i hak podnoszący są w wielu przypadkach połączone w jeden mechanizm - zblocze hakowe.
Drawworks
Wciągarka jest głównym mechanizmem układu podnoszenia wiertnicy. Przeznaczony jest do wykonywania następujących operacji: opuszczanie i podnoszenie rur wiertniczych i osłonowych; utrzymywanie ciężaru przewodu wiertniczego podczas wiercenia lub płukania studni, podnoszenie przewodu wiertniczego i rur podczas przedłużania, ; przeniesienie obrotu na wirnik; układanie i wyłamywanie rur; prace pomocnicze przy wciąganiu narzędzi, sprzętu, rur itp. do wiertnicy; podnoszenie zmontowanej wieży do pozycji pionowej.
Wyciąg składa się ze spawanej ramy, na której zamontowane są wały podnoszące i napędowe, skrzynia biegów, układ hamulcowy wraz z hamulcem głównym (taśmowym) i pomocniczym (regulacyjnym) oraz pulpit sterowniczy. Wszystkie mechanizmy są osłonięte osłonami bezpieczeństwa. Wał podnoszący wciągarki, otrzymując obrót ze skrzyni biegów, zamienia ruch obrotowy napędu na ruch postępowy liny jezdnej, której ruchomy koniec jest zamocowany na bębnie wału podnoszącego. Załadowany hak podnosi się wraz ze zużyciem energii, w zależności od ciężaru unoszonych rur, i opada pod wpływem ciężaru własnego rur lub jezdnego bloku, haka i windy, gdy winda zjeżdża na następną świecę.
Wciągarki są wyposażone w urządzenia do dostarczania mocy podczas podnoszenia liny oraz urządzenia hamujące do pochłaniania uwolnionej energii podczas jej opuszczania. Aby zwiększyć wydajność podczas podnoszenia haka za pomocą nieobciążonej windy lub kolumny o zmiennej wadze, wciągarki lub ich napędy są wielobiegowe. Przełączanie z wysokiej prędkości na niską prędkość i odwrotnie odbywa się za pomocą ciernych sprzęgieł operacyjnych, zapewniających płynne włączanie i minimalny czas poświęcony na te operacje. Podczas podnoszenia kolumn o różnym ciężarze prędkości w skrzyniach biegów są okresowo przełączane. Sterowanie prędkością roboczą skrzynki nie jest wymagane.
Moc przekazywana do wciągarki charakteryzuje jej główne właściwości eksploatacyjne i techniczne oraz jest parametrem klasyfikacyjnym.
Wirniki są przeznaczone do obracania pionowo zawieszonego przewodu wiertniczego lub pochłaniania reaktywnego momentu obrotowego podczas wiercenia za pomocą silników wiertniczych. Służą również do podtrzymywania ciężaru wiertła lub żyłek okładzinowych zamontowanych na stole, na podnośniku lub klinach. Wirniki są również używane do łamania i uzupełniania rur podczas potykania się, wędkowania i operacji awaryjnych. Wirnik jest niejako reduktorem stożkowym, którego napędzane koło stożkowe jest zamontowane na tulei połączonej ze stołem. Oś pionowa stołu znajduje się wzdłuż osi studni.
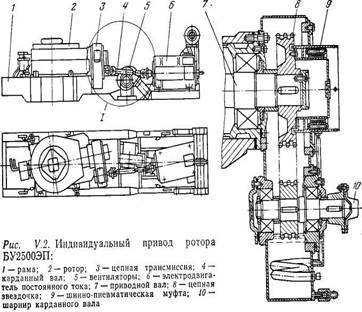
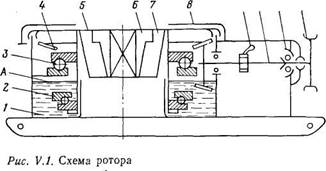
na głównym 3 i pomocniczym 2 wsporniki montowane w obudowie 1, który jednocześnie tworzy kąpiel olejową do smarowania przekładni i łożysk.
Blat stołu jest chroniony płotem. 8. wał napędowy o dużej prędkości 10 umieszczony poziomo na łożyskach 11, postrzeganie obciążeń promieniowych i poziomych. Wał 10 napędzane: obrotowo z koła łańcuchowego 12 lub za pomocą jarzma wału kardana znajdującego się na końcu wału. Wirnik wyposażony jest w stoper 9, po włączeniu obrót stołu staje się niemożliwy. Mocowanie stołu wirnika jest konieczne podczas wyzwalania i wiercenia za pomocą silników wiertniczych w celu wyczuwania reaktywnego momentu obrotowego.
Pompy błotne i wyposażenie układu cyrkulacyjnego
Pompy błotne i system cyrkulacyjny pełnią następujące funkcje:
Wstrzyknięcie płynu wiertniczego do przewodu wiertniczego w celu zapewnienia cyrkulacji w odwiercie podczas wiercenia oraz skutecznego oczyszczenia dna i wiertła z zwiercin, płukania, likwidacji wypadków, wytworzenia szybkości wznoszenia płynu w pierścieniu wystarczającej do doprowadzenia skały do powierzchnia;
Hydrauliczne zasilanie świdra, zapewniające wysokie natężenie przepływu (do 180 m / s) roztworu z jego dysz w celu częściowego zniszczenia skały i oczyszczenia dna z wywierconych cząstek;
Zasilanie hydraulicznego silnika wgłębnego.
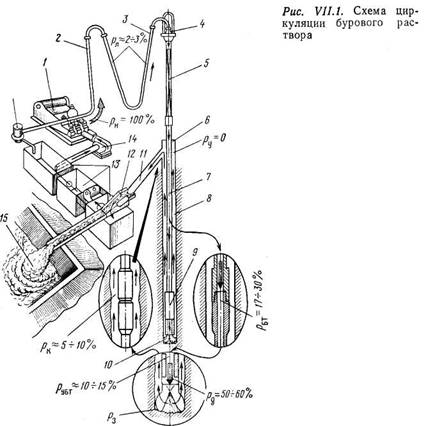
Podczas procesu wiercenia w większości przypadków roztwór krąży w obiegu zamkniętym. Ze zbiorników 13 oczyszczony i przygotowany roztwór dostaje się do pomp wspomagających 14, które podają go do pomp wiertniczych /. Te ostatnie pompują roztwór pod wysokim ciśnieniem (do 30 MPa) przez przewód tłoczny, przez pion 2, elastyczny rękaw 3, obracać 4, Kelly 5 tys studnia 6. Część ciśnienia pomp jest wykorzystywana do pokonania oporów w systemie gruntowym. Następnie płyn wiertniczy przechodzi przez przewód wiertniczy 7 (rury wiertnicze, kołnierz wiertniczy i silnik wiertniczy) 9) do bitu 10. Na tej ścieżce ciśnienie roztworu spada z powodu wydatkowania energii na pokonanie oporów hydraulicznych.
Następnie płyn wiertniczy, ze względu na różnicę ciśnień wewnątrz rur wiertniczych i na dnie odwiertu, z dużą prędkością wypływa z dysz wiertła, oczyszczając dno i świder z nacięć. Reszta energii płynu jest zużywana na podnoszenie sadzonek i pokonywanie oporu w pierścieniu pierścieniowym 8.
Podniesiony na powierzchnię do ust 6 zużyty roztwór przechodzi przez rynny 11 do jednostki czyszczącej 12, skąd są przeniesione do stodoły 15 ścinki, piasek, muł, gaz i inne zanieczyszczenia dostają się do zbiorników 13 z urządzeniami 16 do przywrócenia jego parametrów i jest ponownie wysyłany do pomp wspomagających.Linia wtryskowa składa się z rurociągu wysokiego ciśnienia, który transportuje roztwór z pomp / do pionu 2 i elastyczny rękaw 3, podłączenie pionu 2 z krętlikiem 4. Linia ciśnieniowa jest wyposażona w zawory i oprzyrządowanie. Do pracy na obszarach o zimnym klimacie zapewniony jest system ogrzewania rurociągów.
Układ spustowy wyposażony jest w urządzenia do czyszczenia i przygotowania płuczki wiertniczej, zbiorników, linii ssawnej, filtrów, wtrysku pompy odśrodkowe, zawory i pojemniki do przechowywania roztworu.
krętliki
Krętlik jest łącznikiem pośrednim pomiędzy poruszającym się progresywnie blokiem jezdnym z hakiem, tuleją wiertniczą i obracającym się żerdzią wiertniczą, która jest połączona przez prowadzącą rurę z wałem obrotowym za pomocą gwintu blokującego. Aby zapewnić dopływ płynu wiertniczego lub gazu, ruchomy krętlik jest połączony z przewodem ciśnieniowym za pomocą elastycznego węża wiertniczego, którego jeden koniec jest przymocowany do wylotu obrotowego, a drugi do pionu.
Krętliki posiadają urządzenia do napełniania, spuszczania oleju i kontroli jego poziomu, a także odpowietrznik do równoważenia z ciśnieniem atmosferycznym pary wewnątrz korpusu, która powstaje podczas nagrzewania podczas pracy. Z tego urządzenia nie wycieka olej podczas transportu krętlika w pozycji poziomej.
