Под режимом бурения понимается определенное сочетание параметров, влияющих на показатели бурения. К числу таких параметров относятся:
2) частота вращения долота;
3) массовый расход прокачиваемой промывочной жидкости;
4) качество промывочной жидкости (плотность, вязкость, водоотдача, статическое напряжение сдвига).
Сочетание этих параметров, позволяющее получать наиболее высокие качественные и количественные показатели бурения при данной технической вооруженности буровой, называется рациональным (или оптимальным) режимом бурения.
На практике часто в процессе бурения приходится отбирать керн, бурить скважину в неблагоприятных геологических условиях (зонах, склонных к поглощениям, осложнениям, связанным с нарушением целостности ствола скважины и т. п.), забуривать в сторону от ранее пробуренного ствола и т. д. Режимы бурения, применяемые в таких случаях, называются специальными режимами.
Эффективность работы долота оценивается двумя параметрами:
1) механической скоростью бурения v m е x ′ м/ч;
2) проходкой на долото h,м.
При выборе режима бурения следует учитывать, что с изменением одного из параметров не всегда увеличиваются механическая скорость проходки и проходка на долото. Для каждой породы существует оптимальное сочетание нагрузки на долото, частоты вращения долота и расхода промывочной жидкости.
При турбинном способе бурения изменение одного параметра режима бурения вызывает автоматическое изменение других. В случае увеличения расхода промывочной жидкости при неизменной нагрузке на долото частота вращения n вала турбобура (долота) растет прямо пропорционально. Если же нагрузка на долото будет увеличена, а расход промывочной жидкости останется постоянным, то частота вращения вала турбобура (долота) уменьшится.
В практике бурения скважин расход промывочной жидкости устанавливают с учетом обеспечения наивыгоднейших условий работы турбобура и наибольшего выноса выбуренной породы. С углублением скважины в связи с уменьшением ее диаметра расход промывочной жидкости уменьшают от интервала к интервалу .
При бурении в интервале, для которого установлен постоянный расход жидкости, из трех параметров режима бурения можно изменять только нагрузку на долото, регулируя тем самым частоту его вращения. Последняя при постоянным расходе промывочной жидкости достигает своего максимума при снятии нагрузки на долото.
При создании нагрузки на долото частота вращения вала турбобура (долота) уменьшается, а вращающий момент увеличивается. Эффективная работа турбобура будет обеспечена при таких нагрузках на долото, когда мощность на валу турбобура N достигнет максимального значения. В этот период частота вращения вала турбобура составляет примерно половину частоты вращения долота при отсутствии на него нагрузки, а вращающий момент около половины момента, развиваемого при торможении вала турбобура. При максимальной мощности на валу турбобура турбина имеет и максимальное значение КПД.
Нагрузка на долото зависит от твердости проходимости пород. При разбуривании твердых пород в целях повышения эффективности работы долота повышают нагрузку, а при бурении в мягких породах - снижают. В то же время частота вращения долота в первом случае уменьшается, а во втором - увеличивается, что и требуется для достижения хороших показателей его работы.
При работе турбобуров в соответствии с описанными условиями обеспечиваются наилучшие показатели работы долота, так как повышение и снижение частоты вращения долота приводит к неустойчивому режиму работы турбобура.
При роторном бурении отсутствует ярко выраженная взаимосвязь параметров режима бурения и, следовательно, влияние их друг на друга, как при турбинном способе. Поэтому можно устанавливать любые комбинации параметров режима бурения, контролировать их .
Расход промывочной жидкости устанавливается с учетом качественной очистки забоя скважины. Нагрузка на долото и частота его вращения устанавливаются для каждого геологического горизонта с учетом твердости проходимых пород.
Подача бурильной колонны - вертикальное перемещение на поверхности, которое осуществляется опусканием ведущей трубы в ротор на некоторую величину в результате ослабления тормоза лебедки.
Давление долота на забой создается частично весом бурильной колонны, однако чрезмерное ее увеличение может вызвать поломку бурильной колонны и искривление скважины. Во избежание этого нижняя часть бурильной колонны выполняется утяжеленной.
При работе с утяжеленным низом его вес используется только на 75 %.
Для контроля за равномерным давлением на долото пользуются прибором, называемым индикатором веса. Давление промывочной жидкости измеряется датчиком, который монтируется на трубопроводе между насосами или на стояке нагнетательной линии буровых насосов. Частота вращения ротора измеряется тахометрами различных конструкций. Кроме того, применяют приборы для определения механической скорости бурения, а также другие приборы, регистрирующие и показывающие параметры бурения на забое (частота вращения вала турбобура, пространственное положение забоя скважины и т. д.).
В последнее время все шире внедряется передача параметров режима бурения на расстояние. Это позволяет на диспетчерских пунктах (участках) оборудовать специальные пульты, на которых монтируют показывающие и регистрирующие приборы параметров режима бурения каждой буровой. Диспетчер (инженер участка) получает возможность круглосуточно следить за работой буровых и при необходимости незамедлительно вносить нужные коррективы в процесс проводки скважины.
Технологическим режимом бурения называется сочетание ряда основных задаваемых параметров, характеризующих скоростные и качественные показатели бурения, связанных с разрушением горных пород на забое скважины и выносом выбуренной породы на поверхность.
Основными параметрами режима бурения являются:
Осевая нагрузка на породоразрушающий инструмент;
Скорость вращения бурового инструмента;
Количество и качество промывочной жидкости;
Тип породоразрушающего инструмента.
Осевая нагрузка на породоразрушающий инструмент характеризует параметр режима бурения, определяющий усилие, приложенное по оси бурильной колонны к породоразрушающему инструменту.
Осевая нагрузка на долото в процессе бурения создается весом утяжеленных бурильных труб и колонной бурильных труб.
Режим объемного разрушения породы возможен, если удельное давление на забой превышает сопротивление породы на вдавливание. Таким образом, осевая нагрузка пропорциональна прочности горных пород. Отсюда следует, что при прочих равных условиях наименьшие нагрузки на забой допускаются при бурении мягких пород, с повышением твердости пород осевая нагрузка должна увеличиваться.
При повышении осевой нагрузки на долото механическая скорость бурения увеличивается до определенного критического значения. Сначала скорость возрастает интенсивно, а затем ее рост постепенно замедляется и наступает момент, когда рост прекращается, и скорость начинает уменьшаться. При этом большое значение имеет очистка забоя скважины.
Повышение осевой нагрузки увеличивает проходку на долото и механическую скорость при условии увеличения скорости циркуляции промывочной жидкости, необходимой для полной очистки забоя от выбуренной породы.
При бурении для каждых конкретных условий существует критическое значение осевой нагрузки на долото, которое не может обеспечить дальнейшее повышение скорости бурения. Значение критической нагрузки зависит от физико-механических свойств разбуриваемых пород, а также типа долота.
Оптимальные осевые нагрузки на долото подбираются с учетом полученных результатов отработки долот с различными осевыми нагрузками в зависимости от крепости пород, типа и размера долот, бурильного инструмента и способа бурения.
Повышение механической скорости при увеличении осевой нагрузки, создаваемой на забое весом бурильных труб, без применения утяжеленных бурильных труб не может быть обеспечено. В этом случае от излишней нагрузки бурильные трубы изгибаются, волной изгиба упираются в стенки скважины, чем поглощается большая часть осевой нагрузки и не обеспечивается повышение механической скорости.
Для получения более высокой механической скорости и проходки на долото практикуется создавать наибольшую осевую нагрузку в начале механического бурения. Процесс бурения должен проводиться таким образом, чтобы во время работы долота удельное давление поддерживалось постоянным, а суммарная нагрузка изменялась в необходимых пределах. Бурильный инструмент должен подаваться равномерно и непрерывно с обеспечением необходимой осевой нагрузки по индикатору веса.
Скорость вращения долота
При выборе параметров режима бурения учитывают, что скорость проходки возрастает пропорционально повышению скорости вращения долота при одновременном увеличении осевой нагрузки.
При увеличении скорости вращения повышается износ долота. По достижении определенного числа оборотов износ долота увеличивается быстрее, чем повышается скорость проходки. Влияние скорости вращения долота на эффективность разрушения породы зависит от осевой нагрузки, степени очистки забоя, физико-механических свойств породы и глубины скважины.
Опыт бурения в твердых породах показывает, что для повышения скорости проходки необходимо применять меньшее число оборотов при одновременном увеличении осевой нагрузки на породоразрушающий инструмент.
Скорость вращения долота рекомендуется снижать с увеличением диаметра долота, с повышением твердости и абразивности пород, с уменьшением диаметра бурильных труб, а также при бурении чередующихся пластов небольшой мощности и при переходе из пласта меньшей твердости в пласт большей твердости. Для расчета допустимой скорости вращения для каждого размера бурильных труб применяют формулу:
n - допустимая скорость вращения в об /мин;
l - длина вращающихся бурильных труб в м;
Е - модуль упругости;
g - ускорение силы тяжести, равное 9,8 м/сек2;
q - вес 1 м бурильных труб в кг.
При выборе скорости вращения долота учитывают интервал глубины бурения. С увеличением глубины скважины скорость вращения долота при роторном способе снижают.
Промывка скважины
Процесс очистки забоя скважины от шлама и охлаждения породоразрушающего инструмента буровым раствором называется промывкой скважины.
Практикой бурения и специальными исследованиями установлено влияние параметров промывочной жидкости на качественные показатели бурения.
К числу основных параметров промывки скважины, оказывающих влияние на качественные показатели бурения, относятся: удельный вес, вязкость промывочной жидкости, а также количество подаваемой на забой промывочной жидкости и скорость восходящего потока в затрубном пространстве.
Увеличение удельного веса промывочной жидкости приводит к снижению механической скорости, и, наоборот, при прочих равных условиях скорость проходки повышается при использовании промывочной жидкости меньшего удельного веса.
Промывочные жидкости с меньшей вязкостью лучше очищают забой от разбуренных частиц породы и при условии повышения скорости движения в затрубном пространстве обеспечивают интенсивный вынос их на поверхность.
С повышением количества подаваемой на забой промывочной жидкости увеличивается скорость циркуляции в затрубном пространстве, и при соответствующем изменении параметров режима бурения повышается скорость проходки. При этом существенное влияние оказывают физико-механические свойства пород, тип и размер долота, качественные параметры промывочной жидкости.
С повышением скорости восходящего потока промывочной жидкости в затрубном пространстве увеличивается интенсивность очистки забоя скважины от выбуренной породы, облегчается работа долота на забое и повышается эффективность бурения.
Кроме очистки забоя от выбуренных частиц, промывочная жидкость принимает участие в разрушении пород путем гидромониторного эффекта, который является технической основой для долот с гидромониторной промывкой.
При увеличении осевой нагрузки, скорости вращения и диаметра долота для очистки забоя необходимо повышать количество подаваемой в скважину промывочной жидкости. Таким образом, расход промывочной жидкости находится в прямой зависимости от объема разбуриваемой породы в единицу времени. При недостаточной интенсивности промывки очистка забоя от шлама ухудшается и снижается механическая скорость бурения.
Показателем нормальных условий промывки забоя является скорость движения восходящей струи в кольцевом пространстве между стенкой скважины и поверхностью бурильных труб, имеющая значения от 0,8 до 1,5 м/сек.
В зависимости от скорости циркуляции промывочной жидкости в скважине необходимую производительность насоса определяют по формуле:
Q - производительность насоса в м3/сек;
V - скорость потока промывочной жидкости в м/сек;
F - площадь кольцевого сечения скважины в м2.
Площадь кольцевого сечения скважины рассчитывают по формуле:
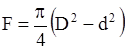
D - фактический диаметр скважины в м;
d - наружный диаметр бурильных труб в м.
При выборе параметров режима бурения необходимо полно использовать установленную гидравлическую мощность буровой установки, бурить при максимально допустимых по геолого-техническим условиям количествах промывочной жидкости. При этом следует учитывать допустимые рабочие давления буровых насосов и увеличение гидравлических сопротивлений с ростом глубины скважины.
Тип породоразрушающего инструмента
Инструментом, предназначенным для механического разрушения породы при бурении, является буровое долото.
В зависимости от физико-механических свойств разбуриваемых пород применяют различные типы и конструкции долот. Долота для вращательного бурения различаются как по назначению, так и по принципу их действия на породу.
По своему назначению буровые долота подразделяются на три группы:
Долота сплошного бурения, разрушающие породу при бурении в скважине сплошным забоем, по всей его площади;
Долота колонкового бурения, разрушающие породу в скважине кольцевым забоем, с оставлением в центре неразбуренного столбика (керна) проходимой породы;
Долота специального назначения, применяемые для различного вида работ в скважине, непосредственно не связанных с процессом бурения скважины (расширения ствола, разбуривания цементного камня и др.).
По принципу воздействия на породу буровые долота разделяются на две группы: долота режущего типа, разрушающие породу в основном резанием, к этому типу долот относятся фрезеры, алмазные; долота скалывающего и дробящего типа, которые разрушают породу в результате скалывающего и дробящего воздействия, к ним относятся все разновидности шарошечных долот.
Долота шарошечные. Шарошечным называется долото, разрушающее горную породу перекатывающимися по забою шарошками. Шарошка - породоразрушающая деталь шарошечного долота, имеющая форму цилиндра или конуса. Боковая поверхность шарошки имеет зубья или твердосплавные вставки (штыри), которые разрушают породу при вращении долота.
Шарошечные долота предназначаются для бурения вращательным способом скважин с промывкой забоя жидкостью или продувкой воздухом. Эти долота применяются для бурения пород с различными физико-механическими свойствами. В зависимости от разбуриваемых пород шарошечные долота для бурения сплошным забоем выпускаются следующих восьми типов:
М - для самых мягких и вязких;
МС - для мягких пород с пропластками пород средней твердости;
С - для пород средней твердости;
СТ - для пород средней твердости с пропластками твердых и абразивных пород;
Т - для твердых и абразивных пород;
ТК - для твердых пород с пропластками крепких и абразивных пород;
К - для крепких, хрупких и абразивных пород;
ОК - для самых крепких и абразивных пород.