Wielkość krętlika zależy od obciążenia dynamicznego, jakie może przyjąć podczas obrotu przewodu wiertniczego, dopuszczalnego obciążenia statycznego i prędkości obrotowej, maksymalnego ciśnienia roboczego pompowanej płuczki wiertniczej, masy i gabarytów. Każdy krętlik ma standardowy gwint blokujący stożkowy lewy do połączenia z prowadzącą rurą w dwóch do trzech rozmiarach. Korpus krętlika wykonany jest w opływowym kształcie, dzięki czemu podczas ruchu nie przylega do części wieży. Krętliki przystosowane są do transportu dowolnym środkiem transportu bez opakowania.
Napędy napędów wiertnic
Napęd wiertnicy to zespół silników i przekładni, które regulują ich pracę oraz urządzenia zamieniające energię cieplną lub elektryczną na energię mechaniczną, sterujące energią mechaniczną i przekazujące ją do urządzeń wykonawczych – pomp, wirnika, wciągarki itp. Moc napędu (na wejściu do przekładni) charakteryzuje jego główne właściwości użytkowe i techniczne oraz jest parametrem klasyfikacyjnym (głównym).
W zależności od zastosowanego źródła energii pierwotnej napędy dzielą się na autonomiczne, niezależne od systemu zasilania oraz nieautonomiczne, zależne od systemu zasilania, zasilane z przemysłowych sieci elektrycznych. Napędy autonomiczne obejmują silniki spalinowe (ICE) z przekładnią mechaniczną, hydrauliczną lub elektryczną. Napędy nieautonomiczne obejmują: silniki elektryczne prąd stały zasilane z przemysłowych sieci prądu przemiennego.
Zgodnie z kinematykami instalacji napęd może mieć trzy główne wersje: indywidualną, grupową i kombinowaną lub mieszaną.
Napęd indywidualny- każdy siłownik (wyciągarka, pompa lub wirnik) jest napędzany niezależnie od siebie silnikami elektrycznymi lub silnikami spalinowymi. Ten rodzaj napędu jest szerzej stosowany w silnikach elektrycznych. Podczas jego używania uzyskuje się wysoką manewrowość w rozmieszczeniu i rozmieszczeniu sprzętu wiertniczego na podstawach podczas instalacji.
Dysk grupowy- kilka silników jest połączonych przekładnią sumującą i napędza kilka siłowników. Stosowany jest w silnikach spalinowych.
Połączony napęd- zastosowanie napędów indywidualnych i grupowych w jednej instalacji. Na przykład pompy są napędzane przez pojedyncze silniki, podczas gdy wciągarka i wirnik napędzane są przez wspólny silnik. We wszystkich przypadkach charakterystyka napędu musi w pełni odpowiadać wymaganym charakterystykom siłowników.
Odbiorcami energii wiertni są:
w procesie wiercenia - pompy płuczkowe, wirnik (w przypadku wiercenia obrotowego), urządzenia do przygotowania i oczyszczania płuczki wiertniczej z zwiercin; kompresor, pompa wody itp.;
przy opuszczaniu i podnoszeniu ciągu rurowego - wciągarka, sprężarka, pompa wodna i zmechanizowany klucz.
Napędy dzielą się również na napędy główne (napędy wciągarki, pomp i wirnika) oraz napędy pomocnicze (napędy innych urządzeń i mechanizmów instalacji). Moc pobierana przez urządzenia pomocnicze nie przekracza 10-15% mocy pobieranej przez urządzenia główne.
Charakterystyka elastyczności- zdolność napędu mocy do automatycznego lub przy udziale operatora w procesie szybkiego dostosowywania się do zmian obciążeń i prędkości obrotowych siłowników. Elastyczność charakterystyki zależy od współczynnika adaptacyjności, zakresu regulacji częstotliwości obrotów wałów napędu oraz reakcji przepustnicy silnika.
Współczynnik elastyczności Charakterystykę określa stosunek zmiany prędkości do spowodowanej nią odchyłki momentu obciążenia. Jest proporcjonalny do przełożenia i odwrotnie proporcjonalny do współczynnika przeciążenia.
ulec poprawie nazywany intensywnością realizacji stanów nieustalonych, czyli czasu, w którym silnik i moc napędu reagują na zmiany obciążenia i zmieniają prędkość.
Zdolność adaptacji- właściwość napędu do zmiany momentu obrotowego i prędkości w zależności od momentu oporu. Samoadaptacja - właściwość silnika umożliwiająca dostosowanie się do obciążenia zewnętrznego. Sztuczna adaptacyjność - właściwość przekładni polegająca na dostosowaniu charakterystyki silnika do zmiany obciążenia zewnętrznego.
Sprzęt do uszczelniania głowic
Obecnie przy wierceniu nie tylko odwiertów poszukiwawczych, ale również produkcyjnych, szeroko stosowany jest sprzęt do uszczelniania głowic. Wcześniej sprzęt ten był używany głównie do kontroli emisji cieczy i gazów podczas AHRP. W związku ze stosowaniem lżejszych płuczek wiertniczych, ciśnienie w odwiercie podczas procesu wiercenia regulowane jest za pomocą prezerwatorów. Zmieniły się wymagania dotyczące ochrony środowiska i wnętrzności ziemi.
Aby uszczelnić głowicę odwiertu, stosuje się trzy rodzaje prezerwatyw: taran - głuche lub na wylot, aby całkowicie zablokować otwór lub przestrzeń pierścieniową, jeśli w odwiercie znajduje się przewód rurowy; uniwersalny - do zamknięcia otworu w studni, jeśli zawiera jakaś część przewodu wiertniczego: zamek, rura, Kelly; obrotowy - do uszczelniania głowicy z obracającą się w niej rurą lub rurą prowadzącą. Ani taran, ani uniwersalne ograniczniki nie są zaprojektowane do obracania sznurka, jeśli są całkowicie zamknięte.
Baran BOP
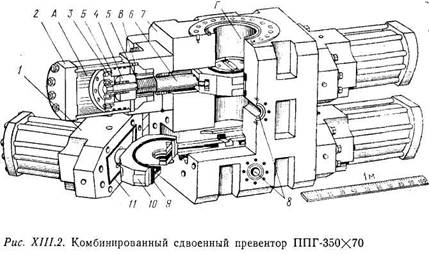
Tłok pomocniczy 4 również porusza się w prawo, a w końcowej pozycji naciska na pierścień zatrzasku 5 i tym samym naprawia matryce 10 w stanie zamkniętym, co wyklucza ich spontaniczne otwarcie. Aby otworzyć dziurę G beczkę, musisz przesunąć matryce w lewo. W tym celu płyn sterujący musi być dostarczony pod ciśnieniem do wnęki B, która porusza tłokiem pomocniczym 4 według magazynu 6 w lewo i otwiera zatrzask 5. Ten tłok, po osiągnięciu ogranicznika w tłoku głównym 3, przesuwa go w lewo, odsłaniając w ten sposób kości. W takim przypadku płyn kontrolny znajdujący się w zagłębieniu £ jest wyciskany do układu kontrolnego.
umiera 10 Zaślepki można wymienić w zależności od średnicy uszczelnianych rur. Koniec matryc na obwodzie uszczelniony jest gumowym mankietem 9, pokrywa 1 - uszczelka //. Każdy z prewencji jest kontrolowany niezależnie, ale oba tarany każdego prewencji działają jednocześnie. dziury 8 w obudowie 7 służą do połączenia zabezpieczenia z kolektorem. Dolny koniec obudowy jest przymocowany do kołnierza głowicy, a uniwersalny ogranicznik jest przymocowany do jego górnego końca.
Jak widać, siłownik sterowany hydraulicznie BOP powinien mieć dwie linie sterujące: jedną do sterowania ustalaniem położenia siłowników, drugą do ich przesuwania. BOP sterowane hydraulicznie są stosowane głównie w wierceniu na morzu. W niektórych przypadkach dolny profilakt wyposażony jest w bijaki z nożami do cięcia rur w studni.
Uniwersalne środki zapobiegawcze
Uniwersalny ogranicznik został zaprojektowany w celu poprawy niezawodności uszczelnienia głowicy. Jego głównym elementem roboczym jest mocna pierścieniowa uszczelka elastyczna, która w stanie otwartym zapobiega przepuszczaniu przewodu wiertniczego, a w przypadku zamknięcia zapobiegacza ściska się, w wyniku czego uszczelka gumowa ściska rurę (kelly). , zamek) i uszczelnia przestrzeń pierścieniową między przewodem wiertniczym a obudową . Elastyczność gumowej uszczelki umożliwia zamknięcie prezerwatywy na rurach o różnych średnicach, na zamkach i kołnierzach wiertniczych. Zastosowanie uniwersalnych prezerwatyw umożliwia obracanie i chodzenie sznurka z uszczelnioną szczeliną pierścieniową.
O-ring jest ściskany albo przez bezpośrednią siłę hydrauliczną działającą na element uszczelniający, albo przez tę siłę działającą na uszczelkę przez specjalny tłok pierścieniowy.
Uniwersalne prezerwatywy z kulistym elementem uszczelniającym i stożkowym uszczelnieniem są produkowane przez VZBT.