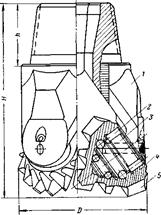
Рисунок 2.6 - Долото трехшарошечное
В зависимости от числа шарошек долота выпускаются одношарошечные, двух-, трех-, четырех- и пятишарошечные долота.
Трехшарошечные долота (рис. 2.6), имеющие конические шарошки и обладающие высокой эффективностью, наиболее распространены при бурении эксплуатационных скважин. По конструктивному исполнению трехшарошечные долота разделяются на бескорпусные (секционные) и корпусные.
Бескорпусное долото состоит из трех сваренных между собой секций. Каждая секция состоит из лапы 1 с цапфой 3, на которой смонтирована шарошка 4 с зубьями 5, свободно вращающаяся на подшипниках качения 2. Бескорпусные долота имеют присоединительную замковую резьбу, которая нарезается после сварки лап. Бескорпусные долота выпускаются диаметром от 76 до 346 мм.
Долота корпусные большого диаметра имеют стальной литой корпус с промывочной плитой, в пазах которого привариваются лапы, оснащенные шарошками. Шарошки в зависимости от числа конусных поверхностей разделяются на одно-, двух- и трехконусные. Двух- и трехконусные шарошки выполняются самоочищающимися.
В долотах самоочищающегося типа зубчатые венцы одной шарошки заходят в проточки между венцами других шарошек, чем достигается их самоочищение от выбуренной породы. В этих долотах одна из шарошек имеет полный конус, вершина которого заходит за осевую линию долота, а другие две - имеют усеченные конусы.
Трехшарошечные долота, применяемые в зависимости от физико-механических свойств разбуриваемых пород, отличаются друг от друга не только величиной диаметра, но и формой шарошек, шагом и формой зубьев, углом наклона оси шарошки к оси долота, промывочным устройством и размерами присоединительной резьбы.
Опора шарошек является одним из основных узлов долота. Для получения прочности и износостойкости опоры изготавливаются с высокой точностью и прочностью из высоколегированных сталей с термохимической обработкой. Конструкции опор шарошек зависят от типа и размера долот и выполняются в различных вариантах с применением подшипников качения (шарики, цилиндрические ролики) или подшипники качения и скольжения.
Промывочное устройство долот оказывает важное влияние на очистку забоя скважины и зубьев шарошек от разбуренной породы, на степень охлаждения опор и шарошек.
В зависимости от типа и размера трехшарошечного долота промывочные устройства различаются между собой. В отдельных типах долот - промывка центральная с одним каналом, направляющим поток промывочной жидкости по оси долота к центру забоя скважины; в других - с тремя каналами, расположенными в лапах и направляющими поток промывочной жидкости на забой скважины между шарошками; в третьих - с тремя каналами, расположенными в лапах или промывочных плитах и направляющими поток промывочной жидкости - на шарошки. Имеется группа долот с комбинированной промывкой, у которых поток промывочной жидкости направляется между шарошками и на шарошки.
Долота разных типоразмеров выпускаются со вставными штуцерами и без вставных штуцеров.
Долота, у которых струя промывочной жидкости подается к забою скважины и направляется через специальные штуцера (насадки), скорость истечения жидкости из которых значительно повышается, называются гидромониторными. Насадки для гидромониторных долот изготавливаются минералокерамическими и металлокерамическими. Для герметизации зазоров между насадками и промывочным каналом применяются уплотнительные элементы.
При изготовлении долот без штуцеров отверстия выполняются в корпусе долота. В этом случае промывочные каналы образуются по форме внутренней поверхности лап сечениями: круглыми, треугольными и щелевидными.
Штыревые долота предназначаются для бурения в крепких и абразивных породах с высоким сопротивлением сжатию, где проходка долота с обычным вооружением шарошек незначительна. Вооружение шарошек этих долот выполнено в виде вставных зубков - штырей, имеющих рабочую поверхность в форме полусферы.
Долота режущего типа. Долото, разрушающее горную породу резанием и истиранием, называется режущим долотом. Для бурения перемеживающихся мягких, средних и твердых пород в последние годы получили распространение долота режущего типа. Долото истирающе-режущего типа состоит из цельного корпуса, приваренных к нему шести лопастей, из которых три нижние имеют нормальную высоту, а три верхние - укороченную. Каждая укороченная лопасть приваривается между двумя лопастями нормальной высоты. Режущие кромки лопастей скошены и армированы цилиндрическими штырями из металлокерамического сплава. Промежутки между штырями и передние грани всех лопастей армируются зернистым твердым сплавом. В нижней части корпуса, в зависимости от размера долота, имеются от двух до шести промывочных каналов, направление которых предусматривает промывку струей промывочной жидкости забой. У долот гидромониторного типа имеются три промывочных канала, в которые вставляются минералокерамические насадки. Насадки крепятся в корпусе долота при помощи пружинных колец и герметизируются резиновыми кольцами.
Долота алмазные. Алмазным долотом называется режущее долото, армированное алмазами. Алмазные долота предназначены для роторного и турбинного бурения скважин в различных по твердости породах, в которых эффективность применения трехшарошечных долот снижается. Практика бурения подтверждает, что с ростом глубины скважин эффективность применения трехшарошечных долот снижается, и расход их увеличивается. Широко используются алмазные долота при бурении нижних интервалов глубоких скважин. Применение алмазных долот дает возможность увеличить проходку на долото, сократить спускоподъемные операции, получить высокие скорости бурения. Алмазные долота работают по принципу микрорезания и истирания. Интенсивность процесса разрушения горной породы при бурении алмазными долотами находится в зависимости от линейной скорости контакта между алмазами и породой, осевого давления и количества подаваемой промывочной жидкости.
Алмазные долота состоят из фасонной твердосплавной алмазонесущей головки - матрицы и стального корпуса с присоединительной резьбой.
Производительность и устойчивость алмазного долота в основном зависят от свойства и размера применяемых алмазов, схемы размещения алмазных зерен на рабочей части долота и качества изготовления самого долота.
Спиральные алмазные долота предназначены для турбинного бурения. Торцовая часть долота представляет собой три сферические поверхности, оснащенные алмазами. Три промывочные отверстия переходят в сферические спиральные каналы, идущие от центральной части головки к периферии долота.
Радиальные алмазные долота применяются как в роторном, так и в турбинном бурении. Рабочая часть долот выполнена в виде шести секторных выступов, оснащенных алмазами, три малых сектора доходят до промывочного отверстия, а три больших соединяются в центральной конусной части долота. Между тремя большими секторными выступами расположены три отверстия для промывочной жидкости, переходящие к периферийной части в шесть промывочных каналов для отвода промывочной жидкости.
Радиальное алмазное долото предназначено для бурения малоабразивных пород средней твердости.
Алмазные долота с резцами типа PDC. Эти долота предназначены для бурения вертикальных, наклонно-направленых, горизонтальных нефтяных и газовых скважин в малоабразивных породах с промывкой водой или глинистым раствором. Долота армированные зубками PDC, обладают высокой износостойкостью и работоспособностью, а также обеспечивают кратное увеличение проходки за долбление, повышая при этом механическую скорость бурения. Отсутствие движущихся и вращающихся частей продлевает ресурс работы алмазного долота по сравнению с шарошечными долотами.
Бицентричные долота. Бицентричные долота предназначены для бурения с одновременным расширением ствола скважины, в мягких и средних малообразивных горных породах. Применяются для расширения боковых стволов из ранее пробуренных обсаженных скважин, а также расширения в продуктивном интервале с целью увеличения дебита скважины.
Бицентричные долота предоставили возможность бурения скважин большего диаметра, чем обычно возможно при данном диаметре ранее спущенной обсадной колонны. Основные преимущества бицентричных долот: возможность расширения скважин; усовершенствование операций цементирования обсадной колонны; снижение затрат на бурение. Применение бицентричных долот при бурении вертикальных, наклонно-направленных или горизонтальных скважин является новым уровнем в развитии технического прогресса.
Буровые коронки. Буровой коронкой называется породоразрушающий инструмент, предназначенный для разрушения горных пород при бурении с отбором керна. Буровая коронка, армированная резцами из твердых сплавов, называется твердосплавной, а армированная алмазами - алмазной коронкой.
Буровая коронка состоит из короночного кольца, из торца которого зачеканиваются с последующим припаиванием латунью резцы из твердого сплава. Короночные кольца изготавливаются из насосно-компрессорных, бурильных труб или трубных заготовок соответствующего размера.
Твердосплавные резцы, закрепляемые в короночном кольце, должны перекрывать всю площадь торца и выступать за наружную и внутреннюю боковые поверхности и над торцом коронки. Выступающие за наружную поверхность коронки резцы образуют при бурении зазор между коронкой и стенкой скважины. Резцы, выступающие за внутреннюю поверхность коронки, образуют при углублении зазор между керном и внутренней поверхностью колонковой трубы. Выступающие над нижним торцом коронки резцы из твердого сплава непосредственно при бурении разрушают породу на кольцевом забое скважины.
В зависимости от твердости разбуриваемых пород буровые коронки выпускаются для бурения мягких пород, пород средней твердости и твердых пород.
Важными факторами, определяющими конструкцию буровой коронки для бурения различных по твердости пород, являются: величины выхода резцов за наружную и внутреннюю поверхность корпуса и над торцом короночного кольца, угол заострения резцов, форма и расположение резцов.
Для бурения в твердых породах величина выхода резцов внутрь и наружу коронки составляет 0,5-1,0 мм, а над торцом 1,5-2,5 мм.
Расположение резцов относительно торца короночного кольца может быть на одном уровне или ступенчатым. В ступенчатых коронках резцы располагаются как на торцовой поверхности, так и на боковой поверхности на расстоянии 20-30 мм от торца. Это делается для того, чтобы избежать расширения интервала ствола скважины после отбора керна при переходе на долото.
Долота-фрезеры. Долота-фрезеры предназначаются для выполнения вспомогательных работ в процессе бурения и при аварийных работах в скважине.
В зависимости от назначения долота-фрезеры имеют различные формы рабочей поверхности и конструктивно выполняются кольцевыми, торцовыми, фасонными. Они используются для разбуривания обратных клапанов, для истирания металлических предметов, находящихся на забое скважины, для фрезерования оборванных концов бурильного инструмента при аварийных работах, для фрезерования нарушенной части обсадных колонн и других работ.
Широко применяется долото-фрезер типа ФР. Оно состоит из корпуса, имеющего в верхней части присоединительную замковую резьбу. Корпус обтекаемой формы в нижней своей части имеет три выступа, армированных с торца и боковых поверхностей твердосплавными резцами. В нижней части корпуса центральный промывочный канал соединяется с дополнительными каналами, посредством которых промывочная жидкость подводится к различным участкам торцовой части фрезера.
Основные параметры режима бурения сведены в таблицу 2.4.
Таблица 2.4 - Основные параметры режима бурения
Интервал, м |
Скорость вращения, об/мин |
Расход бурового раствора, л/с |
Тип долота |
||
Пилот-ствол |
|||||
III 444.5 М-ГВУ R146 |
|||||
III 295.3 С-ГВ |
|||||
Интервал, м |
Скорость вращения, об/мин |
Расход бурового раствора, л/с |
Тип долота |
||
III 295.3 М-ЦГВ R187 |
|||||
III 295.3 С-ГВ |
|||||
III 295.3 С-ГВ |
|||||
III 295.3 С-ГВ |
|||||
III 215.9 С-ГВУ |
|||||
III 215.9 С-ГВУ |
|||||
Горизонтальный ствол |
|||||
Режим бурения К атегория: Буровое оборудование Режим бурения Общие данные по режиму бурения Режим бурения определяется буримостыо горных пород (механической скоростью бурения) и проходкой на долото. Режим бурения выражается пятью основными величинами: Давление долота на забой создается за счет части веса бурильной колонны, однако чрезмерное увеличение нагрузки может привести к поломке инструмента и к искривлению скважины. Во избежание искривления скважины и аварий внизу бурильной колонны устанавливают утяжеленный низ. При работе с утяжеленным низом его вес используется только на 75%. Заданная величина нагрузки на долото контролируется гидравлическим индикатором веса. Индикатор веса ГИВ-2 Индикатор веса ГИВ-2 состоит из трансформатора давления, укрепляемого на мертвом конце талевого каната, указывающего прибора и верньера, записывающего прибора, медных трубок, соединяющих трансформатор давления с указывающим и записывающим приборами, бачка для запасной жидкости, ручного насоса и запорного вентиля. Вся система заполняется жидкостью: в летнее время водой или 1%-ным раствором хромпика в воде для предохранения от коррозии, а зимой незамерзающей жидкостью - смесью воды со спиртом или с глицерином. Показывающий прибор представляет собой манометр с трубчатой пружиной, шкала указывающего прибора разделена на 100 частей. Для более точного определения нагрузки на долото служит верньер 8. Шкала верньера занимает всю окружность и разделена на 40 делений без указания цифр. При изменении нагрузки, действующей в талевом канате, до наибольшего значения, соответствующего 100 делениям прибора, стрелка верньера делает пять оборотов. Таким образом, одно деление верньера соответствует половине деления прибора. Пример. Определить цену одного деления (в кг) по указывающему прибору индикатора веса с верньером (ГИВ-2), если вес бурильного инструмента на крюке 56 делений. При каждом индикаторе веса имеется свидетельство о тарировке на рабочий талевый канат диаметром 1”, I1/8” или 13/4”, которое необходимо иметь при подсчетах цены одного деления. Подсчет. В показании указывающего прибора индикатора веса ГИВ-2 по свидетельству тарировки на канате диаметром i1/8” усилие (в кг) на один конец при 50 делениях 5415 кг, а при 60 делениях 6650 кг. Разность в показаниях усилий между 50 и 60 делениями определится 6650 – 5415 = 1235 кг. Роторный индикатор веса РИГ-1 Гидравлический роторный индикатор веса предназначен для контроля работы забойного механизма подачи долота по изменению веса инструмента в процессе бурения двух- и трехствольных скважин двумя комплектами бурильных труб. При пользовании забойным механизмом подачи бурильный инструмент подвешивают при помощи клиньев, установленных в роторе. Вес инструмента через ротор передается на гидравлический поршневой датчик, установленный под ротором в вырубке