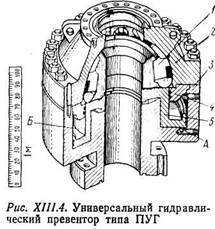
Podczas składania wniosku Działający płyn pod nurnikiem 5 przez otwór w korpusie prewektora, nurnik przesuwa się do góry i ściska uszczelkę / wokół kuli tak, że rozszerza się w kierunku środka i ściska rurę wewnątrz uszczelki pierścieniowej. W takim przypadku ciśnienie płynu wiertniczego w odwiercie będzie oddziaływać na tłok i ściskać uszczelnienie. Jeśli w studni nie ma kolumny, uszczelka całkowicie zakrywa otwór. Górna komora B służy do otwierania prezerwatywy. Po wtryśnięciu do niego oleju tłok przesuwa się w dół, wypierając płyn z komory A do przewodu drenażowego.
Prewencja rotacyjna
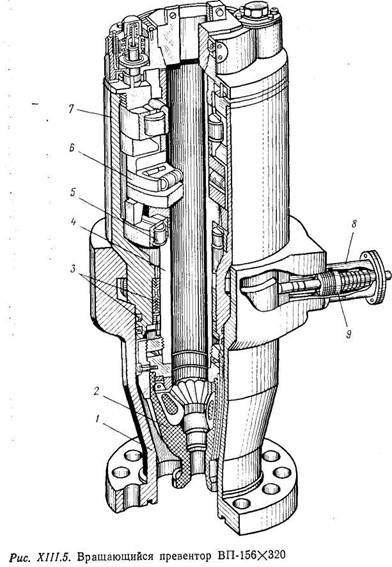
Zapobieganie rotacji służy do uszczelniania głowicy podczas wiercenia podczas obrotu i ruchu posuwisto-zwrotnego przewodu wiertniczego, a także podczas wyzwalania i wzrostu ciśnienia w odwiercie. Ten prewenator uszczelnia rury kelly, lock lub wiertła, umożliwia podnoszenie, opuszczanie lub obracanie przewodu wiertniczego, wiercenie z płukaniem wstecznym, z napowietrzonymi płuczkami, z przedmuchem gazowym, z systemem równoważenia ciśnienia hydrostatycznego na formacji, badanie formacji w proces pokazów gazowych.
II . Część technologiczna
1. Wiercenie szybów naftowych i gazowych
Zapoznanie z metodami ręcznego posuwu wiertła, wiercenie z regulatorem posuwu wiertła, szkolenie z wiercenia z rotorem.
Kiedy bit jest podawany na dno, konieczne jest wytworzenie na nim pewnego obciążenia. Ta operacja jest wykonywana z konsoli wiertła. Wiertarka za pomocą tak zwanego buławy opuszcza narzędzie, a następnie stopniowo, bardzo powoli przenosi ciężar z haka na wiertło. Obciążenie linii przewodowej jest określane przez wskaźnik wagi. Na wskaźniku cena podziału może być inna. Gdy system jezdny jest zawieszony, ale hak nie jest obciążony, wskaźnik wagi pokaże wartość odpowiadającą wadze systemu jezdnego.
WOB powinno być równe nie więcej niż 75% ciężaru sznurka kołnierza wiertniczego. Na przykład istnieje układ: 100 m kołnierza wiertniczego i 1000 m rur wiertniczych. Niech waga struny UBT będzie wynosić 150 kN, a waga struny BT 300 kN. Całkowita waga BC w tym przypadku wyniesie 450 kN. Około 2/3 masy kołnierza wiertniczego musi zostać podane do uboju, tj. w tym przypadku 100 kN. W tym celu sznurek jest płynnie opuszczany o 9 m (długość rury do układania w stos) na dno. Moment kontaktu wędzidła z dnem określa wskaźnik ciężaru: strzałka pokazuje spadek ciężaru na haczyku. Następnie należy bardzo powoli zwolnić wciągarkę i stopniowo obciążać wędzidło, aż strzałka na wskaźniku wagi wskaże 35 ton. na wskaźniku masy oscylacja strzałki nie zawsze może być zauważalna. Pokazuje, ile działek przeszła strzałka na wskaźniku wagi, tj. 3 działki Wernera są równe 1 działce wskaźnika masy.
Wirniki służą do przenoszenia obrotów na przewód wiertniczy podczas wiercenia, aby utrzymać go w zawieszeniu podczas podróży w obie strony i prac pomocniczych.
Wirnik to skrzynia biegów, która przenosi obrót na pionowo zawieszoną kolumnę z poziomego wału transmisyjnego. Rama wirnika odbiera i przenosi na podstawę wszystkie obciążenia, które występują podczas operacji wiercenia i wyzwalania. Wewnętrzna wnęka łóżka to kąpiel olejowa. Na zewnętrznym końcu wału wirnika, na kluczu, może znajdować się koło łańcuchowe lub półsprzęgło wału kardana. Podczas odkręcania świdra lub w celu uniemożliwienia obrotu przewodu wiertniczego pod działaniem nieaktywnego momentu, wirnik jest blokowany zapadką lub mechanizmem blokującym. Gdy obrót jest przenoszony na wirnik z silnika przez wciągarkę, wirnik prędkość zmienia się za pomocą mechanizmów transmisyjnych wciągarki lub zmieniając koła zębate. Aby nie łączyć pracy wciągarki z pracą wirnika, w niektórych przypadkach podczas wiercenia obrotowego stosuje się indywidualny napęd wirnika, czyli nie połączony z wciągarką.
W otwór przelotowy wirnika wkładane są 2 wkładki. Następnie, w zależności od średnicy rur, na wirnik umieszcza się odpowiednie kliny, które są przymocowane do czterech równoleżników. Równolegle z kolei są wprawiane w ruch za pomocą RCC (pneumatyczne kliny wirnika), które są zamontowane po przeciwnej stronie wału wirnika. Za pomocą pedału, który znajduje się na konsoli, wiertarka podnosi lub opuszcza kliny.
Po rozpoczęciu wiercenia kliny są usuwane z wirnika, uwalniając w ten sposób kwadratowy otwór wkładek. Następnie w tym otworze mocuje się tak zwany kelbush - nakrętkę ruchomo zamocowaną na prowadzącej rurze, która porusza się wzdłuż niej w górę iw dół. Ponadto za pomocą przekładni ustawiane są niezbędne obroty wirnika i jest on napędzany z konsoli wiertła.
Zapoznanie z metodyką racjonalnego rozwoju bitów.
Aby racjonalnie wypracować bit, konieczne jest spełnienie wskaźnika penetracji. W miarę pogłębiania się odwiertu narzędzie do cięcia skał zużywa się, a aby zapobiec występowaniu zużycia z wyprzedzeniem, należy obserwować tryb wiercenia.
Tryb wiercenia obejmuje obroty wirnika lub silnika wgłębnego, WOB i ciśnienie pompy (na pionie). Tak więc, dla prawidłowego rozwoju wiertła, obciążenie na nim powinno wynosić więcej niż 75% masy sznurka wiertła. Przeciążenie wiertła może spowodować jego przedwczesne zużycie lub pęknięcie stożka, a niedociążenie może prowadzić do spadku penetracji. Prędkość wirnika i ciśnienie na pionie są ustawiane zgodnie z linią geologiczno-techniczną.
W celu racjonalnego rozwoju wędzidła konieczne jest podawanie go do dna bez obracania i włączanie obrotów dopiero po kontakcie z dnem. Ale przed rozpoczęciem wiercenia konieczne jest „dotarcie” wiertła na 30-40 minut, aby się dotarło. Jednocześnie ciężar na wiertle powinien być niewielki - około 3-5 t. Przy wierceniu za pomocą turbowiertarki lub silnika wiertniczego śrubowego wiertło jest podawane do odwiertu już w obrocie. W takim przypadku można albo zatrzymać płukanie i opuścić wiertło do dołu, albo bez zatrzymywania płukania stopniowo ładować wiertło do wymaganej wartości.
Kodowanie zużycia wiertła stożkowego:
B - zużycie broni (co najmniej jedna korona)
B1 - zmniejszenie wysokości zęba o 0,25%
B2 - redukcja wysokości zębów o 0,5%
B3 - zmniejszenie wysokości zęba o 0,75%
B4 - całkowite zużycie zębów
C - ukruszenie zęba w%
P - zużycie podpory (co najmniej jeden frez)
P1 - luz promieniowy frezu względem osi czopu dla bitów
średnica mniejsza niż 216 mm 0-2 mm; dla bitów większych niż
216mm 0-4mm
P2 - luz promieniowy frezu względem osi czopu dla bitów
średnica mniejsza niż 216 mm 2-5 mm; dla bitów większych niż
216mm 4-8mm
P3 - luz promieniowy frezu względem osi czopu dla bitów
średnica mniejsza niż 216 mm większa niż 5 mm; dla bitów większych niż
216 mm ponad 8 mm
P4 - niszczenie elementów tocznych
K - zacinanie się frezów (ich ilość podana jest w nawiasach)
D - redukcja średnicy wiertła (mm)
A - zużycie awaryjne (w nawiasach podana jest ilość pozostałych noży i łap)
AB (A1) - pęknięcie i pozostawienie górnej części stożka na dole
ASh (A2) - w rozbiciu i pozostawieniu stożka na dole
AC (A3) - zostawiając łapę na dole
Przyczyny nieprawidłowego zużycia wierteł stożkowych:
1) Duża ilość złamanych zębów:
Zły wybór bitu
Nieprawidłowe włamanie bitu
Nadmierna prędkość
Obróbka metali
2) Silne zużycie na średnicy:
Wysoka prędkość
Wyciskanie szyszek w wyniku zejścia do pnia o zmniejszonej średnicy
3) Erozja korpusu stożka:
Duże zużycie płynu do płukania
4) Nadmierne zużycie łożyska:
Brak stabilizatora nad wiertłem lub między kołnierzami wiertła
Wysoka prędkość
Znaczący czas wiercenia mechanicznego
5) Zablokowanie przestrzeni międzykoronowych w frezach ze skałą wierconą i fazą stałą:
Niedostateczne spożycie trzustki
Dłuto jest przeznaczone do twardszych formacji
Wiertło zostało opuszczone do strefy dolnego otworu wypełnionego sadzonkami
6) Duża liczba utraconych zębów:
Erozja korpusu stożka
Znaczący czas wiercenia mechanicznego
Wykonywanie podstawowej pracy z oprogramowaniem open source za pomocą specjalny sprzęt
Główną jednostką w realizacji wycieczki jest wyciągarka, która jest napędzana napędem mechanicznym. W celu lepszego wykorzystania mocy podczas podnoszenia haka przy różnych obciążeniach, przekładnie napędu wciągarki lub napęd wciągarki powinny być wielobiegowe. Wciągarka musi szybko przełączać się z wysokich prędkości podnoszenia na niskie iz powrotem, zapewniając zaplanowane włączenie przy minimalnym czasie spędzonym na tych operacjach. W przypadku sklejania się i napinania sznurka należy szybko zwiększyć siłę naciągu podczas podnoszenia. Przełączanie prędkości podnoszenia kolumn o różnych masach odbywa się okresowo.
Wciągarki pomocnicze i rozgałęźniki pneumatyczne służą do wykonywania prac związanych z wciąganiem ładunków oraz przykręcaniem i przykręcaniem rur podczas SPO.
Młoty pneumatyczne przeznaczone są do odkręcania połączeń narzędziowych rur wiertniczych. Pneumobrancher składa się z cylindra, w którym porusza się tłok z prętem. Cylinder jest zamknięty na obu końcach zatyczkami, z których jedna ma uszczelkę prętową. Metalowy kabel jest przymocowany do pręta po przeciwnej stronie tłoka, którego drugi koniec jest umieszczony na kluczu maszyny. Pod działaniem sprężonego powietrza tłok porusza się i obraca klucz maszyny przez kabel. Maksymalna siła wytwarzana przez cylinder pneumatyczny przy ciśnieniu sprężonego powietrza 0,6 MPa wynosi 50...70 kN. Skok tłoka (pręta) cylindra pneumatycznego wynosi 740 ... 800 mm.
Kompleks mechanizmów ASP jest przeznaczony do mechanizacji i częściowej automatyzacji operacji wyzwalania. To zapewnia:
- połączenie w czasie podnoszenia i opuszczania ciągu rurowego i nieobciążonego podnośnika z operacjami montażu stojaka na stojaku, zdejmowania go ze stojaka oraz przykręcania lub skręcania stojaka z ciągiem wiertniczym;
- mechanizacja montażu świec na świeczniku i ich wyjmowanie do środka, a także chwytanie lub zwalnianie ciągu rury wiertniczej przez automatyczny podnośnik.
Mechanizmy ASP obejmują: mechanizm podnoszący (podnoszenie i opuszczanie oddzielnie obracanej świecy); mechanizm chwytający (chwytanie i przytrzymywanie odkręconej świecy podczas podnoszenia, opuszczania, przenoszenia jej z wirnika na świecznik i odwrotnie); mechanizm umieszczania (przesuwanie świecy ze środka dołka iz powrotem); centralizator (trzymający górną część świecy na środku wieży podczas wkręcania i wkręcania); automatyczny podnośnik (automatyczne przechwytywanie i zwalnianie kolumny BT podczas schodzenia i wynurzania); magazynek i świecznik (trzymający odkręcone świece w pozycji pionowej).
W pracy kompleksu mechanizmów takich jak ASP-ZM1, ASP-ZM4. ASP-ZM5 i ASP-ZM6 wykorzystują klucz AKB-ZM2 oraz pneumatyczny uchwyt klinowy BO-700 (z wyjątkiem ASP-ZM6, do którego stosowany jest uchwyt PKRBO-700).
Przygotowanie rury do przeciągania, montaż elewatora na wirniku, wyjęcie go z wirnika, umieszczenie rur na klinach
Przed wciągnięciem rur na platformę należy dokonać wizualnej kontroli korpusu rury i gwintów. W celu dokładnej analizy wzywany jest zespół defektoskopów, którzy za pomocą przyrządów określają przydatność rur do zastosowania na platformie wiertniczej. Ponadto konieczne jest, w razie potrzeby, oczyszczenie połączeń gwintowych rur, a następnie nasmarowanie ich smarem grafitowym lub smarem plastycznym. Następnie rury są dostarczane do mostów odbiorczych.
Podczas wiercenia rury wiertnicze są przeciągane jedna po drugiej z chodników do wirnika za pomocą pomocniczej wciągarki. Następnie dostarczoną rurę nakręca się na sznurek, a dno pogłębia się o długość przedłużonej rury.
Podnoszenie i opuszczanie rur wiertniczych w celu wymiany zużytego wiertła składa się z tych samych powtarzających się operacji. Ponadto maszyny obejmują operacje podnoszenia świecy ze studni i pustego elewatora. Wszystkie inne operacje wykonywane są maszynowo lub ręcznie, wymagając dużego wysiłku fizycznego. Obejmują one:
· podczas podnoszenia: lądowanie kolumny na windzie; odkręcanie połączenia gwintowego; instalowanie świecy na świeczniku; pusty zjazd windy; przeniesienie ogniw do załadowanej windy i podniesienie kolumny na wysokość świecy;
· przy schodzeniu: wyjęcie świecy zza palca iz świecznika; przykręcanie świecy do kolumny; opuszczanie sznurka do studni; lądowanie kolumny na windzie; transfer linków do bezpłatnej windy. Urządzenia do chwytania i zawieszania kolumn różnią się wielkością i nośnością.
Standardowo sprzęt ten produkowany jest do rur wiertniczych o wymiarach 60, 73, 89, 114, 127, 141, 169 mm o nośności znamionowej 75, 125, 140, 170, 200, 250, 320 ton. rury o średnicy od 194 do 426 mm, kliny w czterech rozmiarach: 210, 273, 375 i 476 mm, przeznaczone do udźwigu od 125 do 300 ton.
Elewator służy do chwytania i utrzymywania ciężaru rur przewodu wiertniczego (obudowy) podczas operacji wyzwalania i innych prac na platformie wiertniczej. Stosowane są różne typy wind, różniące się wielkością w zależności od średnicy rur wiertniczych lub osłonowych, ładowności, zastosowania konstrukcyjnego i materiału do ich wykonania. Winda jest zawieszona na haku za pomocą zawiesi.
Kliny do rur wiertniczych służą do zawieszenia narzędzia wiertniczego na stole wirnika. Wkłada się je w stożkowy otwór wirnika. Zastosowanie klinów przyspiesza prace przy operacjach wyzwalania. Ostatnio szeroko stosowane są automatyczne uchwyty klinowe z napędem pneumatycznym typu PKR (w tym przypadku kliny wprowadzane są do wirnika nie ręcznie, ale za pomocą specjalnego napędu, którym steruje konsola wiertarki).
Do opuszczania cięższych strun osłonowych stosuje się kliny z nierozszczepionym korpusem. Montowane są na specjalnych podkładkach nad głowicą odwiertu. Klin składa się z masywnego korpusu, który przejmuje ciężar rur osłonowych. Wewnątrz korpusu znajdują się matryce przeznaczone do chwytania rur osłonowych i utrzymywania ich w stanie zawieszonym. Podnoszenie i opuszczanie wykrojników odbywa się poprzez obrócenie uchwytu w jednym lub drugim kierunku wokół klina, co uzyskuje się dzięki obecności nachylonych wycięć korygujących w korpusie, po których rolki wykrojników toczą się za pomocą dźwigni.
Sprawdzenie gwintu zamka, przykręcenie BT za pomocą kluczy bateryjnych, ponowne założenie i odpięcie połączeń zamka za pomocą kluczy UMK
W procesie SPO konieczne jest wielokrotne wkręcanie i odkręcanie rur. Aby uprościć te operacje, wiertnica wyposażona jest w specjalny sprzęt. Do skręcania i odkręcania rur wiertniczych i osłonowych służy specjalne narzędzie. Jako takie narzędzie wykorzystywane są różne klawisze. Niektóre z nich przeznaczone są do skręcania, a inne do mocowania i odłączania połączeń gwintowych kolumny. Zazwyczaj lekkie, uniwersalne klucze do wstępnego montażu są przeznaczone do zamków o jednej średnicy, a ciężkie klucze maszynowe do mocowania i połączeń niegwintowanych są przeznaczone do dwóch, a czasem większej liczby rur wiertniczych i zamków.