подроторного бруса; в связи с этим в датчике создается давление, которое измеряется пружинным манометром. В момент сработки забойного механизма на полную длину хода штока вследствие зависания его на колонне бурильных труб и отрыва долота от забоя вес инструмента увеличивается, что фиксируется стрелкой манометра. Датчик роторного индикатора веса представляет собой блок из 11 поршней, помещающихся в расточках вытянутого прямоугольного корпуса. Поршни снабжены резиновыми самоуплотняющимися кольцами, препятствующими вытеканию жидкости из полости цилиндров. Цилиндры сообщаются между собой и заполняются жидкостью через общий штуцер. Наибольший измеряемый вес инструмента 130 т. Давление в гидросистеме при максимальном весе инструмента 120 кГ/см2. Габариты датчика: высота 78 мм, ширина 94 мм, длина 1060 мм. Габариты приборного шкафа: высота 430 мм, ширина 660 мм, глубина 170 мм. Вес датчика 28 кг, а приборного шкафа 17 кг. Числа оборотов долота Как показала практика роторного бурения, оптимальные числа оборотов трехшарошечных долот, при которых были получены наилучшие результаты по механическим скоростям и проходке на долото, находятся в пределах 200-220 об/мин при бурении в верхних интервалах скважины. Расход промывочной жидкости Количество прокачиваемой жидкости зависит от мощности насосной группы бурового оборудования и применяемого бурового инструмента. Современные мощные насосы при спаренной работе позволяют закачивать жидкость в количестве 60 л/сек и более. Однако имеются опасения, что чрезмерное увеличение скорости прокачиваемой жидкости в скважинах, сложенных слабыми породами, приведет к размыву ствола. Расходомер глипистого раствора РГР-1 Этот прибор предназначен для измерения и записи расхода глинистого раствора на выкиде буровых насосов при бурении скважин. Расходомер состоит из датчика и вторичного прибора. Принцип действия прибора В трубопроводе, по которому протекает измеряемый поток глинистого раствора, ребром к потоку установлен диск, укрепленный эксцентрично на оси. При движении жидкости скоростной напор потока действует на диск и стремится повернуть его. Противодействующий момент повороту диска создается спиральной пружиной, связанной с осью, на которую насажен диск. Одновременно при повороте оси измерительного узла ползунок, жестко связанный с осью, перемещаясь по реохорду, изменяет его сопротивление. Рис. 1. Расходомер глинистого раствора РГР-1. Расходомер включен в схему автоматического электронного уравновешенного моста ЭМД-207, при помощи которого производятся измерение и запись расхода глинистого раствора. Режим турбинного бурения Режим турбинного бурения определяется величиной осевой на* грузки, расходом промывочной жидкости н числом оборотов долота. В турбинном бурении повышение мощности и вращающего момента на валу турбобура связано с увеличением расхода промывочной жидкости. При увеличении количества прокачиваемой жидкости наряду с увеличением мощностных характеристик турбобура достигается лучшая очистка забоя от выбуренной породы и улучшаются условия работы долота на забое. С увеличением осевой нагрузки на долото число оборотов вала турбобура уменьшается, а крутящий момент возрастает и при числе оборотов, равном нулю, достигает максимальной величины. Постепенным изменением осевой нагрузки на долото можно найти такое число оборотов, при котором мощность и к. п. д., развиваемые турбиной, а также механическая скорость проходки будут максимальными. Выбранную нагрузку даже при бурении в одной и той же породе в связи с износом долота необходимо периодически проверять путем изменения нагрузки на долото. Турбобуры современной конструкции позволяют работать при нагрузках на долото до 30 т и более. Числа оборотов долота Числа оборотов долота в турбинном бурении зависят от количества прокачиваемой жидкости и величины осевой нагрузки. При долотах современных конструкций наиболее выгодным числом оборотов считается 300-600 обIмин. При работе в твердых породах необходимо нагрузку на долото увеличивать, а в мягких породах - снижать. Требования по технологической дисциплине в бурении Промывочные растворы В качестве промывочной жидкости при бурении нефтяных и газовых скважин применяются глинистые растворы, растворы на нефтяной основе, а также техническая вода. Техническая вода широко применяется в восточных нефтяных районах нашей страны, что позволило улучшить условия работы буровых насосов и сократить расход запасных частей, улучшить очистку промывочной жидкости от выбуренной породы, повысить производительность насосов при меньшем рабочем давлении на выкиде, увеличить мощность турбобура (вследствие чего он стал воспринимать большие нагрузки). Также увеличились проходка па долото и механическая скорость; сократилось количество подъемов инструмента и расход долот, что позволило повысить коммерческую скорость бурения. При использовании воды в качестве промывочной жидкости необходимо соблюдать следующие условия: При переходе с воды на глинистый раствор во избежание прихватов инструмента необходимо тщательно следить за состоянием качества глинистого раствора, не допуская ухудшения его параметров. Бентонитовый глинопорошок При бурении нефтяных и газовых скважин в качестве добавки к структурным глинистым растворам, приготовленным из местных глин, а также в качестве основного материала для приготовления промывочных растворов с низким удельным весом и высокими тиксотропными свойствами при бурении в зонах, поглощающих обычную промывочную жидкость (воду или глинистый раствор), применяют порошок из бентонитовой глины. Бентонитовый порошок приготовляют из бентонитовой глины, не содержащей гипса, мергеля, песка и других вредных примесей. Качество порошка определяют по параметрам растворов, приготовленных на его основе с дистиллированной водой, а тонкость помола бентонитовой глины - по остатку на сите (4900 отверстий на 1 см2), который не должен превышать 5%. Характеристика глинистого раствора, приготовленного из порошка бентонитовой глины, должна быть следующая. Приборы для определения качества глинистых растворов Ареометр АГ-1 для замера удельного веса глинистого раствора. Для определения удельного веса глинистого раствора необходимо отсоединить стакан от поплавка и заполнить его раствором. Затем следует вставить в него поплавок, после чего ареометр нужно опустить в ведерко с водой. Величину удельного веса определяют по шкале. Ареометром АГ-1 можно измерять удельные веса утяжеленных растворов; для этого необходимо отвинтить съемный груз, а отсчет удельного веса вести по второй шкале. Рис. 2. Ареометр АГ-1. Рис. 3. Стандартный полевой вискозиметр СПВ-5. Вискозиметр СПВ-5 Практически замер производится следующим образом. В воронку наливают поочередно 500 и 200 см3 глинистого раствора, закрыв нижний конец трубки пальцем. Для правильности показаний раствор должен быть процежен через сетку, предварительно вставленную в воронку. Подставив под воронку кружку, отнимают палец от конца трубки, а другой рукой засекают время на секундомере. Время истечения 500 см3 воды из вискозиметра при Ъ-мм трубке равно 15 сек. Величина вязкости измеряется временем истечения 500 смг раствора в секундах. Автомат для регистрации параметров глинистого раствора АПГР-1 Автомат АПГР-1 предназначен для непрерывного измерения и регистрации удельного веса и вязкости глинистого раствора. Автомат состоит из шести отдельных узлов, собранных на обгцей раме: Центробежный насос из желоба циркуляционной системы подает глинистый раствор в циркуляционную камеиу. избыток глинистого раствора вытекает через сливную трубу 16. Назначение сливной трубы поддерживать постоянный уровень в камере и постоянную скорость движения раствора в измерительном отсеке. В измерительный отсек погружены две пьезометрические