Do ręcznego obracania rur służy klucz łańcuchowy. Składa się z uchwytu i łańcuszka z urządzeniem mocującym. Aby uchwycić rurę, łańcuch owija się wokół niej i jest zamocowany na górze uchwytu. Praca z kluczem łańcuchowym jest bardzo czasochłonna, dlatego używany jest inny sprzęt.
Automatyczne kleszcze wiertarskie akumulatora przeznaczone są do zmechanizowanego wkręcania i skręcania rur. Panel sterowania znajduje się na stanowisku wiertnicy i jest wyposażony w dwie dźwignie: jedna steruje ruchem samego klucza do wirnika i z powrotem oraz mechanizmem chwytania rur, a za pomocą drugiej rury są ze sobą skręcane . AKB znacznie upraszcza proces oprogramowania open source.
Operacje mocowania i odkręcania połączeń gwintowych żył wiertniczych i osłonowych wykonywane są za pomocą dwóch kluczy maszynowych UMK; podczas gdy jeden klucz (opóźniający) jest stały, a drugi (przykręcany) jest ruchomy. Klawisze zawieszone są w pozycji poziomej. W tym celu metalowe rolki są wzmacniane na specjalnych „palcach” w pobliżu pokładów i przerzucane są przez nie stalową linką uwiązaną lub jednym pasmem liny jezdnej. Jeden koniec tej liny jest przymocowany do wieszaka na klucze, a drugi koniec jest przymocowany do przeciwwagi, która równoważy klucz i ułatwia przesuwanie klucza w górę lub w dół.
Podczas opuszczania rur wiertniczych i kołnierzy wiertniczych do studni połączenia gwintowane należy dokręcać za pomocą kluczy maszynowych i automatycznych, kontrolując szczelinę między elementami łączącymi i przestrzegając, zgodnie z miernikiem momentu obrotowego, wartości dopuszczalnego momentu obrotowego ustalonej przez aktualną instrukcję.
Kontrola i pomiar BT i kołnierza, montaż BT na świeczniku, przykręcanie i odkręcanie dłut
Przed przystąpieniem do wiercenia należy sprawdzić wszystkie rury znajdujące się na wiertnicy. Specjalna uwaga należy poświęcić na sprawdzenie połączeń gwintowanych. Gwint na rurach wiertniczych zużywa się podczas pracy, dlatego długość gwintu i jego średnicę należy okresowo mierzyć. Odbywa się to za pomocą taśmy mierniczej. Dopuszczalne odchyłki w rozmiarach gwintów wynoszą 3-4 mm. Do sprawdzenia rozmiaru rur służą specjalne szablony. Średnica każdego szablonu odpowiada określonej średnicy rury.
W procesie pogłębiania odwiertu przewód wiertniczy stale się powiększa. W tym celu rurę wiertniczą przeciąga się z pomostów za pomocą wyciągarki pomocniczej do wirnika, zaczepia przez elewator, a następnie nakręca na gwint rury osadzony na klinach.
Gdy konieczne jest podniesienie sznurka, rury odkręca się za pomocą świec, aby skrócić czas podróży. W takim przypadku konieczne jest podniesienie górnego końca rury nad stół wirnika, założenie go na kliny i zamocowanie na podnośniku. Następnie kolumna unosi się na wysokość świecy, siada na klinach, świecę odkręca się kluczem do baterii, nawija palcem jadącego i półzawieszonego i umieszcza na świeczniku. Po wykonaniu niezbędnych operacji (zmiana wiertła, BHA) sznurek jest opuszczany za pomocą świec na głębokość nawiercenia.
Wkręcanie i odkręcanie końcówki stożkowej odbywa się za pomocą podłokietnika. Dłuto montuje się ręcznie lub za pomocą wyciągarki pomocniczej w podłokietniku. Wewnątrz znajdują się 3 występy, które przechodzą między frezami. Następnie uchwyt jest umieszczany na wkładkach wirnika, a wiertło jest przykręcane do kołnierza wiertła lub podpory. Wiertło montuje się na wirniku za pomocą specjalnego stojaka, dzięki czemu nad stołem pozostaje tylko jeden gwint, a następnie nakręca się go na rurę.
Dobrze spłukuje
Płukanie studni jest główną częścią wiercenia. To, jak dobrze studnia zostanie doprowadzona do głębokości projektowej, zależy od prawidłowo dobranej formuły roztworu.
W praktyce wiercenia studni stosuje się różne metody technologiczne do przygotowania płynów wiertniczych.
Najprostszy schemat przepływowy (rys. 7.2) obejmuje zbiornik do mieszania składników płuczki wiertniczej 1, wyposażone w mieszadła mechaniczne i hydrauliczne 9, mikser strumieniowy 4, wyposażony w lej załadowczy 5 i brama przesuwna 8, pompa odśrodkowa lub tłokowa 2 (zwykle jedna z pomp wspomagających) i kolektory.
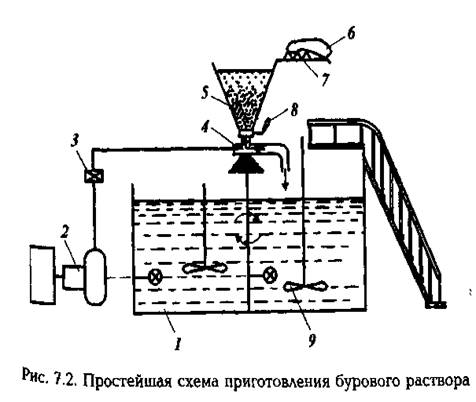
Zgodnie z tym schematem przygotowanie roztworu odbywa się w następujący sposób. w pojemniku 1 wlać obliczoną ilość medium dyspersyjnego (zwykle 20-30 m3) i za pomocą pompy 2 przez linię tłoczną z zaworem 3 jest podawany przez mieszalnik hydroeżektorowy 4 w zamkniętej pętli. Torba 6 lat Materiał sypki transportowany jest ruchomym podnośnikiem lub przenośnikiem na platformę zbiornika, skąd przy pomocy dwóch pracowników jest podawany na platformę 7 i ręcznie przenoszony do środowiska leja 5. Zawiesina jest spuszczana do pojemnika, gdzie jest dokładnie mieszana za pomocą mieszadła mechanicznego lub hydraulicznego 9. Szybkość podawania materiału do komory mieszalnika eżektorowego jest kontrolowana przez zasuwę 8, a podciśnienie w komorze sterowane jest wymiennym dysze ze stopów twardych.
Główną wadą opisywanej technologii jest słaba mechanizacja pracy, nierównomierne dostarczanie składników do strefy mieszania oraz słaba kontrola nad procesem. Zgodnie z opisanym schematem maksymalna szybkość przygotowania roztworu nie przekracza 40 m 3 /h.
Obecnie w praktyce krajowej szeroko stosowana jest progresywna technologia przygotowania roztworów wiertniczych z materiałów sproszkowanych. Technologia opiera się na wykorzystaniu dostępnych na rynku urządzeń: zespołu przygotowania roztworu (BPR), zewnętrznego mieszalnika hydroeżektorowego, dyspergatora hydraulicznego, zbiornika CS, mieszalników mechanicznych i hydraulicznych oraz pompy tłokowej.
Do oczyszczania płuczki wiertniczej z sadzonek stosuje się kompleks różnych urządzeń mechanicznych: sita wibracyjne, hydrocyklonowe separatory szlamu (separatory piasku i mułu), separatory, wirówki. Dodatkowo, w najbardziej niesprzyjających warunkach, przed czyszczeniem z zwiercin płuczka wiertnicza jest poddawana działaniu odczynników flokulacyjnych, które pozwalają na zwiększenie wydajności urządzeń czyszczących.
Pomimo tego, że system czyszczenia jest skomplikowany i kosztowny, w większości przypadków jego zastosowanie jest opłacalne ze względu na znaczne zwiększenie prędkości wiercenia, zmniejszenie kosztów regulacji właściwości płuczki, zmniejszenie stopnia skomplikowanie odwiertu i spełnienie wymagań ochrony środowiska.
W ramach systemu cyrkulacji urządzenia muszą być instalowane w ścisłej kolejności. W takim przypadku schemat przepływu roztworu musi odpowiadać następującemu łańcuchowi technologicznemu: studnia – separator gazu – blok zgrubne czyszczenie z osadu (sito wibracyjne) - odgazowywacz - zespół do dokładnego oczyszczania osadu (separatory piasku i mułu, separator) - zespół do kontroli zawartości i składu fazy stałej (wirówka, hydrocyklonowy separator gliny).