трубки, через которые подается воздух. Воздух от воздуходувки через регулятор давления подается на контрольные стаканчики. Расход воздуха устанавливается регулировочными винтами обычно количество воздуха составляет 120-140 пузырьков, что соответствует расходу 0,7-0,8 л/час через каждую трубку. Рис. 4. Схема автомата для регистрации параметров глинистою раствора АПГР-1. Удельный вес раствора определяется разностью давления, которая измеряется самопишущим поплавковым дифманометром, подключенным параллельно трубкам. Вязкость раствора измеряется стандартным полевым вискозиметром типа СПВ-5, в который опущены три электрода. Каждые 10 мин. таймлер замыкает цепь катушки соленоидного клапана, который, срабатывая, открывает доступ раствору в вискозиметр. Когда уровень раствора в воронке коснется верхнего электрода, что соответствует объему 800-1000 см3, клапан автоматически закроется, а приток раствора прекратится. Уровень раствора в вискозиметре начнет понижаться. Когда в вискозиметре останется 700 см3 глинистого раствора, средний электрод перестанет касаться его уровня и включатся электрические часы 8. Когда в вискозиметре останется 200 см3 глинистого раствора, нижний электрод перестанет касаться уровня и прекратится запись времени истечения. Через 3 мин. после начала цикла измерения вязкости откроется клапан 6, в вискозиметр поступит вода для промывки прибора. Промывка прибора длится 30-40 сек. Следующий цикл измерения начинается через 6 мин. после окончания предыдущего. Диапазон измерения удельного веса 1,0-2,0 г/см3, предел измерения вязкости 50-100 сек. Погрешность измерения удельноговеса ±0,02г/см3, вязкости ±1 сек. Скорость перемещения дисковой диаграммы регистрирующего прибора 1 об /сутки. Питание автомата: переменным током напряжением 220 в, мощностью 300 ва. Габаритные размеры автомата 780 X 450 X 750 мм. Вес 130 кг. Отстойник ОМ-1 Рис. 5. Прибор ЦС-1 для определения стабильности глинистого раствора. В отстойник наливают 50 см3 глинистого раствора, который затем разбавляют водой до объема 500 см3. Содержимое сильно взбалтывают, после чего прибор ставят в вертикальное положение на 3 мин. Этого времени вполне достаточно для осаждения песка, так как при этом успевают осесть все частицы размером более 0,02 мм. Частицы, не успевшие осесть, являются пылью и на качество глинистого раствора практически влияния не имеют. Определение стабильности глинистого раствора Стабильность измеряется следующим образом. Цилиндрический сосуд заполняют глинистым раствором и оставляют в покое па 24 часа. Если вначале раствор в сосуде был однороден, то после стояния в покое его свойства в верхней и нижней частях сосуда становятся различными. После 24-часового отстаивания глинистый раствор из верхней половины сосуда сливают через боковой отвод, снабженный резиновой трубкой и зажимом, а из нижней половины - через нижний отвод. Измеряют ареометром удельные веса обеих порций раствора. Разность удельных весов обозначается буквой С и принимается за меру стабильности глинистого раствора. Рис. 6. Металлический отстойник ОМ-1- Пример. Удельный вес глинистого раствора в верхней половине сосуда равен 1,20, а в нижней 1,24 г/см3\ стабильность при этом будет равна С = 1,24 - 1,20 = 0,04 г/см3. Чем больше число, показывающее стабильность, тем хуже качество глинистого раствора. Для неутяжеленных глинистых растворов стабильность должна быть не более 0,02, а для утяжеленных не более 0,06 г/см3. Суточный отстой Для определения суточного отстоя глинистый раствор наливают в стеклянную мензурку и оставляют в покое на 24 часа. Затем измеряют объем выделившегося из раствора слоя светлой жидкости в процентах по объему от объема глинистого раствора. Для хороших глинистых растворов суточный отстой равен нулю; вообще он не должен быть выше 2-4%. Определение статического напряжения сдвига Статическим напряжением сдвига называется прочность жесткой пространственной структуры, возникающей в глинистом растворе в состоянии покоя вследствие слипания частиц глины. Так как прочность структуры глинистого раствора возрастает с течением времени, прошедшего с момента окончания перемешивания, было установлено, что измерение следует производить через 1 мин. и через 10 мин. после окончания перемешивания; в этом случае статическое напряжение сдвига обозначается вг и 01О. Измерение статического напряжения сдвига на приборе СНС-1 осуществляется следующим путем. Глинистый раствор наливают в стакан, установленный на вращающемся столике. Вращение столику передается при помощи кольцеобразной пружины 3 от маленького электродвигателя. После сильного перемешивания раствора в стакане в него погружают цилиндр, подвешенный на кронштейне на тонкой упругой стальной нити. После паузы в 1 или 10 мин. включают двигатель, стакан начинает вращаться со скоростью один оборот за 5 мин. Пока структура в глинистом растворе не разрушена, вращение от стакана передается через слой глинистого раствора, как через твердое тело, цилипдру, который вращается вместе со стаканом. Нить 2 при этом закручивается и сила сопротивления ее дальнейшему закручиванию все возрастает. Но наступает такой момент, когда сопротивление нити преодолевает прочность структуры глинистого раствора у стенок цилиндра и цилиндр останавливается. В этом положении замечают наибольший угол закручивания нити от первоначального положения и по данным, имеющимся в паспорте прибора, рассчитывают соответствующую этому углу закручивания величину статического напряжения сдвига. Для отсчета углов закручивания на приборе установлен лимб. Рис. 7. Прибор CHG -1 для определения статического напряжения сдвига глинистых растворов. Для утяжеления считаются пригодными глинистые растворы, имеющие статическое напряжение сдвига в пределах в = 30 4—т- 50 мг/см2. Определение водоотдачи глинистого раствэра Измерение водоотдачи на буровых производится при помощи приборов ВМ-6. Образец глинистого раствора объемом 120 см3 заливают в фильтрационный стакан 1. Дно стакана представляет Рис. 8. Прибор ВМ-6 для определения водоотдачи глинистых растворов. собой решетку для вытекания отделяющейся жидкости. На эту решетку в качестве пористой перегородки кладут фильтровальную бумагу. Избыток давления на глинистый раствор создается весом плунжера и кожуха с грузовым кольцом, подобранного с расчетом создания избыточного давления в 1 кГ/см2. Давление плунжера на глинистый раствор передается через машинное масло, заполняющее цилиндр. Объем воды, отжимаемой из глинистого раствора, определяется по опусканию плунжера в цилиндре. Для отсчета на цилиндре сделана метка, а на кожухе прикреплена шкала, деления на которой показывают величину водоотдачи. В нижней крышке сделан запорный клапан, состоящий из стального диска с резиновой прокладкой сверху и нажимного винта. Этот запорный клапан служит для того, чтобы не происходило выделения воды из глинистого раствора во время сборки и регулировки прибора перед измерением. Прибор ВМ-6 позволяет непосредственно измерять водоотдачу до 40 см3. К атегория: - Буровое оборудование Эффективность бурения зависит от комплекса факторов: осевой нагрузки на долото, частоты вращения долота, расхода бурового раствора и параметров качества бурового раствора, типа долота, геологических условий, механических свойств горных пород. Выделяют параметры режима бурения , которые можно изменять с пульта бурильщика в процессе работы долота на забое, и факторы, установленные на стадии проектирования строительства скважины, отдельные из которых нельзя оперативно изменять. Первые называются управляемыми. Определённое сочетание их, при котором осуществляется механическое бурение скважины, называется режимом бурения . Режим бурения, обеспечивающий получение наилучших показателей при данных условиях бурения , называется