Oczywiście przy braku gazu w płuczce wiertniczej etapy odgazowania są wykluczone; przy stosowaniu roztworu nieważonego z reguły nie stosuje się separatorów glinianych i wirówek; przy czyszczeniu ciężkiej płuczki wiertniczej zazwyczaj wyklucza się hydrocyklonowe separatory szlamu (separatory piasku i mułu). Innymi słowy, każdy sprzęt jest zaprojektowany do pełnienia dość specyficznych funkcji i nie jest uniwersalny we wszystkich geologicznych i technicznych warunkach wiertniczych. Dlatego dobór sprzętu i technologii oczyszczania płuczki wiertniczej z zwiercin opiera się na specyficznych warunkach wiercenia studni. Aby dokonać właściwego wyboru, musisz znać możliwości technologiczne i podstawowe funkcje sprzętu.
BHA i kontrola reżimu wiercenia w celu zwalczania samoistnej krzywizny odwiertu
Przyczyny techniczno-technologiczne prowadzą do samoistnego skrzywienia się odwiertu ze względu na to, że powodują wygięcie dolnej części przewodu wiertniczego i niewspółosiowość osi świdra względem środka odwiertu. Aby wykluczyć te procesy lub zmniejszyć prawdopodobieństwo ich wystąpienia, konieczne jest:
1. zwiększyć sztywność dna przewodu wiertniczego;
2. wykluczyć szczeliny między centralizatorami a ścianą otworu wiertniczego;
3. zmniejszyć WOB;
4. w przypadku wiercenia silnikami wiertniczymi należy okresowo obracać przewód wiertniczy.
Aby spełnić dwa pierwsze warunki, konieczne jest zainstalowanie co najmniej dwóch pełnowymiarowych centralizatorów: nad wiertłem i na korpusie kołnierza wiertła zbliżeniowego (lub na RD). Instalacja 2 - 3 pełnowymiarowych centralizatorów pozwala zwiększyć sztywność BHA i zmniejszyć ryzyko zginania nawet bez zmniejszania WOB.
W niektórych przypadkach zespoły pilotażowe są używane, gdy odwiert jest wiercony w sposób stopniowy: pilot - świder o małej średnicy - przedłużenie - świder - rozwiertak - kołnierz wiertniczy - przewód wiertniczy. Pożądane jest stosowanie kołnierzy o jak największej średnicy. Zwiększa to sztywność BHA i zmniejsza szczeliny między rurą a ścianą otworu wiertniczego.
2. Zapoznanie się z wierceniem podkładkowym
Zespół studni jest takim układem, gdy ujścia znajdują się blisko siebie na tej samej platformie technologicznej, a dna studni znajdują się w węzłach siatki zagospodarowania złoża.
Obecnie większość odwiertów produkcyjnych wykonywana jest w klastrach. Tłumaczy się to tym, że wiercenie klastrowe złóż może znacznie zmniejszyć wielkość obszarów zajmowanych przez wiercenie, a następnie odwierty produkcyjne, drogi, linie energetyczne i rurociągi.
Ta zaleta ma szczególne znaczenie podczas budowy i eksploatacji studni na żyznych gruntach, w rezerwatach, w tundrze, gdzie po kilkudziesięciu latach odtwarzana jest naruszona warstwa powierzchniowa ziemi, na terenach podmokłych, co komplikuje i znacznie zwiększa koszty roboty budowlano-montażowe obiektów wiertniczych i eksploatacyjnych. Wiercenie nakładkowe jest również niezbędne, gdy konieczne jest odsłonięcie złóż ropy naftowej pod obiektami przemysłowymi i cywilnymi, pod dnem rzek i jezior, pod strefą szelfową od brzegu i wiaduktów. Szczególne miejsce zajmuje budowa klastrów odwiertów na terenie Tiumenia, Tomska i innych regionów Syberii Zachodniej, co pozwoliło z powodzeniem przeprowadzić budowę szybów naftowych i gazowych na wyspach zasypowych w odległym, bagnistym i zaludnionym region.
Lokalizacja studni w wiertni uzależniona jest od warunków terenowych oraz proponowanego sposobu komunikacji wiertni z podłożem. Krzaki, które nie są połączone stałymi drogami z bazą, są uważane za lokalne. W niektórych przypadkach krzaki mogą być podstawowe, gdy znajdują się na autostradach. Na lejach lokalnych z reguły są one rozmieszczone w formie wachlarza we wszystkich kierunkach, co umożliwia uzyskanie maksymalnej liczby studni na leju wiertniczym.
Sprzęt wiertniczy i pomocniczy jest zamontowany w taki sposób, że podczas przemieszczania wiertnicy z jednego odwiertu do drugiego, pompy wiertnicze, studnie odbiorcze oraz część wyposażenia do czyszczenia, obróbki chemicznej i przygotowania płynu płuczącego pozostają nieruchome do czasu zakończenia budowę całości (lub części) studni na tej platformie.
Liczba dołków w klastrze może wahać się od 2 do 20-30 lub więcej. Co więcej, niż więcej studni w nakładce, im większe odchylenie dna od głowic odwiertu, długość odwiertu wzrasta, długość odwiertu wzrasta, co prowadzi do wzrostu kosztów wiercenia odwiertu. Ponadto istnieje niebezpieczeństwo spotkania pni. Dlatego konieczne staje się obliczenie wymaganej liczby studni w klastrze.
W praktyce wiertnictwa nakładkowego głównym kryterium określania liczby odwiertów w nakładce jest łączne natężenie przepływu odwiertu oraz współczynnik gazowy ropy naftowej. Wskaźniki te określają zagrożenie pożarowe studni podczas przepływu otwartego i zależą od poziomu technicznego sprzętu gaśniczego.
Znając przybliżoną liczbę dołków w nakładce, przystępują do budowy planu nakładki. Plan odwiertu jest schematycznym przedstawieniem rzutów poziomych wszystkich odwiertów odwiertów z danego obszaru odwiertu. Plan nakładki zawiera układ głowic odwiertów, kolejność ich wiercenia, kierunek ruchu maszyny, projektowe azymuty i przesunięcia odwiertów. Zadanie kończy się poprzez zbudowanie schematu ula.
3. Uruchamianie i cementowanie strun osłonowych
Po przewierceniu wymaganego odstępu skał konieczne jest opuszczenie do studni przewodu rurowego. Sznur osłonowy służy do wzmocnienia ścian studni, do izolacji warstw chłonnych i warstw wodonośnych.
Sznur osłonowy składa się z rur na kielichach, bezrękawowych połączeniach gwintowanych lub spawanych i jest opuszczany odcinkiem do studni lub w jednym stopniu od ujścia do dna. W jednym kroku sznurek jest opuszczany w przypadku wystarczającej stabilności ścian studni i udźwigu systemu jezdnego. Przy mocowaniu studni głębinowych, gwintowane bez tulei lub połączenia spawane OK.
Średnie OK są kilku typów:
1) pełny - zachodzenie na cały odwiert od dna do głowicy, niezależnie od podparcia poprzedniego przedziału;
2) wkładki - do ustalenia tylko otwartego przedziału studni z zachodzeniem na dno poprzedniego OK o określoną kwotę;
3) tajne kolumny - specjalne QAP, które służą tylko do pokrycia przedziału komplikacji i nie mają związku z poprzednimi kolumnami.
Odcinkowe prowadzenie ciągów osłonowych i mocowanie odwiertów za pomocą wkładek powstało, po pierwsze, jako praktyczne rozwiązanie problemu prowadzenia ciężkich ciągów osłonowych, a po drugie, jako rozwiązanie problemu uproszczenia konstrukcji odwiertów, zmniejszenia średnic osłonowych, a także jako szczeliny między strunami a ścianami studni, zmniejszając zużycie metalu i materiałów zatykających.
Do skutecznego cementowania i bardziej efektywnego zejścia stosuje się OK sprzęt technologiczny. W skład wyposażenia wchodzą następujące urządzenia: głowice cementujące, korki rozdzielające, zawory zwrotne, stopki kolumn, dysze prowadzące, centralizatory, skrobaki, turbulizatory, dysze stopowe o długości 1,2-1,5 m z otworami o średnicy 20-30 mm spiralnie, pierścieniowe pakery hydrauliczne typu PDM, stopniowane rękawy cementujące itp.
GŁOWICA CEMENTOWA
Głowice cementujące przeznaczone są do stworzenia szczelnego połączenia pomiędzy ciągiem osłonowym a przewodami wtryskowymi agregatów cementujących. Wysokość głowic cementujących powinna umożliwiać ich umieszczenie w cięgnach układu jezdnego i przy odpowiednim osprzęcie służyć do cementowania z rozwiercaniem sznura osłonowego.
ROZDZIELAJĄCE KORKI CEMENTOWE
Korki wyciskowe są przeznaczone do oddzielania zaczynu cementowego od płynu wyciskającego, gdy jest on wciskany do pierścienia studzienek.Istnieją modyfikacje korków, w których gwint na korek jest wykonany w górnej części korpusu po wewnętrznej stronie powierzchni, bez której korki te mogą być stosowane jako korki profilowe.Dolny korek wkładany jest do obudowy kolumny tuż przed przepompowaniem zaczynu cementowego, aby zapobiec jej zmieszaniu z płuczką wiertniczą, a górny po całej objętości pompowano zawiesinę cementową. Centralny kanał w dolnym korku blokowany jest gumową przesłoną, która pęka przy lądowaniu na „pierścieniu oporowym” i otwiera kanał do wpychania zaprawy cementowej.