оптимальным. Иногда в процессе бурения приходится решать и специальные задачи – проводка скважины через поглощаюшие пласты, обеспечение минимального искривления скважины, максимального выхода керна, качественного вскрытия продуктивных пластов. Режимы бурения , при которых решаются такие задачи, называются специальными. Каждый параметр режима бурения влияет на эффективность разрушения горных пород, причём влияние одного параметра зависти от уровня другого, то есть наблюдается взаимовлияние факторов. Выделяют следующие основные показатели эффективности бурения нефтяных и газовых скважин: проходка на долото, механическая и рейсовая скорости бурения . Проходка на долото Hд (м) очень важный показатель, определяющий расход долот на бурение скважины и потребность в них по площади и УБР в целом, число СПО, изнашивание подъемного оборудования , трудоемкость бурения , возможность некоторых осложнений. Проходка на долото в большей мере зависит от абразивности пород, стойкости долот, правильности их подбора, режимов бурения и критериев отработки долот. Механическая скорость (Vм): Vм = Hд / Тм где Hд - проходка на долото, м; Тм - продолжительность механического разрушения горных пород на забое или время проходки интервалов, ч. Таким образом, Vм - средняя скорость углубления забоя. Она может быть определена по отдельному долоту, отдельному интервалу, всей скважине Lс, по УБР и т.д.: Vм = Lс / Тм Выделяют текущую (мгновенную) механическую скорость: Vм = dh / dt При известных свойствах горных пород механическая скорость характеризует эффективность разрушения их, правильность подбора и отработки долот, способа бурения и режимных параметров, величину подведенной на забой мощности и ее использование. Если в одинаковых породах и интервалах одной скважины скорость ниже, чем в другой, надо улучшать режим. Изменение текущей механической скорости связано с изнашиванием долота, чередованием пород по твердости, изменением режимных параметров в процессе отработки долота, свидетельствует о целесообразности подъема долота. Рейсовая скорость Vр = Hд / (Тм + Тсп) где Hд - проходка на долото, м; Тм – продолжительность работы долота на забое, ч; Тсп – продолжительность спуска и подъема долота, наращивания инструмента, ч. Рейсовая скорость определяет темп углубления скважины, она показывает, что темп проходки ствола зависит не только от отработки долота, но и от объема и скорости выполнения СПО. Если долго работать изношенным долотом или поднимать долото преждевременно, то Vр снижается. Долото, поднятое при достижении максимума рейсовой скорости, обеспечивает наиболее быструю проходку ствола. Средняя рейсовая скорость по скважине выражается: Vр = Lс / (Тм + Тсп) 5.1. ВЛИЯНИЕ РЕЖИМНЫХ ПАРАМЕТРОВ НА ПОКАЗАТЕЛИ БУРЕНИЯ 5.1.1. ВЛИЯНИЕ ОСЕВОЙ НАГРУЗКИ Разрушение горной породы на забое механическим способом невозможна без создания осевой нагрузки на долото. На рис. 5.1. показана зависимость механической скорости бурения Vм от осевой нагрузки G на трёхшарошечное долото при проходке мягких (кривая 1), средней твёрдости (кривая 2), твёрдых (кривая 3) и крепких (кривая 4) пород при неизменной низкой (до 60 об/мин) частоте вращения и достаточной промывке за короткий промежуток времени, когда изнашиванием долота можно пренебречь. Как видно из рисунка, механическая скорость непрерывно возрастает с увеличением осевой нагрузки, но темп её роста для мягких пород более быстрый, так как больше глубина погружения зубьев при одинаковой нагрузке. На стенде, и в промысловых условиях наблюдается изменение темпа роста Vм от G при переходе от разрушения пород истиранием при небольшой осевой нагрузке к разрушению пород в усталостной и объёмной областях при больших Если скорость вращения долота неизменна и обеспечивается достаточная чистота забоя, величина углубления за один оборот dу возрастает с увеличением удельной осевой нагрузки Руд так, как это показано на рис. 5.2. (кривая ОАВС). При весьма малой нагрузке напряжение на площадке контакта зуба шарошки с породой меньше предела усталости последней; поэтому при вдавливании происходит лишь упругая деформация породы (участок ОА). Разрушение же породы в этой зоне, которую обычно называют областью поверхностного разрушения, может происходить путём истирания и, возможно, микроскалывания шероховатостей поверхности при проскальзывании зубка. Если нагрузка более высокая (участок АВ), то давление на площадки контакта зубка с забоем превышает предел усталости, но меньше предела прочности породы. Поэтому при первом ударе зубка по данной площадке происходит деформация породы, возможно, образуются начальные микротрещины, но разрушения ещё не происходит. При повторных ударах зубков по той же площадке начальные микротрещины развиваются вглубь до тех пор, пока при очередном ударе не произойдёт выкол. Чем больше действующая на зубок сила, тем меньше ударов требуется для разрушения. Эту зону называют областью объёмно – усталостного разрушения. При более высоких нагрузках разрушение породы происходит при каждом ударе зубка. Поэтому участок правее точки В называют областью эффективного объёмного разрушения породы. В области ОА углубление за один оборот dу мало и возрастает очень медленно, пропорционально удельной нагрузке на долото Руд. Под удельной нагрузкой понимают отношение нагрузки на долото G к его диаметру. В области усталостного разрушения углубление растет быстрее увеличения удельной нагрузки и зависимость между ними имеет степенной характер. В области эффективного объёмного разрушения породы углубление за один оборот быстро возрастает – примерно пропорционально удельной нагрузке (или несколько быстрее), если обеспечена достаточная очистка забоя. Характер зависимости между углублением за один оборот долота dу и удельной нагрузкой Руд существенно изменяется, как только очистка забоя становится недостаточной и на нём скапливаются ранее сколотые частицы, которые не успели переместиться в наддолотную зону. Такие частицы дополнительно измельчаются при новых ударах зубков шарошек по забою. Поэтому с ухудшением очистки забоя прирост углубления за один оборот долота с увеличением удельной нагрузки будет уменьшаться. Так, согласно кривой ОАВДЕ, полученной при бурении с секундным расходом промывочной жидкости Q1, углубление за 1 оборот быстро возрастает, до тех пор, пока удельная нагрузка не превышает Р111уд. При нагрузках выше Р111уд прирост углубления сначала замедляется, а затем (правее точки F) углубление за один оборот уменьшается из-за ухудшения очистки забоя. В случае же увеличения секундного расхода до Q2 влияние ухудшения очистки забоя становится заметным при более высокой удельной нагрузке (правее точки G на кривой АВGH). 5.1.2. ВЛИЯНИЕ ЧАСТОТЫ ВРАЩЕНИЯ ДОЛОТА С изменением частоты вращения долота меняется число поражений забоя зубками шарошечного долота. При малой частоте вращения долота промежуток времени, в течение которого остаётся раскрытой трещина в породе, образующаяся при вдавливании зубка, достаточен для того, чтобы в эту трещину проник фильтрат бурового раствора (или сам раствор). Давления на частицу сверху и снизу практически сравниваются и трещина не может сомкнуться после отрыва зубка от породы. В этом случае отрыв сколотой частицы от забоя и её удаление облегчаются. При увеличении же частоты вращения уменьшается промежуток времени, в течение которого трещина раскрыта, и фильтрат может заполнять её. Если же этот промежуток станет весьма малым, фильтрат в трещину не успеет проникнуть, трещина после отрыва зубка шарошки от породы сомкнётся, а прижимающая сила и фильтрационная корка будут удерживать частицу, препятствовать её удалению с забоя. Поэтому на забое сохраниться слой сколотых, но не удалённых частиц, которые будут повторно размалываться зубцами долота.