SPRAWDŹ ZAWORY
Zawory zwrotne TsKOD są przeznaczone do ciągłego samonapełniania się przewodu rurowego płuczką wiertniczą podczas jej opuszczania do studni, a także do zapobiegania cofaniu się zaczynu cementowego z pierścienia i zatrzymywania rozdzielającego korka cementującego. Zawory typu TsKOD są opuszczane do studni z ciągiem osłonowym bez kuli odcinającej, która po opuszczeniu ciągu jest wpompowywana do ciągu na określoną głębokość.Kula przechodząc przez podkładki dzielone i membranę zajmuje pozycja robocza, której średnica jest mniejsza niż średnica kuli, ta ostatnia jest wrzucana do sznurka przed podłączeniem rur wiertniczych do sekcji. W takim przypadku wykluczone jest samonapełnianie sznurka cieczą, a przy opuszczaniu sznurka konieczne jest dodanie do niego płynu wiertniczego zgodnie z wymaganiami planu pracy. Górna część zaworu ma wewnętrzną końcową powierzchnię podporową, która działa jak „pierścień zatrzymujący”, aby zatrzymać oddzielający korek cementowy. W takim przypadku montaż pierścieni oporowych nie jest wymagany.
BUTY KOLUMNOWE
Podpory słupów służą do wyposażenia dna sznurów okładzinowych wykonanych z rur o średnicy 114-508 mm i służą do prowadzenia sznurów wzdłuż odwiertu i zabezpieczania ich przed uszkodzeniem podczas zanurzania w procesie obudowywania odwiertów naftowych i gazowych przy otworze dennym temperatury do 250 °C.
CENTRATORY
Centralizatory są zaprojektowane tak, aby zapewnić koncentryczne umieszczenie sznurka obudowy w odwiercie w celu uzyskania wysokiej jakości izolacji formacji podczas cementowania. Ponadto ułatwiają prowadzenie przewodu okładzinowego poprzez zmniejszenie sił tarcia między sznurem a ścianami odwiertu, przyczyniają się do zwiększenia stopnia wypierania płuczki wiertniczej przez muł cementowy w związku z pewnymi turbulencjami przepływów w obszar ich instalacji, ułatwiają pracę przy zawieszaniu ukrytych sznurków i dokowaniu sekcji dzięki centrowaniu ich górnych końców w studni.
- SKROBAK
Skrobaki służą do rozbijania glinianego placka na ścianach odwiertu w celu poprawy przyczepności zaczynu cementowego do skały, zwłaszcza przy cementowaniu odwiertów z rozwiercaniem.
Podczas schodzenia ze studni może być konieczne przepłukanie studni. W tym przypadku spłuczka jest przykręcana do kelly z gwintem blokującym na górze i gwintem trapezowym na dole. Następnie, po zakończeniu niezbędnych operacji, do obudowy przykręca się głowicę cementującą.
Po uruchomieniu odwiertu płyn wiertniczy nadal pozostaje w odwiercie. Aby usunąć go z beczki, stosuje się płyn buforowy. Jest pompowany przez głowicę cementującą. Następnie do kolumny pompowana jest szacunkowa ilość cementu. Następnie do przestrzeni wewnątrzrurowej dostarczany jest płyn wypierający, aby cement uniósł się do projektowanej wysokości. W tym samym czasie korek jest usuwany z elementu ustalającego i jest przenoszony w dół przez płyn wypierający. Osadzenie korka na pierścieniu oporowym zaworu zwrotnego, powodując skok ciśnienia na pompie, sygnalizuje zakończenie procesu cementowania.
Czas utwardzania zapraw cementowych dla przewodów ustala się na 16 h, a dla ciągów pośrednich i produkcyjnych na 24 h. Czas utwardzania różnych mieszanek cementujących (bentonit, żużel itp.) ustala się w zależności od danych ich wstępnych test, biorąc pod uwagę temperaturę w odwiercie.
Proces cementowania studni jest realizowany przez kompleks specjalnego sprzętu, który jest umieszczany zgodnie z wcześniej opracowanym schematem.
Jednostki cementujące są przeznaczone do wstrzykiwania zawiesiny cementowej i płynu wypierającego do odwiertu, a także do dostarczania płynu zamykającego do urządzenia mieszającego podczas przygotowywania roztworu. Ponadto służą do mycia i wyciskania korków piaskowych, prób ciśnieniowych rur, kolumn, rozdzielaczy, hydraulicznego mieszania szlamu itp.
Maszyny do mieszania cementu są przeznaczone do przygotowania zapraw cementowych do cementowania studni, różnych mieszanek zatykających; mogą być używane do przygotowania normalnych i obciążonych płuczek wiertniczych z proszków glinianych.
Zgodnie z przeznaczeniem i charakterem pracy mieszarki montowane są na samochodach lub przyczepach.Głównymi elementami mieszarek są kosz samowyładowczy, mechanizm załadowczo-rozładowczy oraz urządzenie mieszające do przygotowywania roztworów.
4. Otwieranie i testowanie horyzontów naftowych
Wiercenie studni kończy się otwarciem zbiornika ropy, tj. komunikacja złoża ropy ze studnią. Ten etap jest bardzo odpowiedzialny z kilku powodów. Mieszanka ropy i gazu w zbiorniku jest poniżej wielka presja, którego wartość może nie być z góry znana. Przy ciśnieniu przekraczającym ciśnienie kolumny cieczy wypełniającej odwiert, ciecz może zostać wyrzucona z odwiertu i następuje otwarty przepływ. Dostanie się płynu płuczącego (w większości przypadków jest to roztwór gliny) do zbiornika ropy naftowej zatyka jego kanały, utrudniając dopływ ropy do odwiertu.
Wydmuchów można uniknąć, instalując prezerwatywy na głowicy odwiertu lub stosując płyn do płukania o dużej gęstości. Zapobieganie wnikaniu roztworu do zbiornika oleju uzyskuje się poprzez wprowadzenie do roztworu różnych składników, które mają podobne właściwości do płynu zbiornikowego, na przykład emulsji na bazie oleju.
Ponieważ po otwarciu zbiornika ropy, przewód rurowy jest opuszczany do odwiertu i cementowany, blokując w ten sposób również zbiornik ropy, konieczne staje się ponowne otwarcie zbiornika. Osiąga się to poprzez strzelanie przez kolumnę w przedziale formacji za pomocą perforatorów. Są one opuszczane do studni na linę linową przez służbę geofizyczną.
Obecnie opanowano i stosuje się kilka metod perforacji studni:
1) Perforacja pocisku
Perforacja pocisków studni polega na opuszczeniu do studni na linie kablowej specjalnych urządzeń - perforatorów, w których korpusie zbudowane są ładunki prochowe z pociskami. Odbierając impuls elektryczny z powierzchni, ładunki eksplodują, dając pociskom dużą prędkość i dużą siłę przebicia. Powoduje zniszczenie metalu kolumny i pierścienia cementowego. Liczbę otworów w kolumnie i ich położenie wzdłuż grubości formacji oblicza się z góry, dlatego czasami obniża się girlandę perforatorów.
2) Perforacja torpedowa
Perforacja torpedowa jest w zasadzie podobna do perforacji pocisku, zwiększa się jedynie ciężar ładunku, a w perforatorze zastosowano poziome lufy.
3) Perforacja skumulowana
Perforacja skumulowana - powstawanie otworów w wyniku ukierunkowanego ruchu strumienia gorących ładunków uchodzących z perforatora z prędkością 6 ... 8 km / s pod ciśnieniem 20 ... 30 GPa. W tym przypadku powstaje kanał o głębokości do 350 mm i średnicy 8 ... 14 mm. Maksymalna grubość formacji, otwieranej przez perforator kumulacyjny do zejścia wynosi do 30 m, z torpedą - do 1 m, z pociskiem - do 2,5 m. Ilość ładunku prochu - do 50 g.
4) Perforacja hydro-piaskowania
Przy zastosowaniu perforacji hydro-piaskowej w kolumnie powstają otwory w wyniku ściernego działania mieszaniny piasek-ciecz przepływającej z prędkością do 300 m/s z dysz kalibrowanych przy ciśnieniu 15...30 MPa .
Zagospodarowanie odwiertów naftowych to zespół prac wykonywanych po odwiertach, których celem jest spowodowanie przepływu ropy naftowej ze złoża do odwiertu. Faktem jest, że w procesie otwierania, jak wspomniano wcześniej, do zbiornika może dostać się płyn wiertniczy i woda, co zatyka pory zbiornika i wypycha ropę z odwiertu. Dlatego spontaniczny dopływ ropy do studni nie zawsze jest możliwy. W takich przypadkach uciekają się do sztucznego wezwania napływu, które polega na wykonaniu specjalnej pracy.
Napływ może być spowodowany przez zastąpienie płynu o większej gęstości w odwiercie płynem o niższej gęstości. W tym przypadku zmniejsza się ciśnienie wywierane przez słup cieczy na formację, a tym samym następuje dopływ ropy z odwiertu. Metoda ta jest prosta i ekonomiczna, ale skuteczna w przypadku niewielkiego zanieczyszczenia formacji.
Jeżeli zastąpienie roztworu wodą nie przynosi rezultatów, to dopływ następuje za pomocą kompresora. Powietrze sprężone przez kompresor jest podawane do beczki. Jednocześnie można odepchnąć kolumnę cieczy od ślizgacza, zmniejszając w ten sposób ciśnienie wsteczne na formację do znacznych wartości. W niektórych przypadkach skuteczne może być okresowe dostarczanie powietrza przez sprężarkę, a cieczy przez zespół pompy, tworząc kolejne wybuchy powietrza. Ilość takich porcji gazu może być kilka, a one, rozprężając się, wyrzucają ciecz z beczki. W celu zwiększenia efektywności przemieszczania na długości ciągu rurowego montuje się zawory-rozruchowe otwory, przez które sprężone powietrze, przemieszczając się przez przestrzeń rurową, wchodzi do KZP i zaczyna podnosić ciecz zarówno w pierścieniu, jak i w rurki .
Napływ może być również spowodowany metodą wymazową. Metoda ta polega na wprowadzeniu do wężyka specjalnej wymazówki wyposażonej w zawór zwrotny. Poruszając się w dół, tłok przepuszcza przez siebie płyn, podczas podnoszenia się zawór zamyka się, a cała kolumna płynu, która znajduje się nad nim, jest zmuszana do podnoszenia się wraz z tłokiem, a następnie wyrzucana ze studni. Ponieważ podniesiony słup cieczy może być duży (do 1000 m), spadek ciśnienia na formacji może być znaczny. Proces wymazywania można powtarzać wielokrotnie, co pozwala na znaczne zmniejszenie nacisku.
Gdy rurki nie zostały jeszcze wprowadzone do studni, dopływ może być spowodowany metodą implozji. Jeśli naczynie wypełnione sprężonym powietrzem zostanie opuszczone do odwiertu, wówczas natychmiast skomunikuje się to naczynie z odwiertem, wówczas uwolnione powietrze przesunie się ze strefy wysokiego ciśnienia do strefy niskiego ciśnienia, porywając ciecz i tworząc w ten sposób obniżone ciśnienie na tworzenie. Podobny efekt można osiągnąć, jeśli prace pompowo-sprężarkowe opróżnione wcześniej z cieczy zostaną opuszczone do studni, a płyn odwiertowy zostanie do nich natychmiast wprowadzony. W takim przypadku ciśnienie wsteczne w formacji zmniejszy się, a dopływ płynu z formacji wzrośnie. Stymulacji napływu towarzyszy usuwanie zanieczyszczeń mechanicznych przyniesionych tam ze zbiornika tj. czyszczenie formacji.
5. Praca awaryjna w studni
Do prac awaryjnych używa się narzędzia wędkarskiego. Konstrukcja narzędzia wędkarskiego jest bardzo zróżnicowana. Jednak zgodnie z zasadą chwytania można je podzielić na trzy główne grupy:
a) Płaskie narzędzia połowowe działające na zasadzie zaklinowania przedmiotu na zewnątrz lub wewnątrz łapacza;
b) Narzędzia wędkarskie z gwintem, działające na zasadzie nacinania gwintu na przedmiocie z jednoczesnym wkręcaniem na niego łapacza;
c) Inne narzędzie.
Rozważ niektóre rodzaje narzędzi wędkarskich.
Rura zewnętrzna jest przeznaczona do chwytania rur, prętów lub innych obiektów w studni za korpus lub tuleję. Jest to dzielony uchwyt grzebieniowy umieszczany w korpusie i mocowany na rurach. Chwytany przedmiot jest przykryty zaczepem, który przy wejściu do góry zwiększa średnicę otworu, przepuszczając przedmiot do łapacza. Po rozciągnięciu ślizgacz schodzi w dół, a jego zęby wbijają się w korpus przedmiotu, zaklinując go w łapaczu.
Wewnętrzna włócznia została zaprojektowana tak, aby można ją było opuścić do rury spustowej. Składa się z korpusu, na którym zamocowana jest płyta, połączonego prętem i ruchomym pierścieniem. Korpus jest wsuwany w chwyt, podczas gdy matryca unosi się, zmniejszając średnicę łapacza i stwarzając warunki do wejścia. Po rozciągnięciu matryca opada, zwiększając średnicę korpusu łapacza i blokując rurę.
Najazd roboczy przeznaczony jest do chwytania rur lub prętów przez sprzęg za pomocą płaskich sprężyn zamocowanych na wewnętrznej powierzchni korpusu. Zbliżając się do obiektu, sprężyny rozchodzą się, przechodząc przez łapacz, a następnie zbiegają się.
Zawór do chwytania prętów służy do chwytania prętów przez sprzęgło. Składa się z korpusu, w którym zamocowane są sprężynowe matryce opuszczane. Matryce otwierają się, mijając obiekt, a następnie zbiegają się.
Frez z wewnętrznymi zębami służy do frezowania górnych końców rur lub prętów awaryjnych, aby następnie mogły pełnić funkcję łapaczy bezpieczeństwa. Składa się z korpusu, w którym wycinane są zęby podłużne.
Kran operacyjny przeznaczony jest do łowienia za pomocą gwintu wewnętrznego rury lub złączki. Składa się z korpusu, na którego ściętej części znajduje się nić. Można go pokroić na chwytliwy przedmiot, a następnie złapać.
Dzwonek przeznaczony do łapania rur do gwint zewnętrzny. Dzwon jest rurą odgałęzioną, na wewnętrznej powierzchni której nacięty jest gwint blokujący. Długość nici ok. 35 cm.
6. Eliminacja oleju napędowego i emisji
Istnieją dwie metody:
metoda zrównoważonego ciśnienia w zbiorniku
Gdy manifestacja jest eliminowana za pomocą pierwszej metody, ciśnienie denne jest utrzymywane nieco wyższe niż ciśnienie formacji podczas całego procesu. W takim przypadku przepływ płynu zatrzyma się aż do całkowitego wytłumienia.
Istnieją cztery sposoby na zaimplementowanie tej metody:
1) metoda ciągłego uboju studni: proces wypłukiwania i uśmiercania
rozpocząć natychmiast na roztworze o gęstości niezbędnej do wykonania
warunki - R zab > R zbiornik. Dzięki tej metodzie najniższa
ciśnienie, dlatego jest najbezpieczniejsze. Jednak do jego realizacji
konieczne jest posiadanie odpowiedniego zapasu odżywki i preparatów instant
płuczka wiertnicza.
2) Sposób oczekiwania na ważenie: po wykryciu objawów są zamknięte
dobrze i przystąp do przygotowania roztworu o wymaganej gęstości i
wymagana objętość. Utrzymuj stałe ciśnienie podczas przygotowywania roztworu.
rury wiertnicze, które zapewniają stałe ciśnienie w zbiorniku podczas wynurzania
pakiety płynów. Wadą tej metody jest konieczność prawidłowego
kontrola ciśnienia pływającego pakietu płynu, tj. tak, aby ciśnienie nie było
przekroczył dopuszczalny sprzęt, a także możliwe jest podklejenie wiercenia
narzędzie, ponieważ studnia pozostaje bez obiegu. Zaleta tej metody
w stosunku do poprzedniego jest to, że możemy przygotować rozwiązanie tego samego
gęstość, a także przy tej metodzie najmniejsze maksimum
ciśnienie, od kiedy gaz nie zbliżył się jeszcze do ust i zaczął się ciężki roztwór
wypełnić KZP, coraz bardziej otwieramy dławik, dlatego
pakiet gazowy rozciąga się bardziej i traci ciśnienie podczas zbliżania się do ust.
3) Metoda dwuetapowego ubijania studni. Na pierwszym etapie jest
poprzez wypłukanie płynu ze studni tym samym roztworem, na którym uzyskano manifestację.
W tym samym czasie zaczynają przygotowywać roztwór o gęstości niezbędnej do
dobrze zabija. W drugim etapie uśmiercania wykonuje się iniekcję do studni
rozwiązanie ważone. Ta metoda jest prostsza niż dwie poprzednie, stosunkowo
bezpieczne, ale podczas jego realizacji powstają największe naciski w
dobrze.
4) Dwustopniowa metoda rozszerzona. W pierwszym etapie z przeciwciśnieniem
wymywanie napływającego płynu ze studni odbywa się na tym samym roztworze, na którym uzyskano manifestację. Po wypłukaniu płynu formacji, bez zatrzymywania cyrkulacji, gęstość krążącego roztworu zwiększa się do wymaganej gęstości, a tym samym rozwijająca się formacja zostaje zabita. Ta metoda jest stosowana w przypadku braku pojemników niezbędnych do przygotowania roztworu.
metoda ubijania studni krok po kroku:
Zastosowanie tej metody jest stosowane, gdy podczas stosowania poprzednich metod powstają ciśnienia przekraczające dopuszczalne ciśnienie w głowicy odwiertu.
Bibliografia
1. Korshak A.A. Shammazov A.M./Podstawy biznesu naftowo-gazowego
2. Sprzęt do pól naftowych. Informator.
3. Ilsky A.L. Shmidt A.P./Wiertarki i mechanizmy
4. Popow A.N. Spivak A.I./Technologia wiercenia szybów naftowych i gazowych
cena studni za metr