5.1.3. ВЛИЯНИЕ РАСХОДА БУРОВОГО РАСТВОРА Непрерывная циркуляция бурового раствора при бурении должна обеспечивать чистоту ствола скважины и забоя, охлаждение долота, способствовать эффективному разрушению породы, предупреждать осложнения. Влияние расхода раствора на механическую скорость бурения показано на рис. 5.4. Как видно из рисунка, при неизменной осевой нагрузке и частоте вращения долота с увеличением секундного расхода бурового раствора улучшается очистка забоя и возрастает механическая скорость проходки. Однако увеличение секундного раствора эффективно лишь пока он не достигнет некоторой величины Qд, при Qмах механическая скорость проходки стабилизируется. Величина Qд зависит от конструкции долота, схемы очистки забоя, удельной осевой нагрузки, частоты вращения, твёрдости породы и свойств бурового раствора.
5.1.4. ВЛИЯНИЕ СВОЙСТВ БУРОВОГО РАСТВОРА На механическую скорость бурения влияют плотность, вязкость, фильтрация, содержание песка и ряд других параметров бурового раствора. Наиболее существенно оказывает влияние плотность бурового раствора. Это влияние объясняется в основном повышением гидростатического давления на забой и ростом перепада давления между скважиной и разбуриваемым пластом, в результате чего ухудшаются условия образования трещин, выкалываемые частицы прижимаются к массиву. Поэтому наиболее значительно влияние r в области объёмного разрушения породы, а при бурении в области поверхностного разрушения и истирания оно незначительно. С понижением плотности в большей мере проявляется эффект неравномерного всестороннего сжатия, облегчающего разрушение пород. Чем выше проницаемость пород и больше водоотдача (фильтрация), меньше вязкость фильтрата, ниже частота вращения, больше продолжительность контакта, тем слабее влияние плотности раствора, поскольку давление на забое и на глубине выкола успевает выровняться. 5.2. ОСОБЕННОСТИ РЕЖИМОВ ВРАЩАТЕЛЬНОГО БУРЕНИЯ . Увеличение осевой нагрузки и частоты вращения, повышение плотности, вязкости и концентрации твёрдых частиц, снижение расхода ниже Qд, а также теплоёмкости, теплопроводности и смазывающих свойств буровых растворов, неравномерная (рывками) подача долота, продольные и поперечные колебания низа бурильной колонны, высокая температура на забое – всё это сокращает производительное время пребывания долота на забое. Однако конечная цель – не увеличение продолжительности пребывания долота на забое, а получение большей проходки на долото за возможно более короткое время. Поэтому если изменение какого-то параметра обуславливает сокращение продолжительности работы долота на забое, но одновременно увеличивается механическая скорость и повышается проходка на долото, то оно целесообразно. Так как параметры режима бурения взаимосвязаны, то наибольшая эффективность бурения достигается лишь при оптимальном сочетании этих параметров, зависящем от физико-механических свойств породы, конструкции долота, глубины залегания разбуриваемой породы и других факторов. Увеличение одного из параметров режима, например, осевой нагрузки, способствует повышению эффективности бурения лишь до тех пор, пока он не достигнет оптимального значения при данном сочетании других параметров. Увеличение рассматриваемого параметра выше этого оптимального значения может способствовать дальнейшему повышению эффективности бурения только в том случае, если одновременно будут изменены все или некоторые другие параметры (например, увеличен расход промывочной жидкости, уменьшена частота вращения). Измененному сочетанию других параметров режима соответствует новое оптимальное значение рассматриваемого. Изменение параметров режима возможно лишь в определённых пределах, которые зависят от прочности долота, особенностей способа бурения , технических параметров буровой установки и ряда других факторов. Регулировать расход бурового раствора можно тремя способами: заменой втулок одного диаметра в цилиндрах бурового насоса на втулки другого диаметра, изменением числа одновременно параллельно работающих буровых насосов, изменением числа двойных ходов поршней в насосе. При первых двух способах расход раствора можно изменять только ступенчато, при третьем возможно также плавное изменение. Второй из названных выше способов применяют, как правило, в случае изменения диаметра долота: при бурении верхнего участка скважины долотами большого диаметра используют два одновременно работающих насоса. При переходе к бурению следующего участка долотами меньшего диаметра один из насосов часто отключают. Менять втулки можно только в неработающем насосе. Поэтому в большинстве случаев расход жидкости в период работы долота на забое остаётся практически неизменным. Если продолжительность рейса велика (несколько десятков часов), расход к концу рейса может несколько уменьшиться вследствие возрастания утечек в насосе, обусловленного износом поршней. Гидравлическую мощность на забое можно регулировать изменением либо расхода бурового раствора, либо диаметра гидромониторных насадок в долоте, либо числа таких насадок. Очевидно, диаметр насадок можно изменить только при подготовке нового долота к спуску в скважину. Число же работающих насадок можно уменьшить так же в период работы долота на забое, если в поток жидкости в бурильных трубах сбросить шар соответствующего диаметра, он перекроет входное отверстие в одной из насадок и выключит её из работы. При этом скорости струй и перепад давлений в оставшихся работающих насадках возрастут, и соответственно увеличится гидравлическая мощность на забое. Такой способ регулирования гидравлической мощности на забое можно использовать тогда, когда рабочее давление в насосах меньше предельно допустимого при данном диаметре втулок в них. |